Since commercialized in the 1960s, aromatic polyimides have remained in widespread use due to their excellent performance in a range of demanding applications. These polyimides are well-known for excellent thermal stability, chemical resistance and mechanical properties.
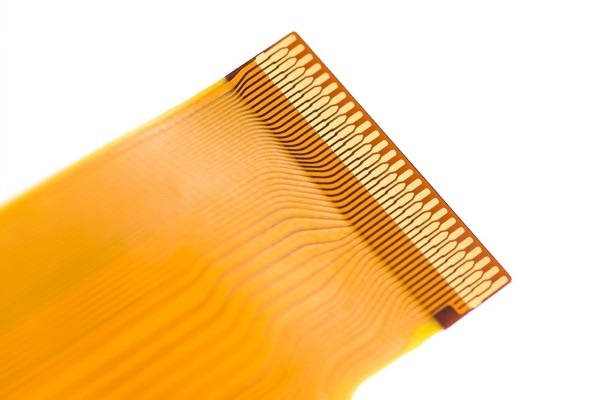
Image Credit: Jayhawk Fine Chemicals Corporation
However, processing of aromatic polyimides has always been a challenge. The task is to maintain a good balance between processability and properties. Presented here is a particular strategy to address this challenge: the use of reactive functional end cappers.
Basic concepts
The primary route of most polyimide synthesis is via a condensation reaction of a diamine with a dianhydride e.g. 1,4-diaminobenzene (PPD) and 3,3',4,4'-Benzophenone tetracarboxylic dianhydride (BTDA®) typically in a polar aprotic solvent. This leads to the formation of a polyamic acid (PPA) intermediate that can be further dehydrated to produce the final polymer.
This technique of solution processing via PAA enables polyimides to be used in the production of films, coatings or fibers. However, in the absence of a solvent the imidization reaction results in an intractable material that is difficult to process due to molecular weight increase and crosslinking.
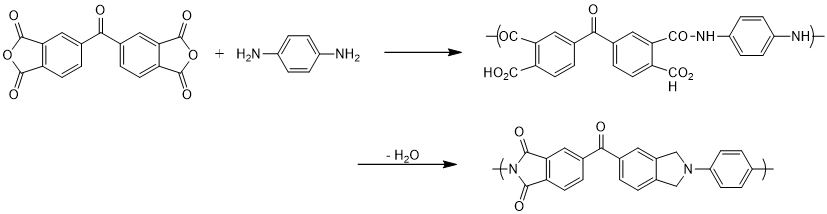
Figure 1. Polyimide synthesis using BTDA and PPD as building blocks. Image Credit: Jayhawk Fine Chemicals Corporation
The properties of polyimides rely on a large number of factors such as solvent, reaction conditions, stoichiometry, and critically, the selection of monomer building blocks. The electronic properties of these building blocks will strongly influence the properties of the final material.
The superior mechanical properties of polyimides arise from the strong intermolecular forces occurring between polymer chains and geometrical factors allowing a close-packed structure. The intermolecular forces include polar interactions between carbonyl groups, the interaction between aromatic rings and charge transfer complexation.
High intermolecular forces contribute to thermomechanical properties but are also ultimately responsible for poor processability. Aromatic polyimides can be classified into two broad categories in terms of chemistry.
There are condensation polyimides, where condensation reactions lead to thermoplastic polymers; and addition curable polyimides, where additional reactions lead to thermosetting materials.
End Cappers
There is an alternative approach to polyimide synthesis that produces an imidized intermediate of lower molecular weight and viscosity that can be manipulated without the need for a solvent, which expands the potential applications available beyond those noted above for solvent based systems.
The molecular weight of the intermediate is controlled by the use of functional end cappers, which are groups that contain a thermally reactive functionality. The oligomers are crosslinked, via thermal addition polymerization of acetylinic groups in the end-cappers, building the molecular weight of the polymer.
The curing temperature for these cross linkers can be selected to fit virtually any processing requirement. Activation temperatures range from 190 - 240 °C to 380 - 440 °C.
Processing rules
There are a few properties to keep in mind when selecting a suitable reactive functional end capper for addition curable polyimides:
- In general, the lower the molecular weight of the end capper, the higher the cross-link density of the polyimide after curing.
- They should have a broad processing window. Remember that thermal activation will occur after polymer processing.
- The curing temperature for reactive nitrogen groups should be above the processing temperature. This difference in temperature defines the processing window.
- They should also cure without the evolution of volatile organic compounds, as these could affect polymer mechanical strength.
Final words
The correct combination of diamine, dianhydride and reactive functional end capper can provide processability that is comparable or superior to that of a more thermoplastic polyimide but with improved mechanical, chemical and thermal properties.
The growing accessibility of building blocks with optimized properties is helping to spread this approach and provide new polymers for new applications.
BTDA is a registered trademark of Jayhawk Fine Chemicals Corporation.

This information has been sourced, reviewed and adapted from materials provided by Jayhawk Fine Chemicals Corporation.
For more information on this source, please visit Jayhawk Fine Chemicals Corporation.