Lithium-ion batteries are commercially important devices that provide low-carbon energy storage solutions for multiple industries. At the end of their service life, recovering their materials improves the sustainability of resources, and a paper published in the jorunal Materials Proceedings has explored the recovery of graphite from lithium-ion batteries.
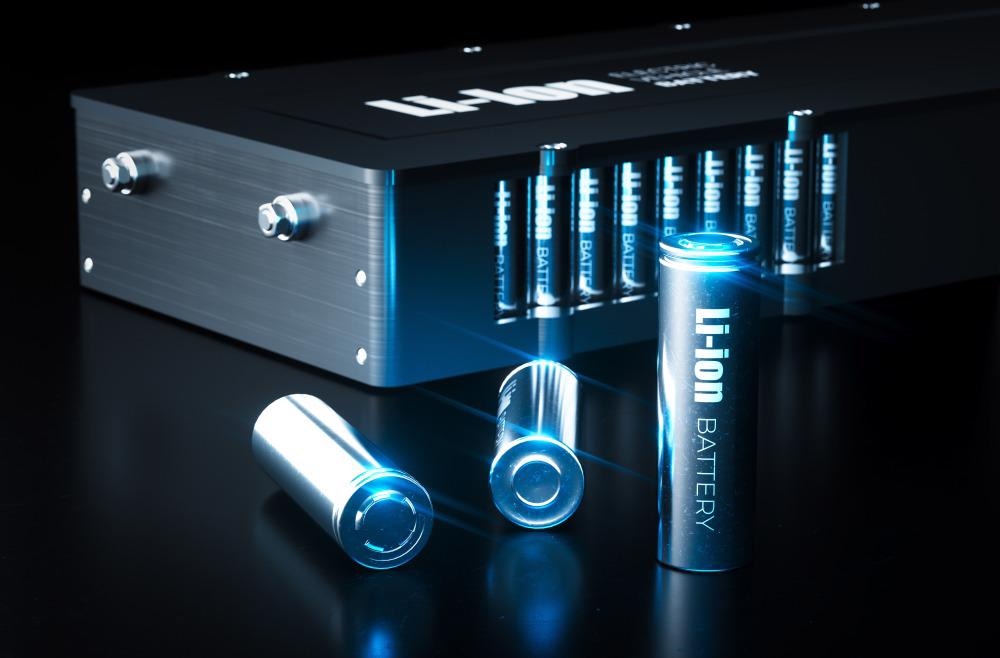
Study: Evaluation of Graphite and Metals Separation by Flotation in Recycling of Li-Ion Batteries. Image Credit: petrmalinak/Shuterstock.com
The Growth of Lithium-Ion Batteries
The global shift toward carbon neutrality and away from reliance on fossil fuels is gathering pace. Recent international agreements such as COP26 have crystallized the need to significantly scale back processes and technologies that emit carbon dioxide and implement technologies that can fill the gap in energy harvesting and storage.
Lithium-ion batteries have emerged as forerunners in technological development and the sector is predicted to grow due to the demand of the transport industry for low-emissions and zero-emissions vehicles. The market is predicted to display a compound annual growth rate between 2020 and 2026 of 15%.
The global electric vehicle market is predicted to grow by 47% in the same period. According to a report by IMARC Group, the electric vehicle industry shipped 2.45 million units globally in 2020.
Waste and Recyclability Issues
However, with the growth in the electric vehicle and lithium-ion battery industries comes an age-old problem: waste. The recycling rate of spent lithium-ion batteries in 2013-2014 was 1900 tons out of 65,000 tons in Europe.
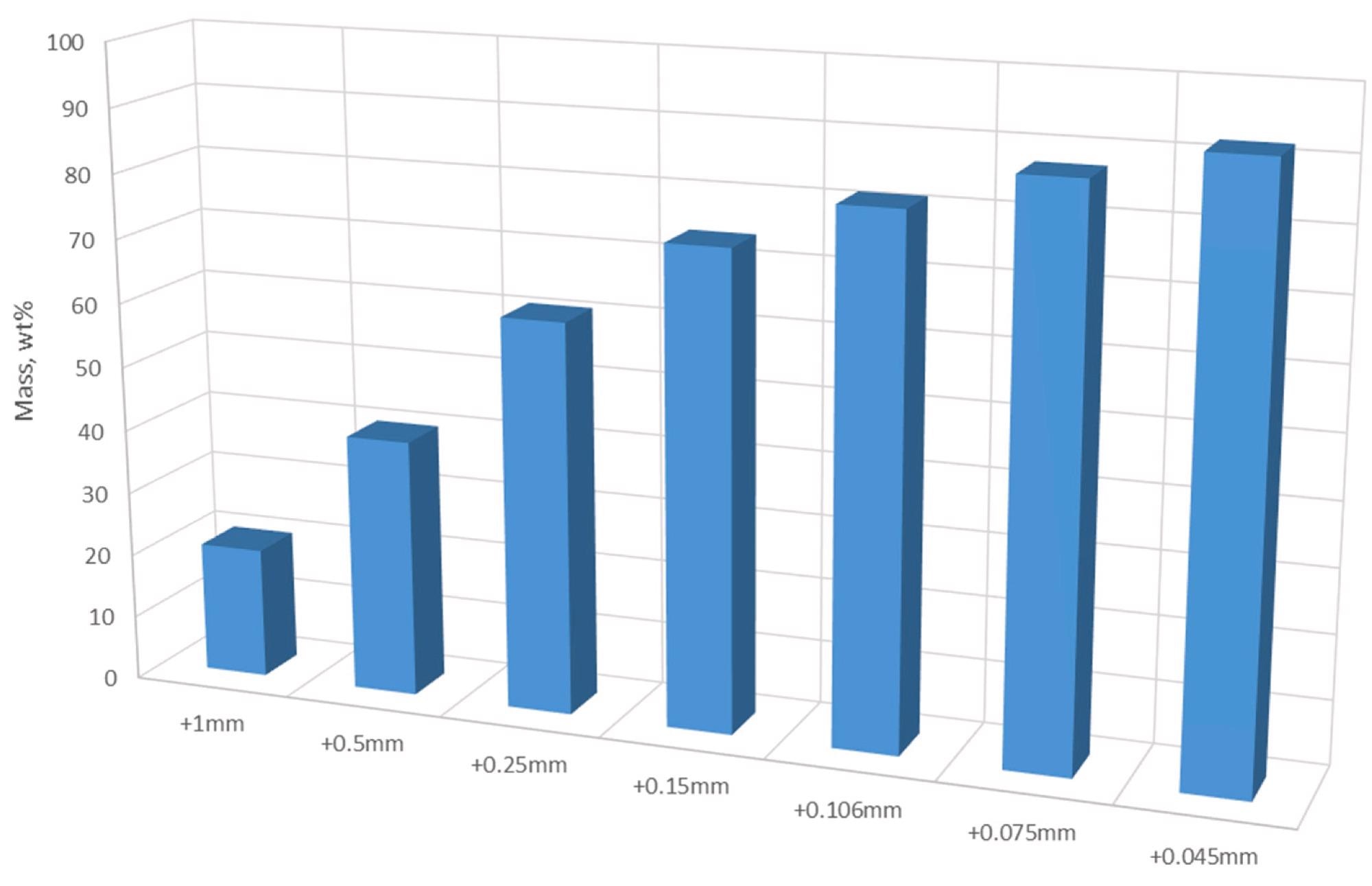
Particle size distribution. Image Credit: Yang, X et al., Materials Proceedings
Batteries contain many commercially important materials. The main current targets for recovery by pyro-metallurgical processes are cobalt, nickel, and manganese. Lithium is recovered as part of the cathode active materials. Copper, iron, and aluminum are recovered via physical and mechanical processes such as magnetic separation.
Graphite is not presently considered in many recycling strategies, is mostly lost in the recovery process. However, graphite recovery from a circular economy perspective is important for the battery industry as it is an economically important material and can increase the efficiency of subsequent metal recovery.
Recovering and Recycling the Graphite in Lithium-Ion Batteries
Recently, there has been increasing research focus on the recovery of graphite from lithium-ion batteries. A method that has been studied for graphite recovery from shredded battery materials is selective flotation, with thermal or chemical pre-treatment of the materials. Both graphite and lithium-containing metal oxides display good floatability due to the presence of organic binders such as polyvinylidene fluoride which are used as coatings.
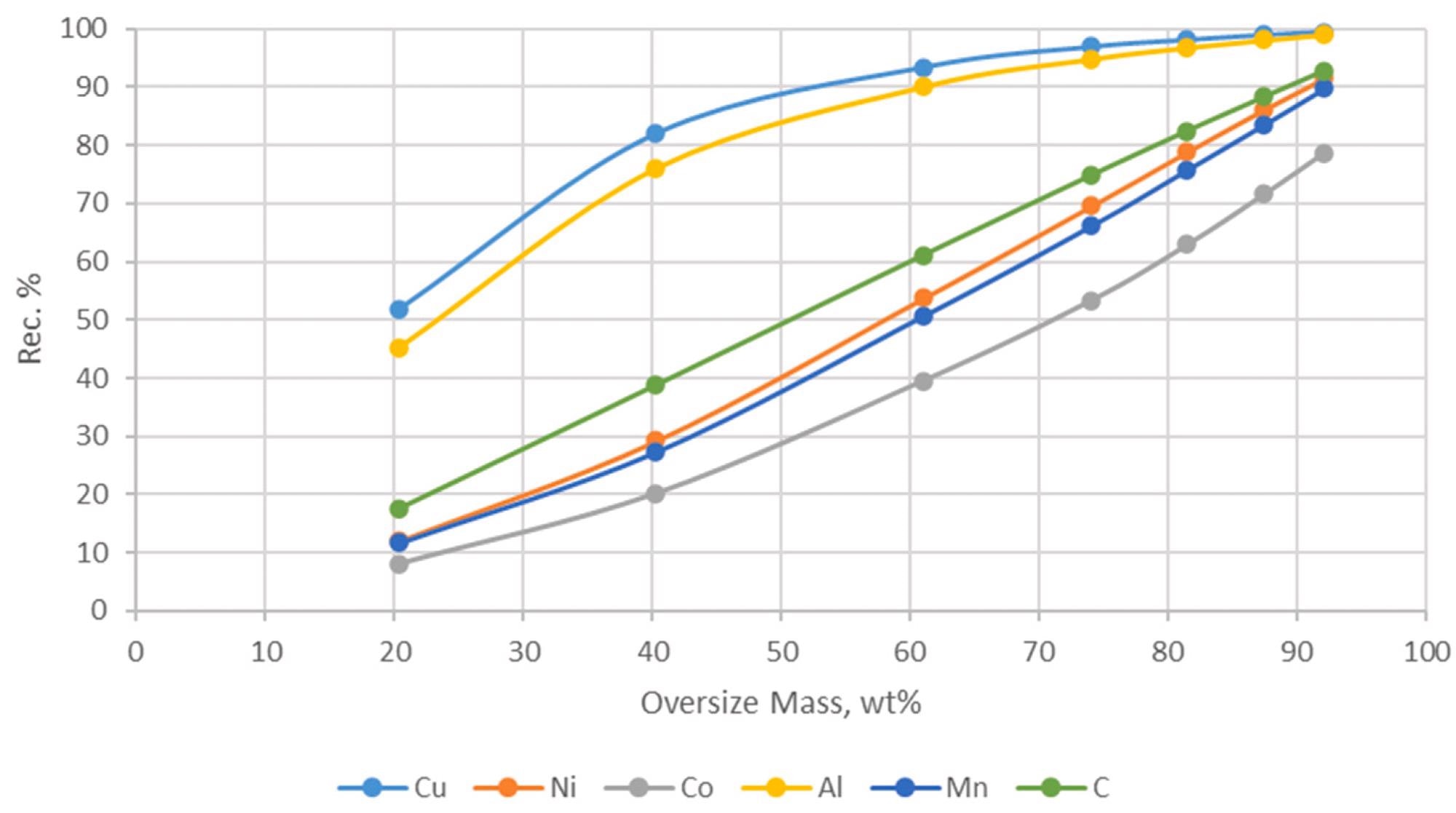
Recoveries of Cu, Ni, Co, Al, Mn, and C in the oversize fractions vs. mass yields. Image Credit: Yang, X et al., Materials Proceedings
Direct floatation of the black mass (BM) material does not selectively separate graphite, nickel, manganese, and copper, however. To remove the organic coatings before flotation, thermal treatments such as roasting or pyrolysis have been applied, which are highly effective.
The study in Materials Proceedings has investigated the efficiency of separating graphite using floatation methods from cathode active materials containing elements such as nickel, cobalt, manganese, and aluminum. The study explored the effectiveness of roasting at 350-450 oC on separation efficiency in flotation methods.
Methods and Analysis Results
Spent lithium-ion battery black mass material was procured from a recycling facility. A 50 kg BM sample of shredded material was split into samples of 500g for analysis and test work. These samples were then sieved into various fractions and their chemical composition was analyzed with XRF. Carbon contents were determined by a separate process. Samples were roasted for 30 minutes.
Results of the chemical analysis showed the main elements which have a significant concentration within the samples were aluminum, copper, cobalt, nickel, manganese, and carbon. Coarser fractions contained more copper and aluminum, whilst the finer fractions contained more nickel, manganese, and cobalt. All the fractions showed fairly even carbon distribution.
The mineralogical analysis demonstrated a complex composition, but graphite and the four lithium-containing metal oxides accounted for 92-94% of the amount.
Different apertures were used to sieve the contents of the samples to classify them. The results of the roasting techniques displayed superior separation efficiency between carbon and metallic elements in the BM. The roasting temperature also affected the floatation and separation efficiency, with higher temperatures hindering floatation. The optimal roasting temperature was discovered to be 400 oC.
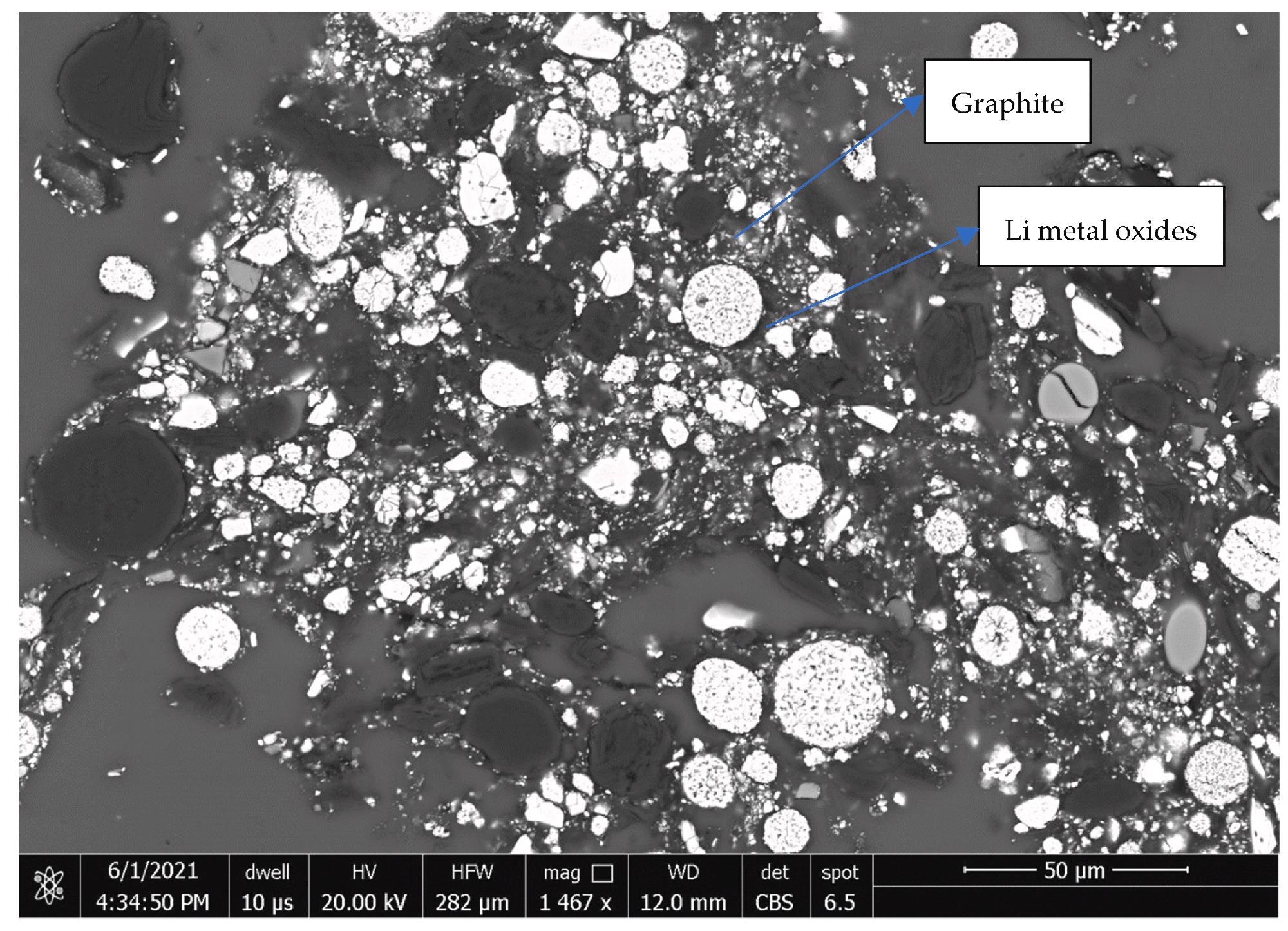
Back-scattered electron image of the fine fraction −0.25 mm. Image Credit: Yang, X et al., Materials Proceedings
The Future
By examining the flotation and separation process for graphite recovery, the team behind the study published in Materials Proceedings has demonstrated that roasting as a treatment significantly improves the recovery rate from lithium-ion battery scrap black material.
This study provides information that can inform future increases in the efficiency of recovering commercially important materials from spent batteries that would otherwise go to waste, improving the sustainability of the battery industry and reducing the resources needed to meet the growing global demand for lithium-ion batteries in sectors such as the automotive industry.
Further Reading
Yang, X, Torpa, A & Kärenlampi, K (2021) Evaluation of Graphite and Metals Separation by Flotation in Recycling of Li-Ion Batteries [online] Materials Proceedings 5:1 | mdpi.com. Available at: https://www.mdpi.com/2673-4605/5/1/30/htm
Disclaimer: The views expressed here are those of the author expressed in their private capacity and do not necessarily represent the views of AZoM.com Limited T/A AZoNetwork the owner and operator of this website. This disclaimer forms part of the Terms and conditions of use of this website.