Hot forming aluminum processes are important for many industrial sectors such as aerospace and automobiles. However, these processes can face challenges. To explore how these processes can be improved, a paper has been published in the journal Wear.
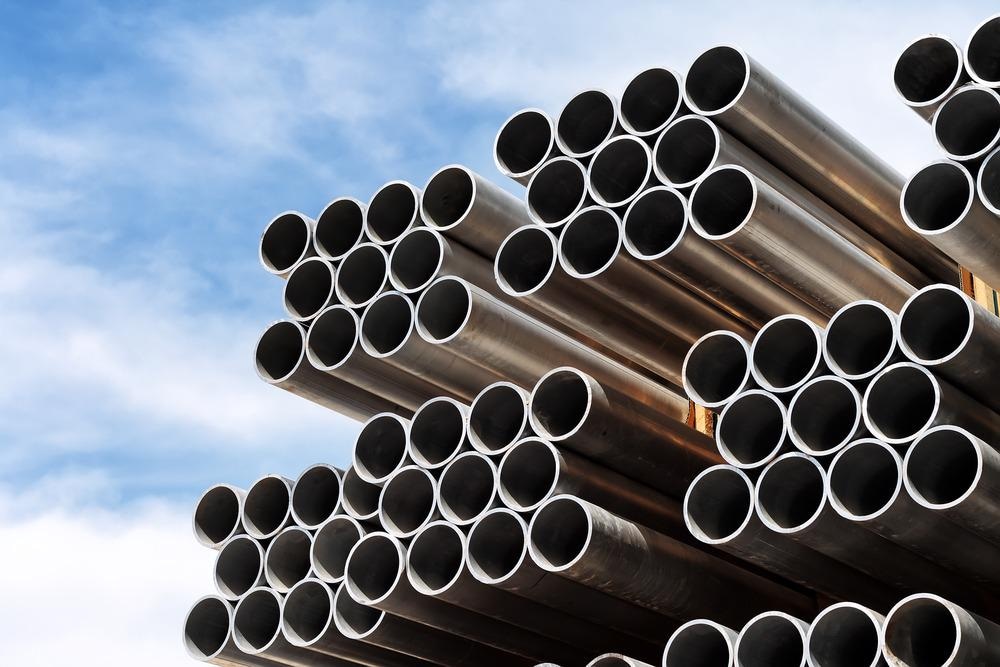
Study: Compatibility of graphite, hBN and graphene with self-lubricating coatings and tool steel for high temperature aluminium forming. Image Credit: ekipaj/Shutterstock.com
Aluminum Alloys and Hot Forming Techniques
Aluminum is used in several commercially important industrial sectors. High-grade aluminum alloys have long been used in aircraft design from military jets to commercial airliners due to their lightweight properties and more recently, their use has increased in the automotive industry. Being lightweight, aluminum alloys provide potential CO2 savings for internal combustion engine vehicles and help compensate for the weight of batteries in electric vehicles. Additionally, aluminum is resistant to corrosion and recyclable.
Despite the obvious advantages of the material, aluminum alloy fabrication can be challenging. The alloys can suffer from spring back and poor ductility when formed at room temperature. To overcome these issues and provide improvements to formability, several processes which use high temperatures have been explored in recent years including hot stamping. These methods have not been widely implemented in industry, however, due to poor tribological behavior during the formation process.
Adhesive Wear: A Problematic Mechanism During the Formation Process.
Adhesive wear is a mechanism that occurs during formation processes, especially hot metal forming, that has a detrimental effect on the finished product’s quality and manufacturing costs. Detachment and material transfer occur between weaker and stronger materials caused by microscopic junction formations. This is aggravated by the high heat and pressure in hot formation techniques. In the case of aluminum, the material can be transferred to tools used in the process, resulting in unstable friction.
Adhesive wear is a significant challenge for aluminum formation processes. Lubricants such as oil and dry films are traditionally used to reduce adhesive wear, but there is a push for processes that use fewer lubricants, in line with the need for cleaner industrial processes. This affects the economic viability and sustainability of aluminum manufacture.
Overcoming Adhesive Wear and Improving Hot Forming Processes
Self-lubricating coatings have been explored to address these issues. These coatings display significant potentials to improve high-temperature processes by reducing material sliding. However, studies on these coatings with aluminum are incomplete. To properly evaluate the properties and potential of these self-lubricating coatings, lab-scale simulations require realistic tribometer configurations for high-temperature aluminum forming. Additionally, studies must consider the interaction of coatings and different tool materials.
Advantages of Aluminum-Scandium Alloy in Shipping
Several solid lubricants have been explored in recent years to improve hot forming processes and overcome issues such as adhesive wear. Of these, graphite, hexagonal boron nitride, and Molybdenum disulfide have been investigated due to their properties. These materials have been used as oil additives for many years.
Exploring these Solid Lubricants
Each material has its own particularities. Graphite, which requires water vapor to effect proper lubrication, is limited ineffectiveness as a solid lubricant to 400 oC. Hexagonal boron nitride displays a similar crystallographic structure to graphite and despite having superior thermal stability, displays higher levels of incompatibility with ceramics and metal alloys. This has limited its application to high temperatures (up to 1200 oC) and where the appearance of the finished product is important.
Molybdenum disulfide and other transition metal dichalcogenides have worse tribological behavior in humid air than graphite but excel in vacuum conditions. Due to insufficient resistance to thermal cycling and oxidation, these compounds are not considered appropriate for high-temperature formation processes.
Despite there being a knowledge gap (which the study in Wear seeks to address) graphite-based materials show the most promise out of all classes of solid lubricants. Graphene, a two-dimensional layered counterpart of graphite, is particularly interesting due to properties including low friction and elevated electrical and thermal conductivity. Additionally, it is less sensitive to humidity than graphite and provides corrosion resistance for coated materials.
However, some challenges exist for using graphene as a coating for hot forming processes. Firstly, studies suggest that to achieve sufficient lubrication, a high degree of graphene coverage must be reached. Additionally, graphene has low solubility in industrial-grade lubricants, leading to uneven agglomeration of particles.
The Gap in Macroscale Tribological Evaluation Studies
Research on the tribological properties of graphene has been largely limited to nanoscale and microscale studies, and not much has been carried out at the macroscale. The study in Wear has attempted to fill this knowledge gap by testing graphene under conditions that are representative of industrial hot aluminum formation. This will help explore its potential as a high-temperature self-lubricating coating for industries such as the automotive and aerospace industries.
Further Reading
Torres, H et al. (2021) Compatibility of graphite, hBN and graphene with self-lubricating coatings and tool steel for high temperature aluminium forming [online] Wear | sciencedirect.com. Available at: https://www.sciencedirect.com/science/article/abs/pii/S0043164821005706
Disclaimer: The views expressed here are those of the author expressed in their private capacity and do not necessarily represent the views of AZoM.com Limited T/A AZoNetwork the owner and operator of this website. This disclaimer forms part of the Terms and conditions of use of this website.