A team of researchers recently published a paper in the journal Advanced Materials Interfaces that demonstrated the advantageous features of bacterial cellulose (BC)-based separators in lithium-sulfur (Li-S) battery applications.
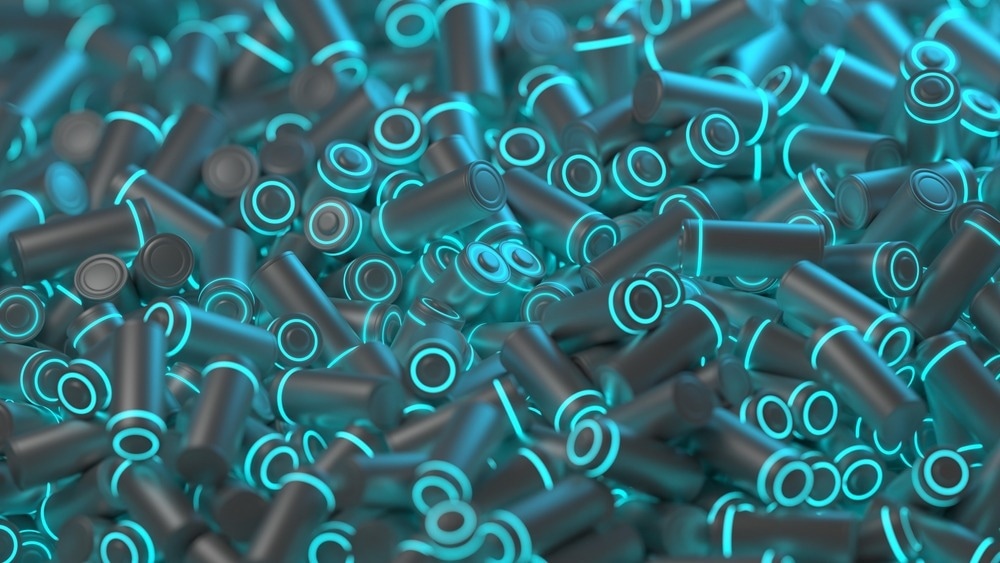
Study: Understanding the Advantageous Features of Bacterial Cellulose-Based Separator in Li–S Battery. Image Credit: RESTOCK images/Shutterstock.com
Background
Li-S batteries have gained considerable attention as next-generation energy storage systems owing to their eco-friendliness and high energy density. The separator is one of the critical components in Li-S batteries that influence the battery performance, as it separates the anode and cathode and prevents short-circuiting in the battery.
The separator influences the homogeneity between the electrolyte and electrode and the ion transport between electrodes. Polypropylene (PP) and polyethylene (PE) separators are used most extensively as battery separators. However, these separators demonstrate low selectivity for ion transport and poor compatibility with the Li anode, making them less suitable for Li-S battery applications.
Cellulose, an abundant, natural, and renewable resource, is considered a suitable alternative to conventional polyolefin separators used in various secondary batteries owing to its greater mechanical strength and high thermal stability, which ensures an enhanced safety performance.
The hydroxyl groups in cellulose facilitate the ion transport process regulation in the battery. Cells using cellulose-based masks as separators demonstrated a uniform Li anode morphology and exceptional charge-discharge performance for 200 h. Moreover, cellulose separators with nanopores displayed a dendrite-free performance for 500 h.
Although several studies have demonstrated the exceptional performance of batteries using different cellulose-based separators, a lack of detailed understanding of different advantageous features of cellulose-based separators, specifically BC-based separators, in Li–S batteries is hindering the large-scale use of these separators.
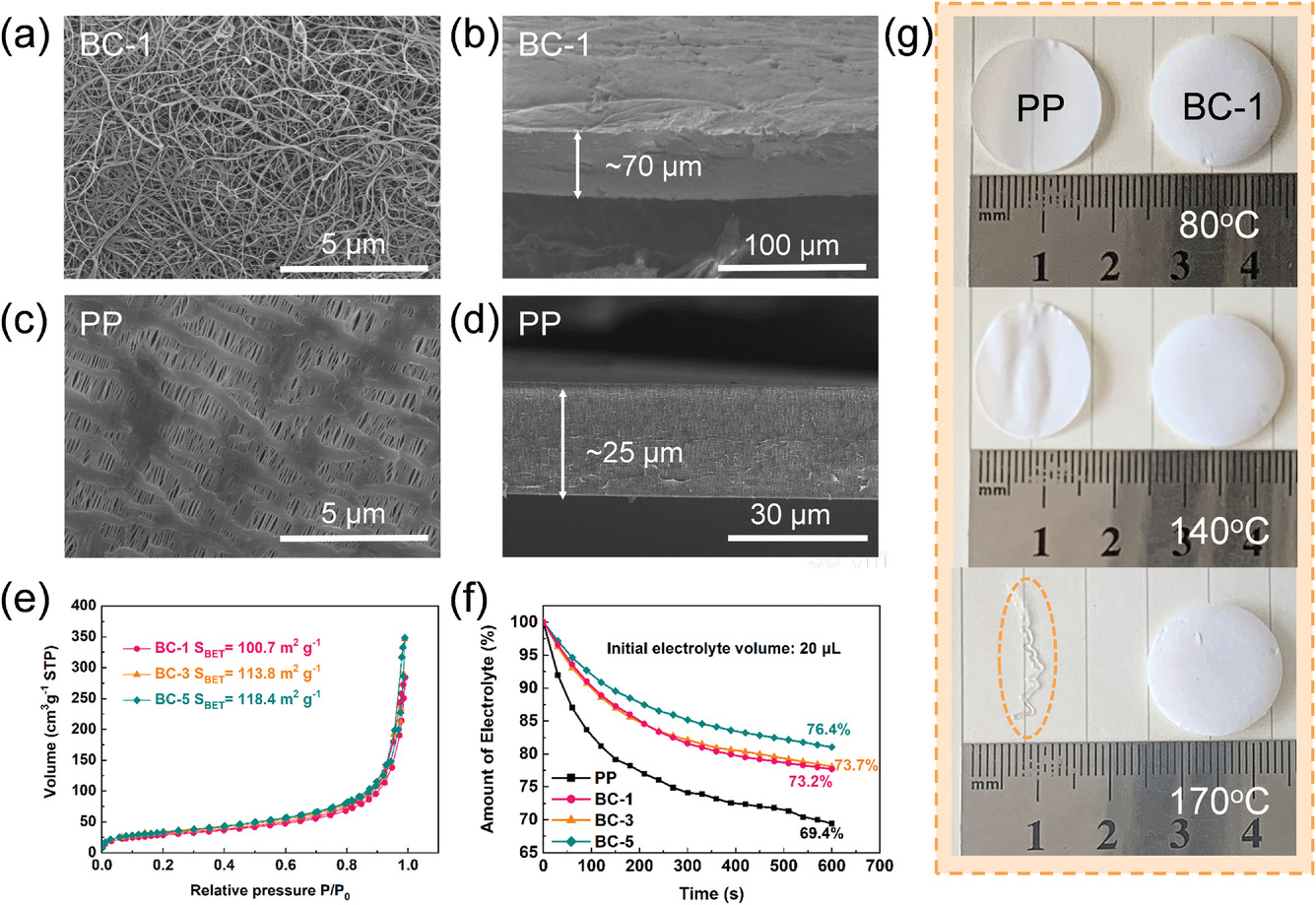
SEM images of the surface and cross-section of the BC-1 a,b) aerogel and c,d) PP separator. e) N2 adsorption–desorption isotherm of different BC aerogels. f) Electrolyte storage capacities of PP and BC separators. g) The thermal stabilities of different separators under different temperatures. Image Credit: Li, J et al., Advanced Materials Interfaces
The Study
In this study, researchers prepared BC separator models with different thicknesses and compared them with PP separators in terms of electrochemical performance. The objective of the study was to confirm the ability of cellulose-based separators to improve Li-S battery performance by regulating the lithium-ion (Li+) deposition on the anode and regulating the movement of ionic species, such as Li+ and lithium polysulfides (LiPS).
BC hydrogel, sodium hydroxide, and lithium sulfide were used as the starting materials. The BC separator thickness was controlled in a microbial fermentation process. In this process, a common aqueous nutrient media was used to cultivate the bacteria, and then BC was produced as an exopolysaccharide at the media/air interface.
A thick gel, referred to as pellicle, composed of 99% water and an interconnected three-dimensional (3D) porous BC nanofiber network was obtained. Subsequently, the protein in the BC hydrogel was eliminated by soaking it in a five% sodium hydroxide solution, heating it at 80 oC for several hours, and finally washing it using deionized water.
The resultant purified BC hydrogel was stored in an aqueous solution at 4 oC and then freeze-dried for 24 h at 10-6 bar pressure and −52 oC temperature to obtain the BC aerogel. Eventually, the BC aerogel was cut into 19 mm discs as separators with five, three, and one mm thicknesses and designated as BC-5, BC-3, and BC-1, respectively.
X-ray diffraction, scanning electron microscopy, Fourier transform infrared spectroscopy, and X-ray photoelectron spectroscopy were performed to characterize the synthesized samples. The dimensional changes of the separators were recorded at different temperatures to measure their thermal stability.
Researchers evaluated the electrolyte absorption rate, electrolyte storage capacities, and porosity of the separator. The Vienna ab initio simulation package was used to perform the theoretical simulation of the binding energies. Researchers also performed electrochemical measurements on the prepared BC separator samples and visual polysulfide shuttle tests.
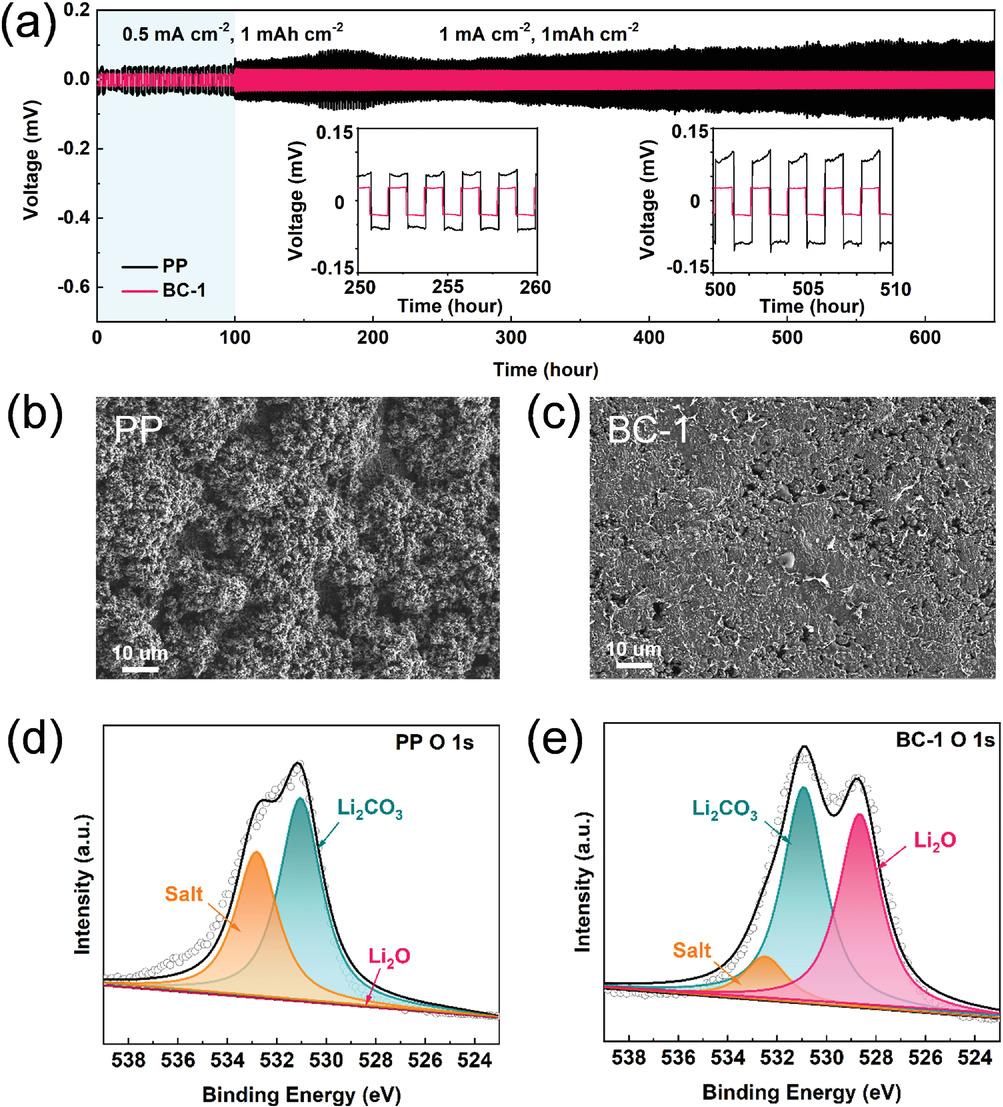
a) Voltage profiles of lithium symmetric cells with PP and BC-1. SEM images of cycled lithium anode surface (after 680 h) in symmetric cell with b) PP or c) BC-1. XPS spectrums of O 1s high-resolution of cycled lithium anode surface in symmetric cell with d) PP or e) BC-1. Image Credit: Li, J et al., Advanced Materials Interfaces
Observations
BC separators with varying thicknesses were synthesized successfully. The BC separators displayed better electrolyte uptake and wettability compared to commercial PP separators due to the abundance of hydroxyl groups and higher porosity, which improved Li+ transportation and enhanced the interface compatibility.
The separators also inhibited the formation of Li dendrites, leading to uniform deposition of Li on the anode. Additionally, the separators demonstrated high thermal stability, which improved the battery safety performance. Moreover, the BC oxygen functional groups suppressed the shuttling of soluble polysulfides by effectively adsorbing the polysulfides through electrostatic interactions.
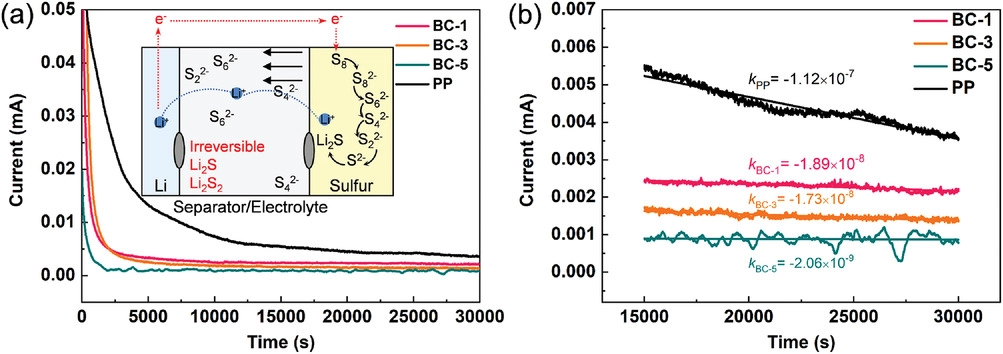
a) Shuttle currents of different separators; b) shuttle current decay rates are calculated after the steady-state current is achieved for a lithium–sulfur cell. The algebraic equations express the decay rate. Image Credit: Li, J et al., Advanced Materials Interfaces
The symmetrical cell with BC separator demonstrated safe electrochemical performance for 680 h due to the formation of lithium oxide (Li2O) from cellulose and Li metal and 3D fiber structure. The quantitative relationship between the capacity loss and physical properties of the separator was described successfully by optimizing a mathematical model. Cellulose played a unique role in the LiPS mass transfer process.
To summarize, the findings of this study demonstrated the feasibility of using BC separators as a suitable battery material for high energy density Li–S and other Li-metal batteries and validated the hypothesis on the advantageous features of cellulose-based separators for Li–S battery applications.
In the future, the insight gained in this study about advantageous BC separator features can provide a theoretical basis for designing functional BC separators for batteries.
References
Li, J., Li, Y., Li, Z., et al. (2022) Understanding the Advantageous Features of Bacterial Cellulose-Based Separator in Li–S Battery. Advanced Materials Interfaces. https://onlinelibrary.wiley.com/doi/10.1002/admi.202201730
Disclaimer: The views expressed here are those of the author expressed in their private capacity and do not necessarily represent the views of AZoM.com Limited T/A AZoNetwork the owner and operator of this website. This disclaimer forms part of the Terms and conditions of use of this website.