A recent article published in Nature Communications reports the three-dimensional (3D) printing of plain carbon steels with tensile and impact properties comparable to, or exceeding, those of ultra-high-strength alloy steels such as Maraging steels.
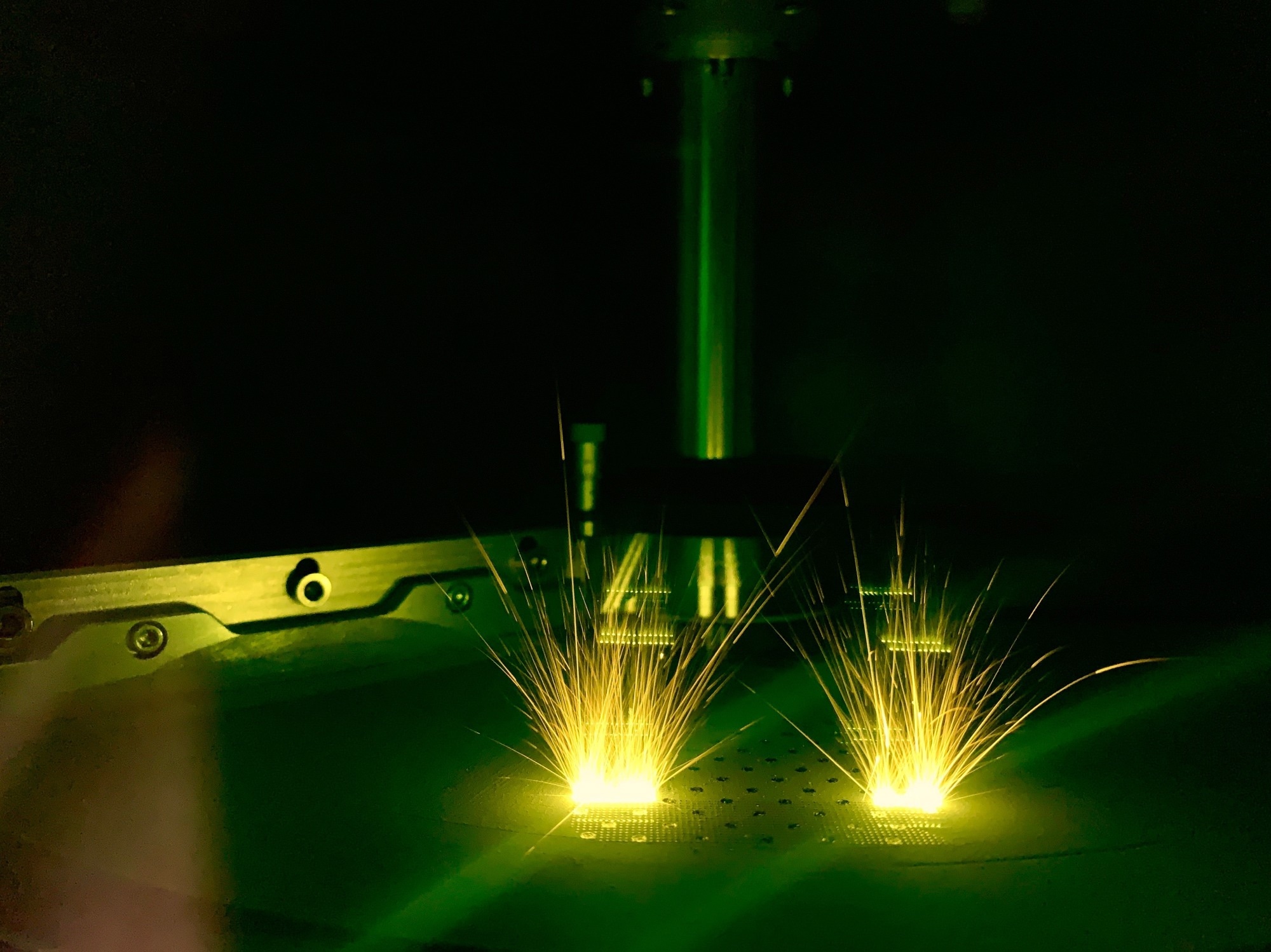
Image Credit: dr_christian_bay/Shutterstock.com
Background
Engineering alloys, such as aluminum and steel, are commonly used structural materials due to their high strength and damage tolerance. Over time, these alloys have evolved into compositionally complex variants with specialized properties.
The demand for improved mechanical performance, including ultra-high strength and wear resistance, has highlighted the need for precise control of microstructure formation. Metal 3D printing, particularly powder bed fusion (PBF), offers opportunities to simplify alloy compositions while achieving the desired performance. However, most 3D-printed components are fabricated using existing complex alloys rather than developing simplified compositions tailored for 3D printing.
PBF is a widely used metal 3D-printing method that employs a high-energy laser or electron beam to selectively melt thin layers of metal powder. This process constructs complex geometries layer by layer. This study utilized the characteristics of PBF to produce high-performance carbon steels.
Methods
Gas-atomized pure iron and steel powders were used as raw materials for the 3D-printing processes. Plain carbon steels with carbon contents of 0.4 wt.% (AISI 1040) and 0.8 wt.% (AISI 1080) were selected for the alloy compositions.
Steel samples (10×10×10 mm3) were produced using a laser PBF 3D-printing system under an inert and high-purity (≥99.99%) argon atmosphere. Optimized printing parameters were then applied to fabricate larger samples for tensile testing, Charpy impact toughness evaluation, and hardness distribution analysis.
The 3D printability of plain carbon steels was assessed through sample densification using image analysis software (ImageJ). Rockwell hardness measurements were conducted on cubic samples at varying processing parameters, and the Jominy end quench test was performed to evaluate the low hardenability of plain carbon steels.
The potential of 3D printing to produce plain carbon steel parts with consistent microstructural and property homogeneity was demonstrated through the fabrication of a bevel gear (40 mm height, 80 mm diameter) using 1080 steel powder and optimized parameters.
To further compare processes, two L-shaped parts were prepared: one machined from commercial 1080 wrought steel and subjected to austenitization and quenching, and the other directly 3D-printed using 1080 steel powder. The 3D-printed part avoided issues such as quenching-related cracking and distortion, highlighting the advantages of the 3D-printing approach.
Results and Discussion
The uniform hardness distribution and precise geometric accuracy of the 3D-printed gear highlighted the ability of 3D printing to address issues associated with conventional water quenching, such as distortions and non-uniform hardness in alloys.
The L-shaped demonstration part machined from commercial 1080 steel exhibited cracking and distortion at the corner due to water quenching. In contrast, the 3D-printed part showed no cracks or distortion. This was attributed to the micro-melting process during printing, which compartmentalized thermal stress and provided an in-situ tempering effect through the melting of successive layers, reducing residual thermal stress.
X-ray diffraction analysis of the 3D-printed 1080 steel revealed a single ferritic phase (α') with no detectable austenite or carbides. Field emission scanning electron microscopy showed fine, plate-like ferrite structures uniformly distributed without preferential orientations.
An approximate Greninger-Troiano relation was observed between the orientation of the α’-blocks and prior γ grains, indicating martensitic and bainitic transformations during 3D printing and the suppression of pearlite transformation at the applied energy inputs.
In 1080 steel, low laser energy input produced high-carbon martensite, resulting in a yield strength (YS) of 1773 MPa and an ultimate tensile strength (UTS) of nearly 2000 MPa. Higher energy input shifted the microstructure from martensitic to bainitic, reducing the YS and UTS to 1100 MPa and 1327 MPa, respectively.
3D-printed 1040 steel also demonstrated strong mechanical properties. Low laser energy input produced a YS of 1340 MPa and UTS of 1430 MPa, while higher energy input reduced these values to 1000 MPa and 1100 MPa. These properties were achieved directly after printing, with subsequent tempering treatments having minimal effect on mechanical performance.
Conclusion
The study demonstrated that 3D-printed plain carbon steels can achieve high mechanical performance without significant alloying additions. The proposed approach offers advantages in cost, recyclability, and raw material availability.
The researchers recommend further investigation into the fatigue resistance, fracture toughness, and stress corrosion cracking of 3D-printed plain carbon steels for practical applications. Enhancing properties such as corrosion resistance may require the addition of elements like chromium, while other alloying elements could be considered for specific requirements, such as improving oxidation resistance.
More from AZoM: What is Material Fatigue?
Journal Reference
Tan, Q. et al. (2024). High performance plain carbon steels obtained through 3D-printing. Nature Communications. DOI: 10.1038/s41467-024-54507-4, https://www.nature.com/articles/s41467-024-54507-4
Disclaimer: The views expressed here are those of the author expressed in their private capacity and do not necessarily represent the views of AZoM.com Limited T/A AZoNetwork the owner and operator of this website. This disclaimer forms part of the Terms and conditions of use of this website.