By Surbhi JainReviewed by Susha Cheriyedath, M.Sc.May 26 2022
In an article recently published in the journal Additive Manufacturing, researchers discussed the utility of geopolymer and binder jetting for additive manufacturing of inorganic components.
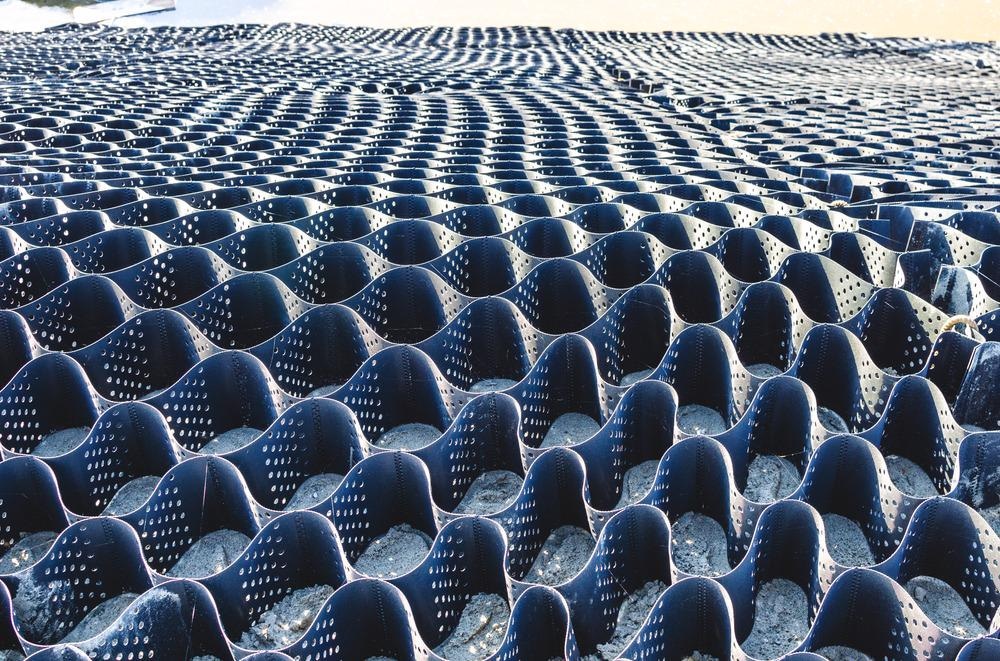
Study: Additive Manufacturing of Inorganic Components Using a Geopolymer and Binder Jetting. Image Credit: Ivan Volchek/Shutterstock.com
Background
Additive manufacturing (AM), often known as 3D printing, has been studied for a variety of purposes. The key issues with AM are maintaining a structure with a well-controlled geometry and low slump while avoiding the collapse of freshly printed structures due to the weight of the printed layers before setting. Geopolymers (GP) are currently widely used in a variety of scientific and technological domains.
Powder bed 3D printing technology has advanced to the point where printers can now produce large parts for conglomerate building blocks or for sand casting molds, allowing this technology to be considered for a variety of applications.
However, research into binder material optimization is still uncommon, and many of the successful procedures for dealing with small dimensional parts are no longer viable. To obtain a suitable powder for creating the powder bed, it must have good flowability, which allows the printer to deposit a uniform layer of particles without developing macro-defects.
About the Study
In this study, the authors created prism-shaped geopolymer components by using a large-volume binder jetting printer. The method consisted of two parts. First was a highly alkaline solution blasted onto a powder bed containing aggregates of sand particles, and a reactive solid component of pure metakaolin or metakaolin plus quick-setting cement present in the powder bed. A granulation approach was used to manufacture acceptable, defect-free powder layers and appropriately discharge the powders from the hopper feeding the layer forming device.
The team performed the proposed experiment on a large-scale, commercially available powder bed 3D printer that could produce huge format objects. Binder jetting was used to produce structural elements made of geopolymers through sustainable development and cleaner production in terms of low CO2 emissions, natural resource utilization, and energy efficiency.
The researchers developed a granulation technique that allowed them to produce a feedstock with reasonable flowability, made up of sand granules covered by the necessary amount of metakaolin. A granulation procedure was used to allow for the incorporation of a higher proportion of metakaolin (MK) with 30 wt.% into the powder bed.
The primary goal was to print metakaolin without the use of cement, and the majority of the tests and results were obtained using pure GP precursor systems. A feedstock made entirely of metakaolin and sand, as well as one that included a small amount of commercial rapid setting cement in the powder mix, were evaluated.
Observations
All of the 3D printed samples were water-resistant, with no significant differences in strength after seven days of exposure to water. After seven and 28 days of storage, an increase in the amount of metakaolin from 23 to 30 wt.% resulted in a 255% and 228% increase in strength, respectively.
For samples produced with amounts of metakaolin of 23 and 30 wt.%, respectively, an increase in the storage time from seven to 28 days resulted in increases in strength of 27 and 13 wt.%. The powder bed's residual porosity before printing was 52 vol.% for the 23MK-77Sand mixture and 50 vol.% for the 30MK-70Sand mixture, respectively.
The alkaline solution blasted into the granules effectively interacted with the metakaolin particles and generated a geopolymer. Even with 30 vol.% residual porosity, printed geopolymer parts containing 30 wt.% metakaolin had a compressive strength of 20 MPa, and no significant variation in compressive strength was detected after leaving the printed parts submerged in water for one week.
Furthermore, using metakaolin to cover the sand particles during the granulation process ensured that the activator solution come into touch with metakaolin first, which enabled the development of the geopolymer binder matrix. The uniform distribution of metakaolin around the sand particles, in the form of a continuous thin film, allowed for good interaction with the alkaline solution.
The findings confirmed that samples produced from a powder bed containing only metakaolin had the same printing accuracy and resolution as those produced from a powder bed containing cement, which confirmed the high reactivity of the corresponding MK granules to prepare the geopolymer gel that assisted in fabricating high-resolution parts without the use of cement.
Conclusions
In conclusion, this study used binder jetting to take advantage of the geo-polymerization process that occurs when metakaolin reacts with an alkaline solution. It was shown that 3D printed geopolymer pieces could be created by reacting with MK present in the powder bed. Granulating metakaolin with sand allowed a considerable amount of up to 30 wt.% fine and reactive metakaolin particles to be introduced into the powder bed, maintaining feedstock flowability during hopper discharge and enabling defect-free powder layer creation during printing.
Increases in metakaolin quantity and age time of 3D printed geopolymer components resulted in considerable increases in compressive and bending strength as well as a homogenous microstructure. The addition of rapid-setting cement to the powder bed had no effect on the parts' printing accuracy or strength. After submerging the parts in water for one week, no significant changes in strength were noticed, indicating that the created formulation could be used outdoors or in applications that need water interaction.
More from AZoM: Use and Applications of Flame Atomic Absorption Spectroscopy
Disclaimer: The views expressed here are those of the author expressed in their private capacity and do not necessarily represent the views of AZoM.com Limited T/A AZoNetwork the owner and operator of this website. This disclaimer forms part of the Terms and conditions of use of this website.
Source:
Elsayed, H., Gobbin, F., Picicco, M., et al. Additive Manufacturing of Inorganic Components Using a Geopolymer and Binder Jetting. Additive Manufacturing 102909 (2022). https://www.sciencedirect.com/science/article/abs/pii/S2214860422003062