3D printing is a pivotal technology that is widely predicted to create next-generation materials with increased toughness, high-strength, and lightweight functional materials for a wide variety of applications.
Studies have shown that designing materials with biomimetic structures using 3D printing will give them outstanding strength and toughness properties. A paper published in Advanced Science has explored this subject.
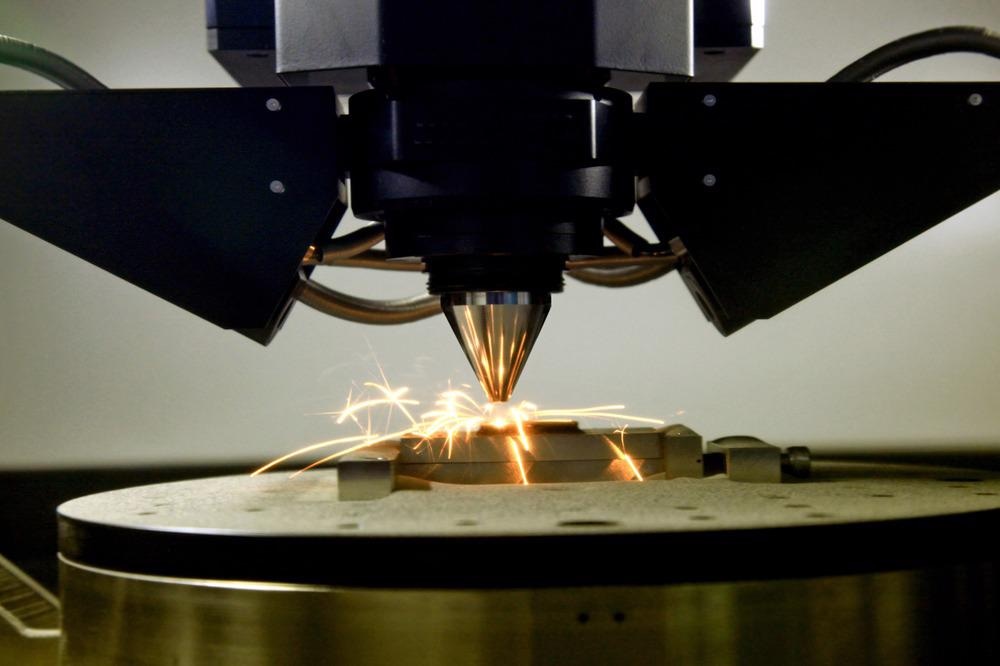
Study: Outstanding Strengthening and Toughening Behavior of 3D-Printed Fiber-Reinforced Composites Designed by Biomimetic Interfacial Heterogeneity. Image Credit: sspopov/Shutterstock.com
Fabricating 3D Printed Composites with Biomimicking Features
In recent decades there has been significant research focus on creating 3D printed composite features with improved physical and mechanical properties. Natural structures show a vast range of exquisitely detailed structures that play a variety of roles within biological systems. Structures within biological organisms include porous structures, highly organized fibrillar structures, and 2D planar structures.
Natural structures such as organs, bones, chitin, and shells have evolved over the course of millions of years to fit specific functions. Emulating them in synthetic systems has proven historically difficult, and there has recently been noteworthy progress in the field of biomimicking materials and structures worldwide. Designing truly biomimicking synthetic structures will provide them with improved properties such as strength, low density, and toughness.
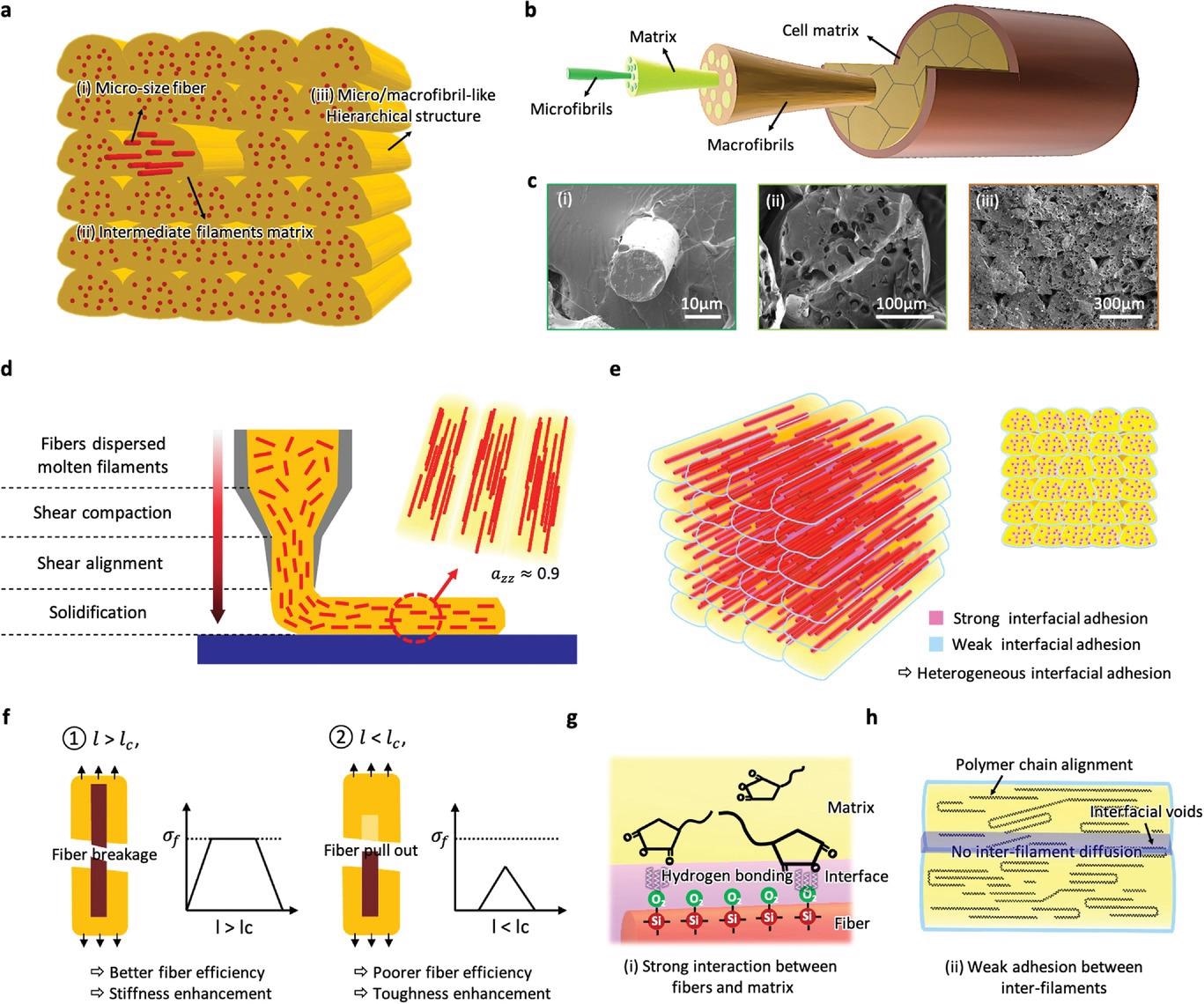
Research strategies for simultaneous improvements of strength, stiffness, and toughness from distinctive architecture by analogy with hierarchically structured nature materials. a) Schematic illustration of 3D-printed SFRP composites showing fibrous assemblies hierarchically built with individual intermediate filaments, with embedded micron-sized fibers. b) Detailed illustration of the natural micro/macrofibril hierarchical structure of biological materials. c) Scanning electron microscopy images of the sequential additive architecture of 3D-printed composites showing structural hierarchy: i) embedded micron fibers, ii) the intermediate filament matrix, and iii) the hierarchical structure. d) Process-induced spontaneous fiber alignment. 3D printing leads to a high degree of material orientation in the printing direction, especially the alignment of embedded fibers with a high degree of orientation reaching azz = 0.9 (Z direction orientation value). e) Contribution of a heterogeneous interfacial adhesion system to biomimetic toughness behaviors. f) The interfacial adhesion of composites is highly dependent on the critical embedment fiber length; the fiber pull-out mechanism, which occurs primarily for l < lc, and the fiber breakage mechanism, which occurs primarily for l > lc. Stress-position profiles show the representative curves when the fiber is ① greater than lc and ② less than lc. σf is the ultimate tensile strength of the fiber. g) Strong interfacial adhesion between the fiber and the matrix was achieved with effective interfacial treatments. h) Weak interfacial adhesion between inter-filaments spontaneously derived from low inter-diffusion of polymer chains at the interface. Image Credit: Yu, S et al. , Advanced Science
Recent studies have taken advantage of 3D printing. 3D printing can fabricate materials with superior orientation and multi-level complex architectures. Additionally, it is a low-cost and environmentally friendly process. These methods provide a route toward materials with superior properties, composition, and structure.
A recent success in the field of 3D printed biomimicking structures is the fabrication of a seashell-inspired structure. An electrically assisted printing process was utilized to fabricate highly aligned graphene nanoplatelets with a polymer mortal material. The results of the study demonstrated a robust material with seashell-like mechanical properties which exceeded expectations.
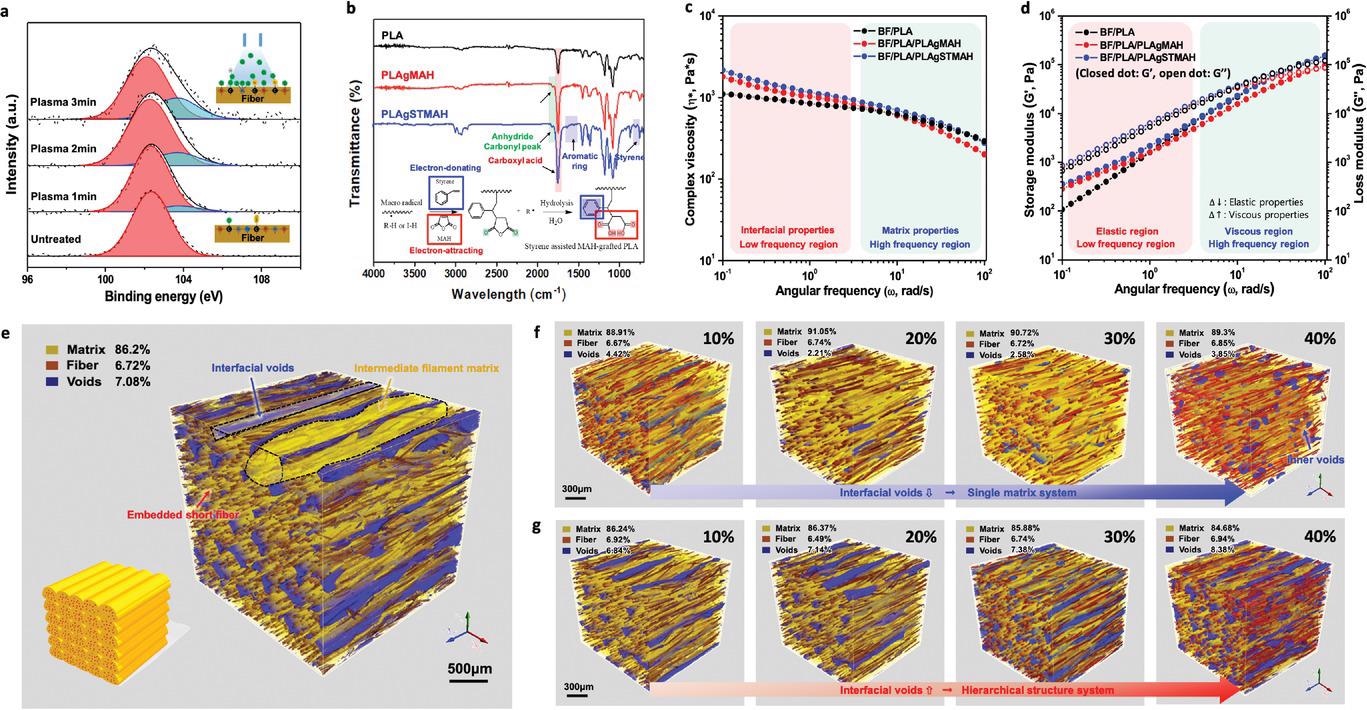
Material designs for strong interfacial adhesion between the fiber and the matrix. a) Formation of O2/Ar plasma induced-polar groups at the fiber surface. The inset describes the change in chemical compositions on the fiber surface before and after plasma treatment. b) Formation of hydrophilic grafting functional molecules in the polymer matrix. The inset shows the mechanism of ST-assisted grafting polymerization of MAH to PLA. (See Figure S1, Supporting Information, for detailed mechanism.) c) Complex viscosity (η*, Pa*s) of the molten composites with respect to the frequency. d) Storage modulus (G′) and loss modulus (G″) curves with respect to the frequency. e) Representative 3D tomographic images of hierarchical SFRP composites inherently induced by the 3D printing process. f, g) Resultant tomographic images comparing the effects of rheological modification on the internal microstructure of the composites according to the contents of 10, 20, 30, and 40 wt% of f) PLA-g-MAH and g) PLA-g-STMAH. (The formation of a high number of isolated inner voids is attributed to poor processing conditions and is accompanied by a significant change in the viscosity.) Image Credit: Yu, S et al., Advanced Science
Creating Biomimicking Fiber-Composite Structures with Interfacial Heterogeneities Using 3D Printing Methods
The research published in Advanced Science has focused on the use of industrial materials. The specific materials it has focused on are fiber-reinforced composites. The use of short fiber-reinforced composites has been extensive in several industrial applications and these materials show promise for creating highly practical functional architectures. These materials are attractive because they possess multi-scale hierarchical microstructures.
Using these materials can help realize some intriguing hierarchical structures which consist of well-aligned intermediate filaments in the printing direction as well as highly orientated short fibers which provide reinforcement for the printed structures. Due to these factors, these composite materials display highly anisotropic mechanical behaviors with a remarkable increase in strength along the optimal direction.
These composite materials have a unique architecture that is uniquely driven by the printing process. Furthermore, they can be understood in the context of inspiration from natural structures. A natural comparison that can be drawn is the anisotropic mechanical behavior of bamboo. In this natural material, fractures display specific patterns, with the orientation of bamboo fibers significantly affecting crack development.
Most studies have recognized that strength reinforcement is positively influenced by the high degree of orientation of the reinforcement elements in 3D printed fiber composites. The authors of the study have stated that 3D printing, by precisely adjusting fiber orientation, can fabricate sophisticated microstructures. This determines the mechanical strength of the printed composites.
Imperfect interfacial void formation is typically undesirable in extrusion 3D printing. This can affect delamination and crack growth. However, in the context of biomimicking materials and nature-inspired engineering, this is not necessarily a drawback., although it can be undesirable. Strategic incorporation of voids into the load paths can help realize engineering solutions that imbue effects such as crack blunting and crack deflection in the printed composites.
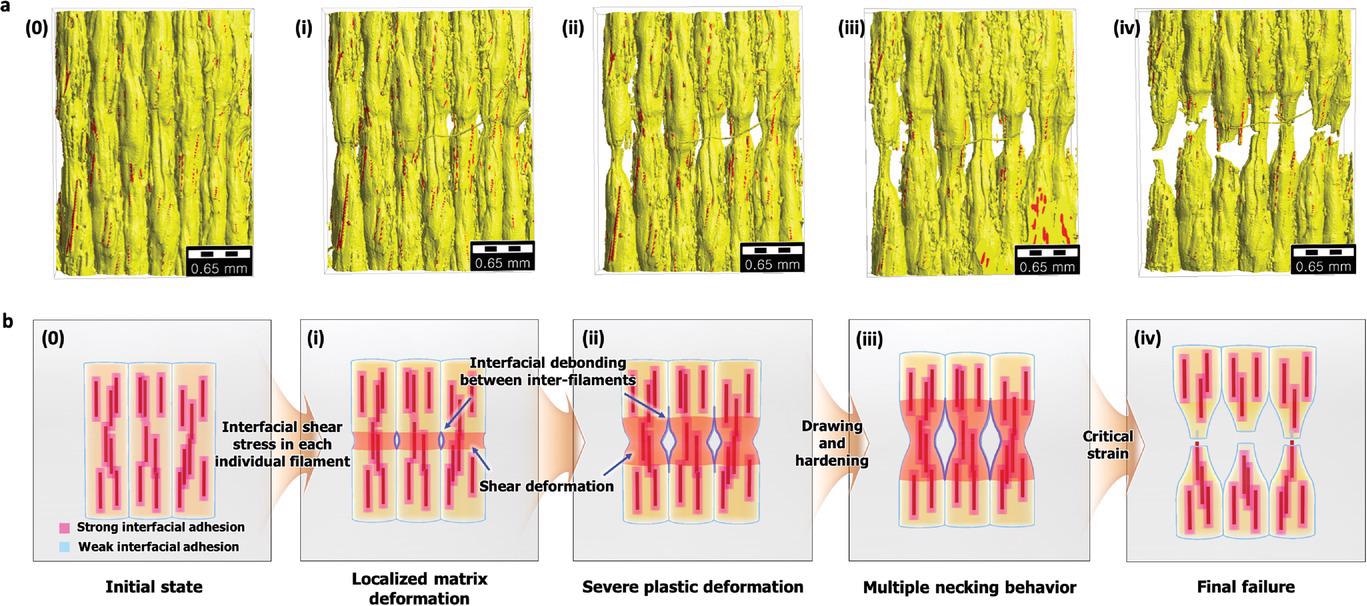
Detailed illustration of representative failure mechanism of 3D-printed hierarchical BF/PLA/PLA-g-STMAH composites. a) 3D tomographic images showing progressive failure process at each tensile loading sequence; (0) initial state, (i) first load sequence, (ii) second load sequence, (iii) third load sequence, and (iv) final failure. b) Comprehensive description of deformation and fracture progression. Image Credit: Yu, S et al., Advanced Science
Studying the Composite Material’s Interfaces
To date, most studies have concentrated on the structural construction of these composites without giving much consideration to the interfaces within the materials. By taking a different approach, the study in Advanced Science raises critical issues in the contact interfaces between different structural elements such as fiber-filament and fiber-fiber interfaces.
The authors behind the research have presented a synergistic mechanism for enhancing the mechanical properties of 3D printed composite materials which possess interfacial heterogeneities. The presence of interfacial voids and highly aligned fibers help the material to behave in the same way as natural analog structures.
Unique toughness and strength properties are yielded in the synthetic composite materials. The interfacial heterogeneity between hierarchical interfaces improves the material’s toughness.
Additionally, the 3D printed composites presented in the research display properties such as elongation rate and stiffness as well as strength and toughness. The material’s optimized architecture configuration can be likened to natural structures, making these composites a superior biomimicking printed material that can be utilized in many applications where superior physical and mechanical properties are required.
Further Reading
Yu, S et al. (2021) Outstanding Strengthening and Toughening Behavior of 3D-Printed Fiber-Reinforced Composites Designed by Biomimetic Interfacial Heterogeneity [online] Advanced Science | onlinelibrary.wiley.com. Available at: https://onlinelibrary.wiley.com/doi/full/10.1002/advs.202103561
Disclaimer: The views expressed here are those of the author expressed in their private capacity and do not necessarily represent the views of AZoM.com Limited T/A AZoNetwork the owner and operator of this website. This disclaimer forms part of the Terms and conditions of use of this website.