Researchers from China and Malaysia have designed a flexible bionic hand possessing soft gripper driver technology capable of replicating basic human gestures via a simple fabrication technique. The process was described in the journal Materials.
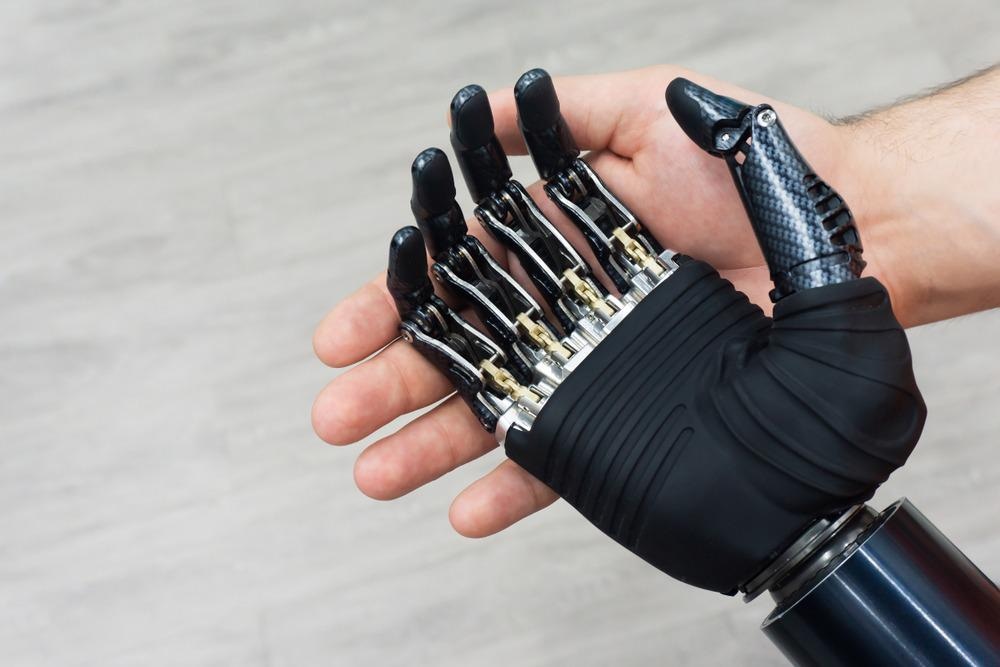
Study: Pneumatic Bionic Hand with Rigid-Flexible Coupling Structure. Image Credit: Dmitry Markov152/Shutterstock.com
Rigid Robotic Gadgets and Soft Gripper Technology
Ever since the dawn of robotics and modern nanotechnology, constant research has been done to revolutionize the fabrication techniques and utilize materials capable of handling the stresses exerted due to robust movements and component friction. The gripping pressure is difficult to correctly regulate when using stiff grips on things with complicated surface forms and delicate goods, and it is easy to harm the item's exterior.
The soft grasping hand can do duties that typically inflexible manipulators cannot due to its inherent mobility, ambient flexibility, and proactive safety improvements. This method is commonly employed in healthcare rehabilitation, aviation, and crisis assistance. Many academics are currently paying close attention to the soft gripper driver. These grippers are continually improving in terms of tactile information, force response, and quick response precise control.
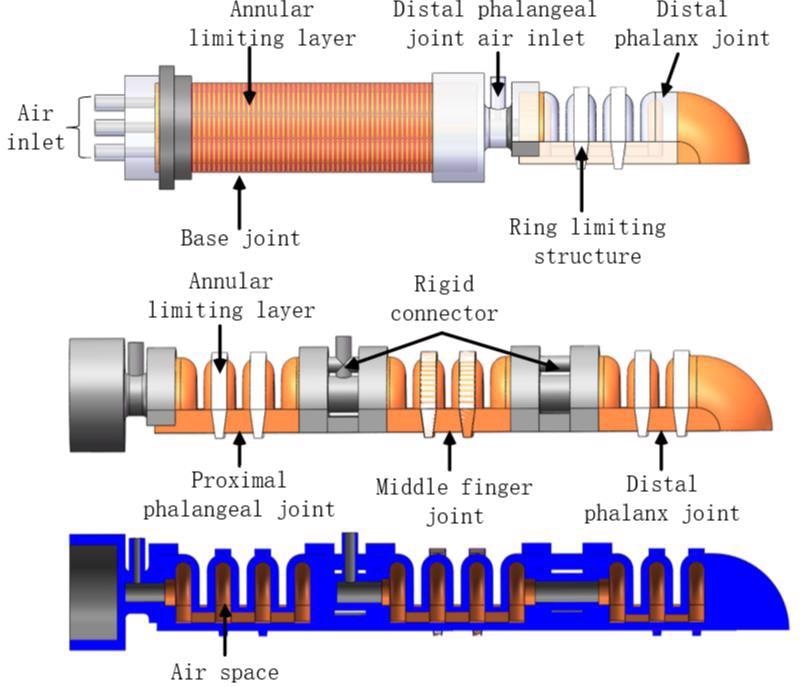
Schematic diagram of soft finger structure. Image Credit: Chen C et al., Materials
The soft gripping hand is more versatile than the standard rigid grasping hand; however, its gentleness causes the difficulty of necessitating a low load in the grasping hand.
Structural Design of the Soft Gripper Technology
The technology is comprised of the soft finger driver as its essential component. The soft finger is separated into two sections: the thumb section and the other four fingers, which are mostly made up of a base joint and ring-shaped restricting membrane. The restricting layer is used to regulate the soft driver's radial displacement. Silicon rubber is used to create a soft air cavity. Silicone rubber has a well-developed mechanical simulation analytical framework, and it is a deformable material that may be used to make soft fingers.
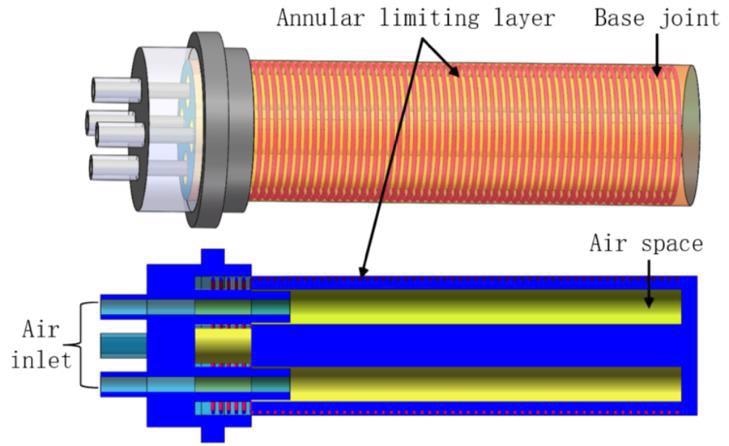
Schematic diagram of base joint structure. Image Credit: Chen C et al., Materials
The Fast Pneumatic Grid Structure (FPN) concept is used to create the bionic finger soft-driven joint. The FPN structure grows through the sidewalls, bending and deforming the activator. The soft-driven joint is mostly made up of air chambers. External air pressure can cause the top and sidewalls of the drive joint to extend and distort at the same time. The expansion and distortion of the top wall, on the other hand, is interference deformation. The silicon rubber substance E60 is used to make the soft bionic gripper.
Design of the Bionic Hand Control System
A pneumatic regulatory loop system and a detection system are part of the physical control system. The higher computer operational gateway and the bottom computer control software comprise the soft control system. The man-machine dynamic regulatory module and the Arduino command center are the major components of the pneumatic control system. The air pressure detection system detects data from the present soft-driven air cavity and compares it to the predefined goal value while the soft finger moves.
The user interface offers manual regulation of the prosthetic finger-driven parts as well as a display of the operating joint sensor's experimental curve. In manual mode, the user may change the airflow stress in each driving joint individually.
Experimental Results
According to the experimental results, varied exterior air pressure stresses were applied to the operating joint cavity, and the generated foundation joint bending angles differed, which is compatible with the soft simulation results. According to the testing results, the insertion of the elastic steel plate at the base had a minor effect on the folding of the soft-driven join.
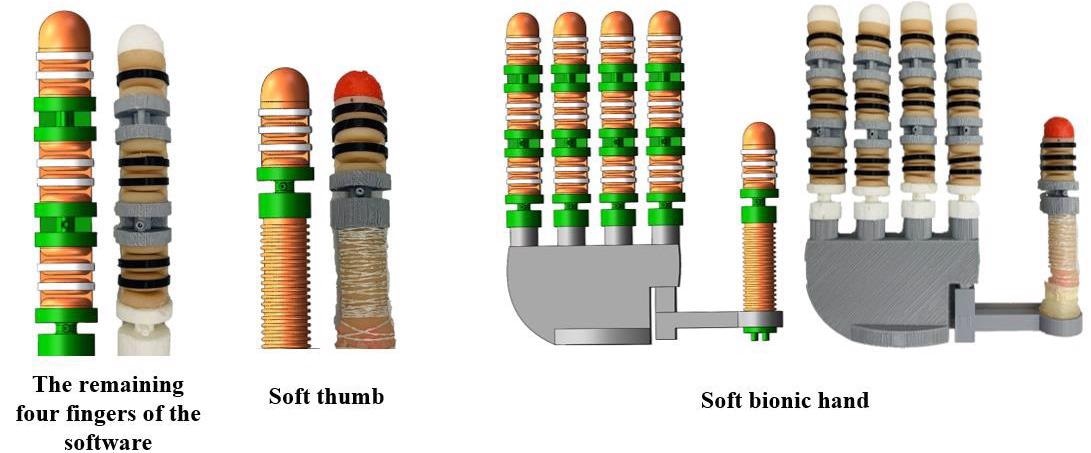
Soft gripper combination. Image Credit: Chen C et al., Materials
Bionic Hand Human Gesture Replication Results
Various external pressurization stresses were applied to the driving joints of each finger in conjunction with the developed control system's particular synchronization control scheme. Based on the findings, it is possible to conclude that soft-driven joints may be regulated autonomously, that the intermediate and distal phalange joints can achieve joint motion, and that the cooperation of diverse joints can realize the imitation of human gestures.
The researchers also studied the response of the bionic hand by testing its gripping technique. The hand was tested by grasping various objects utilized frequently in human life. If the item did not fall during the clutching movement, the grabbing movement was considered successful.
In summary, a novel development of a pneumatic prosthetic hand with a rigid-flexible coupling mechanism has been described successfully. Further examination can employ EMG signal instruments, sight sensors, and other sensors to construct an autonomous gripping software that can track and replicate real-time hand motions.
Further Reading
Chen C, Sun J, Wang L, Chen G, Xu M, Ni J, Ramli R, Su S, Chu C. 2022. Pneumatic Bionic Hand with Rigid-Flexible Coupling Structure. Materials. 2022. 15(4). 1358. Available at: https://www.mdpi.com/1996-1944/15/4/1358
Disclaimer: The views expressed here are those of the author expressed in their private capacity and do not necessarily represent the views of AZoM.com Limited T/A AZoNetwork the owner and operator of this website. This disclaimer forms part of the Terms and conditions of use of this website.