Writing in the journal Metals, a team of researchers from Jilin University in China has demonstrated strengthened H13 tool and die steels with trace nanoparticles which exhibit enhanced wear resistance and other industrially important properties.
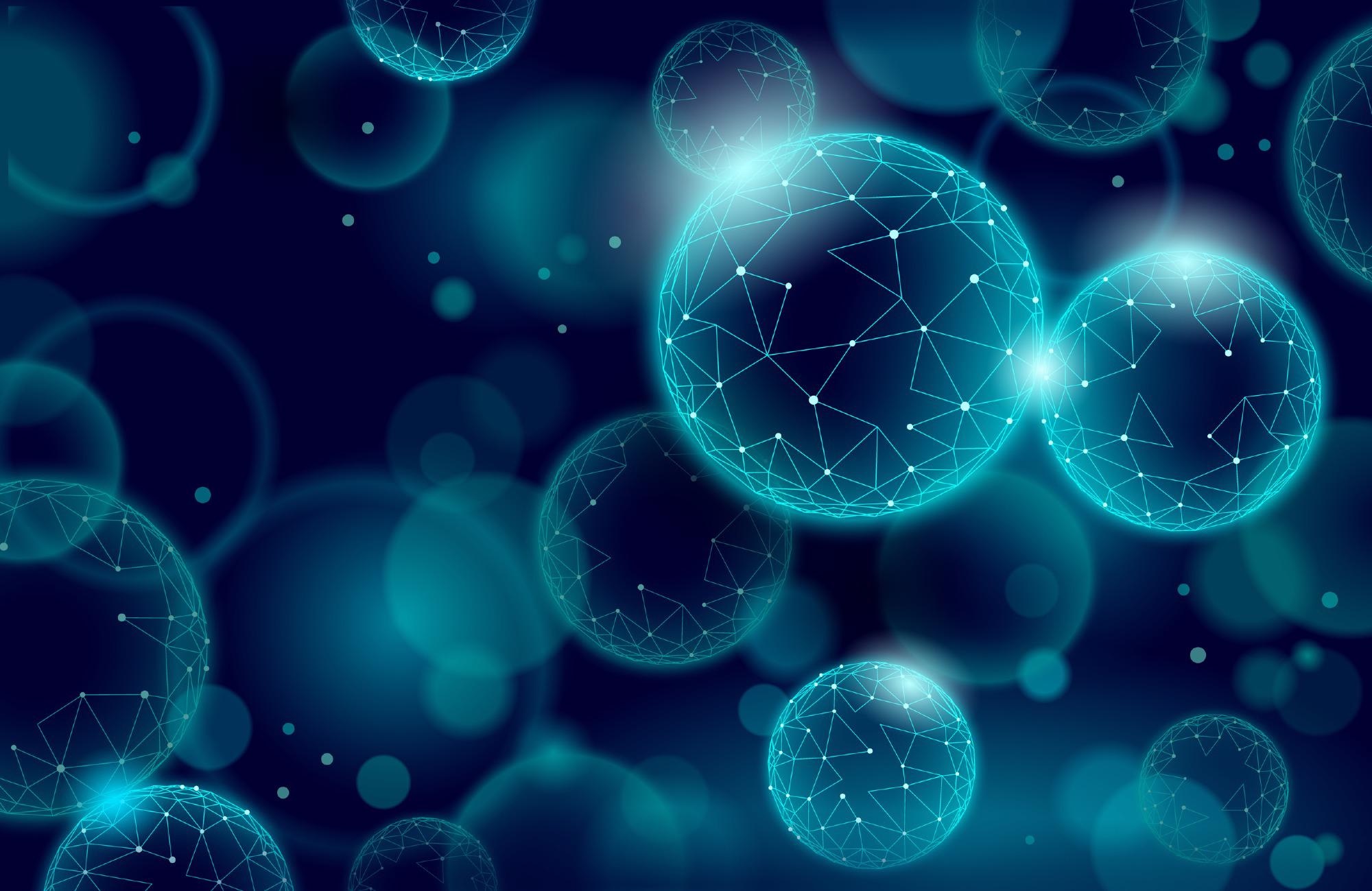
Study: Enhancement of Wear Resistance on H13 Tool and Die Steels by Trace Nanoparticles. Image Credit: LuckyStep/Shutterstock.com
The team has studied several different types and contents of nanoparticles and their effect on the steel’s microstructure and its corresponding properties, focusing on introducing nanoparticles to liquid steel in situ.
Creating High-Grade, Superior Performance Tool and Die Steels
Tool and die steels are important industrial materials, which resist wear and have enhanced impact toughness. For instance, tool and die steels with a high chromium content, which possess the aforementioned properties, are used to manufacture shield machine rolling tools.
Rolling tools must withstand abrasive wear conditions under high degrees of stress, due to abrasion by rocks and materials during the rolling process. Instantaneous friction generates high amounts of heat, causing the temperature of the tool’s surface to rise rapidly. After rotation, water spray is used to cool the tool surface, requiring steel that can withstand not only stressful wear conditions but also fatigue caused by sudden changes in temperature.
In other tool and die steels, however, there is a contradictory relationship between the two properties of impact toughness and wear resistance. Whilst they possess good levels of wear resistance, they display low impact toughness. Therefore, the need to balance both properties is of paramount importance to materials scientists working in the field of tool and die steel manufacture.
Whilst there have been significant improvements of late in methods for improving these contradictory properties, such as heat treatment and ultra-pure purification, on a technical level these steels have reached a limit. This has facilitated the need for developing new and efficient methods for improving the properties of tool and die steels.
The preparation process of H13 tool and die steels manipulated by trace nanoparticles: (a) melt, (b) addition and release of nanoparticles, (c) uniform distribution of nanoparticles, (d) casting, (e) steel ingot. Image Credit: Kou, S-K et al., Metals
How Nanoparticles Can Improve the Properties of Steel
Research into improving these contradictory properties has led to an increased focus on the incorporation of nanoparticles into steels used for tool and die applications. Recent research has indicated that nanoparticles refine the microstructures of steel alloys, as well as increase their toughness and strength.
Nanoparticles strongly influence microstructure refinement and additionally, they control the morphology and growth size of grains within the microstructure. Furthermore, incorporating nanoparticles into steel alloys improves mechanical properties such as strength at high temperatures, impact toughness, fatigue resistance, and high-temperature creep.
Compared with conventional strengthening techniques, incorporating nanoparticles has advantages including improving the environmental friendliness of steel manufacture and the ability to be used with existing casting processes and equipment. Currently, there is a lack of studies in the literature on the microstructural evolution and wear-resistance of steels manipulated with nanoparticles.
Moreover, due to the difference in specific gravity between liquid steel and nanoparticles, augmenting liquid steel with nanoparticles is tough to achieve. Additionally, due to their relatively high surface energy, nanoparticles easily agglomerate, making their dispersion in liquid steel difficult, affecting the strength and other properties of the finished product. Moreover, due to the fact that contaminants are adsorbed by nanoparticles, the strengthening effect can be impacted.
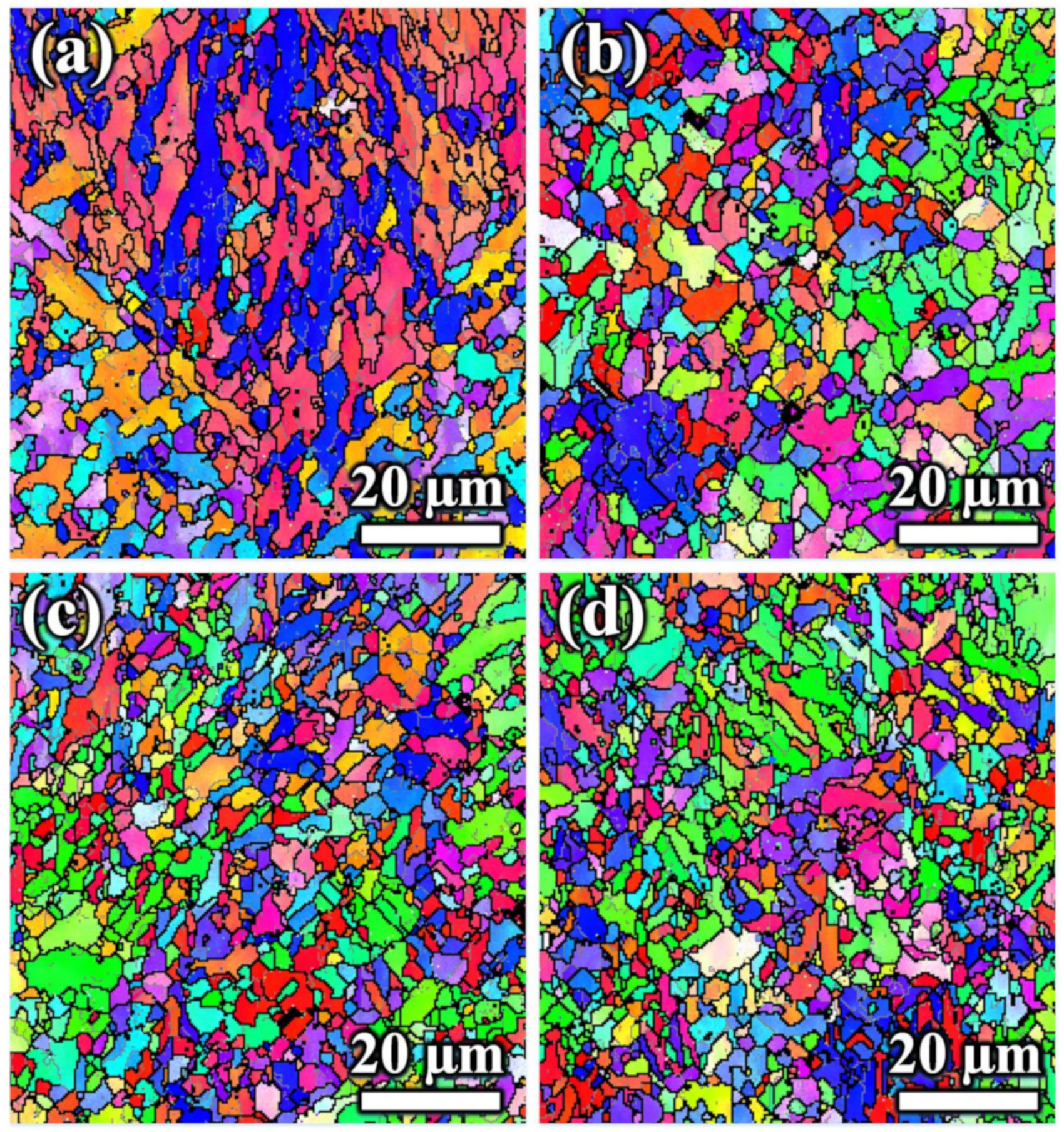
EBSD images of H13 steels without and with different types and contents of nanoparticles: (a) H13, (b) 0.02 wt.% TiC, (c) 0.01 wt.% TiC + TiB2 and (d) 0.02 wt.% TiC + TiB2. Image Credit: Kou, S-K et al., Metals
The Research
The research in Metals has concentrated on using the master alloy method to augment tool and die steel with nanoparticles. The authors have studied including nanoparticles in the microstructure of H13 steel alloys and their effect on the material’s properties.
Impact toughness, tensile strength, and abrasive wear behavior of the nanoparticle-toughened steels were studied at room temperature under different loads and abrasive sandpaper particle sizes. Based on their observations, the authors drew several important conclusions.
Firstly, introducing the single-phase and dual-phase nanoparticles created a more uniform microstructure in the H13 steel than steel without nanoparticles. The refining effect of dual-phase nanoparticles is more pronounced than single-phase nanoparticles. Manipulating H13 steel with nanoparticles enhances its mechanical properties, such as impact toughness and tensile performance.
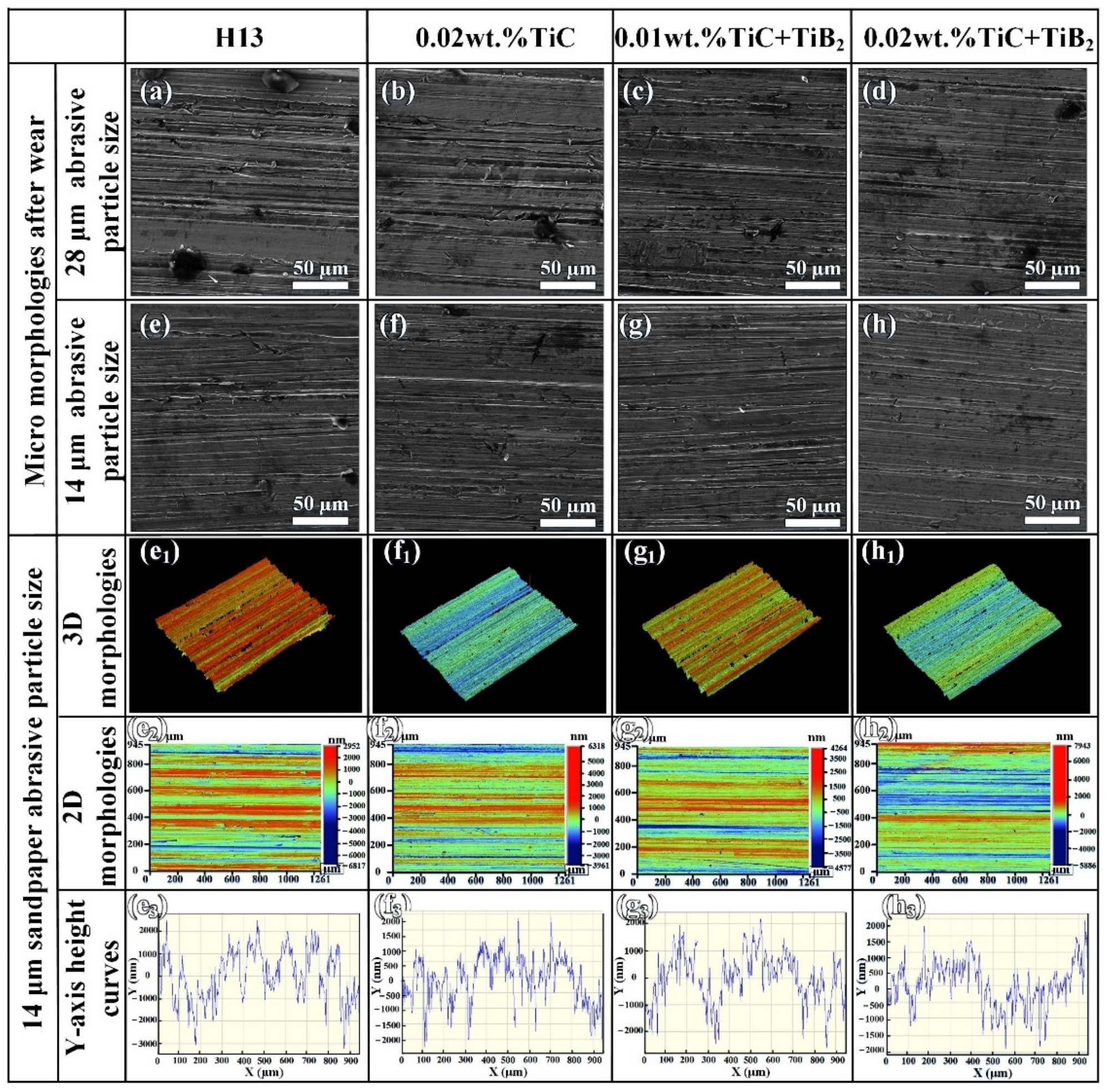
SEM of worn surface of H13 steels without and with nanoparticles under the load of 25 N and different sandpaper abrasive particle sizes: (a–d) 28 μm and (e–h) 14 μm, and white light interference of worn surface of H13 steel reinforced by nanoparticles under sandpaper abrasive particle sizes of 14 μm: (e1–e3) H13, (f1–f3) 0.02 wt.% TiC, (g1–g3) 0.01 wt.% TiC + TiB2 and (h1–h3) 0.02 wt.% TiC + TiB2. Image Credit: Kou, S-K et al., Metals
The authors also observed a greater strengthening effect using dual-phase nanoparticles compared to single-phase nanoparticles. Fracture strain, uniform elongation, yield strength, and other properties were improved compared to conventional H13 steel. The width and depth of surface grooves of trace nanoparticle-reinforced H13 steel were reduced, improving the steel’s resistance to wear. Volume wear rate was reduced using dual-phase trace nanoparticles.
Therefore, the authors have concluded that dual-phase nanoparticles can significantly improve the steel’s resistance to wear. The optimal nanoparticle content was 0.02% by weight. This can be attributed to the production of a denser microstructure in the steel upon manipulation by dual-phase nanoparticles, which weaken plowing wear effects. The study has demonstrated the effectiveness of using trace nanoparticles to improve the properties and, therefore, the industrial applications and life cycle of H13 tool and die steels.
Further Reading
Kou, S-K et al. (2022) Enhancement of Wear Resistance on H13 Tool and Die Steels by Trace Nanoparticles [online] Metals 12(2) 348 | mdpi.com. Available at: https://www.mdpi.com/2075-4701/12/2/348
Disclaimer: The views expressed here are those of the author expressed in their private capacity and do not necessarily represent the views of AZoM.com Limited T/A AZoNetwork the owner and operator of this website. This disclaimer forms part of the Terms and conditions of use of this website.