Producing parts at the lowest possible cost is the goal of every waterjet shop. In order to realize this goal, a correctly sized waterjet pump is very important.
However, many choices and considerations have to be made when it comes to choosing the right pump to charge a waterjet system. There are endless specifications like how much pressure is needed? Is a low-cost direct drive pump better than a hydraulic intensifier pump? How much horsepower is needed? The list goes on.
.jpg)
To help users make an informed purchasing decision, waterjet industry legends Jeff Schibley and Bradley Schwartz of Jet Edge were asked to share a few tips on how to select the right pump for a system. Schibley and Schwartz have more than 50 years of experience in the waterjet field. Jet Edge, based in Minnesota, has been manufacturing waterjet systems from 1984 and provides the broadest range of waterjet pumps available in the industry.
What’s Your Application?
According to Schibley, choosing the perfect pump begins by identifying the specific application. This will help the user’s waterjet pump manufacturer to find out the flow rate, horsepower, pressure, and other specifications.
We’ll ask you several questions. What are you cutting? How fast do we need to cut the product? Can we make the customer’s throughput requirements with a single nozzle? Does the application require multiple nozzles? Can the cutting application be performed with straight water? Does the application require the addition of abrasive?
Jeff Schibley, Jet Edge
Schwartz believes that a good manufacturer generally helps its customer to determine the most efficient and cost effective pump.
“If I’m cutting nothing but very soft tile that cuts fine at 36,000 psi, I might as well put in a 36,000 psi pump and cut with six heads,” he added. “But if I’m cutting 3” to 6” steel all day long, I’ll need a 60,000 psi pump. If I want to use 50hp per head and I want to use two heads, that pump will need to be 100hp.”
The All Important Test Cut
To help their customers, most waterjet manufacturers provide free test cuts to determine the most suitable motor pump and motion set up for their application.
In the test cut, the manufacturer performs a series of tests to discover the most efficient speed, horsepower, and cutting pressure to finalize the customer’s throughput requirements.
.jpg)
“During the test, we determine if we can process the customer’s material with straight water or if we need to add abrasive,” Schibley explained. “We also determine how much pressure and what orifice size and how many cutting heads are required to make their throughput requirements. If the application requires abrasive, we will determine how much abrasive is required and the most efficient orifice/nozzle combination. Once we have determined these factors, we can size the pump and flow rate.”
Schwartz added that the test cut will help customers choose the most cost-effective pump for their specific applications. It will also provide them with the required cutting data to keep their operating costs to a minimum by operating their system at the most cost-efficient pressure, using the least amount of abrasive and running the appropriate number of cutting heads to realize their required throughput.
“As an example, when I’m cutting upwards of a ¼” material, I would use two heads and I would use 25hp per head to cut it because I’m not going to be cutting that much slower than I would at 50hp, but I will use half the abrasive and I am using two heads so I will double my production. When I go up to 2” thick material, I will go to 50hp per head. It only takes me a minute to change the orifice and nozzle to bring my horsepower up and down. That is how you change the horsepower, with different orifice sizes. At 60,000 psi, 25hp uses a 0.010” orifice. When you go to 50hp, you use a 0.015” orifice.
Bradley Schwartz, Jet Edge
The pump must be within a customers budget, even if that means scaling back a bit on horsepower or pressure and accepting a higher cost per part.
“We have to take into consideration the customer’s financial considerations,” he said. “Just because a 60,000 psi 200hp pump operating four 0.015”/0.045” orifice/nozzle combinations makes the lowest cost cut, doesn’t mean it is the best pump for the customer if it doesn’t meet his financial requirements.”
Intensifier vs. Direct Drive
Two basic waterjet pumps are available - hydraulic intensifier pumps and direct drive pumps (also called crank or positive displacement pumps). A crank is used by the direct drive pump to drive the pump’s plunger, while a hydraulic cylinder is used by an intensifier to drive the plunger.
While the upfront costs of direct drive pumps are less than hydraulic pumps, they require more maintenance. Direct drive pumps provide a good economical option for shops that only need an entry level system for low-volume cutting. On the other hand, intensifier pumps can be used by shops that process higher volumes of material and thicker materials.
.jpg)
Hydraulic Intensifier Pump
.jpg)
Direct Drive Pump
“Jet Edge has always been a proponent of intensifier pumps because they are easier to maintain and have lower maintenance costs and less downtime,” Schwartz noted. “We do offer direct drive pumps, however, because sometimes that is all a shop has budget for and it may be all they need.”
Extreme Cutting Pressures
Over the last few years, manufacturers have been providing waterjet pumps with operating pressures surpassing 90,000 psi. While the upfront costs of these extreme pressures pumps are more than 60,000 psi pumps, they can significantly improve productivity and reduce operating costs by as much as 40% by cutting faster and using less water, garnet, and electricity.
.jpg)
Where extreme pressure pumps really come in handy is when you have a single cutting head and you want to double production. Very easily I can do that with 90,000 psi pump as compared with 60,000 psi. It also has the advantage of using less abrasive, and abrasive is your main cost per hour at up to 40 cents a pound. A typical abrasive waterjet system uses a half pound to a pound and a half per head a minute so you can see how the savings can add up quickly if you’re using 40% less abrasive at 90,000 psi.
Bradley Schwartz, Jet Edge
In applications where three to four cutting heads are required, Schwartz suggests sticking with a 150 hp to 200 hp 60,000 psi pump for its higher flow rate.
“A 150hp or 200hp 60,000 psi pump has a higher flow rate than a 100hp 90,000psi pump, and it is easier to divide that up to four heads,” he explained. To determine whether extreme pressure cutting is right for a specific application, users can ask their waterjet manufacturer for a test cut.
Where to go for More Information
As with any capital purchase, users should equip themselves with as much information as they can before purchasing a waterjet pump or system. Manufacturer and trade industry websites contain excellent educational information.
Users can sit in on manufacturers’ webinars, check out their machines at industry trade shows, and visit their manufacturing facilities. They can ask for referrals and references and see whether their manufacturer can arrange a tour at one of their current customer’s shops.
Whatever users do, they should never skip the test cut because this test not only helps them choose the most appropriate pump for their system, but also helps them to determine the most productive and cost-effective set up for their application. Instead of figuring it out on their own, users should use an experienced waterjet manufacturer to deal with all these procedures, and thus save both time and money in the process.
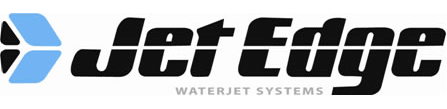
This information has been sourced, reviewed and adapted from materials provided by Jet Edge, Inc.
For more information on this source, please visit Jet Edge, Inc.