In a recent study published in the journal Molecules, researchers from China used a molecular dynamics simulation model to analyze the effect of different machining tool shapes on the surface quality of monocrystalline nickel nanofabrication.
Study: Influence of Tool Shape on Surface Quality of Monocrystalline Nickel Nanofabrication. Image Credit: arrideo/Shutterstock.com
Machining factors such as tool rake angle, clearance angle, and edge radius, which are often ignored compared to processing speeds, processing depths, and different crystal planes, were the focus of the study.
The results showed that the surface roughness distribution of the specimen was ‘W’ when the rake angle of the diamond tool changed from -45⁰ to +45⁰. Also, above the critical clearance angle of 8-10⁰, the workpiece temperature did not change during machining.
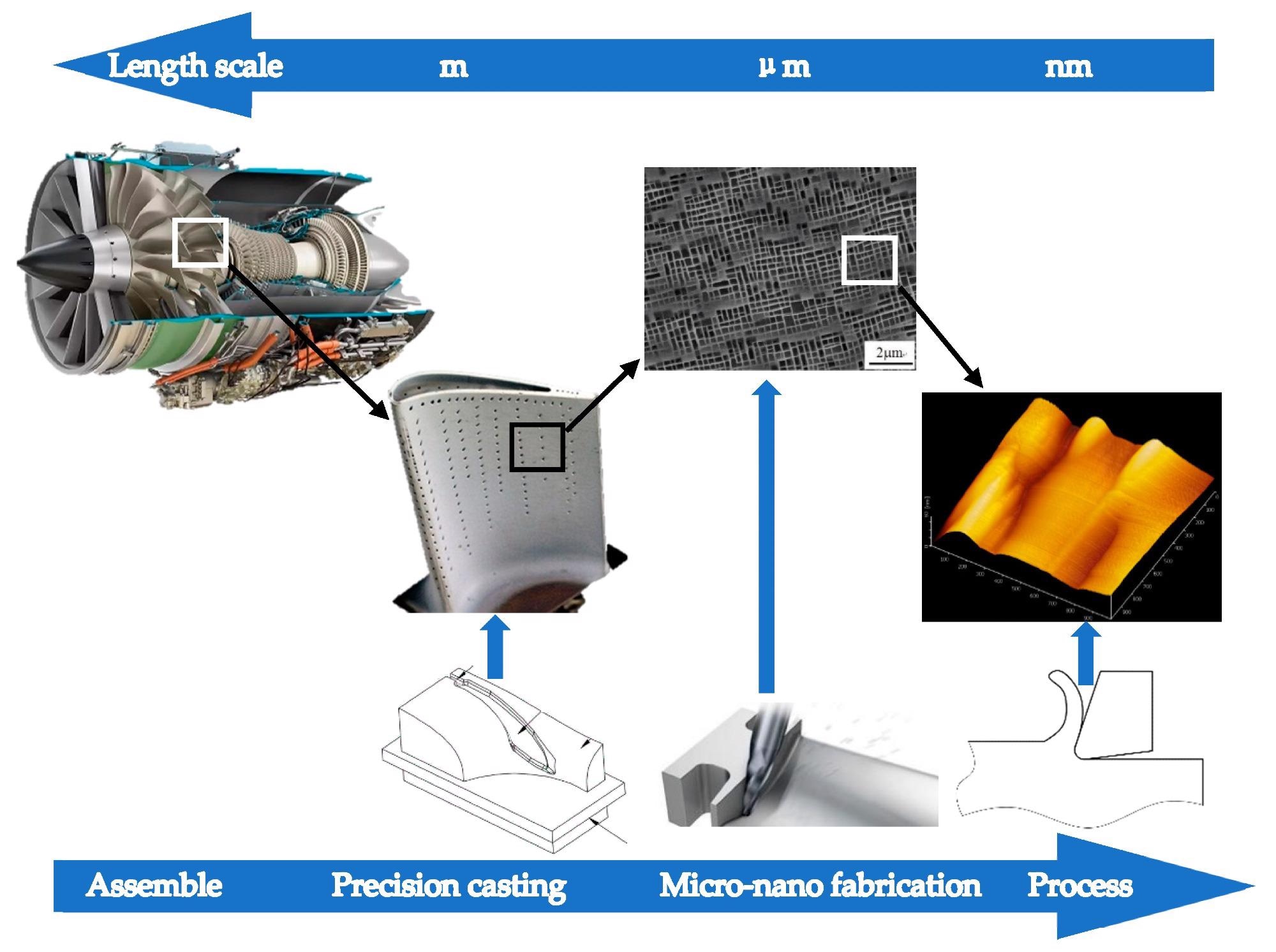
Figure 1. Ultra-precision parts of aero-engines. In the previous study of monocrystalline nickel grinding, it was found that the size of the abrasive grains had a significant influence of surface quality of monocrystalline nickel. The effect of abrasive particle diameter is essentially the reaction of an effective rake angle during processing. Thus, it can be concluded that the size and shape of the machining tool will affect the workpiece even when the size range is small to the nanometer level. Therefore, this study discusses the nanofabrication of tools with different rake angles, different clearance angles, and different tool edge radii, and their impact on the processing mechanism of monocrystalline nickel. © Ren, J. Yue, H., Liang, G., Lv, M., (2022).
Precision Machining of Monocrystalline Nickel
Monocrystalline nickel and its alloys are used in highly critical devices such as aero-engines, nuclear reactors, steam turbines, and petrochemical industries.
The manufacturing of such devices requires high precision up to the nanometer level. Thus, the focus of the nanofabrication technology exceeds beyond product and process-based factors towards machining tool-based factors such as the rake angle, clearance angle, and edge radius.
Moreover, the study of molecular dynamics is a convenient and reliable method to research ultra-precision machining and nanofabrication.
Analyzing the effect of tool geometry on surface grain structure and surface defects and heat generation (auto-annealing) are essential factors in precision machining.
Many studies suggest that the size of the negative rake angle is proportional to the shear stress, and the positive rake angle and the smaller tool tip radius can help improve the workpiece surface smoothness after processing.
For polycrystalline metals, the cutting force increases, and the friction coefficient decreases with the increase of grain size. Also, in mixed machining processes, the number of vacancy defects is proportional to the generated temperature.
About the Simulation Model
In this study, researchers used the open-source large-scale atomic and molecular parallel simulator (LAMMPS) to prepare the molecular dynamics simulation model to analyze the nanofabrication of monocrystalline nickel with different tools shapes. After that, the obtained kinetic results were visualized and analyzed using OVITO software.
They used a monocrystalline nickel specimen of size 21.2 x 10.6 x 10.6 nm, and Y direction was the periodic boundary condition.
The initial temperature was set to 293 K, while the other parameters were as follows: 200 m/s grinding speed, 1 nm depth of grind, 0-18 nm grinding length, x-[100]:y-[10]:z-[1] crystal orientation, -45⁰ to +45⁰ tool rake angle, 0⁰ to 30⁰ tool clearance angel, and 0 to 1.5 nm tool edge radius.
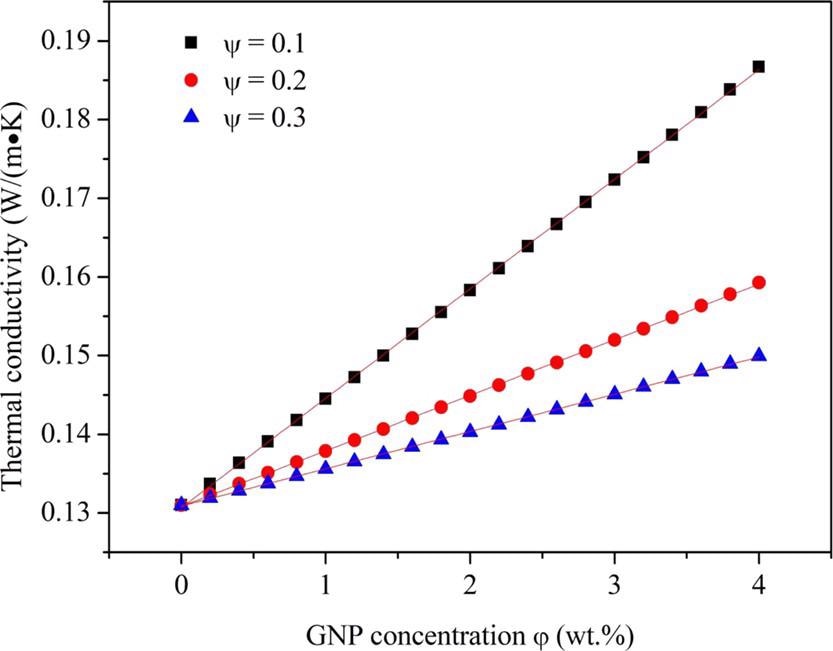
Figure 2. Chip morphology of monocrystalline nickel processed by different tool rake angles. © Ren, J. Yue, H., Liang, G., Lv, M., (2022).
Observations
When the rake angle of the tool was positive, the chips were strip-shaped owing to the relatively high sharpness of the tool.
Also, due to the low shunting point of the tool, most of the atoms in contact with the tool formed chips, rather than being squeezed under the tool after being shunted.
When the rake angle was negative, the chips were piled up owing to the extrusion of chips to the workpiece surface. The reduction of the rake angle changed the chipping process from shearing to extrusion and improved the position of the tool diversion point.
Moreover, when the rake angle was positive, especially at +30⁰, the surface atoms were subjected to shearing, which caused very few atoms to move with the tool and along the processing direction, resulting in a very smaller surface roughness value.
However, when the rake angle was negative, especially at -45⁰, the surface roughness increased sharply due to material retention on the tool's rake face.
At a constant edge radius and clearance angle, the cutting force decreased with increased tool rake angle and vice versa.
As the tool rake angle increased, the friction of the chips along the rake face also decreased. Also, the temperature of the workpiece was directly related to the cutting force, whereas the tool radius had a very low effect on temperature.
When the tool rake angle changed from positive to negative, the friction between the rake face and the chips increased, which increased the force on the chips, and more face-centered cubic (FCC) atomic bonds were destroyed.
However, the number of amorphous and surface atoms increased. The tool negative rake angle facilitated the generation of new surface energy and the energy required to produce surface defects such as dislocations, vacancies, and gaps in the material.
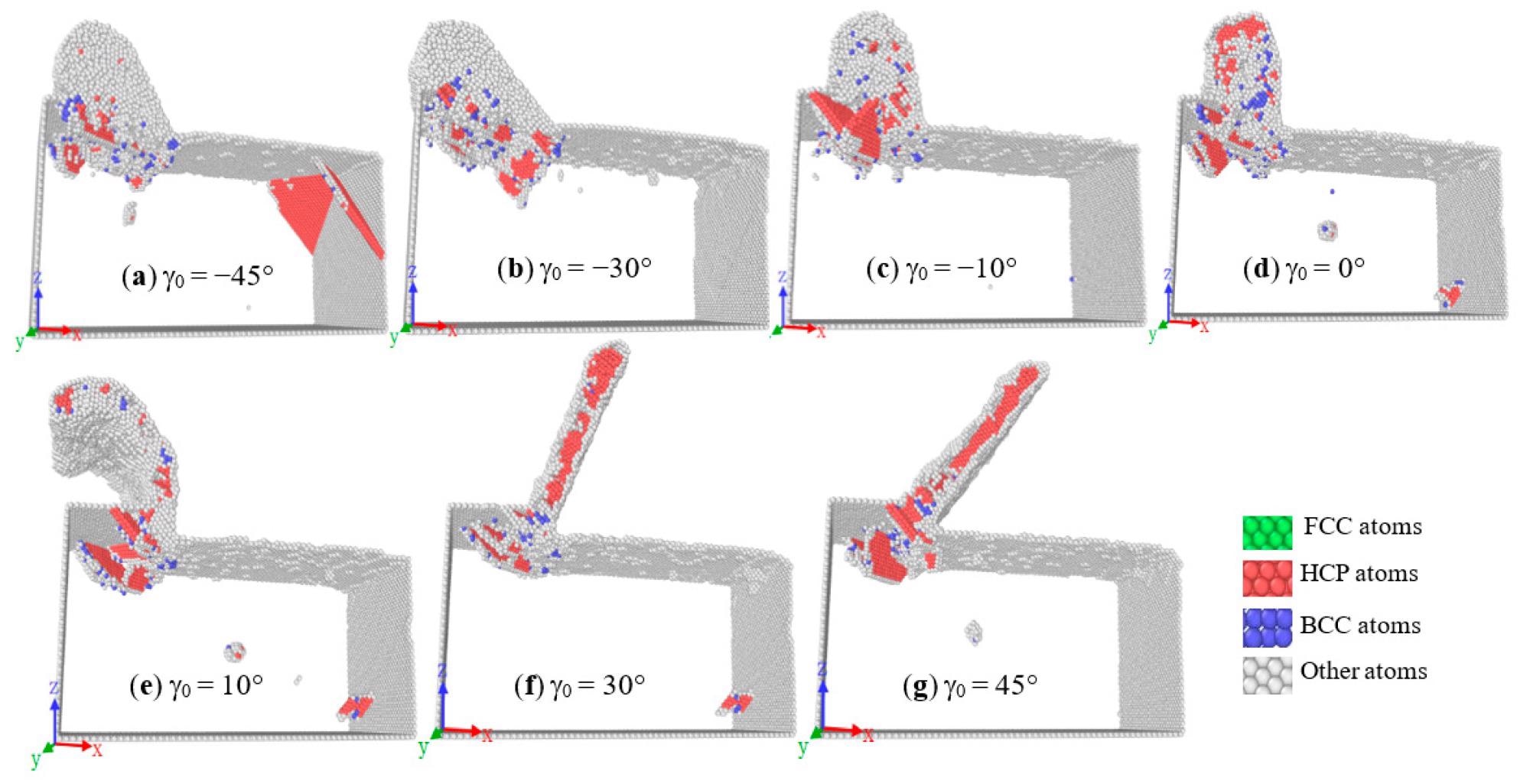
Figure 3. CAN analysis. © Ren, J. Yue, H., Liang, G., Lv, M., (2022).
Conclusions
To conclude, this study investigated the effect of tool shape on the surface quality of monocrystalline nickel nanofabrication.
The findings showed that the surface roughness value of the monocrystalline nickel fluctuated in a ‘W’ curve as the tool rake angle was varied between -45⁰ to +45⁰ during nanofabrication.
Additionally, the cutting force and temperature were highly dependent on the rake angle and mostly unaffected by the change in the edge radius.
Furthermore, the critical clearance angle of monocrystal nickel machining of 1 nm depth was 8-10⁰, above which tool clearance angle did not influence the temperature.
Keeping the tool’s back angle within the critical angle range helps reduce friction and increase the strength of the tool.
Reference
Ren, J. Yue, H., Liang, G., Lv, M., (2022). Influence of Tool Shape on Surface Quality of Monocrystalline Nickel Nanofabrication. Molecules, 27, 603. Available at: https://www.mdpi.com/1420-3049/27/3/603
Disclaimer: The views expressed here are those of the author expressed in their private capacity and do not necessarily represent the views of AZoM.com Limited T/A AZoNetwork the owner and operator of this website. This disclaimer forms part of the Terms and conditions of use of this website.