A new paper published in the journal Energies has investigated the efficient manufacture of magnetic cores using laser additive manufacturing processes. The research has been conducted by scientists from the Tallinn University of Estonia and the Estonian University of Life Sciences.
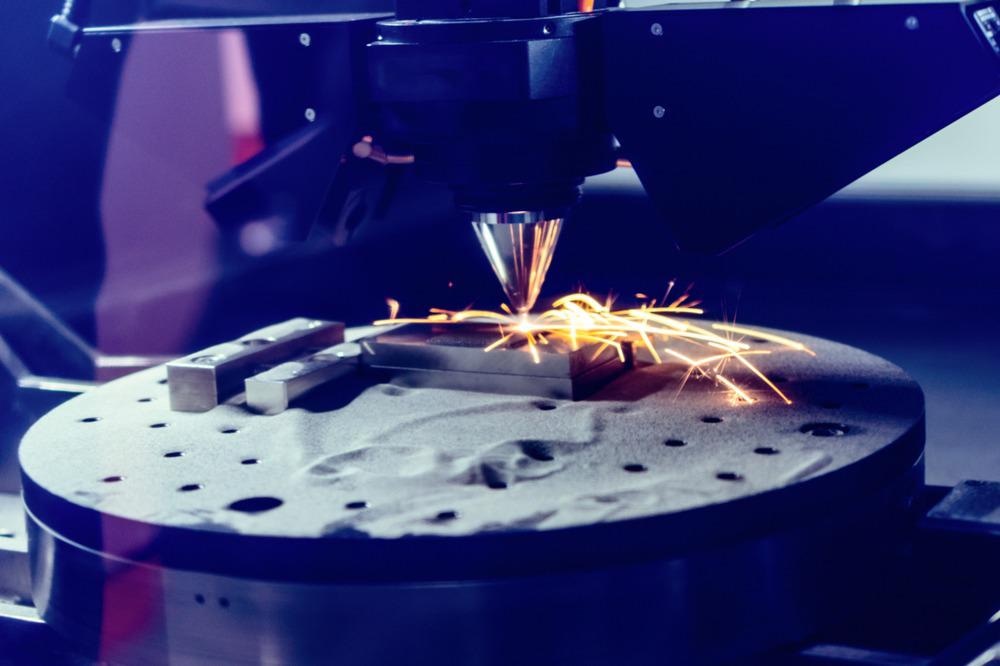
Study: Laser Additively Manufactured Magnetic Core Design and Process for Electrical Machine Applications. Image Credit: Nordroden/Shutterstock.com
Background to the Research
Fabricating electromagnetic materials using metal additive manufacturing is a new and developing research field, having its origins in the mid-2010s. By the last couple of years of the decade, the first overviews of manufacturing electrical machines using this process were published.
Two main advantages of 3D-printing electromagnetic materials and electrical machines were identified in early studies. Firstly, the benefits of using additive manufacturing, with its freedom of design form coupled with the digital system’s topological optimization capabilities could provide the field with a new revolution in manufacturing.
The full realization of Industry 4.0 is rapidly approaching, and additive manufacturing is a central technology in this industrial revolution. Creating a streamlined manufacturing process for these materials and machines will facilitate their continued development, and metal additive manufacturing will become an integral technology in this research field and associated industries.
For these printed products to be meaningful, not only will complex-shaped parts need to be produced, but they will need embedded functionalities such as magnetic, electromechanical, and electrical properties.
Achieving this will translate into mass-produced and customized goods with electrical circuits and moving parts such as motors, actuators, and gearboxes. Manufacturing them in industry 4.0-enabled smart factories without extensive assembly, post-processing steps, and waste will be supremely beneficial for the field.
Currently, fabricating complex electrical machines with additive manufacturing has not been fully realized. This is a challenging endeavor due to the requirements of devices, such as the need for small air gaps in components that improve their power density. Furthermore, there is a need for developing multi-material printing. Many materials in isolation do not perform adequately, which has led to a research focus on hybrid parallel multi-material printing methods.
Because of the challenges with 3D printing these complex devices, research has generally focused on the printing of individual single-material components. Components that have been explored include soft-magnetic rotors, copper coils, and alumina heat guides. Scientists have integrated these components into conventional electrical machines to investigate their effects.
Recently, considerable progress has been achieved in the 3D printing of soft magnetic iron cores. Researchers have produced cores with high permeability and magnetization values. However, achieving optimized additive manufactured cores with minimal core loss has been problematic so far.
The Study
The aim of the study is to demonstrate the optimal process flow for manufacturing 3D-printed high-performance magnetic cores. The process flow covers pre-printing, the printing process itself, and post-printing steps. The paper has focused on laser additive manufacturing.
Optimal parameters and energy density have been determined in the study. Determining these factors enhances the component’s relative density to achieve the maximum value and helps to produce materials and components with minimal surface roughness which may otherwise hinder their performance.
The authors have investigated annealing parameters to obtain minimal quasi-static, hysteresis, DC losses, and the highest permeability of samples. Additionally, the study has investigated topological refinement effects such as introducing air gaps and insulating voids. These effects are used to investigate eddy current loss and tune materials.
The study has also compared the material properties of prepared samples with conventional soft magnetic materials. By investigating total core losses and magnetic polarization in the prepared samples, the maturity of these magnetic core materials for commercial purposes has been evaluated by the authors.
Study Findings
Based on their observations, the authors have made several key findings that demonstrate the suitability of laser additive manufactured high-performance magnetic core materials and components for commercial applications. Scanning parameters (laser power, scanning speed, hatch spacing, layer thickness) were optimized, and nitrogen was used for the processing environment.
Optimal heat treatment temperature was found to be 1200 oC. Preparing samples at this temperature produces materials with the lowest hysteresis losses and highest relative permeability. DC measurements revealed that the 3D laser-printed core materials have comparable magnetic properties to conventional steels. Eddy current losses were limited to acceptable levels by printing shape enhanced cores.
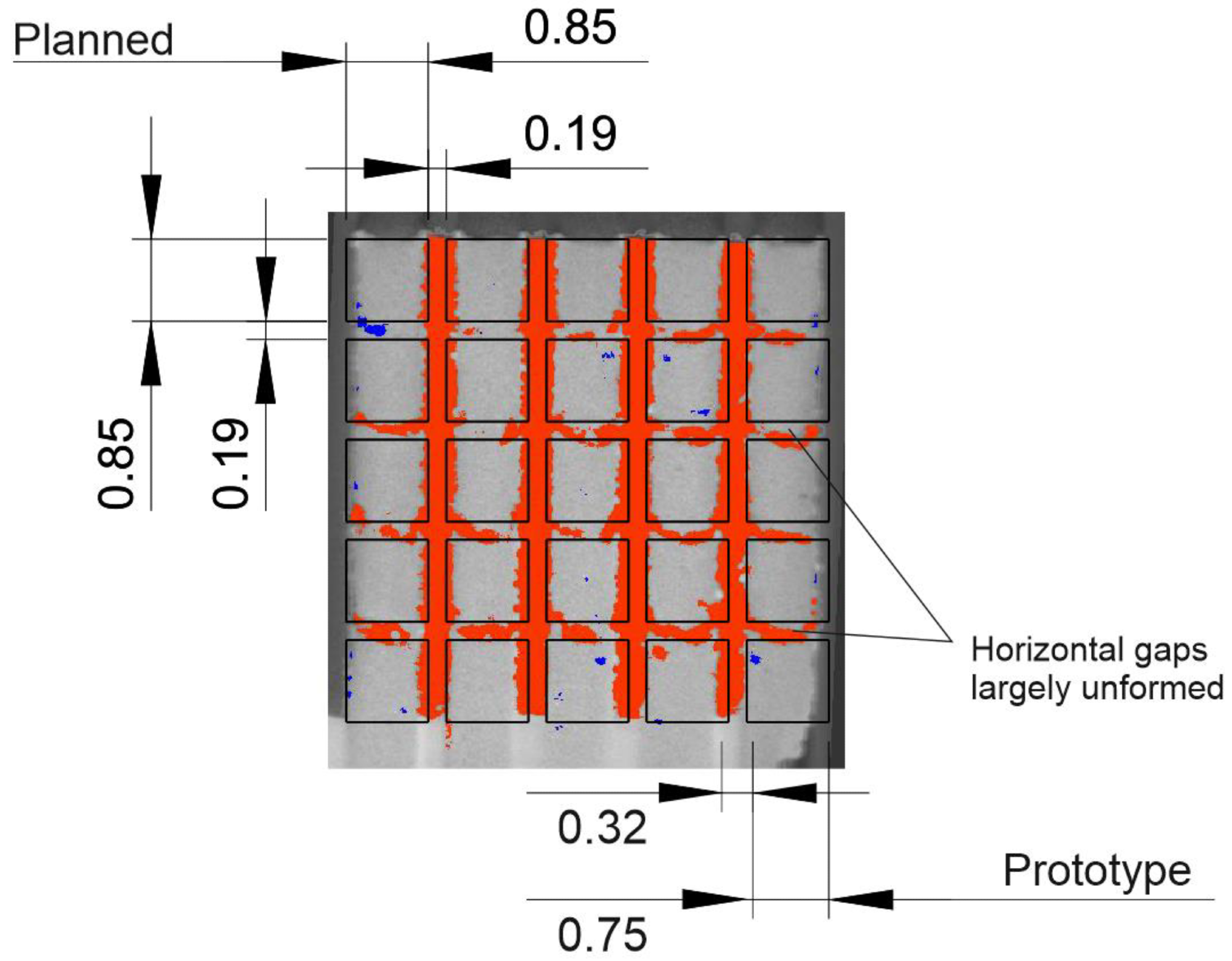
Comparison of the planned 3D model topology with the resultant printed prototype. Image Credit:; Tiismus, H et al., Energies
The paper has demonstrated that laser additive manufactured magnetic core materials can be considered for use in electrical machines. The superior material properties and freedom of design facilitated by metal additive manufacturing make these materials vastly superior to conventional soft magnetic core materials, especially for low-frequency applications.
The authors have stated that these materials could be used for advanced, novel machine designs. Further work will focus on characterizing the microstructure of additive manufactured materials, such as orientation and granular size, its effects on permeability and low- and high-field strength losses, and further shape optimization.
Further Reading
Tiismus, H et al. (2022) Laser Additively Manufactured Magnetic Core Design and Process for Electrical Machine Applications Energies 15(10) 3665 [online] mdpi.com. Available at: https://www.mdpi.com/1996-1073/15/10/3665
Disclaimer: The views expressed here are those of the author expressed in their private capacity and do not necessarily represent the views of AZoM.com Limited T/A AZoNetwork the owner and operator of this website. This disclaimer forms part of the Terms and conditions of use of this website.