Oct 28 2010
Innovative materials and expert application development, aimed at enhancing the performance of vehicle systems, improving their sustainability and reducing their total cost, form the forefront of DuPont Performance Polymers in the automotive sector.
At K 2010, DuPont is focusing on new developments in several of these areas, as it supports the global automotive industry in its drive to reduce dependence on fossil fuels and CO2 emissions. These include new, longer-life, high temperature and chemically resistant materials to help downsize engines whilst maintaining, or increasing, their performance; lightweighting materials and innovative metal replacement ideas to help reduce vehicle weight for better fuel economy; alternative fuel-resistant materials to embrace new, more bio-based fuels; the use of renewably-sourced materials with high performance characteristics; and the development of low-emission materials that maintain their mechanical performance.
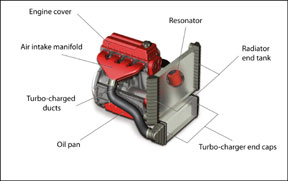
"We are experiencing dynamic times within the automotive industry, as OEMs and suppliers start to rethink almost every aspect of the vehicle in their pursuit of more sustainable, cost-effective and desirable solutions," says Klaus Bender, Automotive Marketing Manager - Europe. "We firmly believe that the drive to reduce cost and weight will introduce plastics in applications never before considered, and that DuPont can actively support this trend by inventing new materials and innovative solutions that can help meet these goals quickly, drawing from our rich history of invention and global team of technical and development experts."
Longer-life. light weight materials
The downsizing of engines to meet fuel economy and CO2 reduction while still delivering engine performance is leading to hotter temperatures, harsher chemicals and tighter underhood packaging constraints. Moreover, metals do not represent the long-term, sustainable answer. In response to the automotive industry's innovative needs, DuPont Performance Polymers has introduced new, long-term aging resistant plastics, such as DuPont Zytel PLUS nylon, inviting new ways to replace metal, especially under the hood, in transmissions and exhaust systems. Zytel PLUS nylon delivers excellent performance levels and importantly maintains those excellent performance levels much longer than traditional nylons.
Alternative-fuel resistant materials
The use of new biofuels places demands greater resistance from the materials used in fuel system and engine hoses, gaskets and o-rings. DuPont research, and independent testing by several leading fuels system OEMs, has demonstrated that fluoroelastomers offer the best permeation performance of traditional elastomeric sealing materials used for such components. Moreover, Viton has been shown to be 1000 times better than silicon (VMQ) and 100 times better than HNBR in permeation resistance. It also has better heat aging and compression set resistance performance than either VMQ or HNBR. In addition, recent testing of Zytel and Delrin engineering polymers and Vamac Ultra ethylene acrylic elastomers (AEM) in aggressive AdBlue1 aqueous urea solution has demonstrated the effectiveness of these products for selective catalytic reduction (SCR) systems used to reduce NOx emissions from diesel engines.
Renewably-sourced materials
DuPont Performance Polymers has introduced a number of renewably sourced products that are made, in whole or in part, from renewable agricultural feedstocks (such as corn, castor beans and non-food biomass) rather than petroleum to help the automotive industry reduce its dependence on depleteable petroleum-based products. Among the 20 high-performance product families are: DuPont Sorona polymer, DuPont Sorona EP thermoplastic polymer, DuPont Hytrel RS thermoplastic elastomer and DuPont Zytel RS long chain polyamides. These products create a much smaller environmental footprint than the entirely petrochemically-based materials they replace with no compromise in performance.
Low-emission materials
At the end of 2009, DuPont introduced three new enhanced low-emission PE grades of DuPont Delrin, which provide extremely low volatile release without a reduction in mechanical performance versus the standard high performance grades, including excellent creep and fatigue resistance. All three PE grades have been specially formulated with a so-called formaldehyde catcher - without compromising the mechanical properties - to substantially reduce their release of formaldehyde during processing and use to levels which meet the stringent emission requirements demanded by some of today's leading automotive OEMs. Their availability is in addition to the low-emission Delrin P grades which meet the standard low emission targets of other manufacturers. The introduction of Delrin PE will open up new opportunities for the cost-effective replacement of existing materials in many automotive interior applications. These include, for example, components for safety systems, door panels and seats, where the unique combination of properties of Delrin can be of great benefit.