Almost a quarter of the global energy supply is spent tackling issues related to wear and tear – or to be more accurate, overcoming common issues related to tribology, according to a team of researchers who published new work in the journal Tribology Methods.
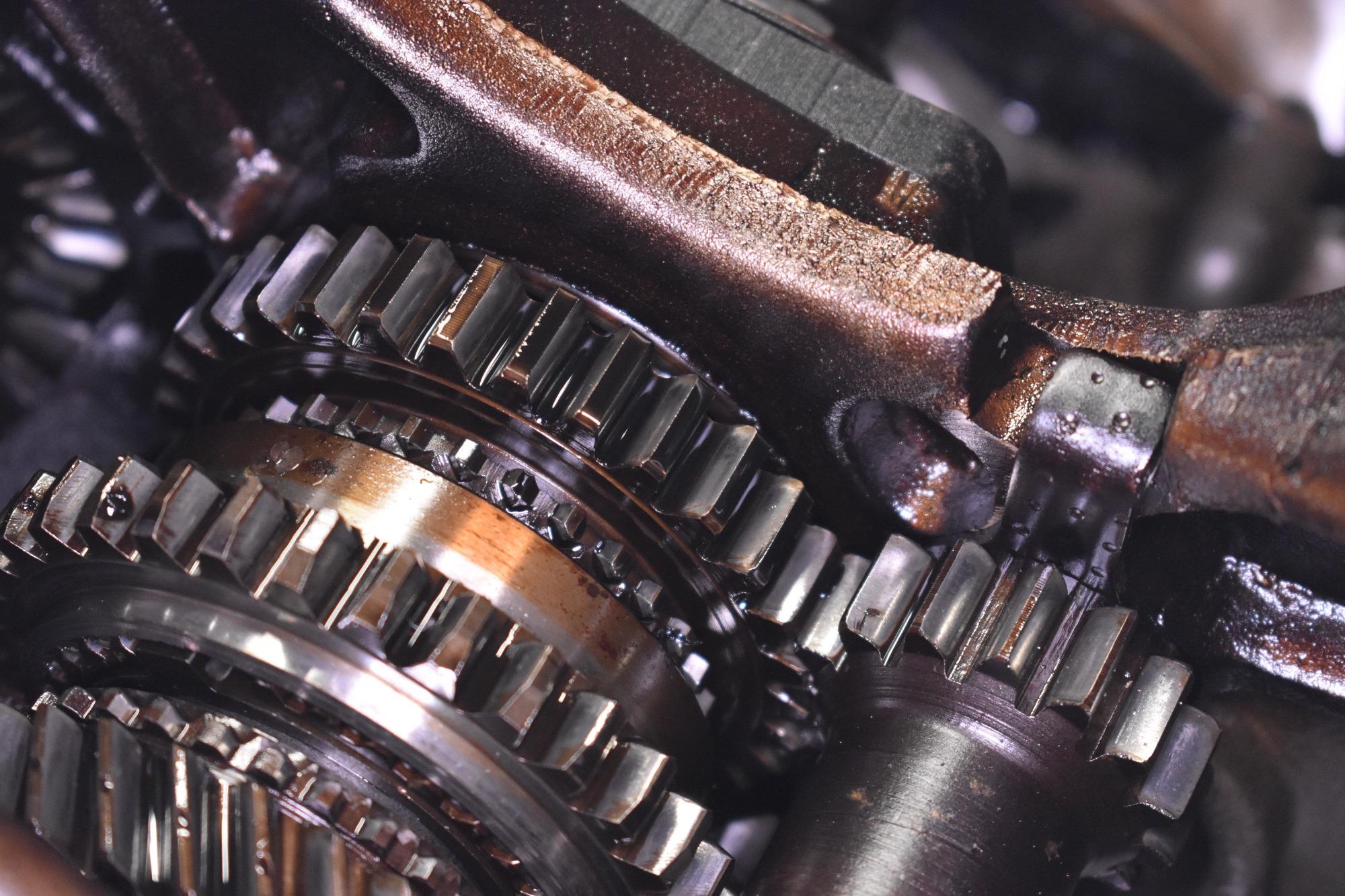
Study: Development of a Protective Coating for Evaluating the Sub-surface Microstructure of a Worn Material. Image Credit: Mathew Alexander/Shutterstock.com
What is more, the issues associated with friction and wear in the mining and mineral industry account for 6% of annual energy consumption, worldwide. To limit and reduce the costs and energy usage associated with operations in this sector, researchers are trying to acquire a greater depth of knowledge in relation to wear mechanisms and, subsequently, improve the materials in use.
The team led by U. Pranav Nayak, lead author and Doctorate student at the Chair of Functional Materials (FuWe) Saarland University, set out to develop a simple and effective method for the protection of a worn surface employing electrolytic deposition with copper (Cu) and nickel (Ni) electrodes.
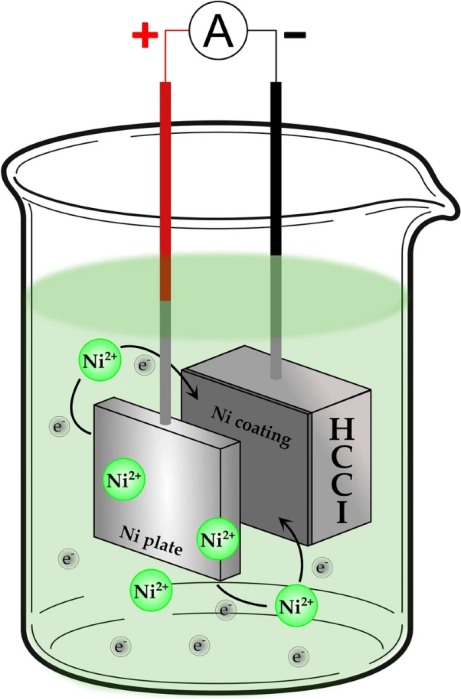
Schematic of the nickel electrodeposition process. Image Credit: Nayak, U.P et al., Tribology Matters
“The main objective of the current work was to develop a simple, yet effective approach to coat the worn surface of an HCCI sample in order to investigate the deformed microstructure underneath the wear track,” explained Nayak.
Tribology Matters
Tribology is the science and engineering of wear, friction, adhesion, and lubrication which draws from a wide range of study fields including physics, chemistry, mathematics, biology, and materials science.
The significance of the global impact of friction and wear on energy consumption and carbon dioxide emissions is considered to be an area of key concern, so implementing advanced green tribological technologies is a primary focus of researchers to limit the environmental impact.
Nayak and his team identified that employing new materials suitable for wear-related functions, modifying the microstructure of existing materials, and even coating materials with a wear-resistant material could extend their longevity.
As well as reducing environmental impact, the application of advanced tribological technologies could yield significant cost savings which in the long term could total close to 1 billion USD. Improving existing materials and technologies would also avoid the potential of catastrophic failures and operational breakdowns that have an adverse effect on productivity, and hence cost.
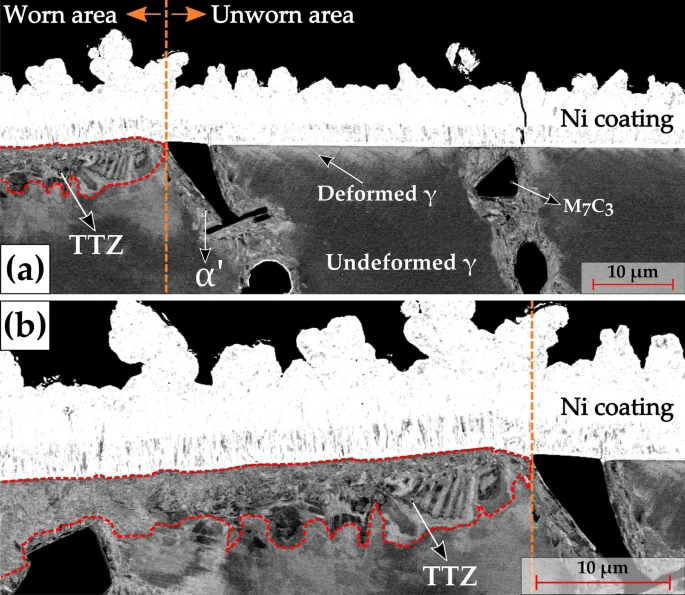
a SEM BSE micrographs of the transverse section encompassing both the worn and the unworn regions. The dashed orange vertical line represents the wear track edge. The respective HCCI microstructural phases are marked for reference along with the Ni coating. The dashed red enclosure represents the tribologically transformed zone (TTZ); b Magnified BSE micrograph of the worn area as indicated in (a). The Ni coating is marked for reference and the dashed enclosure indicates the TTZ. Image Credit: Nayak, U.P et al., Tribology Matters
Copper and Nickel Electrolytic Deposition
For the study, the Saarland team employed a process known as electrolytic deposition using two different electrodes, copper (Cu) and Nickel (Ni), which were applied to a worn high chromium cast iron (HCCI) alloy surface sample.
Electrochemical deposition is a method by which a thin and tightly adherent desired coating of metal, oxide, or salt can be deposited onto the surface of a conductor substrate by simple electrolysis of a solution that contains the desired metal ion, or its chemical complex.
Once applied to the HCCI, the team then employed a series of characterization techniques to assess the efficacy, uniformity, and adhesivity of the Cu and Ni coatings respectively. Optical microscopy (OM) and scanning electron microscopy (SEM) were used to visually assess the coatings. Additionally, EDS was employed to chemically map the cross-section containing both the coating and the HCCI alloy substrate.
They found that the Cu coating exhibited poor uniformity and adhesion and as a result was considered to be ineffective for the intended application. However, the Ni coating demonstrated good uniformity and adhesion with a thickness of around 8 nm, which protected the density of the HCCI sample.
The researchers also used electron backscattered diffraction (EBSD) measurements to observe the deformation of the coated HCCI alloy. “Clearly, the presence of a uniformly coated Ni layer protected the worn surface and prevented the chipping of the brittle EC during the sectioning,” Nayak stated.
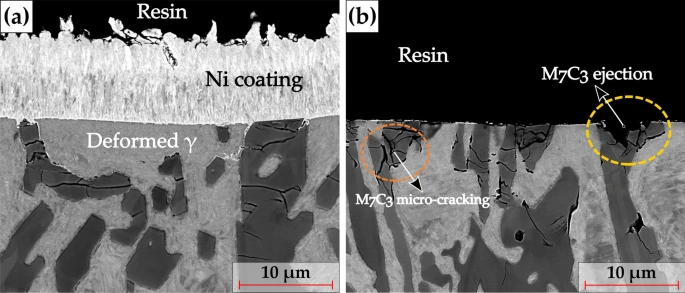
Representative SEM BSE micrographs of the cross-section of the worn sample a with the electrolytic Ni deposition for 30 min, and b without Ni electrodeposition. The dashed orange ellipse and the dashed yellow ellipse in b indicate the fragmentation and ejection of the M7C3 carbide, respectively. It can be visualized from a that the presence of the Ni coating layer has protected the spalled carbides from being ejected. Image Credit: Nayak, U.P et al., Tribology Matters
Future Impact
By taking advantage of new surface materials and coating technologies for improving the quality of existing materials and thereby reducing friction and wear on machinery and other equipment, tribology-related energy losses could be significantly improved upon.
Reports state that in the long term (15 years), the potential is there for a 40% reduction of worldwide energy consumption, and up to 18% in the short term (8 years). On a global scale this equates to around 8.7% savings of total energy consumption, which in theory would offset the current impact of the entire mining and mineral industry.
With the climate crisis front and center of the current global narrative, advanced studies and technologies for improving materials and protecting surface wear are a welcome development that could benefit a vast range of industries, from the mining and mineral sector to transportation and manufacturing.
References:
Nayak, U.P., Webel, J., Pesnel, V. et al. Development of a Protective Coating for Evaluating the Sub-surface Microstructure of a Worn Material. Tribol Lett 69, 165 (2021). https://link.springer.com/article/10.1007%2Fs11249-021-01541-8
Holmberg, K., Erdemir, A. Influence of tribology on global energy consumption, costs and emissions. Friction 5, 263–284 (2017). https://link.springer.com/article/10.1007%2Fs40544-017-0183-5
Disclaimer: The views expressed here are those of the author expressed in their private capacity and do not necessarily represent the views of AZoM.com Limited T/A AZoNetwork the owner and operator of this website. This disclaimer forms part of the Terms and conditions of use of this website.