Scientists from Xi’an Jiaotong University in China and the University of Kashan in Iran have reported the development of a stress-resistant composite electrolyte for use in lithium batteries. The paper is currently in the pre-proof stage in the journal Energy Storage Materials.
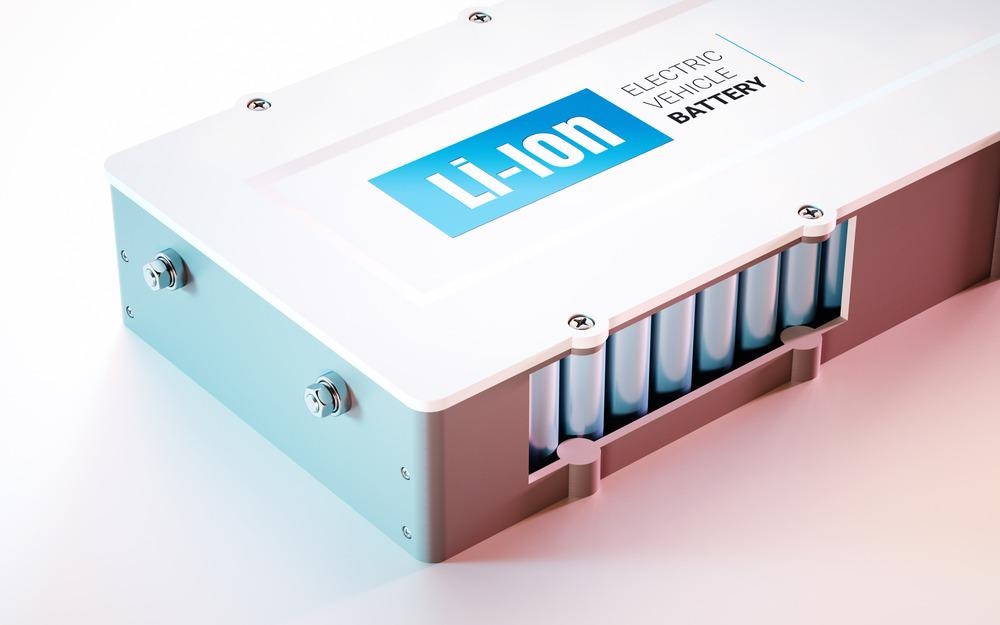
Study: Temperature and Stress -resistant Solid State Electrolyte for Stable Lithium-Metal Batteries. Image Credit: petrmalinak/Shutterstock.com
Improving Lithium Batteries
Lithium-ion batteries are used as energy storage devices for numerous applications such as electric vehicles, smart power grids, and portable electronic devices. Whilst they possess several properties that make them ideal for these applications, they are hindered by several challenges in their design. Prime amongst these design challenges is the use of liquid electrolytes, which can present serious safety problems such as explosion and fire risk.
Solid-state lithium batteries overcome the challenges and risks associated with liquid electrolyte lithium-ion batteries. These next-generation energy storage devices possess excellent electrochemical and thermal stability and, when coupled with lithium metal anodes and high voltage and capacity cathodes, can reach twice the gravimetric energy density of lithium-ion batteries.
Ceramic materials and polymers are typically used as solid electrolytes in these devices. Ceramic materials possess high ionic conductivity and a wide electrochemical potential window, but their high electrode interface impedance and poor fracture toughness hinder their use. Polymers have superior mechanical flexibility but can possess low ion conductivity. To overcome these issues and take advantage of their positive properties, polymer ceramic/polymer materials have been researched.
Optimizing the structure of composite solid electrolytes and the preparation processes has been investigated in several studies to improve their properties. 3D printing and hot pressing, for instance, have been investigated to produce porous structured composite materials. Ball milling or solution casting, which are physical mixing processes, are commonly used to prepare composite electrolytes.
However, the preparation of composite solid electrolytes with sufficient properties for use in lithium batteries is still problematic, with several studies reporting issues with reduced ionic conductivity, mechanical stresses, phase separation, irreversible damage, and problems arising over repeated cycling. Moreover, there has been promising progress in improving the heat resistance of composites, but few solid-state electrolytes have reached the standard required for practical applications.
Another encouraging area of research is solid-state electrolytes with self-healing abilities, which overcome mechanical stresses. However, this field of research is still in its infancy, and studies are lacking in the current literature. Designing solid-state electrolytes with superior resistance to mechanical and temperature stresses is a key area of research in next-generation lithium battery design.
The Research
The authors behind the research have reported the design of a novel composite electrolyte for use in next-generation lithium batteries. The electrolyte has been denoted PUS-LPS by the researchers and consists of a polyurethane-urea matrix and ceramic microparticles. Using in-situ chemical grafting, the researchers have built a bridge between the composite materials with strong dynamic disulfide bonds. The design of the composite material imbues it with superior temperature and stress resistance.
P-N bonds link the materials in the composite electrolyte, giving it a stable structure. Stable ion conductivity is achieved under elevated temperatures, and the novel electrolyte possesses rapid self-healing capabilities due to the dynamic disulfide bonds. Even when damaged, stable ion channels in the material are maintained.
Stepwise polymerization was used to synthesize the PUS element of the composite material. DTDA was chosen as a chain extender, endowing the polymer with self-healing abilities due to the presence of abundant aromatic disulfides. Mechanical resilience and ionic conductivity were maximized by optimizing PEG 2000/IPDI ratios during synthesis.
More from AZoM: What is Femtosecond Laser-Based 3D Printing?
LPS was selected as the ceramic component due to its high chemical reactivity and ionic conductivity. The researchers confirmed the identity of this inorganic component by comparing its X-ray diffractogram with the reference diffractogram. The composite was prepared using a heating and stirring method in an argon atmosphere for twelve hours. FTIR and XPS spectral analysis further confirmed the chemical grafting in the composite.
The superior self-healing abilities of the composite material are demonstrated by a ~100% recovery in current under room temperature conditions within a couple of minutes. Cycling stability after two hundred cycles was excellent, with a capacity retention of 95.4%. Furthermore, capacity recovery post-damage was 95.1%. The composite material possesses superior mechanical performance, with the authors reporting improved tensile strength and elongation at break. Ionic conductivity was demonstrated to be independent of solvent, confirming the electrolyte’s thermal stability.
Overall, the research has demonstrated a novel route for preparing self-healing solid electrolytes with significantly improved mechanical and electrochemical performance and stress and temperature resistance. The composite material presented in the study could be used to improve the performance of lithium batteries, opening the way for commercially viable devices in the future.
Further Reading
Lei, W et al. (2022) Temperature and Stress -resistant Solid State Electrolyte for Stable Lithium-Metal Batteries [online, pre-proof] Energy Storage Materials | sciencedirect.com. Available at: https://www.sciencedirect.com/science/article/abs/pii/S2405829722002057.
Disclaimer: The views expressed here are those of the author expressed in their private capacity and do not necessarily represent the views of AZoM.com Limited T/A AZoNetwork the owner and operator of this website. This disclaimer forms part of the Terms and conditions of use of this website.