Researchers from Korea, in their publication issued in the journal Additive Manufacturing, have efficiently modeled oxide particles in the process of additive manufacturing/3D printing.
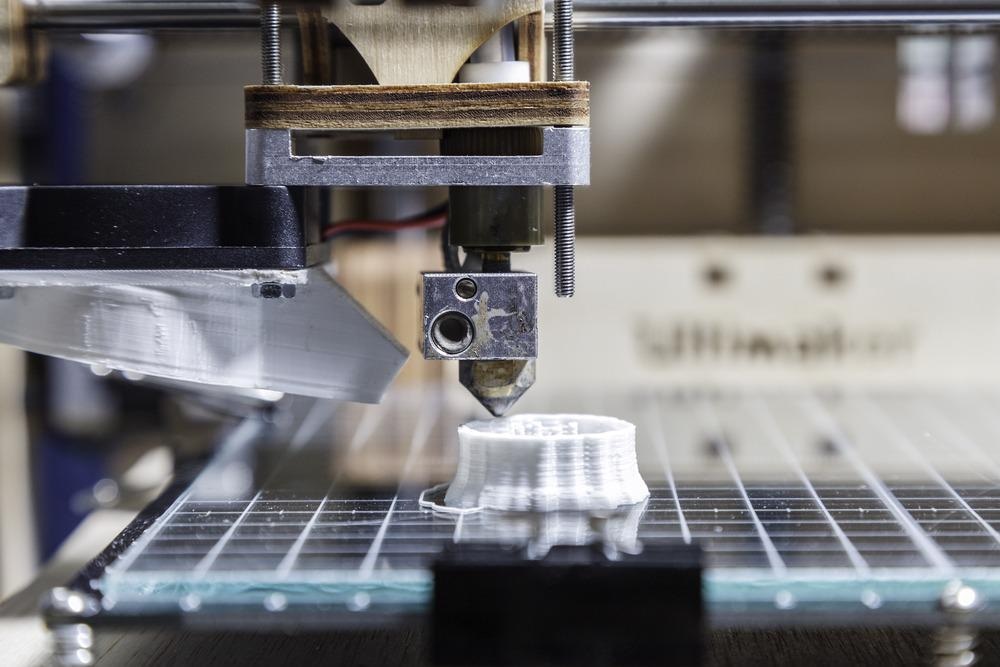
Study: Numerical modeling of oxide particle evolution during additive manufacturing. Image Credit: Sergi Lopez Roig/Shutterstock.com
What is Oxide Dispersion Strengthening?
ODS was developed to improve the creep resistance and tensile qualities of austenitic stainless steels and nickel-based alloy steels for aggressive environments. Several oxide nanoparticles are incorporated in the matrix material of these ODS alloys, limiting dislocation motions and inhibiting grain densification at extreme temperatures.
In addition, the alloys display excellent resilience to neutron-induced vacuum enlargement. Because of these properties, ODS alloy is a good choice for generation-IV nuclear plant elements. Accident-tolerant fuel sheathing for power reactors and improved fusion blanketing are among the uses expected. Injection molding, particularly mechanical alloying (MA), and hot-consolidation procedures, have traditionally been used to manufacture ODS ferritic alloys.
Mechanical Alloying Process
Mechanical alloying generates a large concentration of flaws within the matrix material. These flaws efficiently trap oxygen and improve the absorption of oxygen in the matrix material. The matrix alloy is retrieved during the following hot-consolidation procedure, and completely saturated with oxygen white precipitate to produce nano-oxide characteristics or oxide microemulsion. However, because the methods are costly and the substance is nonuniform, the usage of ODS alloys has been limited.
Introduction to Additive Manufacturing/3-D Printing Process
AM creates components by continuously overlapping a tiny component called a melt pool that is formed by an elevated energy heating element such as lasers, electrical flame, or electromagnetic waves.
This feature of the AM technique enables near-net form or net-shape production and structural optimization at no extra expense. It also allows for the fabrication of ODS alloys. The melt pool's heating and cooling cycles are relatively quick (melt pool residence time ranges from 100 ms for directed-energy deposition (DED) to 1 ms for powder bed fusion (PBF).
Further Reading: 3D Printing with Aluminum
Some costly and time-consuming operations of traditional powder metallurgy can be categorised into three or fewer steps if ODS is manufactured utilising AM. ODS products, in theory, may be simply scaled up to any size. As a result of these factors, AM is predicted to significantly expand the commercial application of ODS alloys in the fusion reactors sector.
What is the Need to Study Oxide Particle Precipitation?
However, for AM to achieve the same distribution fortification as typical ODS alloys, the diameter of the iron oxides in the alloys must be lowered to a few nanometres or the quantity of the oxide particles enhanced significantly. The kinetics of oxide particle deposition in the melt pool should be explored for this objective. Furthermore, the AM procedure involves multi-physics occurrences, and the melt pool's lifespan is rather short, so indirect approaches must be applied.
As a result, in the latest work, the oxide deposition mechanism was statistically simulated using the Kampmann and Wagner numerical (KWN) model.
Research Findings Regarding Oxygen and Temperature
It was found that the oxygen concentration of the melt pool fluctuates dramatically with heat. Until crystallization commenced, the oxygen accumulation in the melt pool was insufficient to induce a substantial nucleation event.
Because oxygen was refused from the solid to the liquid state due to its limited absorption in the hardened steel, the concentration of oxygen was hastened throughout solidification. The germination rate was minimal before the melt pool temperature dropped below the glass transition temperature, thus the investigation concentrated on the range of temperature between the liquidus and solidus values.
When the temperature dropped below the liquidus temperature, the nucleation speeds of all three situations rose comparably.
Processes for Increasing Oxide Precipitates Strengthening
To boost the reinforcing effect of oxide crystallites, 4 distinct methods could be regarded, including increasing the cooling rate via increased scanning rate, boosting the oxygen levels in the melt pool, reducing the temperature difference for crystallization (mush zone), and eventually lowering the range of temperature for crystallization (mush zone).
Effects on Particle size
The small decrease in surface energy from 0.4 to 0.3 N/m resulted in a reduction in particulate mass and volume. The particle density rose 16 times, and the reinforcing properties reached 389 MPa. The composition of the oxide or melt pool must be meticulously chosen to minimize the contact energy of the particulate nucleus to modify the interfacial energy. A fine morphology and enhanced stress concentration, in addition to the diffusion reinforcement from the oxide particles, will boost the material's strength.
To summarise, the development of endogenous oxide particles during two AM processes will pave the way for future reinforcing approaches.
Further Reading
Du-Rim Eo, Seong-Gyu Chung, JeongHo Yang, In-Ho Jung and Jung-Wook Cho. Numerical modeling of oxide particle evolution during additive manufacturing. Additive Manufacturing. (2021). Available at: https://www.sciencedirect.com/science/article/pii/S2214860422000380?via%3Dihub
Disclaimer: The views expressed here are those of the author expressed in their private capacity and do not necessarily represent the views of AZoM.com Limited T/A AZoNetwork the owner and operator of this website. This disclaimer forms part of the Terms and conditions of use of this website.