In a paper recently published in the journal Additive Manufacturing, researchers explored the polymer melt-extrusion-based 3D printing (ME3DP) process and the involved temperature reduction of freshly deposited thermoplastic polyurethane (TPU). They also considered the associated mechanical dependence over the development of the interface.
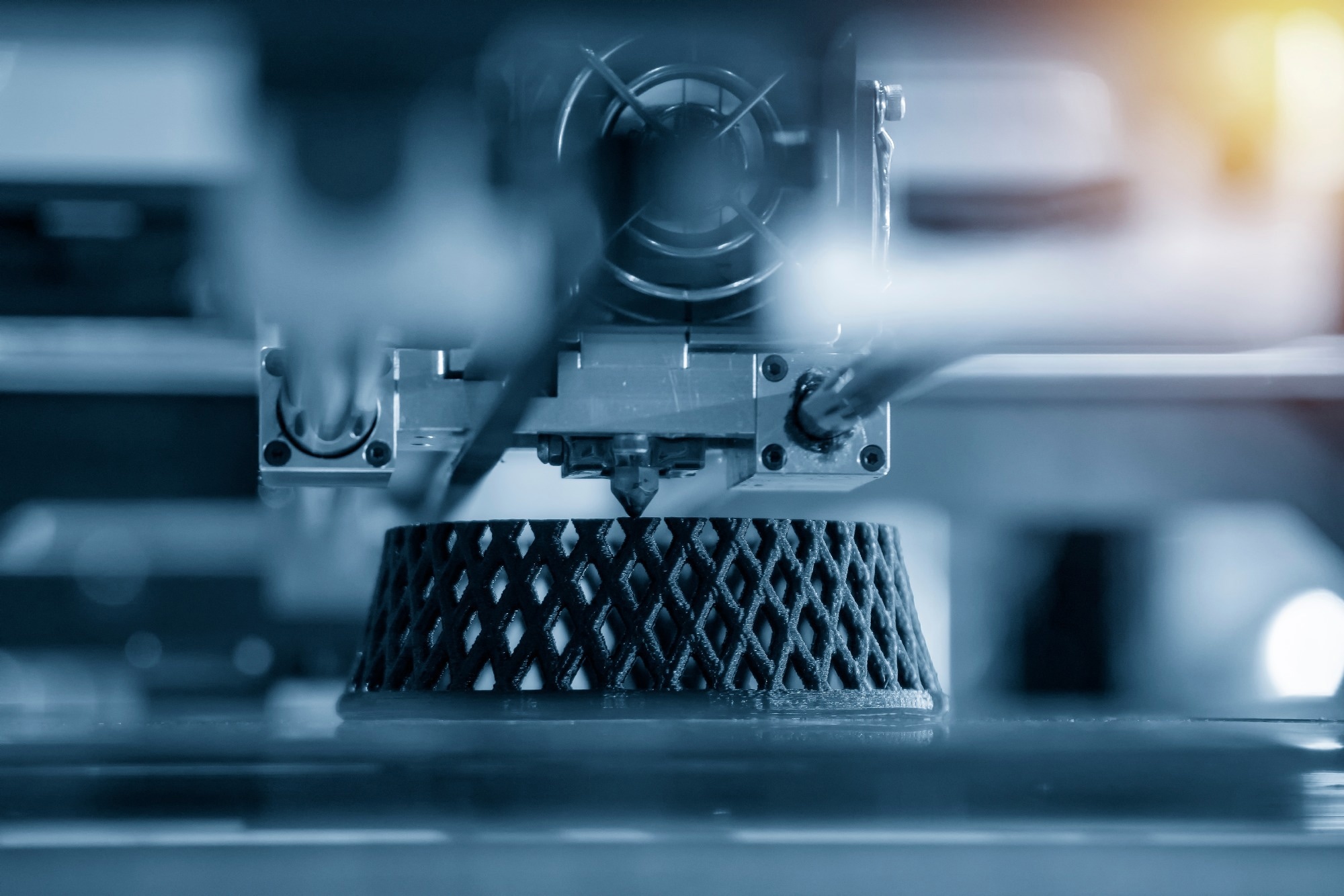
Study: An insight into the tensile anisotropy of 3D-printed thermoplastic polyurethane. Image Credit: Pixel B/Shutterstock
Background
Due to its simplicity of usage, low cost, and suitability for various polymers, ME3DP is a frequently employed material. Mechanical anisotropy is typically achieved because the rastering structure in 3D space is not uniform, and failure of such items is initially found in interfacial regions. Therefore, the overall mechanical performance observed for 3D-printed objects is mostly determined by the interfacial layers' bonding strength and porosity.
Additionally, the temperature observed for freshly deposited melt and the amount of time needed for reptation above the critical temperature (Tg) determine the degree of diffusion and entanglement of molecular chains throughout the bond layer. TPU and other amorphous elastomers typically have a Tg less than zero, which cannot be attained by only ambient cooling. Therefore, it is unclear at what temperature diffusion kinetics must end. The production of orthopedic devices, low-temperature isolators, shock absorbers, and other products can be potentially facilitated with 3D-printed TPU. However, thorough research is needed to understand the process-structure-property exhibited by 3D-printed TPU.
About the Study
In the present study, commercial TPU filaments, composed of polyester-group compounds, were produced with butane-1,4-diol and methylene diphenyl diisocyanate. The nozzle temperature was set to 245°C when the extruded molten strands were deposited. A self-edited G-code controlled the nozzle's trajectory. Then, the printed sheets were cut into tensile bars. A universal testing device was used to examine the tensile characteristics of the CM and 3D-printed samples. The mechanical strength noted for as-printed materials was assessed using a metric called the ultimate tensile strength (UTS).
Scanning electron microscopy (SEM) was used to analyze the printed specimen's cross-sectional morphology. The team examined the crystallization morphology of printed pieces under a polarized microscope. To record the changing transient temperature observed for the deposited melt, the Tools+ program was used. Differential scanning calorimetry was utilized to analyze the thermodynamic behavior of TPU. At room temperature, wide-angle X-ray diffraction (WAXD) confirmed the microstructure of printed samples.
Observations
An IR camera measured the initial melt temperature at 223°C around the nozzle exit. The simulated result was similar to the behavior of previously estimated temperature attenuation. In this procedure, the substrate layer was simultaneously heated up to almost 120°C depending on conductive heat transfer. At the same time, the temperature observed for the newly deposited melt fell rapidly due to radiative and convective heat transmission. Due to the moderated reduction rate of melt temperature, it could be predicted that the deposited melt line created by a large-diameter nozzle could prove beneficial to creating a much more developed interface layer. A numerical simulation of a multi-line accumulated structure revealed that the melt lines in contact with the newly deposited line showed the greatest healing. In contrast, the alternated lines showed less damage.
The sample produced at a higher bed temperature (Tb) of electric heating had a smooth surface. The sample maintained its intended shape after cooling and finishing the printing process. Up until the Tb reached 160°C, the findings demonstrated mechanical anisotropy. As Tb rose, the tensile strain at break across the transverse direction increased. However, the strain at break for longitudinal tensile testing remained steady. The interfaces created by a pair of melt lines that were not parallel to the direction of the load were primarily responsible for the observed tensile anisotropy.
The team noted that raising Tb significantly made it easier to lower the porosity of the printed samples. In contrast, higher Tb encouraged soft segment crystallization dynamics and produced many crystallites, resulting in a more striking phase separation. When adequate crystallization time was given, it was inferred that the considerable elevation in yield stress exhibited by the samples that were printed at Tb =100-140°C, comprising both transverse and longitudinal yield stress, should be due to this crystallization behavior. Therefore, the two main factors contributing to the improved tensile characteristics and tensile isotropy were the enhanced crystallization kinetics and the highly reduced porosity.
Conclusions
In conclusion, engineering applications can use the present technology to convert 3D-printed items into a one-step manufacturing process. According to the simulation results, the melt's heat only affected the layers immediately surrounding it, while it had little effect on the layers farther away. Tensile characteristics changed from anisotropy to isotropy when Tb rose from 25°C to 160°C.
The weak orientation degree associated with molecular chains on the deposited molten filament surface could be eliminated by raising Tb under a long residence time. Overall, this work offers a simple method to print high-strength parts while highlighting the mechanical anisotropy of printed TPU. According to the authors, a printer having ambient heat sources and a separate cooling system can be developed in the future. This will help to transcend the current limitations and flaws in ME3DP technology.
Source
Xiang Lin, et al., (2022). An insight into the tensile anisotropy of 3D-printed thermoplastic polyurethane. Additive Manufacturing. doi: https://doi.org/10.1016/j.addma.2022.103260
Disclaimer: The views expressed here are those of the author expressed in their private capacity and do not necessarily represent the views of AZoM.com Limited T/A AZoNetwork the owner and operator of this website. This disclaimer forms part of the Terms and conditions of use of this website.