A recent article published in Scientific Reports explored the impact of atomic layer deposition (ALD) of Al2O3 on LiNi0.8Mn0.1Co0.1O2 (NMC811) cathodes for Li-ion batteries. The coated electrode’s long-term cycling stability, storage stability, rate capability, and charger transfer kinetics were compared to bare electrodes.
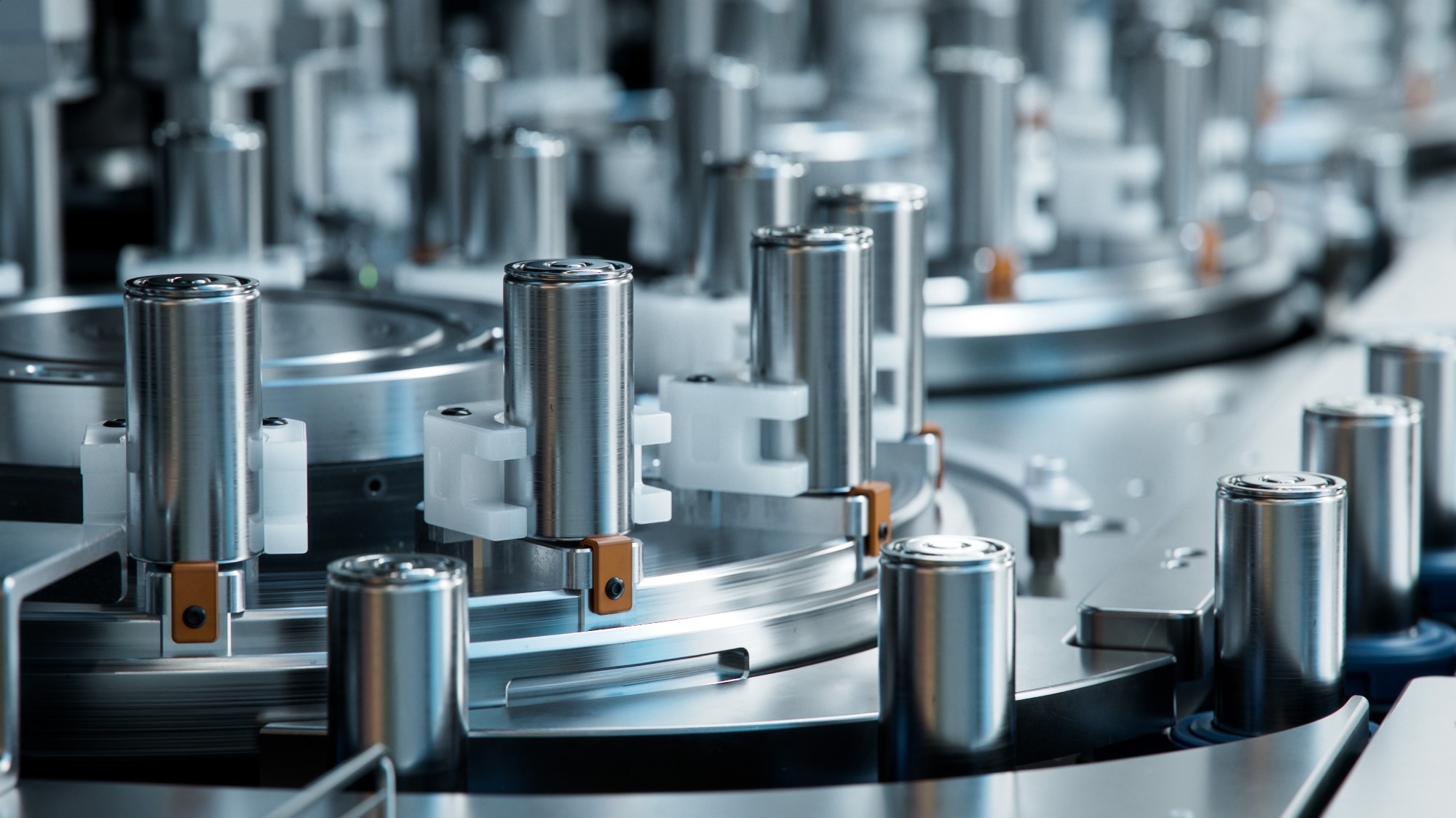
Image Credit: IM Imagery/Shutterstock.com
Background
Layered lithium transition metal oxides with a general formula of LiNixMnyCo1−x−yO2 (NMC) are important cathode materials for Li-ion batteries due to their high theoretical capacity, energy density, and tunable chemical composition. Specifically, Ni-rich NMC811 is widely adopted in commercial Li-ion battery cells.
However, the reversible capacity of Ni-rich NMC cathodes is only about 80 % of their theoretical capacity, as significant degradations occur at a higher capacity utilization. Surface coatings are, therefore, employed to tailor the chemical and physical properties of the electrode surface and enhance its stability against the electrolyte.
Among various coating methods, ALD stands out for its ability to provide controlled and conformal coatings with diverse chemistries at moderate temperatures. Additionally, ALD directly coats composite electrode films, protecting all exposed surfaces from direct contact with the electrolyte and improving electrochemical performance.
This study investigated the effect of Al2O3 coatings applied via ALD on commercial-grade NMC811 electrodes.
Methods
The active cathode material was commercially sourced polycrystalline NMC811 powder. It was mixed with acetylene black (5 wt.%) and polyvinylidene fluoride (PVDF, 5 wt.%) in N-methyl-2-pyrrolidone to form a homogeneous slurry. This slurry was then cast into a thin film electrode with an aerial loading of 5.6 mg/cm2.
The Al2O3 coating was deposited on the NMC811 electrode films at 80 °C using an ALD system. After initial trials at 80 °C, 100 °C, 120 °C, and 140 °C, the coating was applied using trimethylaluminum (TMA) and water vapor as precursors, carried by high-purity N2 gas into the chamber.
The thickness of the Al2O3 coating was controlled by varying the ALD cycles (2, 5, 10, and 20 cycles). Subsequently, coin cells were assembled with an NMC811 electrode disc as the cathode, a lithium chip as the anode, a glass fiber disc as the separator, and a 1 M LiPF6 electrolyte.
The NMC811 particles and electrodes were characterized using X-ray photoelectron spectroscopy, scanning electron microscopy, energy-dispersive X-ray spectroscopy, and X-ray powder diffraction. In addition, transmission electron microscopy was performed on the coated electrodes.
Electrochemical cycling measurements were performed using a battery testing system using the constant current constant voltage (CCCV) charging method for long-term cycling and galvanostatic discharge. In addition, the potentiostatic intermittent titration technique (PITT) was employed on the second cycle during charge and discharge, and electrochemical impedance spectroscopy measurements were recorded during the discharging of the second cycle.
Results and Discussion
The study revealed that Al2O3 coating provided only limited benefits to the NMC811 electrodes, offering slight improvements in stability against one-day ambient exposure. These results contrast with previous reports that indicated significant improvements in the electrochemical performance of coated electrodes; however, those studies used homemade electrode material rather than commercial-grade NMC811.
The capacity retention of the base electrode (160 mAh/g at 100 cycles) outperformed the Al2O3-coated homemade NMC811 electrodes (160 mAh/g at 40 cycles). This was attributed to the superior quality of the commercial NMC811, leaving less scope for enhancement in the electrochemical performance by surface coating.
The ALD process successfully coated all exposed surfaces of the electrode films with Al2O3, including the carbon additives and PVDF binder. However, homogeneous deposition across the porous electrode could not be ensured. Elemental mapping of the electrode’s cross-section revealed a higher concentration of Al near the surface compared to the interior.
The study suggested that ALD could effectively coat all NMC811 particles if the electrode was sufficiently thin, as indicated by the homogeneous spatial distribution of Al and the increased surface resistance of the coated electrodes.
Elemental mapping also revealed a spatial overlap between F-containing species (from PVDF) and NMC particles, indicating at least partial surface coverage of the electrode particles with the PVDF binder. This suggests that secondary species on the surface of NMC particles prevented a direct reaction and bonding between the ALD precursors and the electrode’s oxide surface.
Conclusion
The study investigated the impact of Al2O3 coated on the electrochemical performance of NMC811 electrode films using ALD. The electrochemical measurements showed no significant differences in capacity retention at different cut-off voltages or in the rate capability of the coated versus bare electrodes.
While the coated electrodes demonstrated better stability against short-term air exposure, this enhanced stability did not depend on the coating thickness and was not evident in long-term air exposure.
The researchers speculated that pre-existing secondary species on the electrode particle surface created an interlayer between the electrode’s oxide surface and the Al2O3 coating, undermining the coating’s effectiveness.
Journal Reference
Huang, H., et al. (2024). Efficacy of atomic layer deposition of Al2O3 on composite LiNi0.8Mn0.1Co0.1O2 electrode for Li-ion batteries. Scientific Reports. DOI: 10.1038/s41598-024-69330-6, https://www.nature.com/articles/s41598-024-69330-6
Disclaimer: The views expressed here are those of the author expressed in their private capacity and do not necessarily represent the views of AZoM.com Limited T/A AZoNetwork the owner and operator of this website. This disclaimer forms part of the Terms and conditions of use of this website.