By Susha Cheriyedath, M.Sc.Reviewed by Skyla BailyJan 27 2022
A study recently published in the journal Cement and Concrete Composites demonstrated the effectiveness of reinforcing carbon fiber in geopolymer matrix composites in order to improve the mechanical properties of the composites.
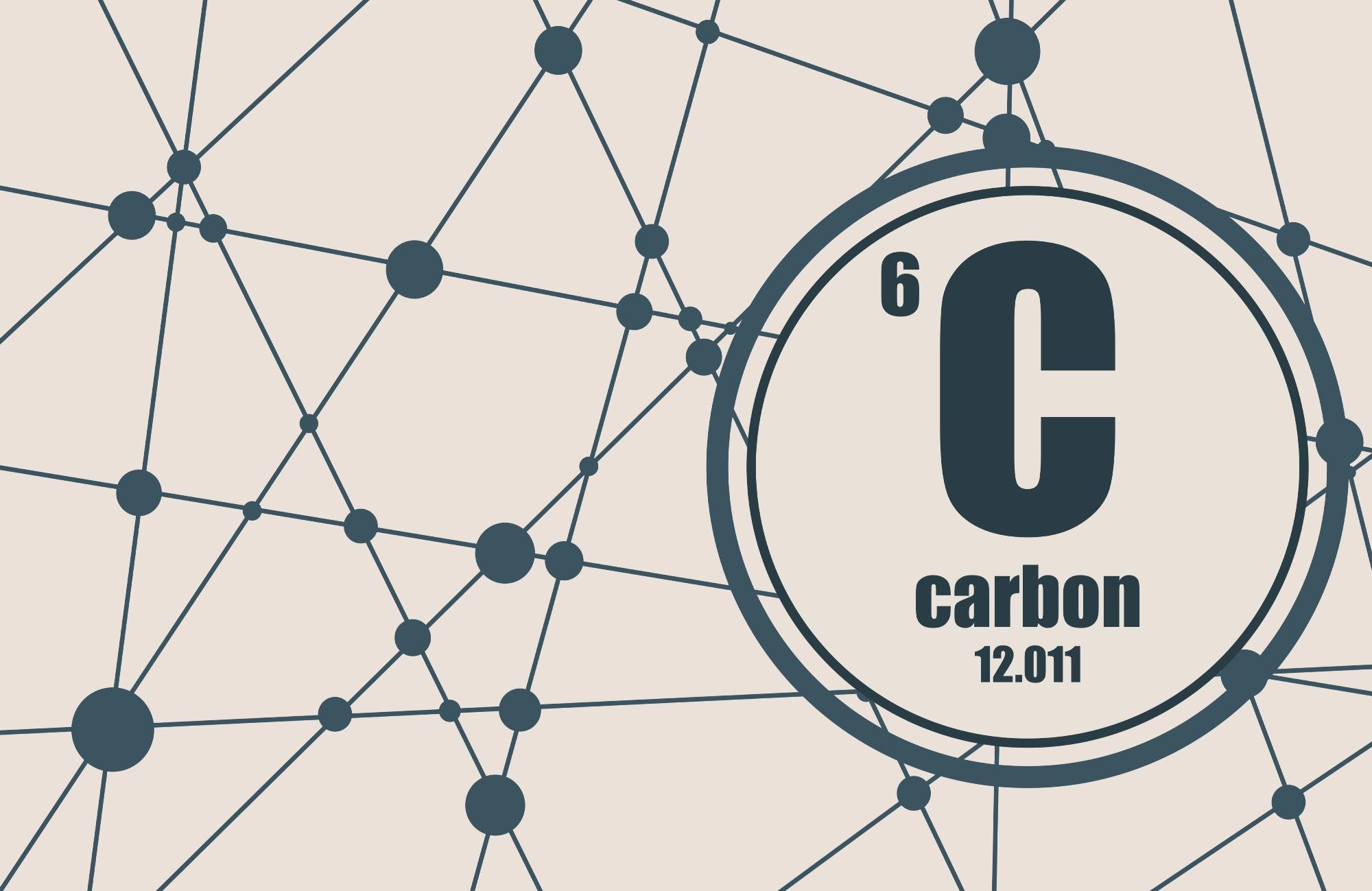
Study: Interface failure and delamination resistance of fiber-reinforced geopolymer composite by simulation and experimental method. Image Credit: GrAl/Shutterstock.com
Background
Geopolymers are primarily inorganic polymers comprising alkali-balanced binders and aluminosilicates. These polymers are chemically inert, lightweight, and can remain thermally stable for a long duration at temperatures up to 800oC without undergoing any degradation. These characteristics of geopolymers made them suitable for manufacturing components in automobile and aerospace structures that are exposed to extreme environments.
However, extreme brittleness and weak interlaminar strength of geopolymer composites hinder their adoption in industrial applications on an extensive scale. Different factors such as the crack initiation and propagation caused due to the residual stress, process-induced shrinkage, and high porosity of the polymers are responsible for the poor toughness and delamination of the composites. Delamination is referred to as interlaminar damage that causes failure in composites, specifically in composites without any type of reinforcement.
Delamination can occur due to the difference in coefficient in thermal expansion or defect in the interlaminar structure of the composite materials. Delamination plays a crucial role in influencing the behavior of composites during the damages caused by impact loading, and the response of the composites after the impact. Interface failure in the fiber-reinforced composites occurs due to the debonding or delamination of laminate structures. Interface failure can significantly reduce the compressive load-carrying capacity of a fiber-reinforced composite structure.
The processing steps associated with the fabrication of geopolymers play a crucial role in limiting the flaws. Mechanisms such as crack bridging, crack deflection, and fiber pullout allows the dissipation of crack energy in the material and prevent the possibility of early failure of cracks. Cracks can also be limited by particle or fiber reinforcements in order to improve the strength of geopolymers. For instance, plain weave fiber reinforcements can increase the strength of geopolymer composites by enhancing the mechanical properties of the material.
This study evaluated the delamination behavior and inner strength of geopolymer composites when they are reinforced with electrical-grade glass (E-glass) and carbon fibers respectively. A simulation approach was followed to evaluate the study and correlate the experimental observations.
The Study
The cohesive zone model (CZM) in the multiphysics model was used to simulate the interfacial failure of E-glass and carbon fiber reinforced geopolymer composite. The delamination simulation in composites was divided into delamination propagation and initiation. The simulation model was also utilized to predict the interfacial crack propagation under mixed-mode loading. Alkali activator solution, alumina-silicate powder, and metakaolin were used in the preparation of the geopolymer matrix.
More from AZoM: Constructing a Nuclear Submarine
Woven fabrics of E-glass and carbon were utilized as reinforcement during the development of the composite. Initially, alumina-silicate powder, alkali activator solution, and metakaolin were mixed for 10 min to prepare the geopolymer mix, and then the mix is filled manually in the woven fabrics and compressed by a roller until a thickness of 3mm was attained. The fabric reinforced geopolymer composites were placed in a vacuum bag, cured at 0.03 MPa for 2 h at ambient temperature, and then cured again for 20 h in an air medium.
The composite density was initially measured at room temperature, and then again at 1000oC. For 30 min, the E-glass and carbon fiber reinforced composites were heat-treated at temperatures between 200 and 1000oC in order to determine the flexural strength and modulus of both composites in terms of exposure temperature. The thickness expansion and mass retention were observed in terms of heating temperature.
Observations
The density of the geopolymer matrix was higher than the fiber-reinforced composite. The carbon fiber reinforced geopolymer composite demonstrated greater mechanical strength than the E-glass reinforced composite. The strength of the carbon fiber-reinforced composite was 200 MPa, while the strength of the E-glass reinforced composite was 50 MPa.
The E-glass fiber composite displayed a lower flexural strength compared to the carbon fiber composite at temperatures above 600oC. Similarly, the flexural modulus of carbon-reinforced composite was higher at temperatures above 1000oC compared to E-glass reinforced composite as the modulus of carbon increases at a higher temperature. This factor was responsible for the strong adhesion between the geopolymer matrix and carbon fiber.
E-glass reinforced composite demonstrated greater thickness expansion than the carbon-reinforced composite. Both E-glass and carbon-reinforced composites experienced a loss of mass at temperatures below 600oC. However, the carbon-reinforced composites displayed a more stable behavior after 600oC, while the E-glass reinforced composites displayed a reduction in the loss of mass.
The E-glass fiber-reinforced composite displayed significant bending and delamination of layers at higher load displacement. Observations from the interface of both composites indicated that excluding the impact region, the carbon fiber reinforced composites possess an intact behavior in their residual part compared to the E-glass composite.
This study demonstrated that the interlaminar strength of carbon fiber reinforced composites is stronger compared to the E-glass reinforced composites. Additionally, the carbon-fiber-reinforced composites demonstrated higher delamination resistance and better intact behavior than E-glass reinforced composites.
Disclaimer: The views expressed here are those of the author expressed in their private capacity and do not necessarily represent the views of AZoM.com Limited T/A AZoNetwork the owner and operator of this website. This disclaimer forms part of the Terms and conditions of use of this website.
Source:
Samal, S. Interface failure and delamination resistance of fiber-reinforced geopolymer composite by simulation and experimental method. Cement and Concrete Composites. 2022. https://www.sciencedirect.com/science/article/pii/S0958946522000166?via%3Dihub