This article describes the testing results following routine performance assessment of an electrical motor both in its original state and after rebuilding it using products made by Zeus, such as the crystalline magnet wire coated with PEEK, an insulating material composed of tubing made of PEEK Lay-Flat® material.
In comparison the original motor contained standard magnet wire, and insulation materials made of Nomex®, Nomex® laminate, and Dacron®-Mylar®-Dacron® (DMD). The chief tests were Electrical Signature Analysis (ESA) and Motor Circuit Analysis (MCA). In addition, testing was carried out at high voltage to enable testing at high potential, surge comparison and surge partial discharge as per the guidelines in IEEE Std 1415-2006.
The results showed that Zeus products had a better insulating effect, which caused a better performance in terms of Q factor, capacitance and partial discharge. These in turn improved motor efficiency, reducing leakage and enabling faster absorption.
Thus the primary advantages of using Zeus PEEK insulation products are better efficiency, lower energy consumption and costs, and more reliable performance.
Introduction
The motor used for the current testing was a 0.75 HP motor with a four-pole AC induction motor operating at 460 volts. The motor was originally built with insulation material from Class 155C (Class F) coated with light varnish and Class F lead wire was used. Standard magnet wire (MW) 35 was used (24 AWG) as seen in Figure 1 on the left. After the first round of testing, the motor’s wire and insulation were substituted with Zeus products, namely PEEK magnet wire, PEEK lead wire and PEEK Lay Flat® tubing.
The latter was used both to line the slots and for phase insulation. The insulation was rebuilt with Class 180C (Class H) material impregnated by polyester resin trickle varnish as seen in Figure 1 on the right. Tests were completed both before and after the substitutions and additionally, both before and after the trickle varnish was used to impregnate the Zeus insulation system.
The tests were done using an ALL-TEST PRO 5™, an ALL-TEST PRO OL™, an Amprobe® AMB55 tester for high voltage resistance of insulation, and an Electrom iTIG 12D. The results showed that the insulation resistance curve and the capacitance of the motor were significantly different when performed before and after trickle varnish was added to the rebuilt motor.
Other test results fell within the limits expected. Simultaneously, severe imbalance and wrong alignment were observed with respect to the motor, and the rotor was aligned eccentrically in the air gap separating the rotor and the stator, but these factors were not relevant to insulation system testing.
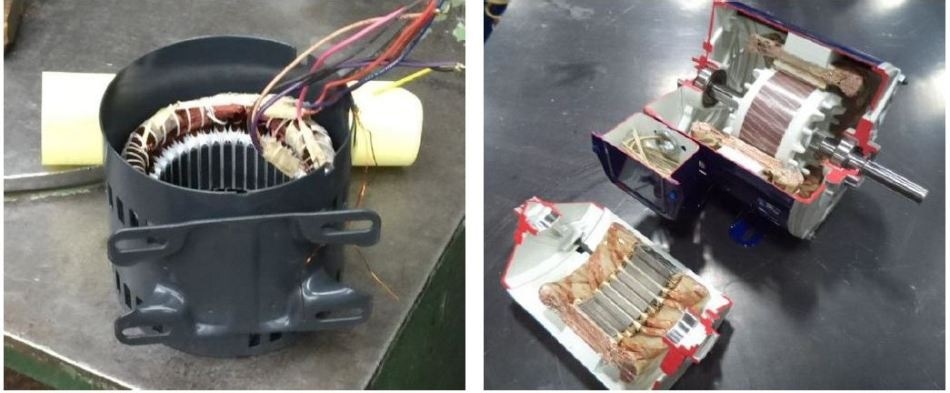
Figure 1. Test motor used for evaluation of Zeus PEEK insulation products: Left: Original stator prior to head removal and stripping. Right: New insulation system cut-away.
Testing with the All-Test Pro 5
The All-Test Pro 5 is a motor circuit analyzer instrument meant for low voltages, to assess the capacitance in the circuit and the insulation-to-ground loop. Thus it picks up any insulation defects that occur before the motor fails. The tests carried out on the original motor and the new model following the rebuild included low ohm resistance, inductance and impedance, the capacitive phase angle, the current-frequency response (I/F), the insulation to ground and the capacitance to ground, as shown in Table 1.
Table 1. Test results for low ohm resistance, inductance, impedance, capacitive phase angle, current/frequency (I/F) response, insulation to ground, and capacitance to ground for original motor and motor rebuilt with Zeus-manufactured products.
Test |
Original Motor |
Zeus Materials |
Resistance |
37.7 Ohms |
38.0 Ohms |
Inductance |
159 mH |
159 mH |
Impedance |
106 Ohms |
107 Ohms |
Phase Angle |
68.8 degrees |
68.6 degrees |
I/F |
-47% |
-46.9% |
Insulation Resistance |
>1 GigOhm |
>1 GigOhm |
Capacitance |
<2 µF |
<2 µF |
The results were almost the same in both cases. The small differences are usual when conducting comparisons between motors of the same build. Care was taken to balance each phase in both stages of testing to ensure that the motor would work as planned after its rebuild using Zeus products.
Testing with the AMPROBE® AMB55
The AMB55 is an industrial insulation tester designed for high voltages and can produce insulation curves that pick up on any variations in the motor before and after rebuild. These resistance curves are assessed in conformity to the insulation resistance profile (IRP) testing or the IEEE Std 43-2013 Annex D. During the ten-minute test the original motor polarization index curve was as expected - the absorption current within the insulation system went down to zero, as shown in Figure 2A.
IRP testing on the rebuilt motor was then carried out prior to and following trickle varnish addition. One TeraOhm of polarization appeared in the original insulation in 12 seconds as seen in Figure 2B, but the period declined to 5 seconds after the trickle varnish resin was added, as depicted in Figure 3. This shows that polarization of the Zeus-rebuilt motor occurs quickly and the absorption current is too slight to be measured. The leakage current was 1 TeraOhm in both cases, which was much smaller than that in the original machine which was over 10 GigaOhms.
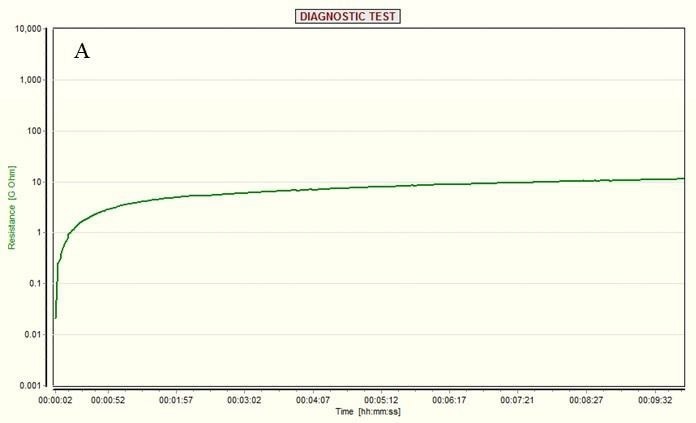
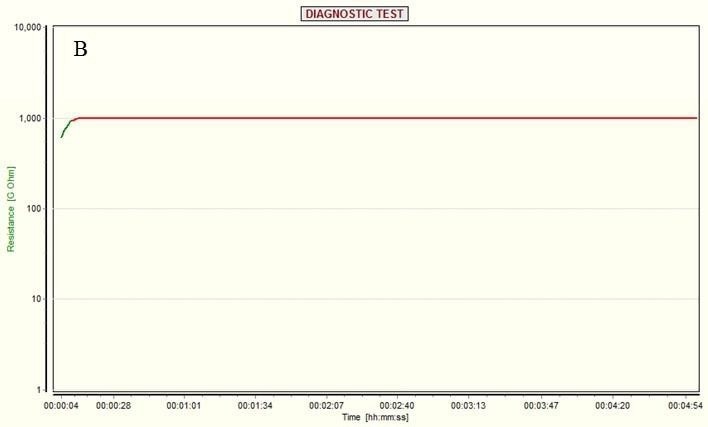
Figure 2. Motor insulation polarization indices. (A) Insulation resistance profile (IRP) of the original motor insulation system. (B) Insulation resistance curve before the addition of trickle varnish showing that the insulation polarized to 1 TeraOhm in 12 seconds.
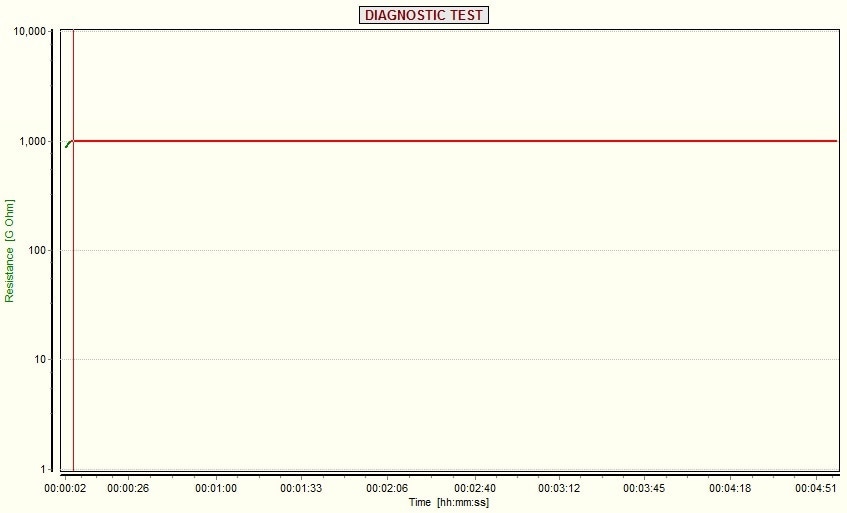
Figure 3. Motor insulation polarization index for the rebuilt motor after trickle varnish impregnation showing that the insulation polarized to 1 TeraOhm in 5 seconds.
Low and High Voltage Testing Using the Electrom iTIG D12
The Electrom iTIG D12 is an instrument designed to carry out a series of motor winding tests at both high and low voltages, to assess the insulation condition. Some of the tests are resistance, insulation resistance, dielectric absorption, polarization index, high potential test, and surge comparison.
Surge partial discharge tests show if there are voids within the insulation, which could lead to failure of insulation in applications that involve variable frequency drive (VFD). At low voltage, other tests are performed such as capacitance (C), dissipation (D) factor, inductance (L), impedance, phase angle (Ø), and quality (Q) factor.
The tests carried out on the original motor showed it to be at increased risk of winding failure during VFD applications, with the partial discharge being quite significant at 668,070 pC, as Figure 4A shows. With the rebuilt motor, partial discharge was observed to be 703 pC, a reduction by almost three orders of magnitude compared with the original motor, as seen in Figure 4B.
After trickle varnish application, the partial discharge went up by a small amount. The reduced partial discharge was observed even at higher voltages as well. This could mean that the Zeus motor had a better operating condition compared to the original build, and that it would resist winding failure in VFD applications.
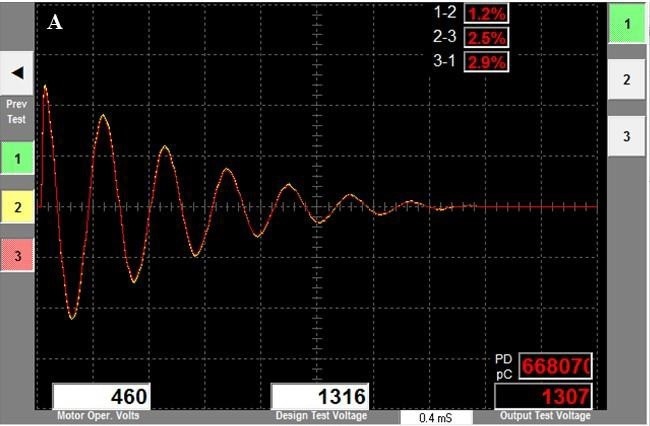
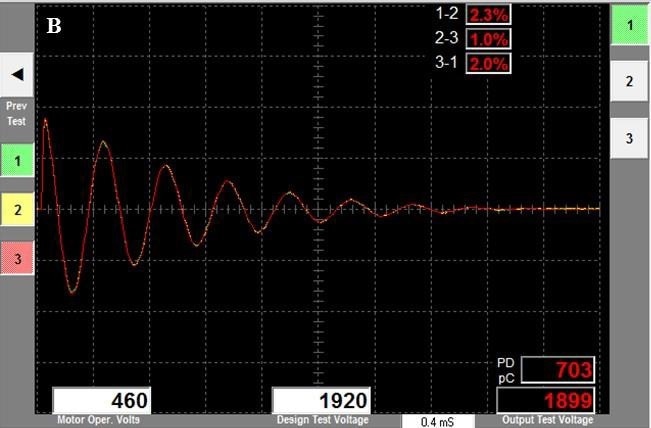
Figure 4. Partial discharge tests for the OEM and rebuilt motors. (A) Original insulation system showing partial discharge of 668,070 pC at 1316 V test voltage. (B) Zeus-rebuilt insulation system showing partial discharge of 703 pC at 1920 V test voltage.
Test results thus indicated much similarity between the original windings and those in the Zeus-rebuild, but with better capacitance, D factor and Q factor for the latter, as Table 2 reveals. The Q factor went down by about 1 after the rebuild in all of the three lead configurations tested. There was a 0.001 reduction in the D factor, corresponding to about 8.3%. The capacitance went up by 0.01 or about 7.3%.
Table 2. Results of low voltage testing for capacitance (C), dissipation (D) factor, inductance (L), impedance, phase angle (Ø), and quality (Q) factor: Top: original motor insulation system; Bottom: Zeus insulation system.
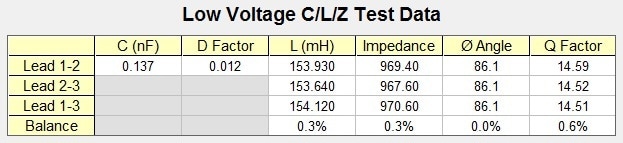
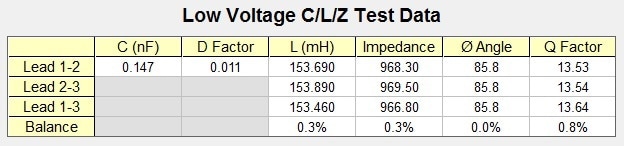
The All-Test Pro OL: Electrical Signature Analysis
The motor efficiency was tested on a dynamometer using specific values, as well as to pick up any important electrical or mechanical conditions of concern. The original and rebuilt insulation were both tested.
With the original insulation in place, the RPM was 1715 at 80% load, which was below the nominal value of 1725 RPM on the motor nameplate, seen in Figure 5A. After rebuild the efficiency value at the same load was 79.8%, as measured using Oak Ridge Motor Efficiency and Load software (ORMEL ′96), and the RPM was 1746 as Figure 5B shows.
With respect to voltage and current harmonics, the total harmonic distortion for current (THDC) and voltage (THDV) for the original motor insulation system was 2.4% and 1.3% respectively, while for the Zeus motor the THDC and THDV was 3.8% and 2.4% respectively. The higher values generally show reduced efficiency, but when viewed along with the higher RPM at the same load, it signified a greater motor efficiency after the rebuild.
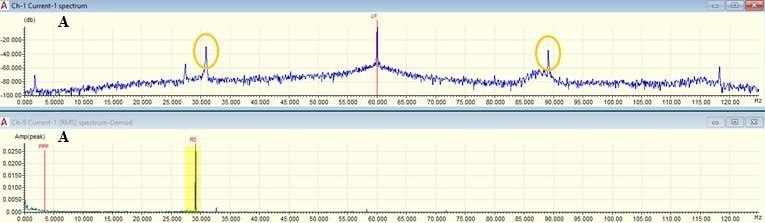
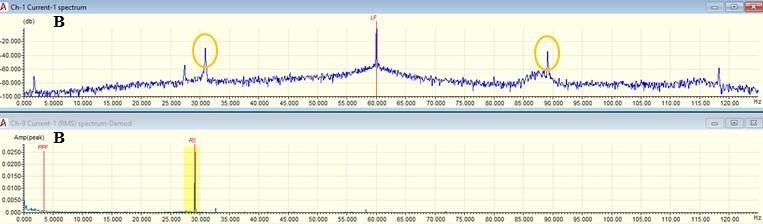
Figure 5. Dynamometer and motor efficiency test results. (A) Unbalance and misalignment (circles) detected in original motor. (B) Unbalance and misalignment (circles) detected in the new insulation motor.
Conclusion
The motor rebuilt using Zeus products performed better than the OEM insulation and winding material in several tests, such as the Q factor, D factor, capacitance, partial discharge, and winding stiffness. The partial discharge tests are especially significant in indicating better chances of survival in VFD (inverter) applications for the Zeus-rebuilt motor compared with the original.
This must be quantitatively assessed under different temperatures and testing conditions. Another finding is that the leakage current and absorption current are both very low following the rebuild, which was very much improved compared to the original. Lastly, the rebuilt motor seemed to have better operating efficiency than the original, due to decreased losses from the insulation system.
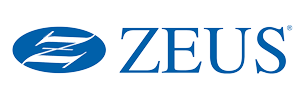
This information has been sourced, reviewed and adapted from materials provided by Zeus Industrial Products, Inc.
For more information on this source, please visit Zeus Industrial Products, Inc.