A new paper published online in the journal Additive Manufacturing has explored the question of how to strengthen pretreated aluminum during ultrasonic 3D printing methods.
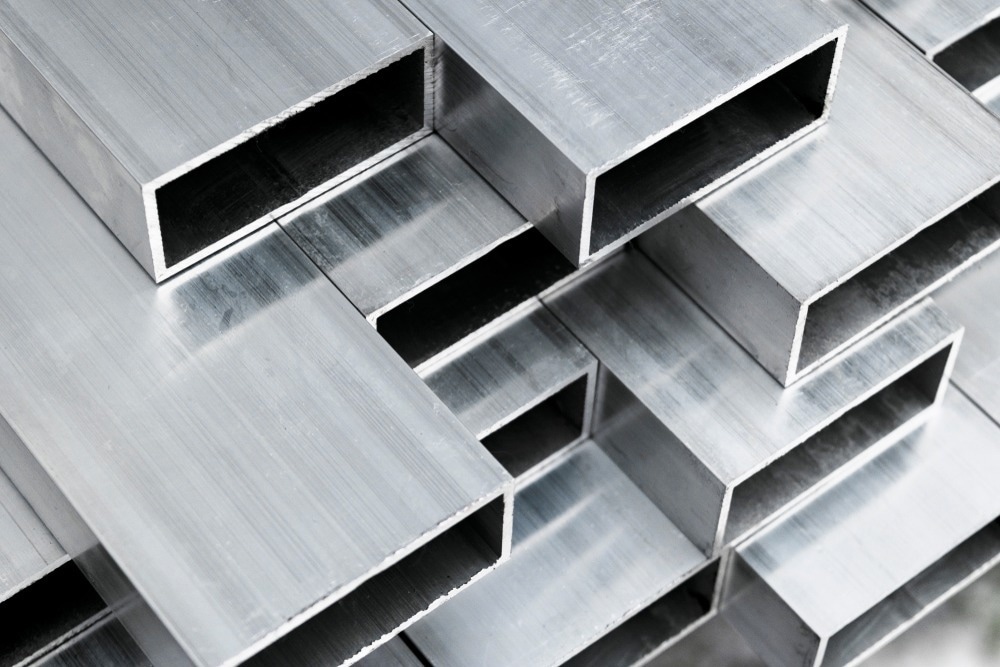
Study: Strengthening of Pretreated Aluminum During Ultrasonic Additive Manufacturing. Image Credit: BigTunaOnline/Shutterstock.com
Ultrasonic Additive Manufacturing
Additive manufacturing has emerged as one of the key disruptive technologies of the 21st century. It provides several benefits compared to conventional manufacturing approaches, including freeform design, multimaterial printing capabilities, low cost, and a lack of waste materials after construction.
Several additive manufacturing methods have been developed over the past few decades, including material extrusion processes, binder jetting, powder bed fusion, stereolithography, vat polymerization, and selective laser sintering.
Ultrasonic additive manufacturing has emerged in recent years as a suitable candidate for the production of constructs from difficult-to-weld or dissimilar materials. Materials that this method can process include aluminum-titanium, steel-nickel, nickel-aluminum, and aluminum-copper. Furthermore, ultrasonic additive manufacturing can produce engineering constructs such as novel cooling channels, strengthened composites, and sensor-embedded structures.
Ultrasonic additive manufacturing involves the use of ultrasonic welding to join thin laminate layers at relatively low temperatures. Welding new layers to previously deposited layers and/or selective removal of unwanted materials creates three-dimensional printed parts.
Evaluating the Mechanical Properties of Ultrasonic Additive Manufactured Parts
Several tests can be employed to evaluate the mechanical properties of parts produced using ultrasonic additive manufacturing methods. These include tensile tests, shear tests, nanoindentation testing, and microhardness tests.
Shear tests are commonly applied for the initial investigation of bonding strength in printed parts. Longitudinal tensile tests provide optimal information on the total build’s mechanical properties. Build-direction tensile tests, however, do not provide any more information than initial shear tests, as they only test the weakest interface.
Finite element modeling has also been employed in research, revealing the relationship between imposed plastic deformation and increases in dislocation density. This deformation action refines grain size in printed materials. Studies have suggested that the strength of materials can be potentially enhanced by nanometer-sized voids at printed interfaces, with dispersed dislocation barrier effects playing a key role.
Previous research has indicated that microvoids and shear bands are created at the interfaces of ultrasonic additive manufactured parts. When subjected to tensile load, interfaces can undergo negative behaviors such as brittle failure due to the coalescence of microvoids, leading to void creation and cracking. Decreased build strength compared to bulk values has been observed by some researchers.
Ultrasonic additive manufacturing can cause significant microstructural changes in materials due to the process’s high strain rate plastic deformation. Point defect vacancies and dislocation structures can be formed, although thus far, there has been a lack of experimental evidence to confirm this. Some studies have indicated that welds can age more rapidly than parts produced by other methods.
The Paper
The research has been conducted by scientists from the University of Tennessee, Ohio State University, the Technical University of Denmark, and Oak Ridge National Laboratory. The main focus of the paper is exploring the influence of pretreatments on the microstructure of aluminum parts produced using ultrasonic additive manufacturing and how this affects the mechanical strength of builds.
Pretreatments can have positive effects on the mechanical properties of printed parts and include annealing and T4 tempering. They can have an effect on the material’s thermomechanical energy state, producing energetically favorable precipitates.
The authors have conducted a thorough literature review of 121 current papers from the past five decades. The paper is supported by funding from institutions including the Air Force National Laboratory and the US Department of Energy.
Study Results
The authors performed rolling x-direction tensile tests on pretreated aluminum samples, revealing the microstructural evolution and strengthening effects of ultrasonic additive manufacturing of these parts. Tempered T4 and annealed O conditions of Al 6061 were evaluated.
Tensile testing results revealed that the strength of the bonded materials was significantly enhanced, with nanoindentation tests revealing much stronger foil-foil interfaces in the bonded aluminum parts than bulk foils. Overall strengthening was caused by changes in crystal lattices at the interface regions of the bonded materials.
Dynamic recrystallization and recovery and adiabatic heating caused microstructural changes, including increased aluminum lattice strain, the coalescing of mono-vacancies into vacancy clusters, point defect vacancy creation, and refined grain size in the printed and bonded material. Additionally, enhanced magnesium diffusion and dissolution of Mg2Si precipitates were observed.
A potential future research direction, as noted by the authors, could include varying the plastic deformation rate magnitude by changing processing parameters such as bonding temperature, induced plastic strain rate, and internal strain energy of materials.
Whilst a preliminary study on the effects of ultrasonic additive manufacturing and pretreatments on mechanical strength properties and microstructural evolution, this paper presents an in-depth knowledge base for future research.
More from AZoM: How are Graphene Batteries Made?
Reference
Pagan, M et al. (2022) Strengthening of Pretreated Aluminum During Ultrasonic Additive Manufacturing Additive Manufacturing Vol. 60 Part A [online, pre-proof] sciencedirect.com. Available at: https://doi.org/10.1016/j.addma.2022.103228
Disclaimer: The views expressed here are those of the author expressed in their private capacity and do not necessarily represent the views of AZoM.com Limited T/A AZoNetwork the owner and operator of this website. This disclaimer forms part of the Terms and conditions of use of this website.