In a recent study published in the journal ACS Energy Letters, researchers from China reviewed the green process for producing sustainable perovskite solar cells (PSCs). They focused on the environmental and health impact of lead (Pb) and solvents used for manufacturing PSCs.
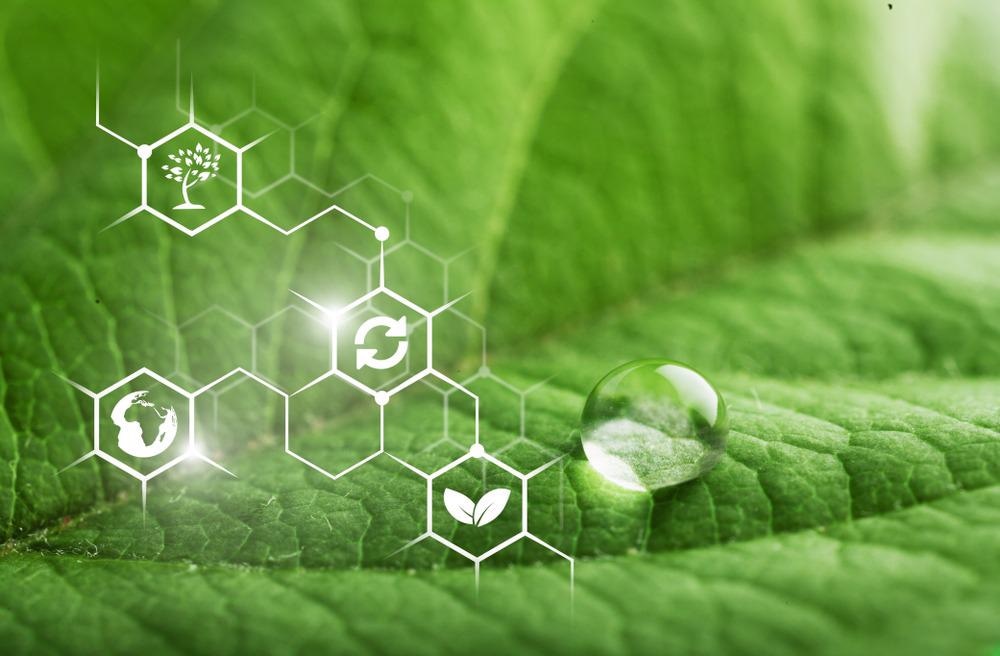
Study: Sustainable Green Process for Environmentally Viable Perovskite Solar Cells. Image Credit: Billion Photos/Shutterstock.com
Hazardous Materials and PSCs
PSCs have been considered as alternative materials for solar cells by researchers and industries. They have more than 25% power conversion efficiency due to electronic and optical properties. The significant properties of PSCs are their high light absorption coefficient, low exciton binding energy, and long charge diffusion length that enable their use in a wide range of industrial applications. Additionally, PSCs are also commercially suitable because of their low cost.
Compared to other commercial photovoltaic (PV) technologies such as copper indium gallium selenide and silicon-based solar cells, the life cycle assessment studies on industrial-scale PSCs have demonstrated low environmental impact and high energy payback time. Despite the fact that PSCs have a lower environmental impact, the treatment of Pb-containing non-aqueous waste produced during their manufacturing and continuous exposure to Pb from the device causes long-term environmental and health risks.
In this review, the researchers studied the hazardous materials used to manufacture PSCs and their impact on health. They specifically discussed PSCs' environmental and health effects and provided analytical data on the toxic materials used in their manufacturing.
Environmental and Health Hazards of PSCs
Pb, a material that causes develops significant environmental and health risks, is used in the light-absorbing layer of PSCs. Pb is a hazardous element to ecological receptors such as terrestrial and aquatic organisms and humans, yet only a few studies on the toxicological effects of chemicals from PSCs have been published worldwide. Pb would gradually accumulate in the bones as impenetrable lead phosphate during continuous exposure in humans.
Furthermore, Pb excretion in breast milk poses a severe risk to breastfed infants, which can cause heavy metal poisoning. Although Pb is present in PSCs at lower amounts, strategies for limiting Pb exposure are significant for health and environmental concerns. Recently, approaches for waste management and recycling processes of Pb in PSCs have been developed as recycling Pb from PSCs is critical from a sustainability standpoint.
PSCs have four stages in their life cycle: material selection, fabrication, operation, and disposal. The use of toxic Pb ions occurs at the materials selection stage. Hence, PSCs must be designed to minimize the use of Pb to reduce the overall impact on the environment. Additionally, during the disposal stage, a process must be developed to improve the efficiency of Pb recycling.
More from AZoM: Introducing a Commercially Stable Lithium-Sulfur Battery>
The majority of the parts in PSCs can be efficiently recycled, which reduces their environmental impact. However, using these recycled materials results in slightly lower performance in other products due to impurities. In some exceptional cases, recycled photovoltaic materials of PSCs result in performance identical to the new material.
Due to complicated and diverse configurations of devices used to manufacture PSCs, the use of advanced recycling technology is critical. However, using a toxic solvent in the advanced recycling process may consume higher energy and cost. Due to this, it is critical to develop a low-cost and environment-friendly recycling process to use PSCs.
Solvents used in the production process of PSCs develop health risks for humans. Inhalation or skin contact with solvents poses a risk to the human body, due to which their industrial use is regulated in many countries. Using green fabrication processes that use environmentally friendly solvents can reduce this impact.
According to researchers, finding a green solvent for PSCs is a challenge, though according to some studies, using no toxic solvent in the manufacturing process has improved results. Green anti-solvents such as ethyl acetate and anisole have demonstrated improved device performance. The use of green anti-solvents can significantly mitigate the health risk posed by inorganic solvents during the manufacturing of PSCs.
Conclusions
To summarize, hazardous chemicals such as Pb must be used in significantly lower quantities, and advanced recycling technologies need to be developed for the safe use of PSCs. The advancement of technology for reusing the green solvent will significantly impact the use of green technology in PSC commercialization.
Additionally, efforts to replace currently used toxic chemicals with environmentally sustainable chemicals have introduced green chemistry into PSC production. The significance of green chemistry will be emphasized more in the future to protect worker health and maintain workplace safety.
Overall, developing a comprehensive recycling system can reduce the environmental impact of Pb and the solvents used in PSC production. Future studies need to analyze the collective strategies of PSCs to develop sustainable PSCs and focus on reducing the use of Pb and inorganic solvents in the manufacturing process.
Disclaimer: The views expressed here are those of the author expressed in their private capacity and do not necessarily represent the views of AZoM.com Limited T/A AZoNetwork the owner and operator of this website. This disclaimer forms part of the Terms and conditions of use of this website.
Source:
Hui-Seon Kim, Youn-Joo An, Jin Il Kwak, Hee Jung Kim, Hyun Suk Jung, and Nam-Gyu Park, Sustainable Green Process for Environmentally Viable Perovskite Solar Cells. ACS Energy Letters 0, 7, https://pubs.acs.org/doi/abs/10.1021/acsenergylett.1c02836