A team of researchers recently published a paper in the journal Additive Manufacturing that demonstrated the feasibility of using a three-dimensional (3D)-printed electrically conductive silicon carbide (SiC) ceramic fabricated using the vat photopolymerization 3D printing technique to address the temperature-dependent electrical property of conventional electrically conductive ceramics (ECCs) at high temperatures.
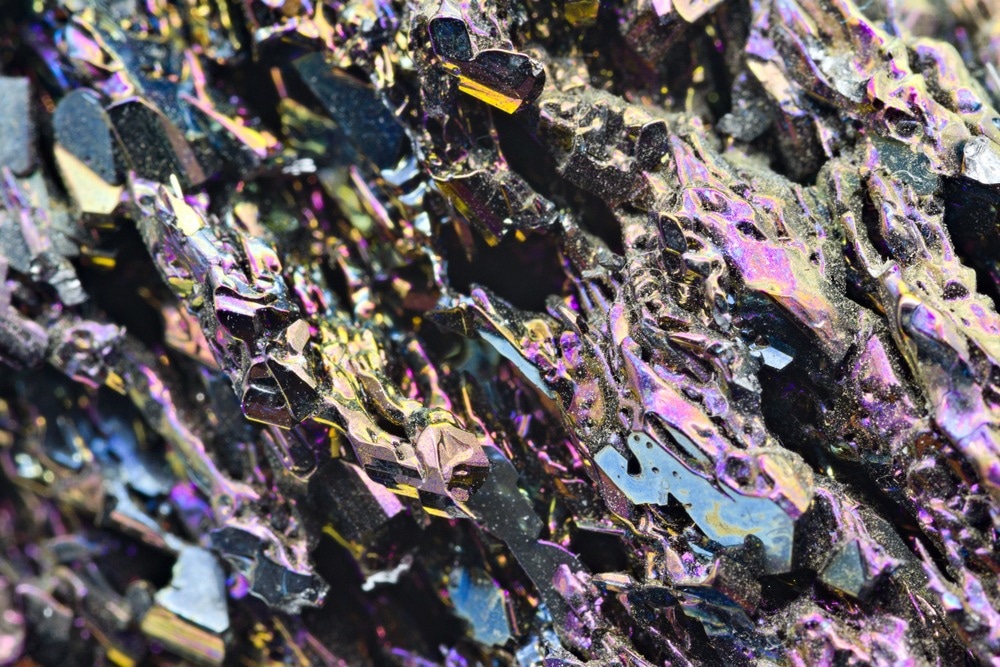
Study: 3D-Printed Electrically Conductive Silicon Carbide. Image Credit: Marco Fine/Shutterstock.com
Background
Electrically conductive ceramics (ECCs) are used in several applications, such as batteries, gas sensors, fuel cells, and catalyst supports, owing to their high thermal conductivity, enhanced wear and corrosion resistance, and greater stiffness at elevated temperatures.
Although the dense structure of the ECC facilitates a higher thermal conductivity, it hinders the thermal management capability of the ceramic. Thus, an ECC typically demonstrates a temperature-dependent electrical behavior at high temperatures.
The ECC structure must be designed at several length scales, from macroscopic to nanoscopic, to develop a conductive ceramic that displays a high electrical conductivity and electrical stability at temperatures above 600 oC.
However, readily machining ceramics into complex shapes is difficult owing to their brittle nature. Additive manufacturing (AM)/3D printing is considered a suitable method to fabricate 3D-printed ECCs with customized architectures.
Currently, the research on AM of ECC is primarily focused on the use of semiconductors, such as SiC, as the input material for 3D printing and fabrication using binder jetting or direct ink writing techniques.
However, structures printed using these AM techniques demonstrate limited resolution and do not possess the electrical property required to realize practical applications, such as catalyst and microwave optics.
Among the different 3D printing techniques, the vat photopolymerization 3D printing is more suitable to print cellular- or lattice-like ceramics as it allows accurate manipulation of the printed macroscopic structures and high-resolution printing of fine features.
The hollow ceramic structures obtained post-heat-treatment of the ceramics printed using the vat photopolymerization technique are lightweight and demonstrate a similar stiffness as solid ceramics.
Moreover, the filler material is distributed uniformly in the 3D space during the AM process due to the layer-by-layer configuration of this printing technique, which promotes electrical conductivity in the fabricated structure.
The Study
In this study, researchers used the vat photopolymerization 3D printing technique, a bottom-up additive manufacturing approach, to fabricate 3D electrically conductive SiC ceramic architectures that simultaneously possess low thermal conductivity and high electrical conductivity.
Mesoporous silica possessing nano-sized porous structures and a high specific surface area was used as the feedstock material to realize the thermal insulation characteristics effectively. Graphene, an electrically conductive filler material, was incorporated into the ceramic mix to allow the formation of an electrically conductive network in the ceramic.
Initially, poly (ethylene glycol) diacrylate (PEGDA), graphene, and 15 wt% mesoporous silica were mixed to obtain a graphene/silica mixture. 0.5 wt% phenylbis (2, 4, 6-trimethylbenzoyl) phosphine oxide was then added to the as-prepared mixture as the ultraviolet (UV) light photoinitiator. Additionally, 0.04 wt% 2-nitrophenyl phenyl sulfide, the light absorber, was also added to facilitate high-resolution printing.
The weight ratios of the porous silica and graphene varied from 0.015 wt% to 0.1 wt%. A dispersing agent was added to the mixture by two wt% of the PEGDA to prevent solid particle sedimentation and aggregation. A sonicator was employed to mix the precursor for two hours to prepare the graphene/silica ink.
A custom-programmed slicing software was utilized to slice the 3D computer-aided design (CAD) models to mask images with 50 μm layer thickness, while a custom-programmed control software was employed to synchronize the build-platform motion and mask image projection.
Subsequently, a customized mask image projection-based vat photopolymerization printer was employed for the AM of the porous silica/graphene nanocomposites. The as-printed 3D ceramic structures were sintered using the spark plasma sintering (SPS) process.
Scanning electron microscopy (SEM), thermogravimetric analysis (TGA), and high-resolution transmission electron microscopy (HR-TEM) were used for the characterization of the sintered printed conductive ceramics. Researchers also measured the density, electrical conductivity, and thermal conductivity, and evaluated the mechanical properties of the printed samples.
Observations
3D electrically conductive porous SiC ceramic samples were fabricated successfully using the vat photopolymerization printing technique.
The synthesized photosensitive ink was dark as the graphene content effectively absorbed light spanning from the visible to the near-UV region, which can adversely affect the printing quality by preventing the light from penetrating the ink during the vat photopolymerization printing.
Thus, a 1080P projector with a 385 nm UV light was used as the light source for the mask image projection-based vat photopolymerization system after measuring the absorption spectrum of the graphene/silica ink.
Although higher UV intensities cured the ink at a faster rate, the maximum single-layer curing depth observed was 0.217 mm, and no further increase in the curing depth was observed even at higher UV intensities. The vat photopolymerization printing layer thickness was set at 0.05 mm to print structures with good structural integrity.
In the graphene-silica nanocomposites, the graphene sheet was wedged into the porous silica scaffold. After pyrolysis, graphene percolated into the siloxane network and formed the robust SiC-silica matrix.
An amorphous structure was observed in the printed samples when the sintering temperature was less than 1400 °C, while β-phase SiC and silicon dioxide cristobalite were observed at 1400 °C, indicating that a portion of silicon-oxygen bonds was replaced by the silicon-carbon bonds and the porous feedstock silica was crystallized in an inert and high-temperature environment.
The carbon substances that did not form silicon-carbon bonds were percolated on the silica skeleton and created lots of pores. Additionally, new pores were formed due to the volatilization of carbonyl and methylene groups as gases. These two factors played a crucial role in limiting significant shrinkage at high temperatures. Thus, no substantial shrinkage was observed in both printed and sintered samples.
Mesoporous structures were observed in the sintered conductive ceramics, with 10-150 nm pore size. The 3D-printed conductive ceramics displayed a low thermal conductivity, ranging from 62 to 88 mW/mK. A slight increase in thermal conductivity was observed with the rising concentration of graphene due to the strong in-plane bonding of graphene.
The printed porous sample effectively insulated the heat transfer, and the sample temperature was successfully maintained at 89.2 °C, indicating its exceptional thermal performance.
0.02 wt% graphene/silica samples withstood maximum compressive stress of 46.625 MPa, while the highest compressive strain of 0.142 at failure was observed in conductive ceramics with 0.10 wt% graphene/silica nanocomposites.
SPS treated 0.10 wt% graphene/silica graphene-silica nanocomposites displayed the maximum compressive strength of 57.947 MPa, which was 96.19% higher compared to the untreated sample, indicating that the SPS treatment effectively reinforced the mechanical performance of the sample.
The electrical conductivity increased with the rising graphene concentration from 0.02 to 0.1 0 wt%, indicating the formation of conductive pathways due to graphene percolation. The highest electrical conductivity was 680 S m−1 in the printed conductive ceramics, which was substantially higher compared to conventional conductive ceramic composites due to the high specific surface area provided by the porous feedstock silica for graphene percolation.
The minimum and maximum bulk density values of the 3D-printed ceramic were 0.366 g cm-3 to 0.897 g cm-3, respectively, and the sample demonstrated an extremely lightweight structure. Moreover, the 3D-printed conductive ceramics displayed a stable electrical performance when used in an electric circuit consisting of 64 light-emitting diodes (LEDs) and a 5V DC-powered microcontroller board.
The printed ceramic maintained a constant resistivity from room temperature to 600 °C due to its good thermal management capability, indicating that the 3D-printed SiC was less prone to temperature changes. Additionally, the porous structure created a thermal barrier to maintain stable electrical conductivity and protect the conductive network.
To summarize, the findings of this study demonstrated the feasibility of using the 3D-printed electrically conductive porous SiC ceramic in applications operating in high-temperature environments and effective strategies to address the temperature-dependent electrical property of conventional metallic conductors.
More from AZoM: How Does Laser Cleaning Technology Function?
Disclaimer: The views expressed here are those of the author expressed in their private capacity and do not necessarily represent the views of AZoM.com Limited T/A AZoNetwork the owner and operator of this website. This disclaimer forms part of the Terms and conditions of use of this website.
Source:
Chivate, A., Khuje, S., Armstrong, J. et al. 3D-Printed Electrically Conductive Silicon Carbide. Additive Manufacturing 2022. https://doi.org/10.1016/j.addma.2022.103109