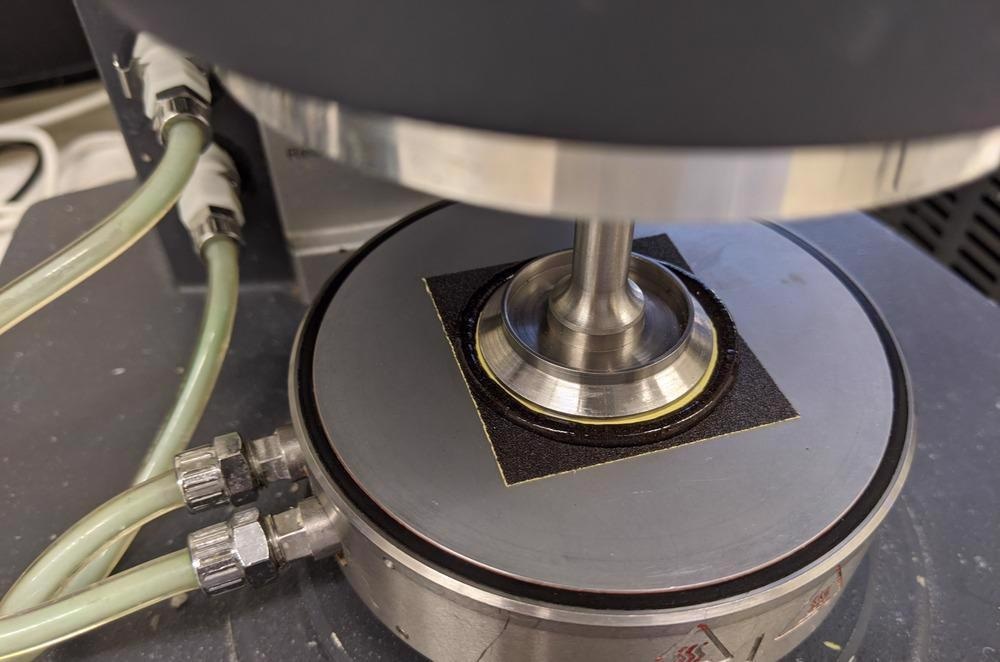
Image Credit: Bhavesh R Panchal/Shutterstock.com
In 2009, researchers at Anton Paar Germany utilized a rheometer linked to a tribology cell to effectively examine the tribological functionality of numerous greases. In a recent study, scientists used a similar analytical set up to investigate the grinding of various coated abrasives.
Coated abrasives such as sandpaper have been getting a significant amount of attention in recent years because of their increased usage in various industries and research fields, particularly in relation to manufacturing and industrial applications.
An exact grinding mechanism with a precise and known result is very valuable. In the industrial sector, it is very important that coated abrasives have standardized, exceptional quality. For this reason, it is important to have suitable analyzing methods for coated abrasives.
Scientists seeking to assess the potency of numerous coated abrasives often focus on tribology, which is the study of interfacing surfaces in motion relative to one another along with the description of system attributes, including the abrasive wear process. Notably, numerous phenomena within tribology, including wear and lubrication, are related to rheology, which is the science of flow and material deformation.
One of the instruments used in rheology is a rheometer. Some kinds of rheometers use a rotating cylinder to assess flow dynamics. These rheometers offer many perks in a tribology setting. Specifically, a rheometer has precise speed and force controls, as well as multiple rudimentary parameters relating to torque and temperature control.
Usually, coated abrasives are made up of a paper or cloth backing, an adhesive, abrasive grains, and other components essential for improving the abrasiveness. The two most widely used grain types in sandpaper are made of aluminum oxide or silicon carbide. Variants in material morphology and surface structure have a big effect on the performance and wear dynamics of coated abrasives. For instance, wear rate is strongly related to the grain size of a coated abrasive.
In tribological research, the experimental trials are often executed with different kinds of tribometers devices, including ball-on-disc and ball-cratering. With the aid of these classic tools, data on the wear process can be acquired, and information on important variables, including the wear coefficient and friction coefficient.
A surface ground by coated abrasives could be analyzed with various analytical techniques, including scanning electron microscopy (SEM) and optical microscopy. In addition, gravimetric approaches are often conducted. This involves weighing materials both before and after the wear test. Any abrasive loss can then be determined and applied for wear characterization.
Some commercially available tribometers offer comprehensive data with regards to friction mechanisms, but tribometers tend to be costly. Typically, a laboratory often has a rheometer, but not a tribometer. For this reason, developing a way to use a rheometer for tribology can reduce costs and allow for broader usage across different areas of study.
Applying a Rheometer to Tribology
According to a study due for publication in the Tribology Letters journal in June 2021, a team of Finnish researchers was able to develop a new technique for analyzing the wear behavior of coated abrasives by utilizing a rheometer connected to a tribology cell. The study team used a balls-on-disc type cell because it can execute tribological measurements in precisely outlined conditions to closely simulate real-life conditions using a manageable sample size.
The team investigated the tribological action of coated abrasives by having smooth steel balls grinding against various coated abrasives. The wear experiments were performed by an Anton Paar rheometer and tribology cell. The spring-loaded measuring shaft was lowered to achieve contact between the balls and the abrasive surface, which was placed on the cell's disc, and to apply the essential normal force at the point of contact site. The experimental setup rotated the balls around the disc at an established speed, as dictated by the rheometer. After the grinding phase, the team measured and documented the weights of the steel balls to identify mass decrease. SEM was also used for analysis.
Study Conclusions
The study team stated that its multidisciplinary setup was effective, and the results correlated with expectations based on previous research. For example, the results accurately demonstrated how wear increased relative to larger grain sizes.
As seen in previous studies, the Finnish researchers noted three distinct phases to the grinding process, which have been described as run-in, steady-state, and failure phase. These three specific stages allow for the precise comparison of different coated abrasives. The experimental setup also precisely showed how wear performance is strongly related to the degree of the normal force, with higher wear directly related to the higher normal force.
The study team did say more investigations are necessary to examine and enhance the testing variables of the combination system to measure a broader range of coated abrasives, with different kinds of grains and adhesives.
Resources and Further Reading
Gammelgård A. et al. A Method for Tribological Measurements of Coated Abrasives using a Rheometer. Tribology Letters. [Online] Available at: https://www.proquest.com/openview/4c75cc3eef75a1843bb34771945cf025/1?pq-origsite=gscholar
Heyer, P. et al. Correlation between friction and flow of lubricating greases in a new tribometer device. Lubrication Science. [Online] Available at: https://onlinelibrary.wiley.com/doi/abs/10.1002/ls.88
Disclaimer: The views expressed here are those of the author expressed in their private capacity and do not necessarily represent the views of AZoM.com Limited T/A AZoNetwork the owner and operator of this website. This disclaimer forms part of the Terms and conditions of use of this website.