May 14 2021
Safran Landing Systems, a wholly-owned subsidiary of French multinational aerospace company Safran SA and the world's largest supplier of landing gear, has teamed up with German powder bed, metal additive manufacturing (AM) equipment specialist SLM Solutions to evaluate the feasibility of using its technology to produce large, safety-critical aircraft components. SLM Solutions' sole agent for the UK and Ireland, Kingsbury, describes the project.
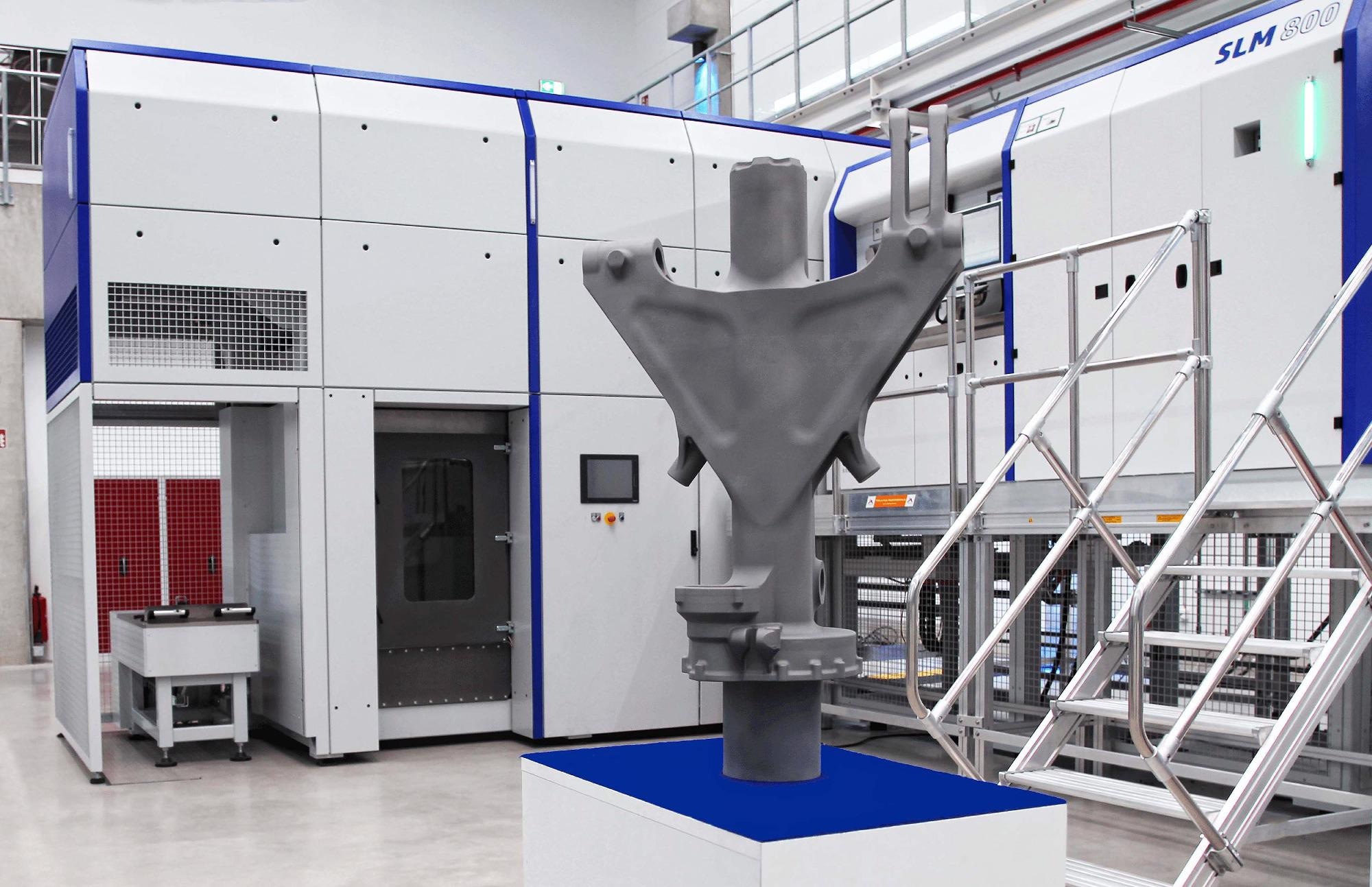
The main fitting for the nose landing gear of a business jet 3D-printed from titanium alloy in a quad-laser SLM®800 powder bed AM machine at SLM Solutions in Luebeck. Image Credit: Kingsbury
The trial involved 3D-printing the main fitting for the nose landing gear of a business jet layer by layer from titanium alloy powder by selective laser melting. It was a world-first for such a large part measuring 455 mm x 295 mm x 805 mm tall. The component was redesigned to optimize its production using metal powder bed AM, leading to a time-saving in the build process and a significant weight reduction of around 15 percent compared with if the part were to be milled from a forging.
Due to the stringent demands placed on this component, which is one of the landing gear elements that transfers the load from the front wheel to the aircraft structure and is retracted after take-off, titanium is the ideal material due to its good mechanical properties, durability, and resistance to corrosion without the need for surface treatment.
Thierry Berenger, Additive Manufacturing project leader at Safran Landing Systems said: "We chose SLM Solutions as a partner because of their expertise and the availability of an SLM®800 machine at their facility in Luebeck, which exactly met our requirements in terms of size and reliability."
Having a vertically extended build envelope, the machine is equipped with SLM Solutions’ proven quad-laser technology and other innovative features such as a patented gas flow system and a permanent filter, which ensure high reliability. One of the strengths of SLM® technology is its flexibility. Design changes can be quickly made and modifications printed and tested, so less time is spent in prototype development.
Gerhard Bierleutgeb, EVP Global Services & Solutions at SLM Solutions explained, "Additive manufacturing contributes to saving time in the qualification and certification phases by rapidly providing parts for testing.
"We were able to produce this main fitting in a few days on the SLM®800, whereas it would take a few months using a traditional process based on a forging.”