By Surbhi JainReviewed by Susha Cheriyedath, M.Sc.Sep 26 2022
In an article recently published in the journal Additive Manufacturing, researchers discussed the overlapping effect of melt pools in powder bed fusion based on a novel prediction method.
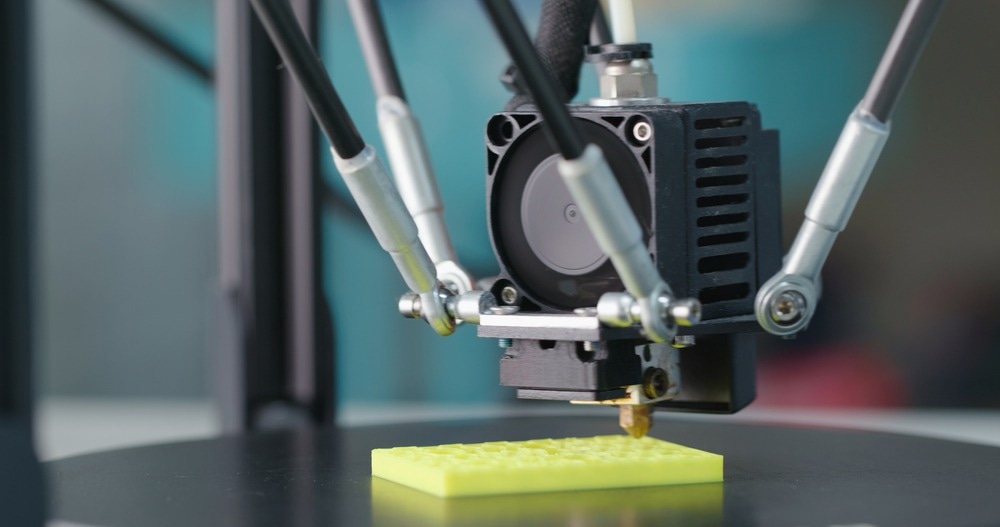
Study: A study on overlapping effect of melt pools in powder bed fusion based on a novel prediction method. Image Credit: leungchopan/Shutterstock.com
Background
In today's industries, metallic components are frequently used. Metal components with better performance are required for ongoing industrial innovation. Rapid prototyping technology gave rise to metal additive manufacturing (AM), often known as 3D printing, which has since evolved into a process that can create parts for a variety of purposes. The fundamental workings of processing units and how they interact must be thoroughly studied to make use of the design flexibility offered by AM.
Determining the solidification and heating behaviors in a single or overlapped melt pool is challenging since processing units are produced at micrometer spatial scales and solidify at millisecond temporal scales.
To monitor the transient heat reaction during the laser powder bed fusion (LPBF) process, thermal imaging technology has recently been employed. The tendency of melt pool dimensions to change with processing settings has long drawn a lot of interest. The majority of research has only looked at one or two nearby melt pools' worth of layers, which is very different from the actual circumstances that exist during additive manufacturing.
The micro-scale melt pools and the ensuing overlapping of those melt pools are the sources of all the distinctive benefits that set AM apart from other processing technologies. Existing research, however, has concentrated on the individual effects of processing factors on fabrication quality. This has led to a dearth of practical prediction algorithms that can swiftly ascertain the operation window during actual production, as the optimal processing parameters of several reports are based on entirely distinct energy input levels.
About the Study
In this study, the authors used Python and laser powder bed fusion to develop a novel reconstruction model for melt pool overlapping. This model's melt-pool dimensions could be obtained through experimentation or foreseen using normalized enthalpy. The periodic regulation of deposition, which aided in simplifying the microstructure created by serial melting and layer-by-layer deposition, was proposed to cause the overlapping unit.
Based on the average number of melting cycles (NMC) of the overlapping unit and the predicted thermal history, the overlapping effect and its effects on elemental losses, defect formation, and microstructure evolution was subsequently explored.
The team inferred that NMC was positively connected with the loss of elements with low boiling points as a result of repeated vaporization. While hole flaws predominated in regions that melted more than six times, the majority of incomplete defects occurred in regions that melted less than twice. Furthermore, melt pool overlapping and heat accumulation caused changes in the fine-grained area, which had an average diameter of fewer than 1 μm. Overlapping could increase the sample temperature, which could increase the size and number of precipitates.
The researchers presented a novel approach to optimize overlapping circumstances to enhance the microstructure and mechanical properties of materials. A dimension prediction method was used to offer a more accurate description of the melt pool profile. The geometric link between melt pools served as the foundation for a practical prediction model that was created using Python to forecast overlapping. Numerical simulation was utilized to estimate the thermal information, which could be used to support the research on the overlapping effect. The developed model was used to investigate the defect generation, precipitation, and solidification that occurred during LPBF processing.
Observations
The majority of errors in the experimental and forecast results had diameters lower than 10 μm. Incomplete fusion flaws were among the other defects, which were in the diameter range from 14 to 24 μm. The size distribution trend of defects with widths between 14 and 24 μm was quite similar and well predicted. While scanning-related parameters had an impact on how melt pools overlap, this phenomenon also contributed to heat buildup. The findings showed that the overlap of melt pools and the subsequent buildup of heat were directly related to defects, microstructure, and precipitates.
The input energy density and the separation between melt pools in both X/Y and Z directions had the most effects on the NMC. The accumulation of heat was the result of multiple melting, which the NMC could reflect. Increased remelting and a more substantial heat buildup effect were correlated with higher NMC. The loss of elements with low boiling points was increased during the formation process. Since pore flaws were not taken into account, the anticipated relative density of 97.53% was slightly greater than the actual number. Additionally, due to oscillations in the melt pool, no fusion flaws were seen in the area where the melt only happened once.
Under a stronger heat buildup effect, which was brought on by a higher NMC, hole flaws had a propensity to occur easily. NMC could be kept within a specific range by using the right processing parameter combination. Since only a piece of the solidified structure was preserved in a single melting step, both overlapping and the heat buildup that resulted had an impact on the FGZ ratio. The repeated melting and ensuing heat buildup caused the sample temperature to be higher. As a result, at a higher sample temperature, precipitates increased in quantity and size.
Conclusions
In conclusion, this study explored the impact of melt pool overlapping and the heat buildup in the LPBF process. The authors mentioned that although these outcomes were seen for alloys based on aluminum and one type of stainless steel, the suggested method and mechanism might work for other alloys as well.
Based on the geometric link between layers, an overlapping unit was proposed as the fundamental periodic structure. The deposition structure was additionally condensed as an accumulation of these periodic sub-structures. An attempt was made to develop a linearized link between the ratio of FGZ, G/R ratio, and NMC. The findings presented a novel strategy for process optimization based on overlapping conditions to improve microstructure.
The team mentioned that the findings of this study would facilitate quick determination of the operation windows and provide recommendations for enhancing mechanical qualities in the first phases of manufacturing.
More from AZoM: A Review of Modern Wastewater Treatment Methods
References
Zhao, J., Wang, B., Liu, T., et al. A study on overlapping effect of melt pools in powder bed fusion based on a novel prediction method. Additive Manufacturing, 59, 103151 (2022). https://www.sciencedirect.com/science/article/abs/pii/S2214860422005401
Disclaimer: The views expressed here are those of the author expressed in their private capacity and do not necessarily represent the views of AZoM.com Limited T/A AZoNetwork the owner and operator of this website. This disclaimer forms part of the Terms and conditions of use of this website.