Glass fiber-reinforced plastic (GFRP), renowned for its exceptional strength and durability as a composite material, finds extensive application across various industries, ranging from aircraft components to wind turbine blades. However, the inherent resilience that renders it suitable for diverse uses also poses challenges in its disposal. Consequently, the majority of GFRP waste is typically relegated to landfills upon reaching the end of its life.
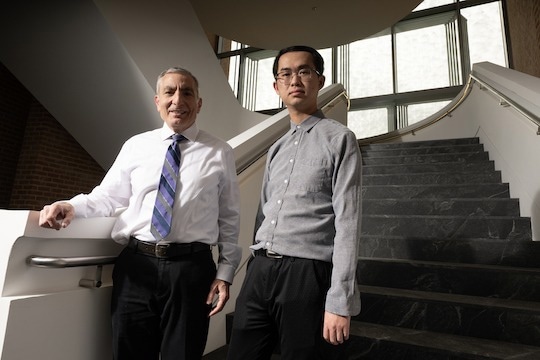
James Tour (left) and Yi Cheng. Image Credit: Jeff Fitlow/Rice University
A novel, energy-efficient upcycling technique has been created by Rice University researchers and partners to convert glass fiber-reinforced plastic (GFRP) into silicon carbide, which is extensively used in semiconductors, sandpaper, and other goods, according to a study published in Nature Sustainability.
GFRP is used to make very large things, and for the most part, we end up burying the wing structures of airplanes or windmill blades from a wind turbine whole in a landfill. Disposing of GFRP this way is just unsustainable. And until now there has been no good way to recycle it.
James Tour, T.T. and W.F. Chao Professor, Rice University
As regulatory agencies intensify their focus on improving recycling practices for end-of-life vehicles, there is a pressing demand for more effective methods to manage GFRP waste.
While attempts have been made to explore avenues such as incineration or solvolysis for GFRP disposal, Yi Cheng, a postdoctoral research associate and Rice Academy Junior Fellow associated with the Tour lab, underscores their inadequacy owing to resource-intensive requirements and environmental contamination concerns.
This material has plastic on the surface of glass fiber, and incinerating the plastic can generate a lot of toxic gases. Trying to dissolve GFRP is also problematic as it can generate a lot of acid or base waste from the solvents. We wanted to find a more environmentally friendly way to deal with this material.
Yi Cheng, Postdoctoral Research Associate, and Junior Fellow, Rice University
Through the use of flash Joule heating—a method that involves passing a current through a moderately resistant material to swiftly heat it to extremely high temperatures and change it into other substances—Tour’s lab has already made news for creating novel waste disposal and recycling applications.
Tour stated that he believed that this type of turbo-heating could convert GFRP into silicon carbide, which is commonly used in semiconductors and sandpaper, after learning about the problems associated with GFRP disposal from colleagues at the Defense Advanced Research Projects Agency.
Tour added, “We already knew that if we heat the mixture of metal chloride and carbon by flash Joule heating, we could get metal carbide ⎯ and in one demonstration, we made silicon carbide. So, we were able to leverage that work to come up with a process to transform GFRP into silicon carbide.”
This new process grinds up GFRP into a mixture of plastic and carbon and involves adding more carbon, when necessary, to make the mixture conductive. The researchers then apply high voltage to it using two electrodes, bringing its temperature up to 1,600-2,900 degrees Celsius (2,912-5,252 Fahrenheit).
“That high temperature facilitates the transformation of the plastic and carbon to silicon carbide. We can make two different kinds of silicon carbide, which can be used for different applications. In fact, one of these types of silicon carbide shows superior capacity and rate performance as battery anode material,” Tour stated.
While the first study was a proof-of-concept test on a bench size in the laboratory, Tour and colleagues are already collaborating with other companies to scale up the technique for wider use. Upcycling GFRP is more cost-effective and ecologically beneficial than incineration or solvolysis, with running costs below $0.05 per kilogram.
According to Tour, scaling out this novel flash upcycling technique effectively will require good engineering and patience. He expressed his excitement that his group was able to create a viable method for turning GFRP waste into silicon carbide treasure.
Tour further stated, “This GFRP is a waste product which usually ends up in a landfill, and now you can turn it into a usable product that can help humankind. This is exactly the kind of approach we need to support a circular economy. We need to find ways to take waste products from a wide variety of different applications and turn them into new products.”
The US Army Corps of Engineers (W912HZ-21-20050), Rice University, and the Air Force Office of Scientific Research (FA9550-22-1-0526) provided funding for the study.
Journal Reference:
Cheng, Y., et. al. (2024) Flash upcycling of waste glass fibre-reinforced plastics to silicon carbide. Nature Sustainability. doi:10.1038/s41893-024-01287-w.