A recent paper presented in the Materials journal outlines some innovative experimental research into the development of 3D structures with an SLA additive technique and Durable Resin V2.
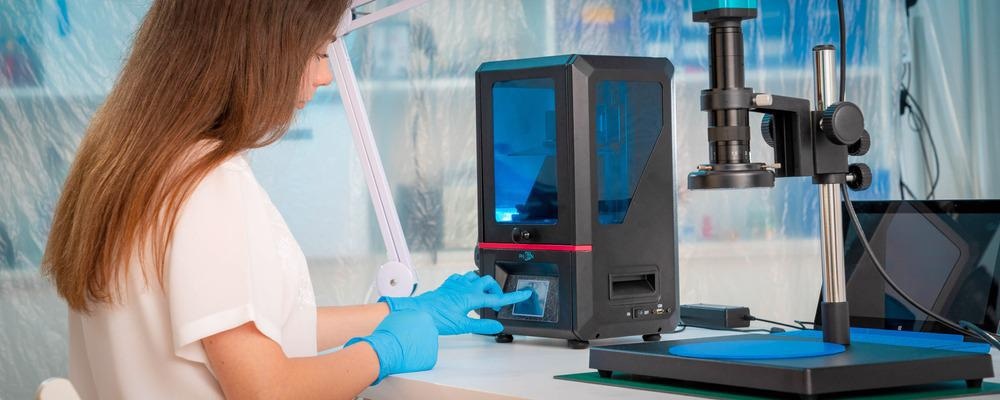
Study: Experimental Research of Selected Lattice Structures Developed with 3D Printing Technology. Image Credit: luchschenF/Shutterstock.com
The paper’s primary goal was to compare and evaluate the compression curves, deformation processes, and energy-absorption parameters of topologies exhibiting a range of different characteristics by subjecting these to a quasi-static axial compression test.
Micro-lattice structures generated via additive manufacturing provide a distinct combination of physical properties. They are lightweight while exhibiting high levels of impact resistance, compressive strength, and energy absorption.
It is also possible to alter and optimize these structures’ properties by changing their shape, meaning that they can be adapted to accommodate a range of applications and settings.
The authors cite a number of studies that evaluate the impact of alterations in the relative density of lattice structures that had been printed using a 3D incremental stereolithography method.
Lattice structures designed in Autodesk Netfabb 2021, with the following topology: (a) Grid; (b) Hexagon; (c) Star; (d) Tetra; (e) Trabecular, together with enlarged beam-like shapes. Image Credit: Bogusz, P et al., Materials
It was determined that a uniform structure with a homogeneous relative density distribution offered the highest initial stiffness of all printed shapes, but a graded design with differences in relative density would notably improve the stiffness and energy absorption capacity of lattices destined to be subjected to high compressive stresses.
Ongoing research and analysis are required to determine the most beneficial design for a myriad of applications, as well as ensure these structures offer robust mechanical properties.
In order to advance this area of work, the authors evaluated five types of beam-like structures that had been printed via stereolithography (SLA) and Durable Resin V2.
Each of these structures exhibited regular-cell type topologies with periodically interconnected and repeating elementary cells, and while they maintained relatively basic designs, it was ensured that their topological characteristics were as distinct and flexible as possible.
The structures themselves were generated using the Autodesk Netfabb 2021 software. The different types of 3D printed structures were described by the authors as Grid, Hexagon, Star, Tetra, and Trabecular.
Each structure was comprised of interconnected beams with circular cross-sections of equal nominal diameters. Two flat faceplates were printed on the faces of the samples on the top and bottom. A total of five specimens was tested for each structure, meaning that a total of 25 specimens was investigated overall.
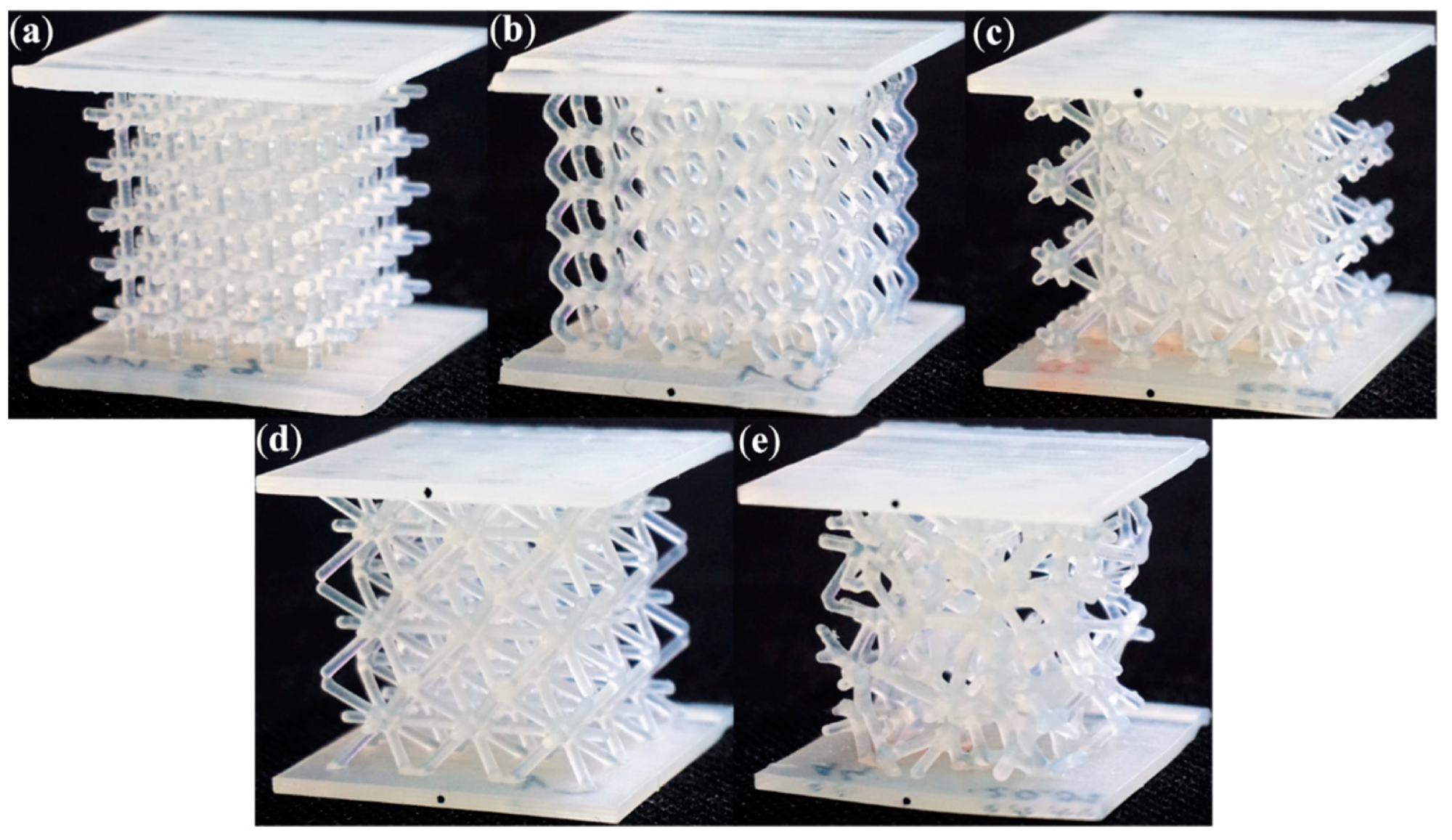
Photographs of the printed structures: (a) Grid; (b) Hexagon; (c) Star; (d) Tetra; (e) Trabecular. Image Credit: Bogusz, P et al., Materials
Once they had been generated, the structures were subjected to a quasi-static axial compression test and their fundamental material and energy-absorbing properties were elucidated via recorded compression curves acquired during testing. The beams’ deformation processes were also compared.
The authors found that individual structures’ print quality was largely determined by their specific topology and its orientation in the printer workspace. For example, it was noted that the highest rate of printing error occurred when working with a trabecular structure while the lowest occurred when working with a grid structure. Meanwhile, it was noted that star and tetra topologies were less sensitive to print quality issues.
The study also found that grid and star topologies exhibited the most substantial initial local force extremes and also the highest stiffness in terms of the linear range.
Perhaps most notably, it was shown that when working with structures containing beams that were aligned with the load axis, the application of a higher load was necessary to shorten these. Once the beams had buckled and stability was lost, a measurable decrease in force was observed. This was found to be especially the case for a grid topology, which exhibited the highest maximum force and a steep reduction.
Because the hexagon and tetra topologies under investigation did not include beams oriented in the load axis, their transition from the linear part of the compression curve was found to be very smooth, likely due to their capacity for bending.
An analysis of the various structures’ energy-absorbing parameters revealed that star and hexagon topologies performed the best in terms of compression resistance, with the trabecular topology also performing admirably. Conversely, the tetra topology performed the worst in this respect.
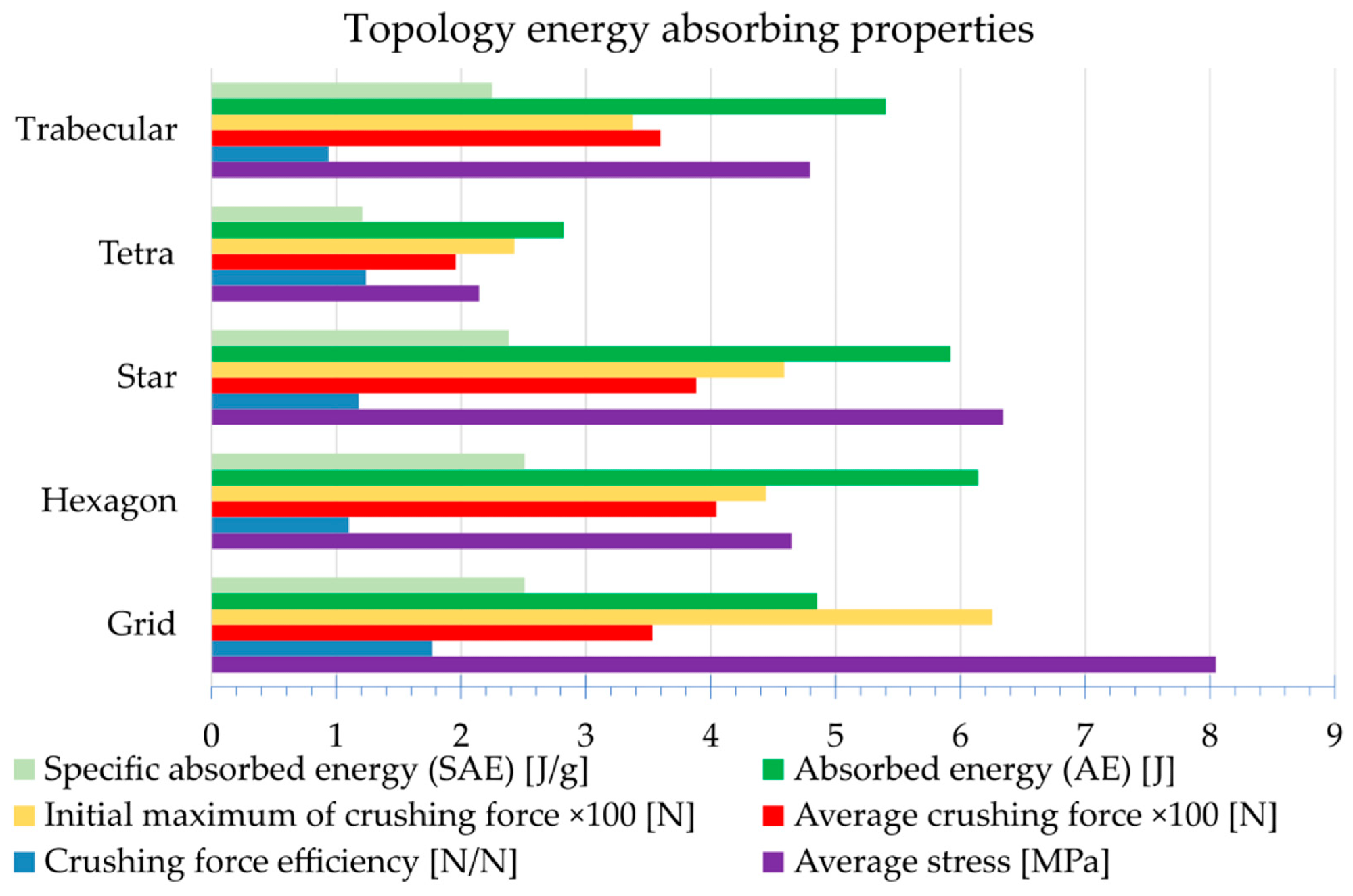
Graphical comparison of the energy-absorbing parameters of the topologies studied. Image Credit: Bogusz, P et al., Materials
The authors found that the grid structure was highly resistant to crushing force, primarily due to its initial force extremum.
This work adds to a growing body of research into lattice structures and their applications. These materials have huge technological potential, particularly in aviation, automotive, aerospace and other industries where it is essential to strike a careful balance between structural strength and component weight – potential which is only improved by the utilization of additive manufacturing processes.
Ongoing and rapid developments in modern industry are fueling the search for unconventional technological solutions to an array of structural challenges.
The most durable and rigid mechanical structures must be achieved with the lowest possible weight, prompting ongoing research into materials and complex spatial structures produced using additive manufacturing methods.
References
Bogusz, Paweł, Arkadiusz Popławski, Michał Stankiewicz, and Bartłomiej Kowalski. 2022. "Experimental Research of Selected Lattice Structures Developed with 3D Printing Technology" Materials 15, no. 1: 378. https://www.mdpi.com/1996-1944/15/1/378
Disclaimer: The views expressed here are those of the author expressed in their private capacity and do not necessarily represent the views of AZoM.com Limited T/A AZoNetwork the owner and operator of this website. This disclaimer forms part of the Terms and conditions of use of this website.