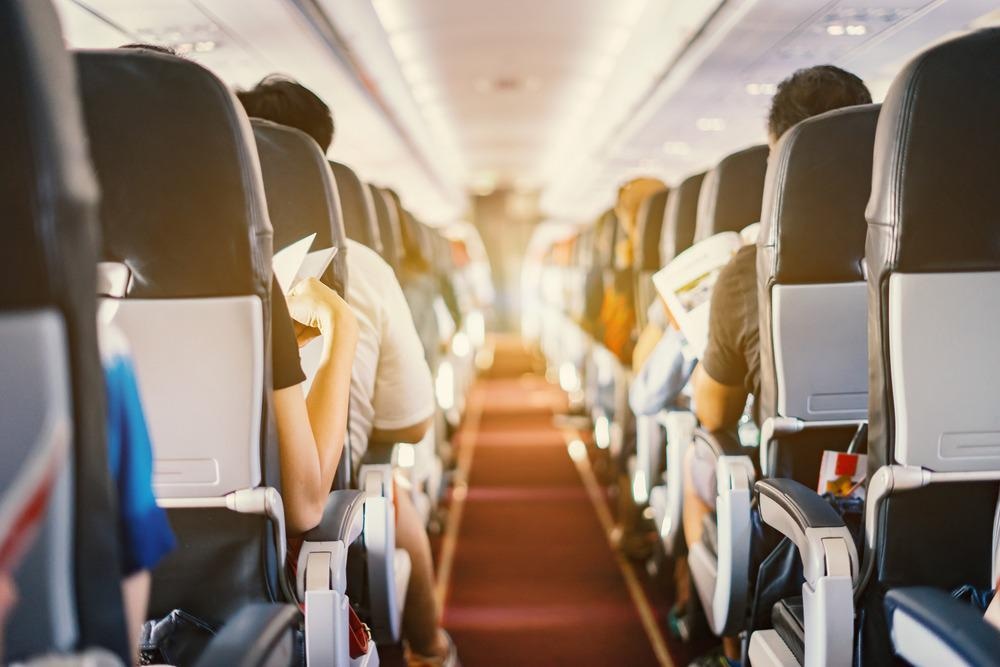
Image Credit: Have a nice day Photo/Shutterstock.com
In an industry as large and competitive as the aeronautical business, production optimization and efficiency are imperative. This need for production advancements is intensified further by increasing the environmental need to seek more sustainable methods. 3D printing is a relatively new manufacturing process, and aerospace companies are looking for more uses it has in the industry.
3D Printing vs. Traditional Manufacturing Processes
3D printing is a form of additive manufacturing (AM), which builds products up layer by layer. Its counterpart process, subtractive manufacturing, takes an object and removes material from it to create the final product (stamping out a component from a larger piece of sheet metal, for example).
Subtractive manufacturing is the more commonly used process and is more beneficial for larger parts that do not require intricate detail levels. However, the process struggles in waste; certain structural components of an aircraft can waste up to 90% of the machining process's original material (Balazinski et al. 2019).
The speed of the process is a notable factor. In high product volume, subtractive is almost always faster (the exceptions being products with exceptionally high detail). However, in some low volumes of components, or components that require customization, additive manufacturing can be significantly faster.
3D Printing in the Aeronautical Industry
It is important to note that 3D printing is already integrated into the aerospace industry. Large companies such as Airbus have been 3D printing brackets, clips, and holding devices for their aircraft (Griffiths, 2018). Its 2018 3D-printed spacer panel saw a 15% decrease in weight to the original, with no loss of aesthetic or functional value to the passengers (Griffiths, 2018).
How Much Further can Additive Manufacturing be Taken in the Industry?
Additive manufacturing is an appealing option in particular circumstances. However, the component must be under easily followed regulations, with a constant need for new components over a long period, to counter the long print times of some components (with larger components taking up to 80 hours to print (Griffiths, 2020)).
Thankfully, the aerospace industry does have a need for this. Aerospace engineers are aware of the nature of aircraft lifespans and cycles and how these things affect component usage and replacement. In checks, 5-10% of the passenger interior are damaged somehow (Griffiths, 2020).
Even though the cabin only contributes to 3-5% of the total cost (Lv, 2019), it is a large part of the design phase. This is the most customer-facing location of the aircraft, and therefore its aesthetic, ease of use, and comfortability define the airline’s brand and image (Lv, 2019). Because of this, rapidly produced, simple components such as cupholders and monitor shrouds can be continuously produced using 3D printing.
Not only does 3D printing satisfy the need for consistent, customer-facing component replacements, in some cases, it improves on current designs. The aforementioned monitor shrouds are 9-13% lighter than their traditionally manufactured counterparts (Griffiths, 2020). The cup holders can also be customized to reduce spillage risk, further reducing damage to the cabin.
Additive Manufacturing and Current Standardization and Certification
One of the most notable disadvantages of 3D printing and any other new production method introduced to the industry is the incredibly stringent standards and certifications needed for every aircraft component.
These requirements are justified, and aircraft components should be standardized as precisely as possible to ensure the passenger’s safety. However, they also make it challenging to introduce parts made from different manufacturing methods without some degree of friction. This is one of the main reasons manufacturers are not implementing more AM into their production line: The benefits of AM are outweighed by the risk that the parts will not meet these increasingly obsolete requirements (Griffiths, 2020).
If these standards and certifications were reconsidered to accommodate newer manufacturing methods, then this bottleneck (Griffiths, 2020) will be removed, and more AM innovations will be introduced.
Though 3D printing is unlikely to be responsible for the complete construction of an aircraft (at least, not with current technology), the expected range of AM usage varies widely, with some companies such as Etihad Airways suggesting up to 60% of a next-generation aircraft cabin could be 3D printed.
3D Printing Opportunities Outside the Cabin
Even in the many cases where additive manufacturing is not suitable to create the specific aircraft component, it can still be implemented to improve the subtractive manufacturing process. Researchers such as Lv (2019) have noted significant opportunities for additive manufacturing methods to develop toolings such as jigs, fixtures, mandrels, surrogates, dies, and molds.
In these single-use, job-specific tools, 3D printing would be a faster and cheaper production option. Another benefit of these parts is that the standardization for these components is less strict than aircraft components, meaning they do not run into any issues with certification checks. Currently, the aerospace industry's two giants, Boeing and Airbus, use 3D printing for this purpose (Lv, 2019).
References and Further Reading
Griffiths, L. (2018). How 3D printing is shaping the future of aircraft maintenance, repair & overhaul. [Online] TCT Mag. Available at: https://www.tctmagazine.com/additive-manufacturing-3d-printing-news/additive-manufacturing-aerospace-maintenance-repair/ Accessed 14th January 2021.
Griffiths, L. (2020). Additive manufacturing in the aircraft cabin [Online] TCT Mag. Available at:
https://www.tctmagazine.com/additive-manufacturing-3d-printing-news/additive-manufacturing-in-the-aircraft-cabin/ Accessed 14th January 2021.
Griffiths, L. (2020). There's "huge potential" for 3D printing inside aircraft cabins [Online] TCT Mag. Available at: https://www.tctmagazine.com/additive-manufacturing-3d-printing-news/the-huge-potential-for-3d-printing-inside-the-aircraft-cabin/ Accessed 14th January 2021.
Singamneni, Sarat & Lv, Yifan & Hewitt, Andrew & Chalk, Rodger & Thomas, Wayne & Jordison, David. (2019). Additive Manufacturing for the Aircraft Industry: A Review. Journal of Aeronautics & Aerospace Engineering. DOI: 10.35248/2168-9792.19.8.215
Hodonou, C., Balazinski, M., Brochu, M. et al. Material-design-process selection methodology for aircraft structural components: application to additive vs subtractive manufacturing processes. Int J Adv Manuf Technol 103, 1509–1517 (2019).
https://doi.org/10.1007/s00170-019-03613-5
Disclaimer: The views expressed here are those of the author expressed in their private capacity and do not necessarily represent the views of AZoM.com Limited T/A AZoNetwork the owner and operator of this website. This disclaimer forms part of the Terms and conditions of use of this website.