Vehicles and equipment launched into space require advanced materials with enhanced properties to withstand the rigors of outer space. Exploring the potential of carbon-reinforced polymers for use in space, a research paper has been published, which has been included in Recent Advances in Manufacturing Processes and Systems.
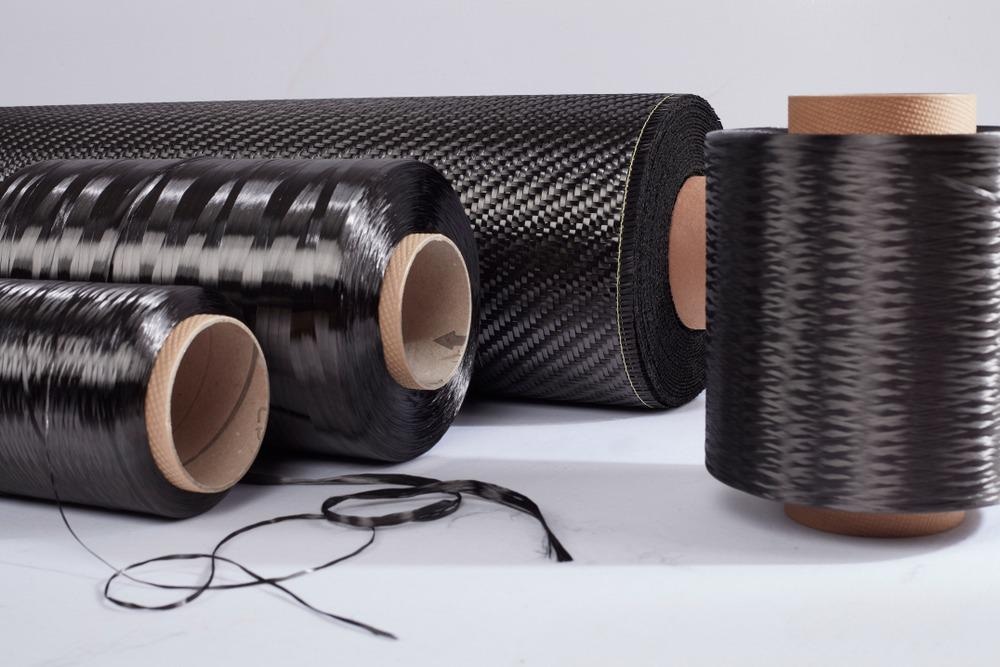
Study: Hybridized Nanotubes and Graphene Oxide in CFRP Development for Space Use. Image Credit: porti/Shutterstock.com
Developing Advanced Materials for Use in Space
The space industry makes use of several advanced materials such as Kevlar, aluminum alloys, ceramics, and Invar. Materials used in components must possess specific electrical and thermal characteristics due to the rigors of outer space. However, despite their superior electrical and thermal performance, many metals which are used in components have high density and can be expensive to manufacture.
Carbon-based nanofillers such as graphene oxide, single-walled carbon nanotubes, and multi-walled carbon nanotubes and combinations thereof have been explored extensively to replace conventional materials. These classes of nanomaterials possess superior electrical and thermal conductivities and are sustainable and cheap to produce. They confer significant advantages for the design of components for use in vehicles and equipment in the harsh environments of outer space.
The Importance of Electrical and Thermal Conductivity
Equipment that is going into space requires specific material properties in its construction. Radiofrequency applications benefit from materials with good electrical conductivity which allows electroplating of highly conductive metals on CFRP laminates. Additionally, electrical conductivity is an important property for electromagnetic shielding for payload elements and is required for electrical performance compliance.
Thermal conductivity is especially important for payload elements as it dissipates the heat generated by them, preventing damage to vital systems, and improving safety for humans on board spacefaring vehicles. Therefore, materials which possess both superior electrical and thermal characteristics are central to the design of payload elements and other components for use in outer space.
Examples of How Carbon Nanomaterials Improve These Properties
Each type of carbon nanomaterial possesses different characteristics which can improve thermal and electrical conductivity, making them attractive candidates as advanced materials for space exploration.
For example, carbon nanotubes can be embedded in carbon fiber reinforced polymers. Different concentrations of these nanofillers confer the material with varying electrical conductivities. Additionally, the hybridization of multi-walled carbon nanotubes and reduced graphene oxide enhances the thermal conductivity of materials due to the presence of carbon-carbon covalent bonds. Phonons transmit more rapidly in covalent bonds compared to non-covalent Van der Waals bonds.
Phonon transportation is directly proportional to the material’s thermal conductivity. The large contact area of graphene oxide with multi-walled carbon nanotubes is due to its multiple internal layers, and moreover, it participates actively in phonon transport with minimal coupling loss. Graphene oxide stabilizes multi-walled carbon nanotubes, as indicated by uniform dispersion of complexes with no precipitation at room temperature.
There is a relationship between the electrical and thermal conductivity in these hybrid systems which is related to the ratio of multi-walled carbon nanotubes over reduced graphene oxide. Thermal conductivity is highest in the through-plane direction, whereas minimal value in the in-plane direction gives these hybrid materials the maximum electrical conductivity.
The Research
The study has aimed to improve carbon nanomaterial-based advanced materials for use in space exploration. In the study, the researchers have investigated improving the thermal and electrical conductivity of carbon fiber reinforced polymers by including different concentrations of reduced graphene oxide and multi-walled carbon nanotubes. Additionally, they have explored different nanofillers which can be incorporated into carbon fiber reinforced polymers.
Thermal and electrical characterization of composite materials with different concentrations of multi-walled carbon nanotubes and reduced graphene oxide has been carried out by the authors. They characterized resistivity, shielding effectiveness, thermal expansion, and thermal conductivity. Advantageous characteristics of the novel composite carbon nanofiller/polymer materials were observed.
Silver electroplating was carried out as a surface treatment process on the samples to test them for performance under conditions typically encountered in outer space. A peel test was carried out on the samples, with no degradation in plating observed by the authors, demonstrating the suitability of the proposed materials for payload components in spacefaring vehicles.
The results of material characterization and physical tests carried out in the research have demonstrated a class of composite materials with enhanced thermal and electrical conductivity. The authors have stated that their results display confidence that carbon fiber reinforced polymers incorporating multi-walled carbon nanotube and reduced graphene oxide warrant further evaluation for applications in the space industry.
Furthermore, they have stated that the data gathered in their research will be essential for the manufacture of new feed horns, RF reflectors, and low-power carrier plates for use in future space research projects.
Further Reading
Solanki, J.D. (2022) Hybridized Nanotubes and Graphene Oxide in CFRP Development for Space Use [online] Recent Advances in Manufacturing Processes and Systems pp. 545-553 | link.springer.com. Available at: https://link.springer.com/chapter/10.1007/978-981-16-7787-8_44
Disclaimer: The views expressed here are those of the author expressed in their private capacity and do not necessarily represent the views of AZoM.com Limited T/A AZoNetwork the owner and operator of this website. This disclaimer forms part of the Terms and conditions of use of this website.