A team of researchers recently published a paper in the journal Composite Structures that demonstrated the feasibility of using lower-order models to analyze and optimize the dynamic and steady performance of marine composite hydrofoils.
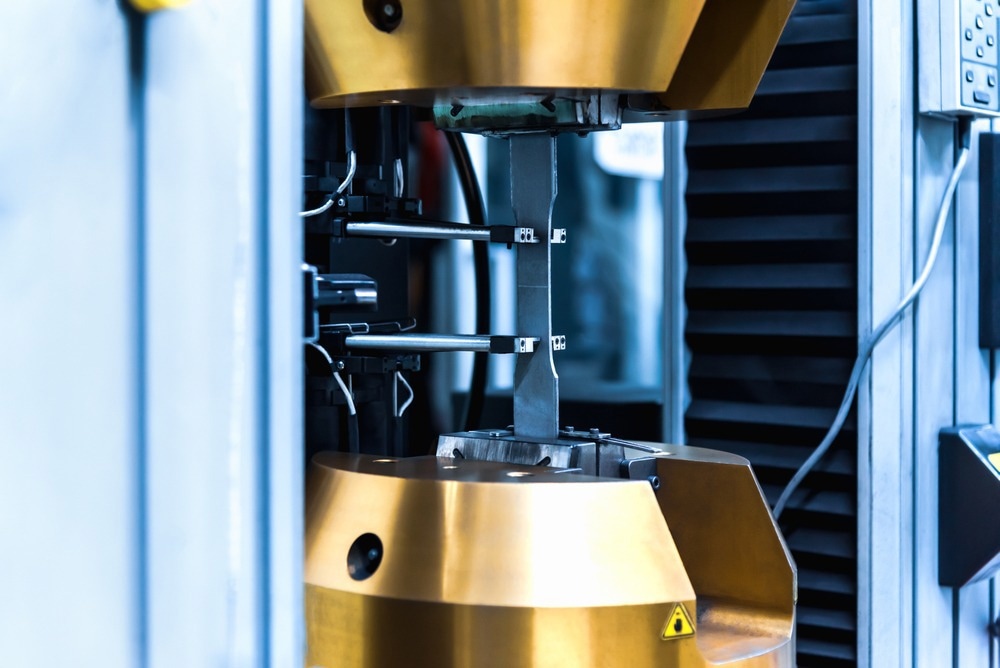
Study: Optimizing steady and dynamic hydroelastic performance of composite foils with low-order models. Composite Structures 2022. https://www.sciencedirect.com/science/article/pii/S026382232200839X?via%3Dihub Image Credit: N_Sakarin/Shutterstock.com
Background
In the maritime sector, lifting surfaces are used extensively in hydrofoils, propellers, fin stabilizers, bilge keels, and energy harvesters. They are crucial components that substantially affect the overall efficiency and performance of marine platforms and vessels.
Marine composites are more advantageous to lifting surface design compared to conventional metallic marine structures due to their reduced manufacturing cost and lower structural weight.
Moreover, the load-dependent static hydroelastic response can be tailored in marine composites at several operating conditions by carefully designing the fiber layups to enhance the overall efficiency compared to the rigid lifting surfaces.
Marine composite lifting surfaces have attracted considerable attention owing to the advances in materials science, manufacturing techniques, and computational modeling. However, controlling and predicting the dynamic and steady hydroelastic performance is a significant challenge in the marine composite lifting surface design.
Specifically, accelerated fatigue and excessive flow-induced vibrations can lead to severe issues if they are not considered in the initial lifting surface design. Previous design optimizations have overlooked the crucial dynamic aspects, such as various band gaps between modal frequencies in water compared to air and lower resonance frequencies, of the marine environment and only considered the steady performance.
The Study
In this study, researchers used lower-order models to obtain the dynamic and steady fluid-structure interaction behavior and optimize the design of composite hydrofoils. Lower-order models typically provide comprehensive insights into design trade studies and can be evaluated in an inexpensive manner. Thus, these models were selected to understand the ways to tailor the dynamic and steady performance of hydrofoils.
Researchers formulated multipoint objective functions and dynamic and steady constraints to obtain the speed-dependent effects on the dynamic response of the system and avoid system- and flow-induced vibrations caused by rigid body resonance frequencies, engine frequency, propulsor shaft and blade rates, and cavity shedding frequencies.
Dynamic composite foil (DCFoil), a composite lower-order hydrofoil model experimentally validated against published hydroelastic and aeroelastic results, was used in this study. The hydrofoil was modeled as a canonical cantilevered beam as it can be represented in different structures such as propellers, fins, and rudders.
The problem size was reduced to only three material and geometric design variables, including sweep angle, fiber angle, and angle of attack. Researchers used a heuristic optimization method, which was suitable for the reduced problem size and provided the freedom to adjust the optimal design based on viscous and submergence effects that were not captured in the model.
A formal optimization algorithm, such as a genetic algorithm or particle swarm method, was not employed due to these unmodeled parameters as it could lead to highly swept designs with high fiber orientation angles. Merit constraints and functions were used in place of a formal optimization algorithm to make more informed decisions about the optimal design variables.
Multiple design speeds were considered in the optimization of composite hydrofoils due to changing steady loads, damping, and natural system frequencies corresponding with the flow speed. Researchers also assessed the role played by water in lowering the natural frequencies of the system and changing the band gaps between optimization modes that substantially change the design problem.
However, the computational time of this study increased significantly due to the use of a scripted language/Matrix Laboratory (MATLAB). The time was higher for several discrete frequencies as each forcing frequency required a solution of governing equations.
Overall, 2000 discrete frequencies were analyzed between 0 Hz and 200 Hz for the full-scale hydrofoil model. Every frequency response analysis for a designed run required 30 min and a total of nine h of simulations were performed for 18 full runs, which was not practically feasible for design optimization.
Observations
This study successfully realized the first dynamic and steady hydroelastic optimization of marine composite hydrofoils that uses both geometric and material design variables, considering multiple operating points and modal coalescence.
An optimized composite hydrofoil with better dynamic and steady performance was produced using the merit constraints and functions compared to the baseline design while avoiding excessive deflections, dynamic instability, dynamic load amplification, noise, vibrations, and accelerated fatigue and satisfying the steady lift requirements.
Resonance frequencies were sufficiently far from wave frequencies, cavity shedding frequencies, impeller blade, and impeller shaft rate frequencies, engine frequencies, and rigid body modes. Researchers also avoided frequency coalescence, which was not addressed in the previous hydrofoil design optimizations.
The optimized hydrofoil was damped and stiffer at critical frequencies due to the slight forward fiber and slight backward sweep angles caused by the relative contributions of the generalized fluid forces in the coupled equations of motion. However, severe sweep and fiber angles led to lower critical instability speeds and frequency coalescence.
Dynamic hydroelastic performance was tuned easily in different ways in the marine composite lifting surface design compared to aircraft lifting surface design as the marine composite design avoided greater fluid de-stiffening effects and exploited more significant hydrodynamic damping effects.
Dynamic characteristics of the baseline hydrofoil changed with the flow speed, increasing the possibility of resonance of the hydrofoil with the waterjet impeller frequency. The optimized hydrofoil avoided resonance with all external frequencies, including the waterjet frequency, for the set design speeds.
However, the resonance frequency of mode two crossed the waterjet impeller frequency between the design speeds with a positive damping loss factor. Although the transient resonance can create issues, it was still better than resonance or lock-in at a design point. Thus, the optimized composite hydrofoil was superior to that of the baseline hydrofoil.
Significant differences in the system pole behavior were observed for both optimized and baseline hydrofoils across the speed sweep when in-water to in-air loci plots were compared.
Conclusion and Future Outlook
To summarize, the findings of this study demonstrated the feasibility of using low-order models to effectively optimize the dynamic and steady hydroelastic performance of marine composite foils and the importance of considering the in-water dynamic performance to avoid erroneous results while analyzing the dynamic performance of marine composite foils.
However, the model did not integrate the memory and viscous effects in time domain simulations, leading to overprediction of the motion amplitudes. In the future, high-fidelity computational models can be used to refine the steady performance of the optimized hydrofoil design to improve several characteristics, including material failure avoidance, flow separation, cavitation avoidance, and lift-drag ratio. Accurate damping forces from memory and viscous effects must be considered in higher fidelity models as these effects contribute to damping.
Multiphase and depth flow effects on added mass and damping must also be considered in future optimizations as small amounts of ventilation and cavitation, or changing depth can lead to potential lock-in, modal coalescence, or resonance.
Additionally, the effect of taper and twist on dynamic performance must be evaluated as they alter the structural and flow performance. Future studies can use a probability density function on critical frequencies to model the variations in excitation frequencies over the operating envelope.
Researchers also proposed using a gradient-based method to decrease the number of function evaluations in the future. The computational performance can be further enhanced using parallelizing processes and a compiled coding language.
Disclaimer: The views expressed here are those of the author expressed in their private capacity and do not necessarily represent the views of AZoM.com Limited T/A AZoNetwork the owner and operator of this website. This disclaimer forms part of the Terms and conditions of use of this website.
Source:
Martins, J. R. R. A., Ng, G. W., Young, Y. L. Optimizing steady and dynamic hydroelastic performance of composite foils with low-order models. Composite Structures 2022. https://www.sciencedirect.com/science/article/pii/S026382232200839X?via%3Dihub