In a recent study published in the journal Metals, researchers from Spain carried out a state of art investigation on essential process parameters of magnesium laser cladding to understand the effect of different coating-substrate systems for mechanical and corrosive resistant properties.
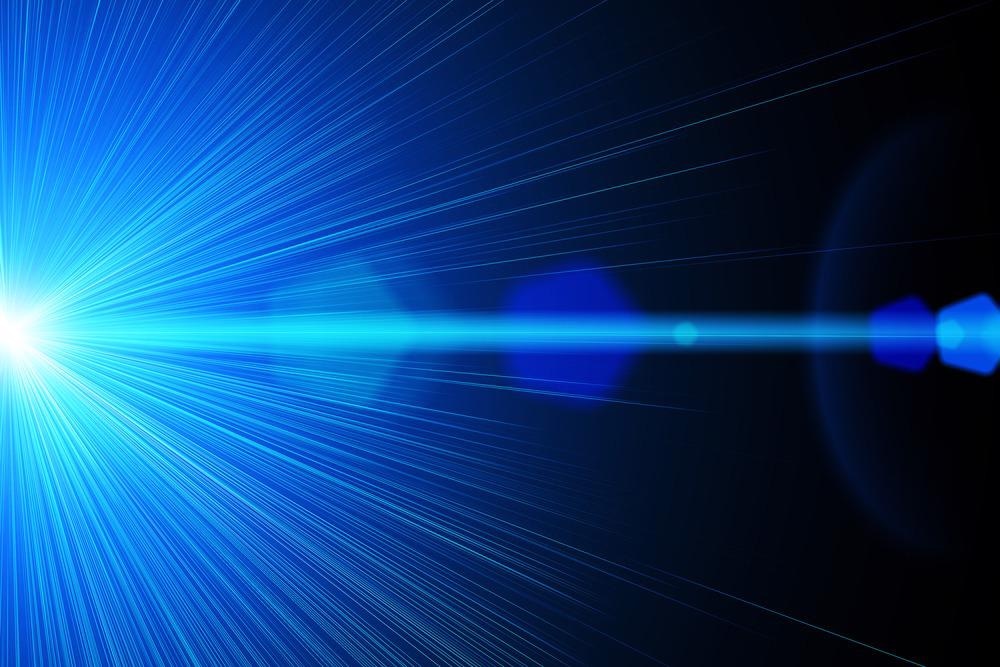
Study: An Introduction on the Laser Cladding Coatings on Magnesium Alloys. Image Credit: Juergen Faelchle/Shutterstock.com
Magnesium Alloys and Laser Cladding
Magnesium alloys are good structural materials because of their low density, which results in very high specific mechanical properties, ease of machining, and low cost. The primary constraints of magnesium alloys are their low surface characteristics and low wear and corrosion resistance. One strategy for overcoming these constraints is to use laser cladding techniques to create protective surface coatings.
![Different methods of laser cladding feeder: (a) paste feeding; (b) powder injection; (c) wire feeding; (d) preplaced powder [6].](https://www.azom.com/images/news/ImageForNews_57678_16394838827067744.jpg)
Different methods of laser cladding feeder: (a) paste feeding; (b) powder injection; (c) wire feeding; (d) preplaced powder. Riquelme, A et al., Metals
The primary advantages of laser cladding over traditional approaches include reduced substrate thermal distortion, improved surface attributes with low dilution, and improved surface quality. To obtain coatings with good mechanical properties, it is required to choose the suitable process parameters (laser power, powder feed, scanning speed, and properties of the substrate and the powder)
Laser fabrication methods are divided into three types: laser cladding, laser alloying, and laser glazing. Laser cladding is a coating manufacturing technology that uses a laser as an energy material to generate low porosity and improved coatings on metals. The laser alloying technology simultaneously simulates the feeding material and the substrate, resulting in a homogeneous alloyed metal. Laser glazing is melting only a small portion of the substrate and rapid cooling, resulting in amorphous crystals.
This study examines the current processes in magnesium laser cladding and investigates the effect of the most critical fabrication parameters on the interaction of various coating-substrate systems employed on mechanical properties and corrosion resistance.
Methodology
The coating process was carried out using a laser cladding system, which includes a laser (diode laser or Nd: Yag laser or CO2 laser), excimer laser, and a feeding material, which is sprayed with a carrier gas and coaxial with the laser beam. The feeding material is a spherical powder sprayed with a carrier gas through a cladding nozzle. The cladding nozzle laser is linked to a motor control system, typically consisting of a CAD (computer-assisted drafting) system and a motion robot or an x-y motion table.
![Inputs, outputs and process parameters of laser cladding [6].](https://www.azom.com/images/news/ImageForNews_57678_16394839007878704.jpg)
Inputs, outputs and process parameters of laser cladding. Riquelme, A et al., Metals
Effect of Process Parameters
According to the various studies, input parameters impact laser cladding of magnesium alloys and to get high-quality coatings, the optimal combination of scanning speed and laser power must be determined. The coating geometry, dilution, melting, and heat impacted zones are all affected by the focal position to the substrate surface. The wavelength of the laser beam has a significant impact on metal reflectivity-absorptivity. The energy absorbed by the substrate expands the dilution zone, affecting the microstructure and characteristics of the coating.
The output laser cladding parameters are determined by the input factors such as dilution rate, coating geometry, and the existence of cracks and pores, which are primarily governed by the laser, motion device, and feeding material characteristics.
Most pure metal, binary, and ternary alloy coatings comprise Mg-Al because Al increases Mg hardness; however, adding Al to Mg alloys reduces corrosion performance. The presence of Al enables some of the phases generated to conform to the equilibrium Al-Mg phase diagram, and the presence of other metals causes Al-metal or Mg-metal phases to form.
The study of high entropy alloy (HEA) coatings (AlCoCrCuFeNi coatings) on pure magnesium reveals that dilution between the substrate and the coating help detect some CuMg2 dendrites.
The studies on the fabrication of ceramic coatings on magnesium alloys suggest that ceramics have a low affinity to react with the magnesium substrate, form other compounds, refine the substrate's microstructure, and improve the substrate wear resistance and corrosion resistance.
Conclusions
The researchers studied the effect of process parameters on magnesium laser cladding. According to researchers, the most researched matrixes are aluminum-based alloys, and frequently used ceramic reinforcements have particle morphology because these composite coatings combine improved tribological properties and high corrosion resistance.
Understanding how different coating manufacturing parameters affect the final surface properties of magnesium alloys is critical for their use in a wide array of manufacturing situations. In the future scope, multiple processes such as welding with laser cladding or three-dimensional printing with direct laser deposition can be integrated as an extension of the laser cladding process.
References
Disclaimer: The views expressed here are those of the author expressed in their private capacity and do not necessarily represent the views of AZoM.com Limited T/A AZoNetwork the owner and operator of this website. This disclaimer forms part of the Terms and conditions of use of this website.
Source:
Riquelme, A.; Rodrigo, P. An Introduction on the Laser Cladding Coatings on Magnesium Alloys. Metals 2021, 11, 1993. https://www.mdpi.com/2075-4701/11/12/1993