By Surbhi JainReviewed by Susha Cheriyedath, M.Sc.Jun 17 2022
In an article recently published in the journal Additive Manufacturing, researchers discussed the development of 3D printed crack-free polymer-derived dense ceramic monoliths and lattice skeletons with better thickness and mechanical performance.
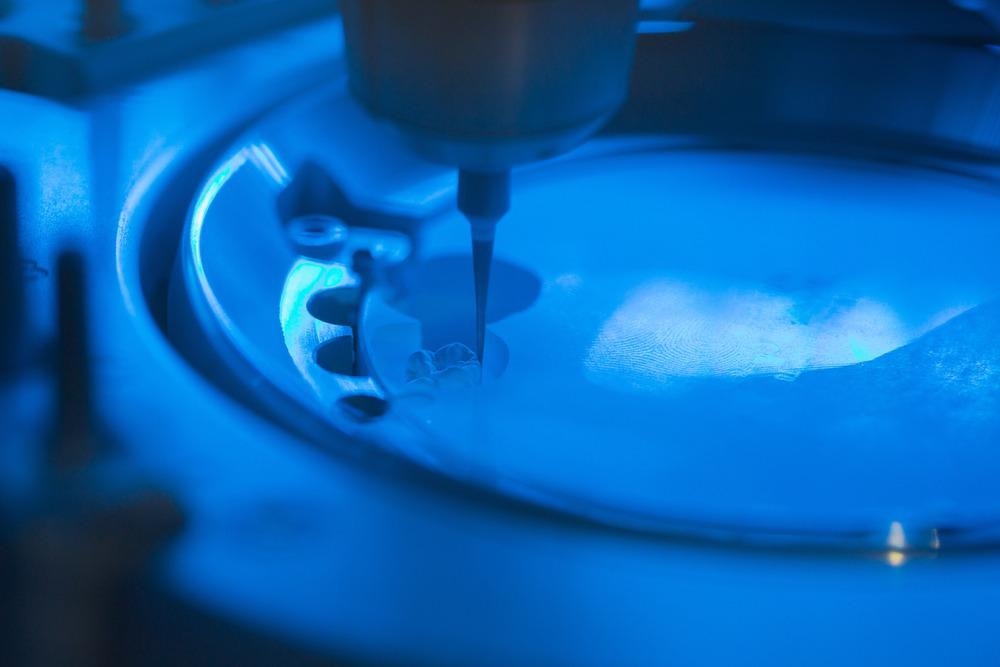
Study: 3D printing of crack-free dense polymer-derived ceramic monoliths and lattice skeletons with improved thickness and mechanical performance. Image Credit: krigo/Shutterstock.com
Background
In a range of fields, ceramics with exceptional corrosion resistance, mechanical performance, and stability at high temperatures are used. Traditional powder forming procedures for ceramics need many steps and high sintering temperatures, limiting their development and applicability. Due to the composition's designability, high-temperature stability, and low pyrolysis temperature, polymer-derived ceramic (PDC) technology has become widely used in the fabrication of innovative non-oxide ceramics in recent decades.
Additive manufacturing (AM), often called 3D printing, is currently widely utilized in a variety of disciplines. Preceramic polymers (PCPs) are particularly well suited to vat photopolymerization AM for the fabrication of ceramics. When the ceramic powder is used as the raw material for AM, the combination of the PDC technique and the AM technology could solve not only the problem of difficulty in fabricating complex structures during standard manufacturing processes but also the problems of poor homogeneity, high viscosity, and high refractive index of the slurry of the ceramic.
The synthesis of SiOC using the PDC approach has gotten a lot of attention because of its potential for use in harsh environments. Due to porosities and cracks formed during the pyrolysis process, previous research has often failed to prepare polymer-derived SiOC ceramic components with dense and thick monoliths/skeletons using AM procedures.
About the Study
In this study, the authors presented a straightforward approach for the vat photopolymerization additively made SiOC ceramics that included the addition of phenolic resin (PR) as an additive and the use of a controlled pyrolysis strategy. The particular dense thickness to ceramic yield ratio (T/Y) was calculated as a measure of dimensional retention, with maximum values of 101.9 μm/(wt%) for lattice skeletons and 254.7 μm/(wt%) for monoliths.
The team disclosed the mechanism of defect-free densification through enhanced characterization and analysis of material phase and shape changes during the pyrolysis process. Various amounts of phenolic resin (PR) as an additive were added to the polysiloxane PCP resin, and good curing qualities were produced.
The researchers constructed crack-free dense monolith and complex lattice skeleton structures with greatly enhanced achievable thickness and good structural and mechanical properties based on vat photopolymerization AM and additive-assisted pyrolysis. In addition, the additive-assisted pyrolysis method, as well as the crack-free densification mechanism, were thoroughly examined.
Observations
The prepared dense monoliths had a thickness of above 5 mm, while the lattices exhibited a maximum density skeleton thickness of 2 mm. The apparent density and specific strength of the lattice structures were 0.55g/cm3 and 6.6 x 104 N.m/kg, respectively. As a result of the formation of organized gas-releasing channels in the sample bodies during the pyrolysis process, the introduction of PR allowed for a very smooth gas-releasing procedure.
Furthermore, after pyrolysis at 1400 °C, the samples containing 15 wt.% PR in the preceramic condition still had amorphous SiOC ceramics, but the samples containing 0 wt.% PR had SiC crystallization.
After pyrolysis, the dense monolith parts had a thickness of more than 5 mm, which was comparable to those made using traditional methods with even higher ceramic yields. The maximum specific dense skeleton thickness to ceramic yield ratio (T/Y) was 101.9 μm/(wt %). In comparison to the samples having 0 wt.% PR addition in the raw materials, the samples having 15 wt.% PR addition in raw materials could maintain the amorphous SiOC following pyrolysis at 1400 °C.
The transition temperature between crystalline and amorphous forms of free C in SiOC ceramic samples was 1000–1200 °C. The addition of PR increased the mechanical characteristics and the C/O ratio of the SiOC ceramic samples.
Conclusions
In conclusion, this study proposed PR as an additive with controlled pyrolysis schemes to build crack-free dense monolith and lattice skeleton polymer-derived SiOC structures with better thickness based on vat photopolymerization AM. PR's impacts on the material, mechanical, and structural properties of additively built polysiloxane PCP and pyrolyzed SiOC ceramic monolith and lattice sections were studied. Five PCP resins were made, each with a different PR concentration.
The results revealed that the curing characteristics and fluidity were ideal for vat photopolymerization AM, and a wide range of complicated shapes could be made effectively. Crack-free dense monolith and lattice skeleton samples with reasonably uniform shrinkage were effectively created using the synergy effect of the PR addition and the controlled pyrolysis technique.
The authors believe that the proposed additive-assisted preceramic material pyrolysis and preparation method could be a potential route for the development of crack-free dense monolith and lattice skeleton SiOC ceramics with high-quality mechanical performance and structures.
More from AZoM: Reviewing the Use of Computational NIR Spectroscopy
Disclaimer: The views expressed here are those of the author expressed in their private capacity and do not necessarily represent the views of AZoM.com Limited T/A AZoNetwork the owner and operator of this website. This disclaimer forms part of the Terms and conditions of use of this website.
Source:
Xiong, S., Liu, J., Cao, J., et al. 3D printing of crack-free dense polymer-derived ceramic monoliths and lattice skeletons with improved thickness and mechanical performance. Additive Manufacturing 102964 (2022). https://www.sciencedirect.com/science/article/abs/pii/S2214860422003578