Sep 13 2002
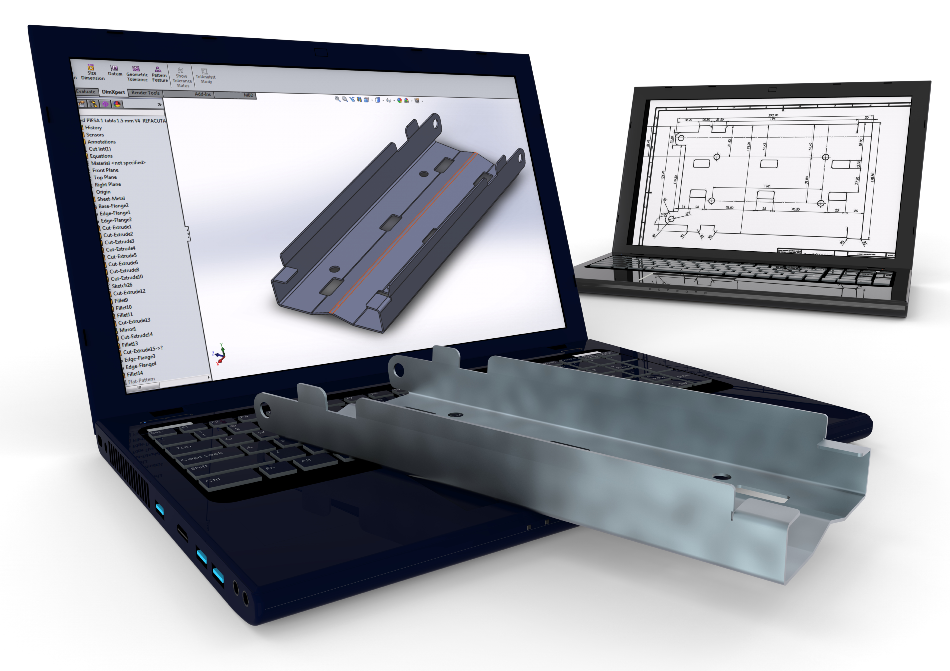
Solcan Design / Shutterstock
Besides cost and quality, time to market has become an increasingly significant factor in the success of a product. An important contributor to product development cycles is the time required to make prototypes.
In markets where customers are seeking individually customized components, significant time and cost may be involved in the production of molds or tools.
Rapid Prototyping (RP), also called Solid Freeform Fabrication (SFF) processes, helps to resolve these issues. Normally, additive processes are used to build intricate shapes, creating components without using any tools.
Lamination Modeling
Laminated Object Manufacture (LOM)
The Laminated Object Manufacture (LOM) process involves using a CO2 laser fitted on a 2D plotter to cut the components from thin layers of material. Generally, the system uses sheets of paper that are automatically placed on top of one another and adhered together using an adhesive.
The parts of the sheet on the outer side of the model offer support. These undesirable areas are labeled with intersecting lines, which form cubes that can be removed from the model once it is completed.
Advantages of LOM
The main advantages of LOM are given below:
- LOM has the potential for high manufacturing speeds
- Components do not require support structures
Only the circumference of the part is processed, whereas, in a majority of the RP techniques, the entire part has to be processed<th2>Disadvantages of LOM
The main drawbacks of LOM are given below:
- Surface finish is poor
- Does not produce good bonds between layers
- Difficulty in creating hollow parts
Manufacture of Ceramic Components using LOM
The LOM method has been used to make modern ceramic structural components. Sheets with a thickness of 0.015 to 0.12 mm made by tape casting have yielded ceramic parts with homogeneous as well as multi-layered composite microstructures. Excellent outcomes have been reported with Ce-ZrO2 and Ce-ZrO2/Al2O3 parts, which resulted in a microstructure and provided high strength after sintering.
The LOM process has been used to make silicon nitride, alumina, Yttria- and ceria-stabilized zirconium, and Ce-ZrO2/Al2O3 components with standard densities of 96%. Equipment suppliers demonstrate applications like alumina biomedical filters and silicon nitride turbine blades, indicating that the process is ideal for applications where small order sizes or prototypes make tooling costs prohibitive.
The method is currently used for making mimetic bone bio-structures for study purposes. These structures are made from zirconium, alumina, and phosphate-based bio-ceramics. By using Computer Tomography (CT) scanning, facial bones, wrist, and inner ear are measured in patients. The data is processed to make geometric models that can be sent to the LOM machine, where the components are finally created. Eventually, custom bio-ceramic implants may also be produced directly from the patient-specific data.
Computer-Aided Manufacturing of Laminated Engineering Materials (CAM-LEM)
Unlike the LOM method, Computer-Aided Manufacturing of Laminated Engineering Materials (CAM-LEM) uses a “cut then stack” method instead of “stack then cut.”
Advantages of CAM-LEM
Advantages of CAM-LEM over LOM are given below:
- Hollow parts can be produced
- The laser beam can be handled effortlessly and provides greater precision and smoother surfaces