A paper recently published in the journal Resources, Conservation and Recycling proposed a new mechanism to recover iron and lead from disposal residues of lead-acid batteries (DR-LABs).
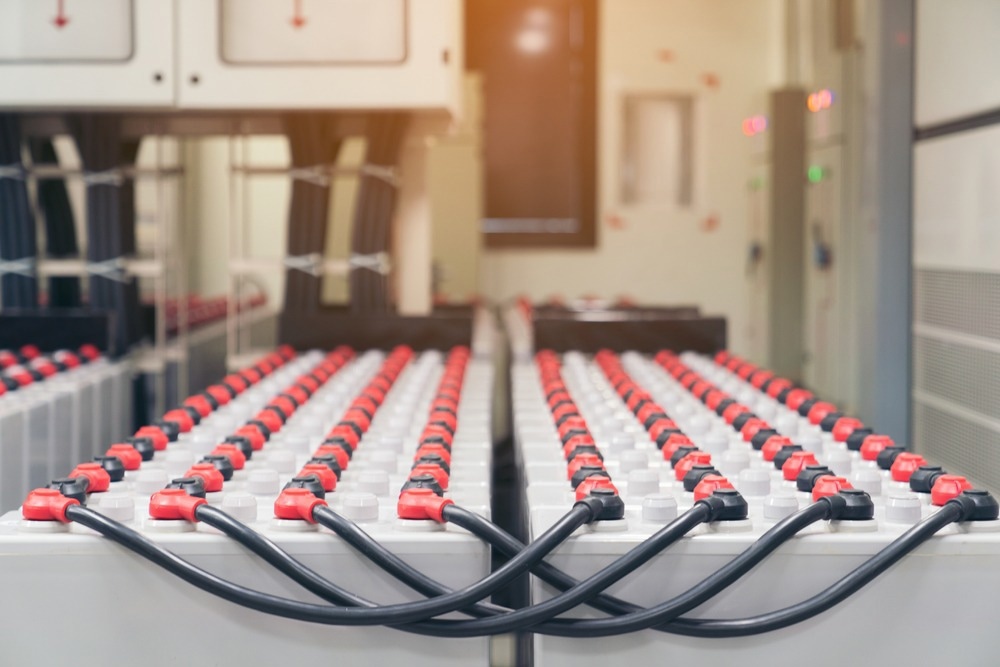
Study: Efficient recovery of lead and iron from disposal residues of spent lead-acid batteries. Image Credit: tong patong/Shutterstock.com
Background
Lead is a strategically important and versatile non-ferrous metal resource for the global economy as it is inherently associated with energy storage for renewables and automotive and backup power systems.
Higher demand for lead from different industrial and energy storage applications has led to a significant increase in the production of primary lead resources, such as cerussite and galena (PbS), around the world.
Rising production of primary lead resources has resulted in a rapid depletion of their reserves, which has shifted the focus on the recovery of lead from lead waste, such as discarded and spent lead-acid batteries (LABs).
LABs are used extensively owing to their high operational safety and low manufacturing cost. A substantial share of lead produced globally is used in LABs. Annually, millions of tons of LABs are discarded across the world, which can be used to recover the lead.
Recovering lead from discarded and spent LABs is relatively easier and less energy-dependent compared to the primary lead production from ores. Currently, the lead recovery plants primarily depend on pyrometallurgical methods for the lead recovery process.
100.0–350.0 kg of DR-LABs containing 1.2–22.0% of lead is generated for every ton of metallic lead production in the secondary lead recovery process. Thus, a significant amount of lead can be produced annually from DR-LABs, which necessitated the identification of an efficient process to recover lead from DR-LABs and make the disposal residues harmless.
DR-LABs are primarily composed of lead-rich phases such as lead, lead oxide (PbO), PbS, and iron-rich compounds, such as ferrous oxide (FeO), iron (II, III) oxide (Fe3O4), iron sulfide (FeS), and fayalite (Fe2SiO4). Among them, the Fe2SiO4 and PbS are the main iron- and lead-rich phases, respectively.
During the lead recovery process from LABs, the stable and abundant Fe2SiO4 produced by high-temperature smelting possesses binding effects or complex spatial position relationships with the lead compounds, which potentially results in a low leaching efficiency.
Although the concentration of iron in DR-LABs ranges from 20.1% to 55.7%, only lead is extracted during the metal extraction process, leading to the wastage of a significant amount of iron resources. Thus, a mechanism must be developed for the efficient recovery of iron and lead from DR-LABs based on the identification of spatial position relationships between lead compounds and Fe2SiO4.
The Study
In this study, researchers proposed a mechanism for the efficient recovery of iron and lead from DR-LABs based on the spatial position relationship identification between Fe2SiO4 and PbS.
Specifically, researchers obtained the spatial position relationships between Fe2SiO4 and PbS of DR-LABs, assessed the feasibility of using sodium hydroxide (NaOH) to release the Fe2SiO4-bound PbS, identified the mechanism and pathway of Fe2SiO4 destruction, and evaluated the recovery of iron and lead by acid leaching, followed by pH adjustment using an alkaline waste solution.
Initially, DR-LABs were dried for 12 h at 100 oC, crushed using a jaw crusher, and screened to control the size of the crushed particles from 0.08 mm to 0.16 mm in a sequential manner. Subsequently, the influence of different NaOH concentrations and liquid-solid (L/S) ratio on DR-LABs treatment were investigated.
Experiments were conducted using NaOH/DR-LABs with 10:1, 9:1, and 8:1 (S/S) mass ratio under the conditions of 15:1 of L/S mass ratio and 300 r/min mechanical stirrings for six hours at 140 ℃ and using deionized water/DR-LABs with 15:1, 12.5:1, and 10:1 L/S mass ratio under the conditions of 10:1 of S/S mass ratio and 300 r/min mechanical stirrings for six hours at 140 ℃.
Moreover, the influence of five, four, and three h of reaction times and 140, 120, and 100 ℃ temperature gradients on the reaction were also evaluated. Eventually, the residue obtained after the reaction was collected, cleaned, and vacuum-dried for subsequent tests.
HNO3 acid leaching tests of treated DR-LABs were performed to recover iron and lead from the residue, and the optimum conditions of nitric leaching were determined. The residue obtained after HNO3 leaching was vacuum-dried. Researchers then analyzed the magnetic separation, iron abundance, and phase of the residue.
Researchers also determined the iron and nitrate content, calculated the recovery efficiency of the total lead, and investigated the decomposition mechanism and pathway of Fe2SiO4 by NaOH using density functional theory (DFT) calculation.
X-ray diffraction (XRD), field-emission scanning electron microscopy (FE-SEM), energy-dispersive spectroscopy (EDS), Fourier transform infrared (FTIR) spectroscopy, Raman spectroscopy, and a double–beam digital ultraviolet-visible (UV–vis) spectroscopy were performed for characterization of DR-LABs.
Observations
Three positional relationships, including loading, embedding, and wrapping, were identified between Fe2SiO4 and PbS in DR-LABs. Among them, wrapping was the strongest positional relationship between Fe2SiO4 and PbS in DR-LABs.
PbS was exposed efficiently on the DR-LAB surface after Fe2SiO4 destruction when the NaOH/DR-LABs S/S mass ratio, deionized water/DR-LABs volume L/S mass ratio, reaction time, and temperature were 10:1, 10:1, 4 h, and 140 oC, respectively.
The Fe2SiO4 phase transformation, pH adjustment, and acid leaching occurred at a relatively low temperature with efficient iron and lead recovery. 98.9 wt% of lead was recovered from DR-LABs as lead (II) hydroxide/iron (III) hydroxide/iron (II) hydroxide Pb(OH)2 /Fe(OH)3/Fe(OH)2 by acid leaching, followed by pH adjustment.
The relative abundance of FeO and Fe3O4 in the acid leaching residue that can be recovered magnetically as raw material was 66.1%, while the relative abundance of Fe(OH)2 recovered at 9.5 pH was 57.3%. Overall, 90.3% iron was obtained from the recovery process as raw material.
Theoretical and experimental investigations confirmed that NaOH induced hydroxylated Fe2SiO4 (010) surface formation and the near-surface Na+ substitution, which modulated the coordination environments and local electronic structures of Fe2SiO4 and facilitated the Fe2SiO4 to FeO phase transformation.
Conclusion
To summarize, the findings of this study demonstrated the feasibility of using the proposed strategy to realize efficient recovery of iron and lead from DR-LABs. The proposed mechanism for lead and iron recovery from DR-LABs made full utilization of the DR-LABs and reduced the need to mine the primary iron and lead ore. Low carbon dioxide emission and energy consumption are the other major advantages of the method.
However, a part of iron was leached during the HNO3 leaching process and precipitated with lead ions due to the non-selectivity and strong acidity of HNO3. Previous studies have shown that the addition of hydrogen peroxide can effectively prevent iron leaching Thus, more research is required to focus on selective leaching of iron and lead to improving the magnetic iron recovery efficiency and lead abundance.
More from AZoM: How Does Laser Cleaning Technology Function?
Disclaimer: The views expressed here are those of the author expressed in their private capacity and do not necessarily represent the views of AZoM.com Limited T/A AZoNetwork the owner and operator of this website. This disclaimer forms part of the Terms and conditions of use of this website.
Source:
Zhu, N., Li, F., Wu, P. et al. Efficient recovery of lead and iron from disposal residues of spent lead-acid batteries. Resources, Conservation and Recycling 2022. https://doi.org/10.1016/j.resconrec.2022.106614