.jpg)
Induction hardening provides excellent hardness distribution with minimal deformations, and also offers significant benefits over conventional techniques. However, induction hardening also places high demands on the generators and the inductor used. Achieving ideal hardening results can only be achieved by perfectly matching a precisely controlled energy source with an optimum inductor design.
Heating Directly in the Workpiece with Induction Hardening
Induction hardening is a heating technique where the heat is produced directly in the workpiece. The principal benefit is that the heat is not applied to the part indirectly by heating its surface. In conventional heating techniques, such as with an oven or a flame or by convection, heat is applied to the part by heating up its surface.
These techniques take significantly longer and require considerably more energy to turn out the desired hardening result. Conversely, induction hardening offers very short heating times, making it a very appealing technique - especially in the industrial sector.
Additionally, induction heating can be controlled very precisely via the frequency, power, and the inductor geometry. This reduces deformations in the workpiece and makes the process very efficient.
How Induction Hardening Works
A coil is used to produce an alternating electromagnetic field that induces alternating currents in the workpiece. The electrical resistance in the workpiece causes it to heat up, which results in the heat being generated in exactly the desired location.
The induction heating technique is used primarily for surface hardening. The workpiece’s hardening depth is controlled precisely via the electrical power output and frequency of the inductor/coil current in order to achieve an optimum hardening result. The generator is an especially vital part in this process. The energy source must be tailored to the needs of each application so that the frequency is perfectly matched to the hardness distribution required.
Different Frequency Ranges for Induction Hardening
- Low frequency: 1 - 7 kHz
- Medium frequency: 8 - 40 kHz
- High frequency: 60 - 500 kHz
eldec provides energy sources with the newest converter technology for all three frequency ranges.
Induction Hardening with Simultaneous Dual Frequency
With Simultaneous Dual Frequency (SDF), eldec offers an additional technique that used specifically for workpieces with complex shapes. A medium frequency is overlaid with a high frequency so that both act upon the workpiece at the same time.
What are the Advantages of Induction Hardening?
- High process stability
- Excellent control of the hardening process
- Highly versatile in application
- Minimal heating times
- Minimal space requirements
- Minimized deformation of the workpieces
- Accurate hardening results on contours
- Excellent energy efficiency
- Ideal integration into manufacturing systems
- Safe heating technique
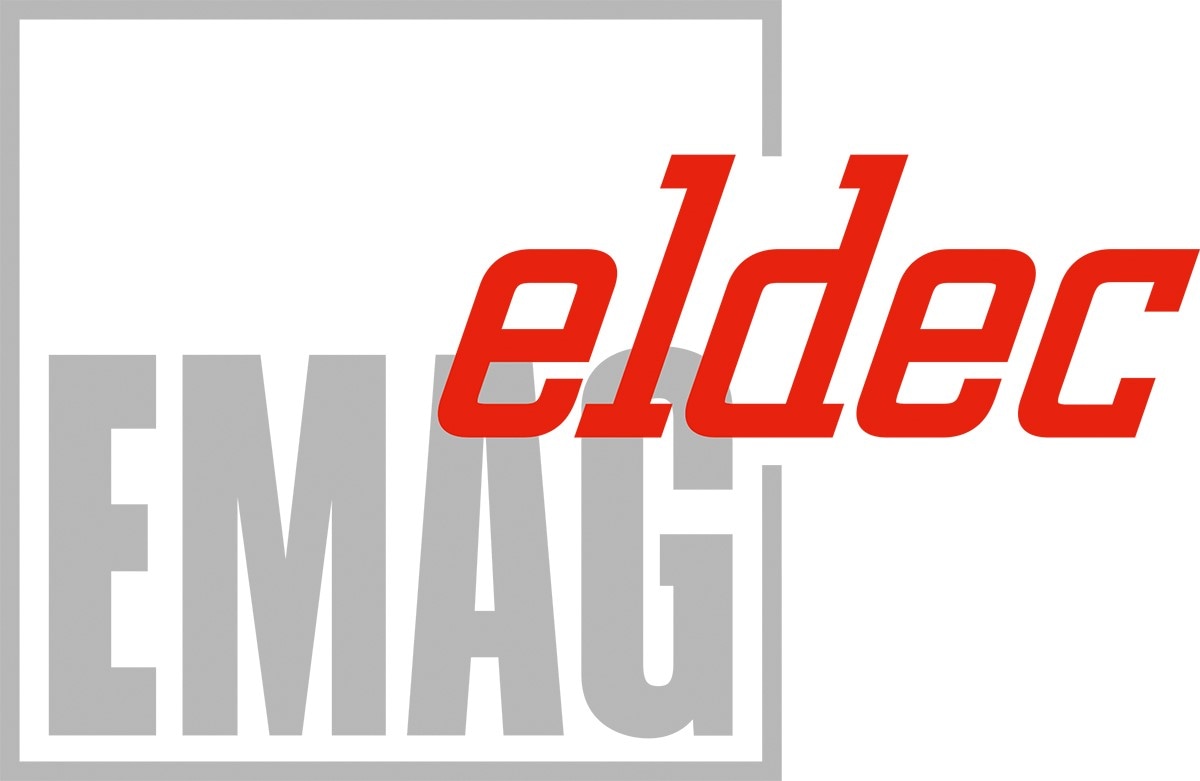
This information has been sourced, reviewed and adapted from materials provided by Eldec Induction USA, Inc.
For more information on this source, please visit Eldec Induction USA, Inc.