In a recent paper published in the journal Materials, researchers from China prepared thermal interface material with magnetically aligned carbon fibers for heat management in electronics packaging.
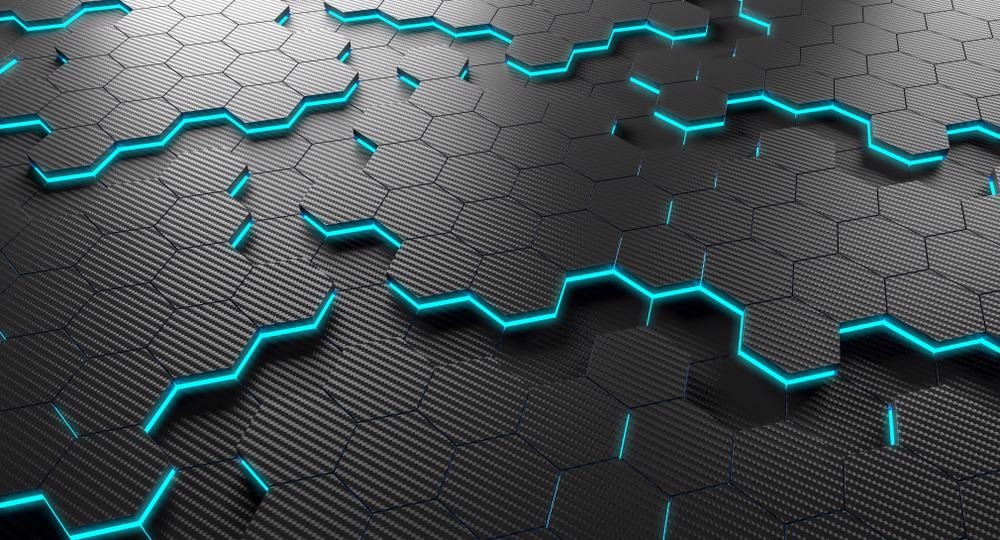
Study: High-Performance Thermal Interface Materials with Magnetic Aligned Carbon Fibers. Image Credit: gualtiero boffi/Shutterstock.com
Thermal Interface Material
Thermal interface material (TIM) is a thermal management material used in electronic packaging to fill the gap between the contact interface of heat sources and heat sinks. One of the essential properties required in TIMs for effective heat transfer is high intrinsic thermal conductivity. Additionally, low hardness is also significant for achieving high performance in TIMs because it can help the TIMs adapt to the topography of the mating surface and improve interfacial heat transfer.
However, achieving low hardness and intrinsic thermal conductivity simultaneously is difficult in TIMs because increasing the filler content improves thermal conductivity but decreases the hardness. Hence, a high-performing microstructure with low filler loading is required to achieve improved heat management in TIMs.
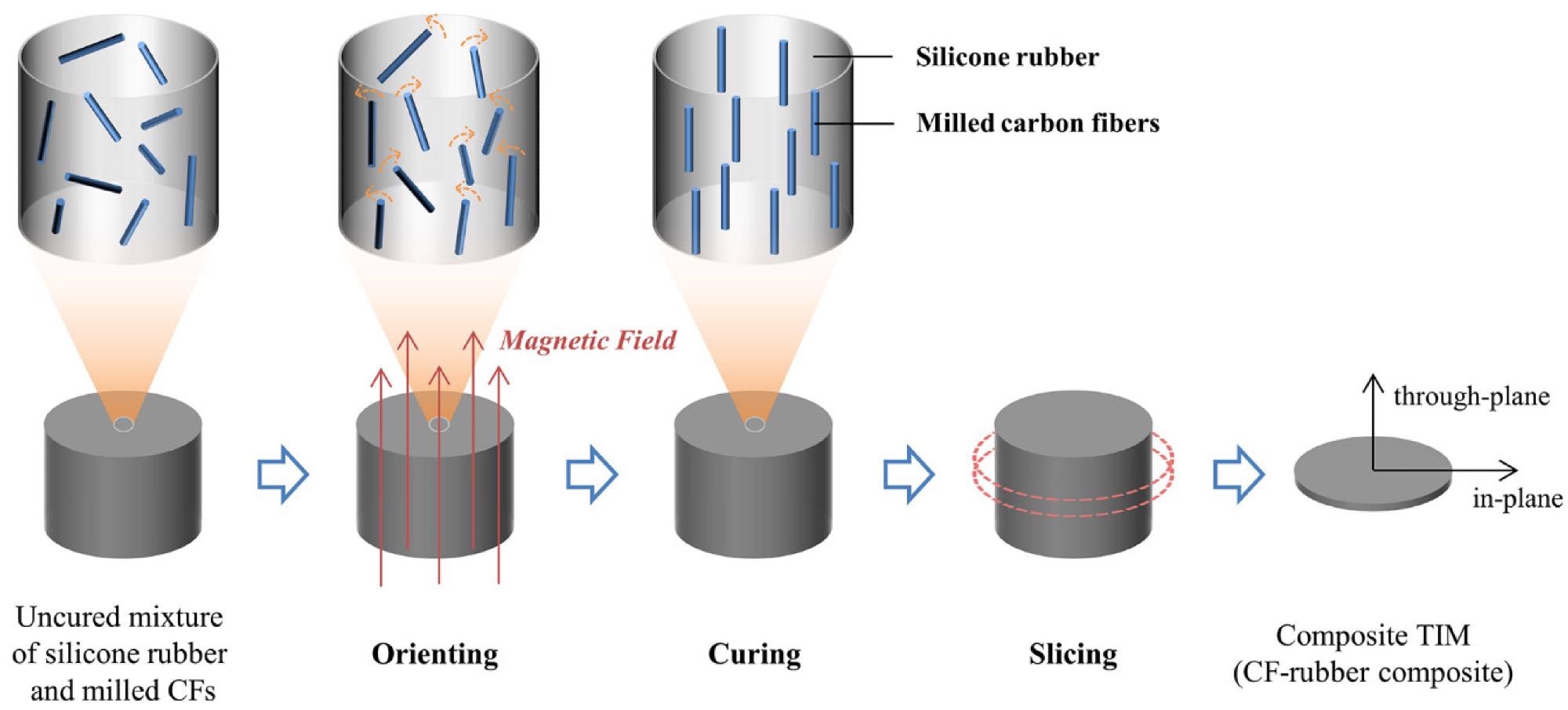
Schematic illustration of the preparation process of CF–rubber composites. Image Credit: Wu, Q et al., Materials
In the present study, researchers used a high magnetic field to align milled carbon fibers (CFs) in a silicone rubber matrix. Furthermore, an experimental study and a theoretical analysis were conducted to investigate the relationship between magnetic field density, CF alignment degree, and the properties of the resulting composites (CF-rubber composite).
The Study
For this study, TIMs were manufactured using the magnetic alignment process. To begin with, an uncured sample of CFs and silicon rubber was produced by adding CFs to silicone rubber and mixing them in a planetary centrifugal mixer. Then, the uncured mixture was placed in the bore of a cryogen-free superconducting magnet. Until the mixture was fully cured, the magnetic field direction was kept parallel to the uncured sample's thickness.
The researchers used ultrasonic cutting (in-plane direction) to achieve the required thickness of TIMs. In addition to this, they made some samples by cutting along the through-plane direction for thermal conductivity measurements. For comparison, reference samples were developed without the use of magnetic alignment.
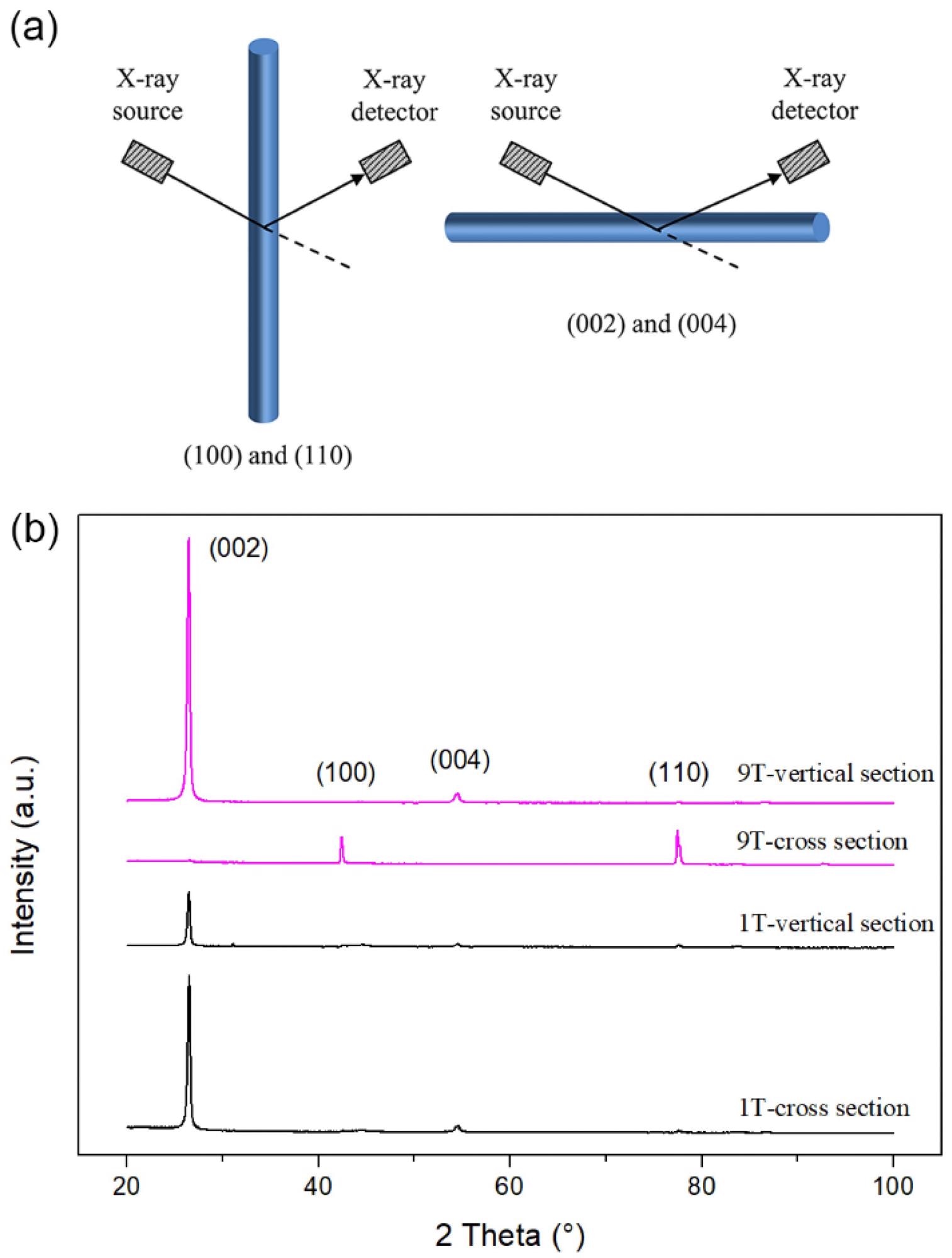
XRD analysis of CF–rubber composites. (a) Illustration of alignment effect of CFs on XRD patterns; (b) XRD patterns of 1 T and 9 T samples in vertical-section and cross-section. Image Credit: Wu, Q et al., Materials
Post preparation, it was observed that in the uncured mixture, the CFs were distributed in the silicone rubber at random. Additionally, the CFs gradually rotated in the magnetic field's direction during the orientation process. As a result, the orientation structure was fixed when the curing process was completed.
Results
The researchers used a magnetic field (1 T, 3 T, 5 T, 7 T, and 9 T) with different magnetic flux densities to develop the CF–rubber composites. It was observed that when no magnetic field was applied, the CFs aligned along the in-plane direction. This is because, under the influence of gravity, fillers with a high aspect ratio tend to align with the substrate.
Additionally, it was also observed that the thermal conductivity of the CFs is anisotropic. The axial thermal conductivities of CFs reached 900 W/m K, but the radial thermal conductivities were only around 5 W/m K, indicating a significant difference between both the thermal conductivities of CFs. As a result, it can be determined that CF alignment is critical to the composites' thermal properties.
The developed CF–rubber composites were soft, easy to bend, and deform, indicating a low hardness value. The shore hardness results showed that the composites have a hardness ranging from 60 to 70 (shore 00).
Moreover, due to the magnetic alignment and anisotropic mechanical property of CFs, the magnetic flux density has a minor effect on the hardness of the CF–rubber composites.
The thermal management performance (TMP) analysis of CFs and the composite revealed that a composite with a higher magnetic flux density had improved TMP due to the alignment degree of CFs. Additionally, due to the magnetic field treatment, the CF–rubber TIMs conduct heat more rapidly, allowing heat-generating devices such as electronic components to operate at lower temperatures, extending their life and reliability.
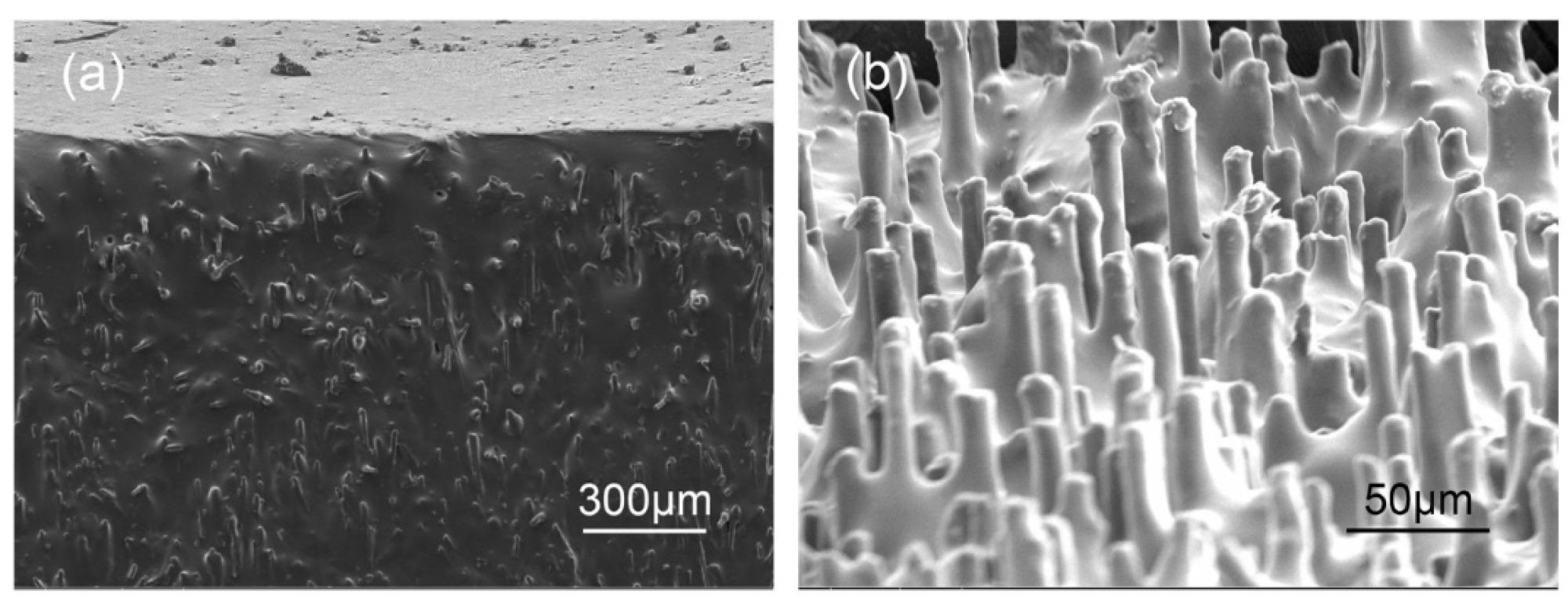
SEM images of the surface of the CF–rubber composites. (a) Before slicing (b) After slicing. Image Credit: Wu, Q et al., Materials
Conclusions
In the present study, researchers demonstrated a simple and effective solution for improving thermal interface materials' thermal conductivity and hardness.
The results indicated that the magnetic flux density was found to significantly affect the alignment of CFs and the properties of composites. The CF–rubber composites with high magnetic field treatment exhibit high anisotropy with increased through-plane thermal conductivity. Moreover, the CF-rubber composite also had low hardness, low filler loading, and a discontinuous microstructure.
If used as TIMs, the CF-rubber composite could efficiently reduce the maximum equilibrium temperature of the heat source. Hence, the CF-rubber composites discussed in the present study are ideal for thermal management applications in high-power electronic components.
Disclaimer: The views expressed here are those of the author expressed in their private capacity and do not necessarily represent the views of AZoM.com Limited T/A AZoNetwork the owner and operator of this website. This disclaimer forms part of the Terms and conditions of use of this website.
Source:
Wu, Q.; Miao, J.; Li, W.; Yang, Q.; Huang, Y.; Fu, Z.; Yang, L. High-Performance Thermal Interface Materials with Magnetic Aligned Carbon Fibers. Materials 2022, 15, 735. https://www.mdpi.com/1996-1944/15/3/735