A new study in the journal Crystals has attempted to better characterize the microstructure of aluminum-erbium master alloys.

Study: Microstructural Master Alloys Features of Aluminum–Erbium System. Image Credit: Maksim_Gusev/Shutterstock.com
Aluminum remains one of the most popular and widely used metals, the key to a significant number of technologies and tools that are central to modern society. Aluminum is also widely employed due to its recyclability.
Pure aluminum is relatively soft, however, and the addition of other elements to aluminum is a key approach to enhancing its physical properties, particularly its strength, formability, and resistance to corrosion.
More recently, the addition of rare Earth metals to aluminum alloys has revealed the potential uses of erbium and ytterbium as a means of further reinforcing aluminum alloys.
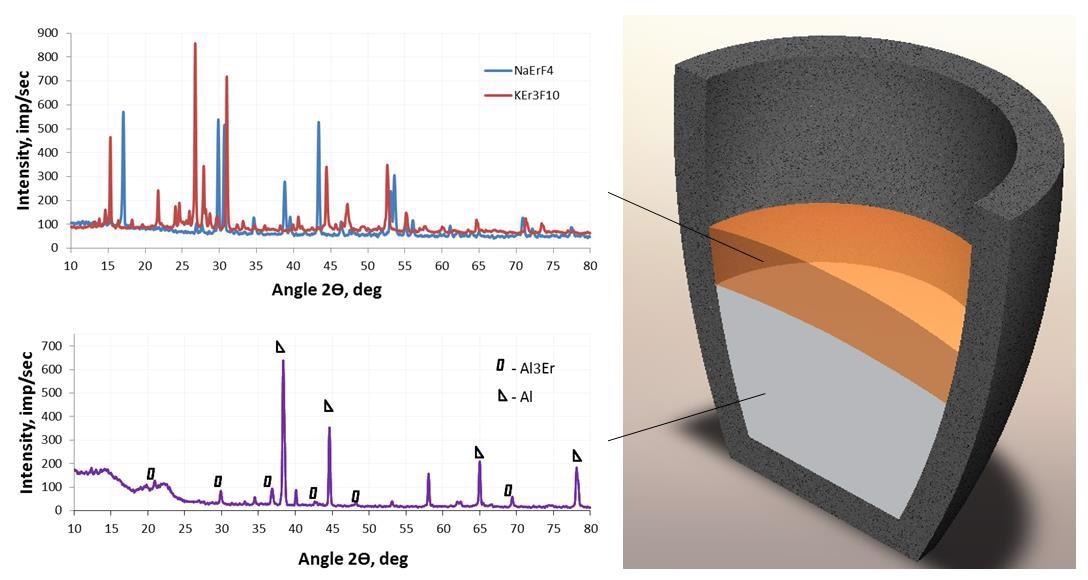
Diagram of the location of melts during aluminothermic preparation of master alloy and radiographs of components. Image Credit: Savchenkov, S et al., Crystals
Aluminum alloys with rare earth metals are a popular choice in construction, aircraft and automotive engineering, and a range of other industries due to their lightweight and high strength.
In order to produce high-performance aluminum alloys and derivative products, it is important to use an optimal master alloy. Master alloys remain the key charging material and are central to the quality of alloys during their preparation and any products subsequently cast from these.
The microalloying of aluminum alloys with erbium, in particular, is gaining increasing amounts of attention, but its potential uses are thus far hindered by challenges in properly implementing this in the alloying process.
To help address these challenges, new research presented in the Crystals journal has aimed to better characterize the microstructure of aluminum-erbium master alloys with a view to optimizing their production and increasing their applicability.
The production of aluminum master alloys with erbium first requires the production of pure metallic erbium. This process itself is complex and highly technical, with challenges stemming from the significant difference in the components’ melting temperatures (more than 800 °C).
Further issues arise due to the associated losses of the aluminum itself and the alloying component—up to 10% of the aluminum and approximately 25% of the alloying component. Incomplete absorption of erbium during fusion can also further complicate this process.
In order to help fully realize their benefits and improve their methods of production, the researchers worked to develop a more efficient means of obtaining aluminum–erbium master alloys.
The production of aluminum–erbium master alloys is typically achieved via specific high-temperature physicochemical processes, depending on the characteristics of the reducing metal or the elements that make up the flux used in its production.
The researchers sought to determine how the quality of the obtained master alloys could be impacted by the content and specific qualities of the alloying component.
In order to do this, they used a series of metallographic studies, paying specific attention to the microstructural parameters of aluminum–erbium master alloys and their impact on both the quality of the master alloys and the quality of castings, ingots, semi-finished products, and products created from those aluminum alloys.
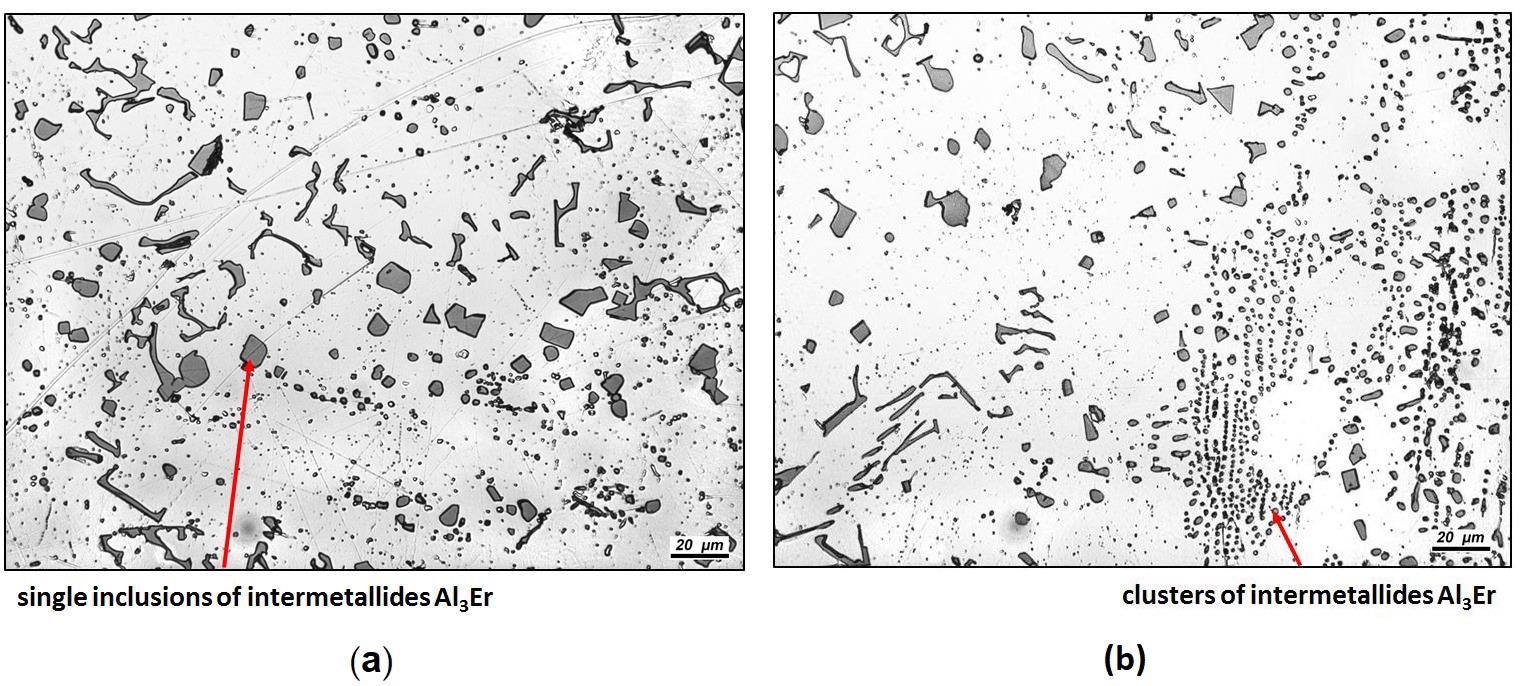
Microstructure of the master alloy composition Al-8Er: (a) x500; (b) x500. Image Credit: Savchenkov, S et al., Crystals
A series of advanced analytical methods were employed in the characterization of the acquired master alloys, most notably X-ray fluorescence spectrometry and atomic absorption spectrometry with ICP (ICP-AAS).
An electron microscope was utilized in the metallographic study of acquired master alloy samples, with additional insight afforded via the use of an energy dispersive X-ray spectrometer and an inverted microscope with image analysis software used to determine grain size.
One of the key parameters under investigation was the microhardness of the obtained master alloys. This was determined using an ultra-micro tester and a standard indenter.
Thanks to this comprehensive and powerful array of analytical tools, the researchers were able to discover that master alloys acquired via metallothermic reduction of erbium compounds from chloride–fluoride melts had a considerable impact on the structure of the alloys.
By analyzing the microstructure of the master alloy, the researchers discovered that this varied depending on its erbium content.
More specifically, they discovered that erbium content up to 6 wt.% in the master alloy resulted in the structure of the alloy’s components (its eutectic structure) being preserved, but erbium content of 8 wt.% or more resulted in the structure becoming a solid solution with different shaped inclusions of intermetallic compounds.
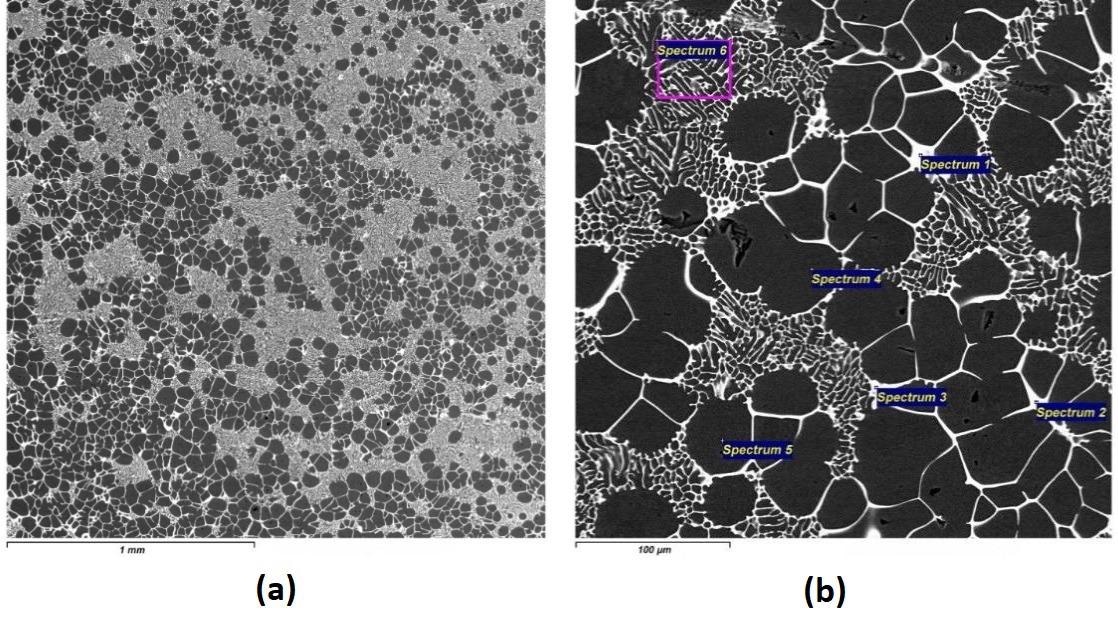
The electronic pictures of the microstructure and the EDX results of master alloys Al-4.2Er cast with a high cooling rate: (a) x40; (b) x400. Image Credit: Savchenkov, S et al., Crystals
Based on these findings, it has been possible to isolate specific powders of aluminum-erbium intermetallides, which offer good potential for the future synthesis of composite metal materials.
While this research is still in its relative infancy, it is clear that these findings may give rise to new pathways for the optimized development and production of aluminum–erbium master alloys with high-performance characteristics.
Disclaimer: The views expressed here are those of the author expressed in their private capacity and do not necessarily represent the views of AZoM.com Limited T/A AZoNetwork the owner and operator of this website. This disclaimer forms part of the Terms and conditions of use of this website.
Sources:
Savchenkov, Sergey, Yaroslav Kosov, Vladimir Bazhin, Kirill Krylov, and Rudolf Kawalla. 2021. "Microstructural Master Alloys Features of Aluminum–Erbium System" Crystals 11, no. 11: 1353. https://www.mdpi.com/2073-4352/11/11/1353
The Aluminum Association. n.d. Aluminum Alloys 101 https://www.aluminum.org/