By Surbhi JainReviewed by Susha Cheriyedath, M.Sc.Sep 12 2022
In an article recently published in the journal Additive Manufacturing, researchers discussed a technique based on optics for the calculation of oxygen concentration in recycled metal powders for additive manufacturing (AM).
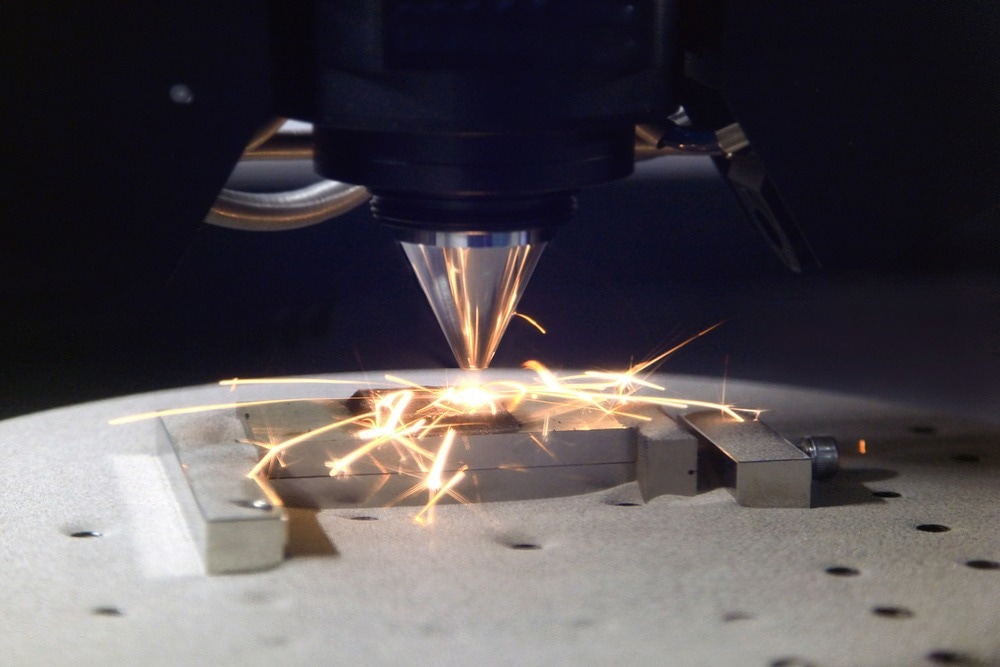
Study: Optical-based method to estimate the oxygen content in recycled metal powders for additive manufacturing. Image Credit: sspopov/Shutterstock.com
Background
The capacity to recycle the leftover metal feedstock without the need for remelting and reforming is one of the characteristics that make powder-based AM methods a sustainable alternative to conventional metal production. Recycled powders are often only utilized a couple of times before being remelted and made using energy-consuming techniques.
Studies have shown that powders recycled using laser powder bed fusion (L-PBF) methods underwent modifications in both their behavior and physical appearance. Even though L-PBF procedures take place in an inert atmosphere, the moisture that remains in powders or adsorbs on the surface of the printing chamber is enough to encourage the development of a thin oxide coating that surrounds particles as they heat up. To ensure dependable L-PBF processes and the creation of uniform builds, it is crucial to monitor and keep the oxygen level in the powder feedstock below a predetermined threshold.
Rejuvenating recycled powders is a popular industry procedure to reach this objective. Identifying the correct age of the feedstock for powder rejuvenation is the key challenge before moving on to combining virgin powder. However, several factors affect how quickly powders age. These and other parameters could differ from one construction to the next, which makes it challenging to estimate the age of the powder. Keeping track of the powder recycling time is difficult, even when parts are made in series using the same process settings, particularly when utilizing commercial L-PBF machines with an auto powder recycling system.
About the Study
In this study, the authors discussed a quick and low-cost method for the optical acquiring of the recyclability of a powder batch during the powder recoating stage. The high-resolution optical images of various powder batches were acquired by using a powder bed scanner, and their relative oxygen content was calculated by evaluating the color of individual powder particles, which was a function of the thickness of the surface oxide layer. These measures were compared to those acquired using traditional methods, and it was determined that the proposed method produced results with higher sensitivity and greater consistency.
The team identified a method for the enhancement of the recyclability of metal powders by continuously tracking their appearance throughout additive manufacturing procedures. An optical-based characterization technique was provided that offered quick and precise assessments of the oxygen content in powders in comparison to a reference value. The proposed approach made use of the powder bed scanner (PBS) technology, which captured vivid, high-resolution images of a powder bed. The oxidized particles’ fraction and their color were quantified to estimate the degree of oxidation in various batches of SS316L powders using digital image processing and numerical image analysis.
The researchers stated that the proposed tests relied on a property of heat-tintable metals and alloys known as the relationship between particle color and oxide layer thickness. The powder age was estimated by using the suggested method. Ex-situ oxygen content testing could be done using the approach as a stand-alone platform. The proposed approach could be used in an L-PBF system to do an in-line assessment of the conditions of the powder feedstock.
Observations
The time required for data analysis on a business desktop computer was significantly under 30 seconds for each sample. According to the results, the proposed method was reliable enough to predict the oxygen concentration from a raw scan with as few as 4000 particles. For all powder samples except the S1-600, the suggested color particle detection algorithm computed the fraction of oxidized particles with 96% accuracy.
36.9% of the oxidized particles in this sample had an S value that was within the virgin threshold, according to the 63.1% detection result. The benchmarking oxygen content and the other two methods exhibit good agreement.
The incorrect color particle identification was responsible for the decline at 600°C. The finding suggested that because badly oxidized particles' colors were too close to those of virgin powders, those whose colors were outside of the S1-550 color range could not be identified and properly accounted for in the computation of bulk oxygen content.
The difference between S3-HVED and S3-LVED was significantly greater than the difference between S3-LVED and V, and OPBS increased monotonically toward volumetric energy density (VED). The specific oxygen concentration variances were 2.5 and 0.5 parts per million.
Conclusions
In conclusion, this study offered a quick and precise optical-based approach to assessing the oxygen content of recycled powders in comparison to a reference value. Metals and metal alloys that were heat-tintable could easily be used with the proposed technique. A series of studies were conducted using SS316L powder as a case study material, and it was verified that the proposed approach was superior to standard inert gas fusion (IGF) in terms of measurement consistency, sensitivity, and amount of information delivered.
It was shown that even after just one cycle, the proposed approach could quantify the minute variations in oxygen content between these powders. The technique could be applied in situ to continually track the oxidation rate of powders during fusion-based AM processes or ex situ to inspect various powder batches and gauge their age. It could also be used to gauge the quality of virgin powders from various vendors.
The authors mentioned that with the newly gained knowledge, a more sustainable method for maintaining a steady supply of powder feedstock could be achieved.
References
Le, T-P., Wang, X., Seita, M., Optical-based method to estimate the oxygen content in recycled metal powders for additive manufacturing. Additive Manufacturing, 103127 (2022). https://www.sciencedirect.com/science/article/abs/pii/S2214860422005164
Disclaimer: The views expressed here are those of the author expressed in their private capacity and do not necessarily represent the views of AZoM.com Limited T/A AZoNetwork the owner and operator of this website. This disclaimer forms part of the Terms and conditions of use of this website.