By Surbhi JainReviewed by Susha Cheriyedath, M.Sc.Apr 14 2022
In an article recently published in the journal Additive Manufacturing, researchers discussed the material extrusion of solid epoxy for functional 3D printing with isotropic mechanical properties.
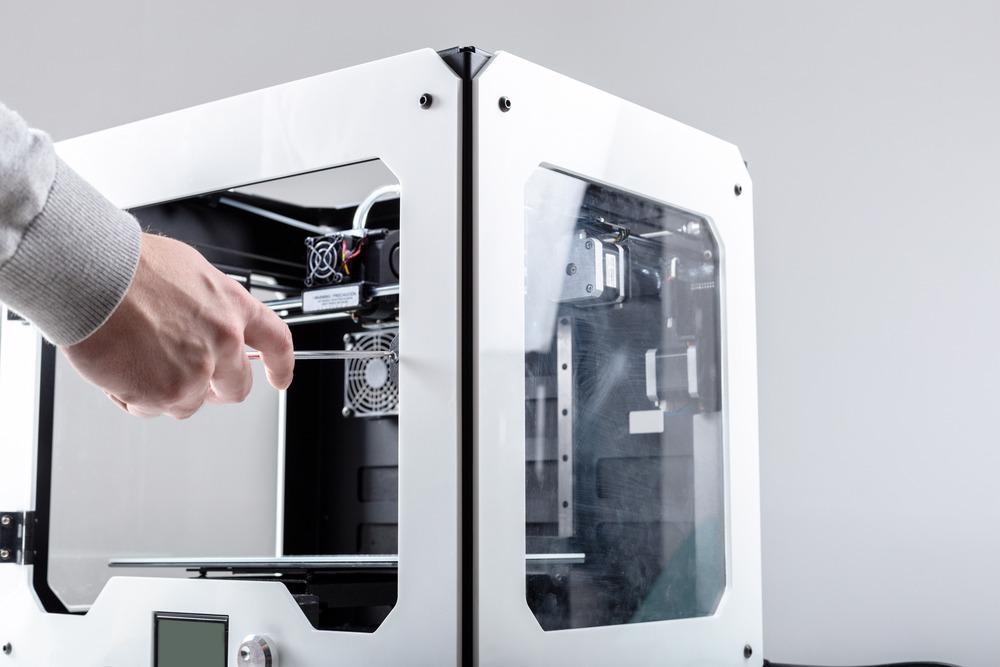
Study: Solid epoxy for functional 3D printing with isotropic mechanical properties by material extrusion. Image Credit: FabrikaSimf/Shutterstock.com
Background
In recent years, additive manufacturing has gained a lot of attention since it has various advantages over traditional production techniques. Material extrusion (MEX), also known as fused filament fabrication (FFF) or fused deposition modeling (FDM), is the most extensively used additive manufacturing approach, and it has a number of advantages over other polymer-based processes.
Despite its benefits, the MEX technique is most commonly used for prototyping, basic jigs and fixtures, and hobby applications.
Several studies examining different materials, printing parameters, load cases, and environmental conditions have demonstrated anisotropy in mechanical properties. Various approaches have been tried in the literature to avoid or at least reduce the mechanical anisotropy issue.
The use of thermosets, where cross-linking can span the layer interfaces and lead to improved bonding, is an alternative to 3D printing of polymers to achieve isotropy. The furan-maleimide Diels-Alder (fmDA) reaction produces reversible cross-linked polymers that behave like thermosets below a particular temperature but melt like thermoplastics at higher temperatures. Despite the fact that almost isotropic material qualities are achieved, the technique has several drawbacks.
Filament production process for the solid epoxy resin. Image Credit: Dr ̈ucker, S et al., Additive Manufacturing
About the Study
In this study, the authors presented the development of a thermosetting polymer. During post-curing, it permitted cross-linking over the interfaces between the infill lines and layers. The formulation was based on a solid epoxy resin that could be processed in filament form, as well as a latent curing agent that prevented the resin from curing inside the hot-end and ensured a long shelf life.
The prepared material was compared to casted and milled bulk specimens as well as 3D printed specimens made with commercial thermoplastic filaments to establish a standard. Tensile testing and micrographs of fracture surfaces demonstrated the solid epoxy formulation's mechanical isotropy. In addition, single-walled carbon nanotubes were added to the material formulation to improve electrical conductivity and enable functional 3D printing.
The team prepared a thermosetting in the form of a filament that could be printed on a low-cost MEX printer. The mechanical anisotropy issue of MEX was solved by cross-linking in a post-curing procedure. The substance was made up of a solid epoxy resin with a high molecular weight.
The researchers investigated the potential of prepared functionalized material with low single-walled carbon nanotube (SWCNT) filler content in strain and temperature sensing applications. Electrical functionalization was discussed, and filament production and sample preparation idiosyncrasies were clarified. Thermal, rheological, fractographic, geometrical, mechanical, and electrical characterization measurements were illustrated.
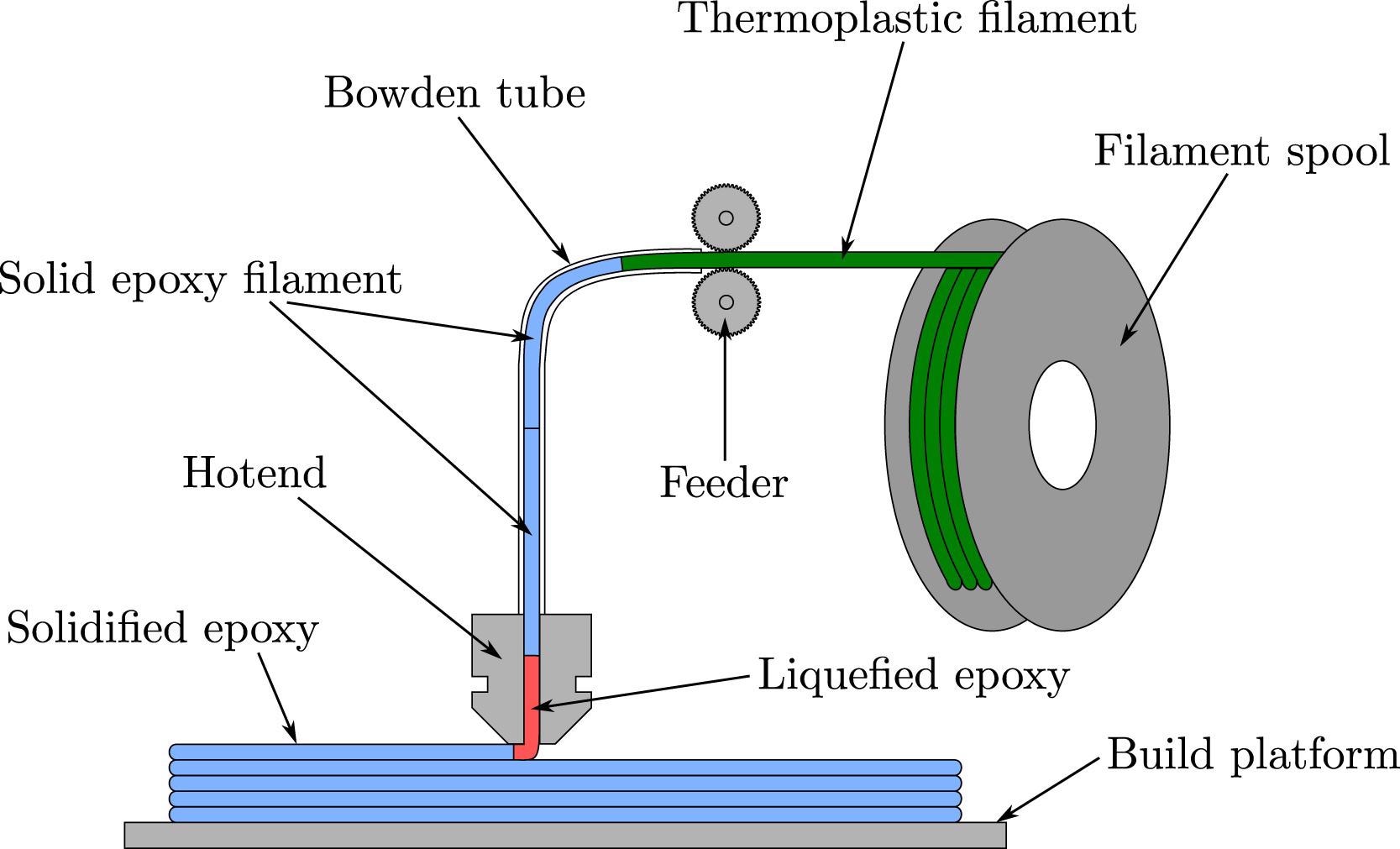
MEX printing process with the solid epoxy resin.Image Credit: Dr ̈ucker, S et al., Additive Manufacturing
Observations
The material remained solid during post-curing to maintain its structure and electrical anisotropy was detected, which limited the mobility of the nanoparticles and suppressed the agglomeration required for conductive network creation. The functionalized material could be used in temperature and strain sensing applications.
The 3D printed solid epoxy specimens showed modest roundings at the higher edges and bigger pores, which were the source of the failure when compared to the casted and milled specimens. Furthermore, the fracture surfaces of the 3D printed specimens displayed residual dicyandiamide (DCD) particles as a result of the post-curing process.
The glass transition temperature of the uncured newly developed material was above room temperature, and the onset temperature of the curing peak was above the processing temperature. Within the first 6 months of storing the uncured solid epoxy formulation at ambient temperature or in the freezer, no significant decrease in reaction enthalpy was observed.
The thermal stability of the cured solid epoxy was greater as compared to commercial polylactic acid (PLA) with a Tg > 100 °C. The relative dimensional change was below 4%. The percolation threshold could be reached with only 0.1 wt% filler material in the infill direction. When compared to commercial acrylonitrile butadiene styrene (ABS)/multi-walled carbon nanotube (MWCNT) material having a carbon additives content of 10 wt%, a similar conductivity was achieved with 0.2 wt% filler content.
A negative temperature coefficient of resistance of α = 0.0158 °C-1 was observed. The signal could be separated from the noise with a signal-to-noise ratio greater than 50 for the temperature range studied.
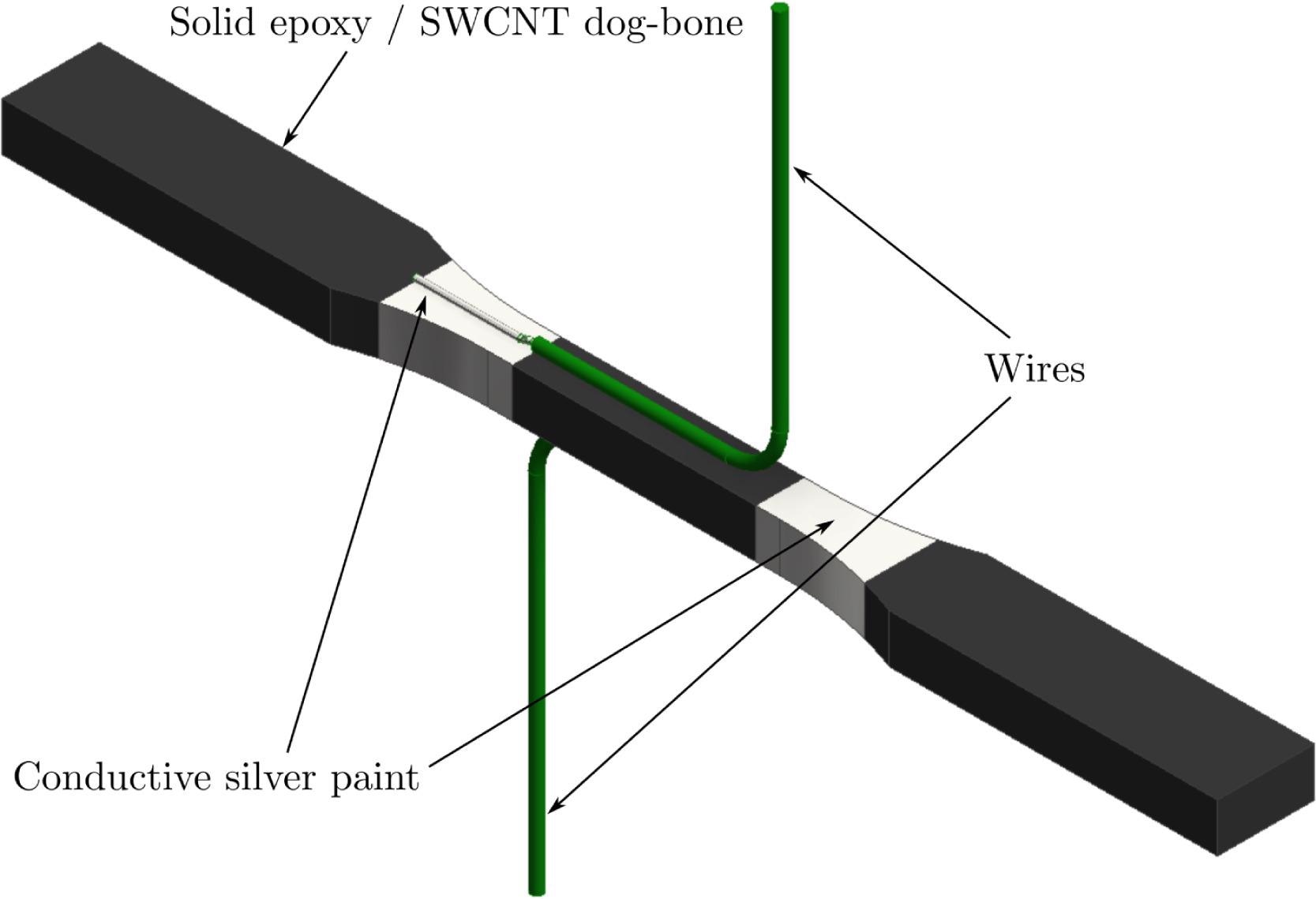
Solid epoxy/SWCNT dog-bone specimen for the characterization in sensing applications.Image Credit: Dr ̈ucker, S et al., Additive Manufacturing
Conclusions
In conclusion, this study elucidated the development of a new MEX 3D printing material that addresses mechanical anisotropy and is suited for functional applications enabled by nanoparticle manipulation. To demonstrate basic qualities, the material formulation was explained, and thermal and rheological measurements were done. To maintain dimensional stability, the geometry changes during post-curing were examined. Static tensile tests were used to demonstrate the material's isotropy, and fracture surfaces were examined to learn more about the failure causes.
The proof-of-concept investigations demonstrated the novel electrically modified material's capability in functional 3D-printed sensing applications. In temperature sensing applications, a corresponding bijective characteristic curve for resistance is found to be a function of temperature in the studied range of -30 °C to 120 °C.
The authors believe that additional research into the printing and curing of tall pieces is required. They also mentioned that the existing post-curing procedure is quite cautious, and it should be improved in the future to achieve more reasonable production timeframes.
Disclaimer: The views expressed here are those of the author expressed in their private capacity and do not necessarily represent the views of AZoM.com Limited T/A AZoNetwork the owner and operator of this website. This disclaimer forms part of the Terms and conditions of use of this website.
Source:
Dr ̈ucker, S., Voorman, H., Berg, K-P.V., et al. Solid epoxy for functional 3D printing with isotropic mechanical properties by material extrusion. Additive Manufacturing 102797 (2022). https://www.sciencedirect.com/science/article/pii/S2214860422001981