In this interview, AZoM talks to Andrew Dugmore, Vice President of New Business Development at TRB Lightweight Structures, about the company, its assets and the future of the materials industry.
Could you please give us an overview of TRB's history?
TRB's roots are in lightweighting innovations - starting with adhesives that allowed for lightweighting of aeroplanes in the 20th century. Since the mid-50's, we have applied our knowledge of material science and manufacturing efficiency to provide lightweight components and structures for a wide variety of markets - Rail, Aerospace, Automotive, and more. Many people will not have heard our company name, but it's very likely you've used one of our products if you ride on trains, use the London Underground, ride in taxi's, or ride in electric buses. These days, we're focused on supporting the EV revolution through lightweight battery enclosures and other structural components.
What types of materials does TRB work with, and what applications and industries are these utilized in?
The main types of materials that the company uses are metallic and thermoset composite. Our metallic materials tend to be aluminum or aluminum honeycomb - lightweight structures that see aluminum bonded to both sides of a honeycomb structure.
Our composite materials tend to be thermoset, which consist of predominantly epoxy resin systems. These are often used with fabric such as carbon fiber, glass fiber, Kevlar, U.D, etc.
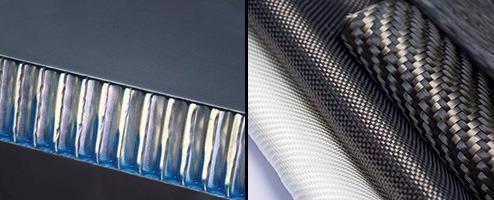
Image credit: TRB Lightweight Structures
The main applications for these materials and components are found in the rail, automotive and aerospace sectors.
The components TRB makes for the Rail industry are predominantly aluminium or aluminium honeycomb structures. These components, such as train doors, train flooring, interiors and partitions, are often finished with high-pressure laminate skin for cosmetic purposes, which is also very durable.
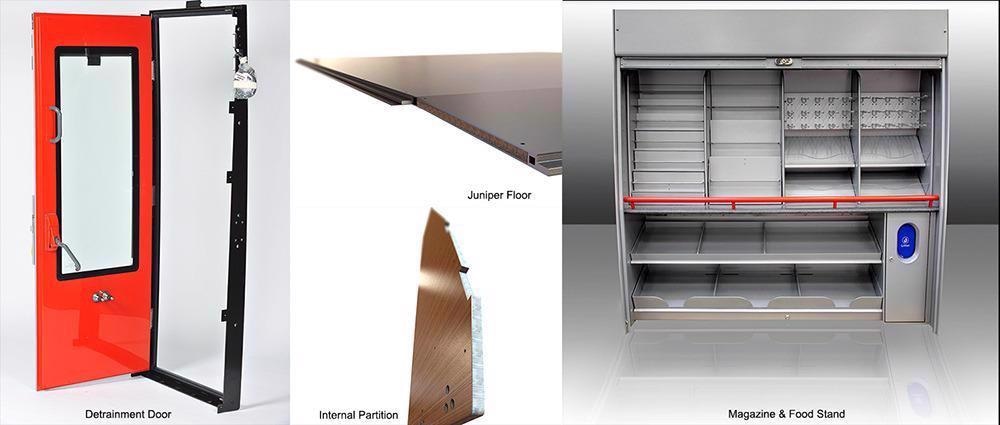
Image credit: TRB Lightweight Structures
In aerospace and aircraft interiors, we build, for example, overhead lockers, galleys and other modules. These components tend to use composite materials rather than metallic, typically using phenolic resin systems on glass fiber.
We also engineer and manufacture components that support the emobility sector, specifically battery enclosures. We design and manufacturing battery enclosures using both composites and aluminum materials to meet the criteria for several different emobility applications, from electric buses to UAVs.
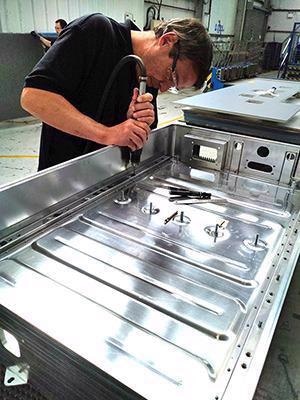
Image credit: TRB Lightweight Structures
The battery enclosures, when made from aluminum, tend to use sheet folded aluminum or extruded aluminum. If the customer requires further weight reduction, then composites can provide this.
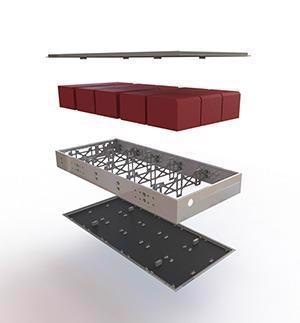
Image credit: TRB Lightweight Structures
For composite battery enclosures, materials such as carbon fibre, which is used for its strength and lightweight properties, are often used in conjunction with other materials such as glass fiber for electrical insulation and nickel veil for EMI shielding.
We often work with high-temperature applications, such as thermal runway protection in batteries, both at the module level and the pack level. Here we also use bio-resins, such as PFA, that derive from 100% waste Biomass.
What does TRB do differently from other component manufacturers?
TRB differs from other component manufacturers in a number of ways, not just in terms of its engineering prowess but also in its use of different materials for different applications.
We do not specifically point customers in the direction of metallic or composite materials. Rather, we determine what the customer’s goal is and then select the right materials based on that.
Because we work with both metallic and composite materials, the biggest differentiator for TRB is in our composite components. We manufacture the components in presses, using a system called Fast Press Cure (FPC) for mid to high volume manufacture. This is considerably quicker than the current industry standard process.
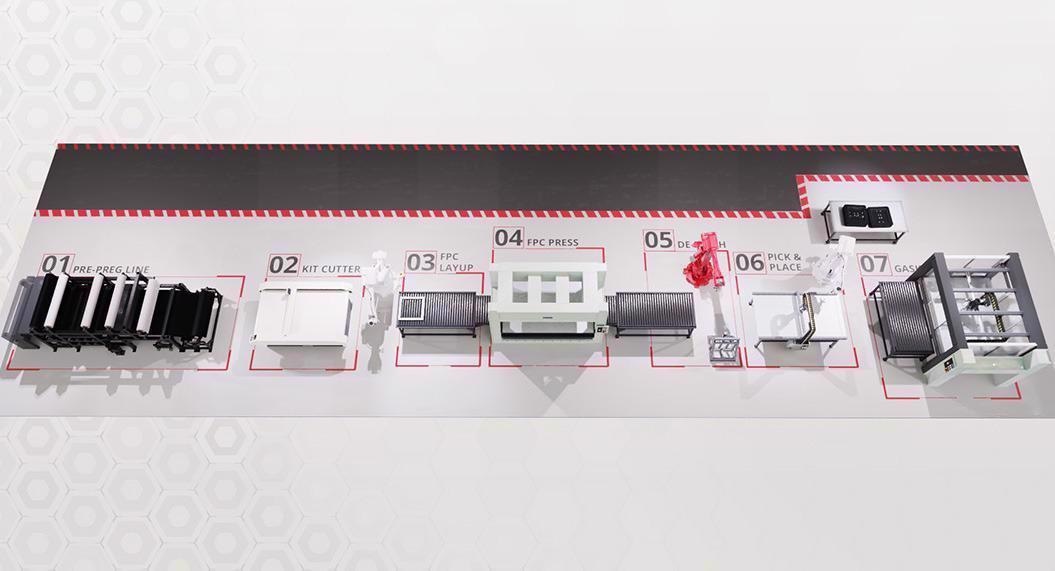
Image credit: TRB Lightweight Structures
For low-volume manufacturing, we still use autoclaves and ovens, but for high-volume applications, FPC takes out a lot of the manual labour, thus reducing the cost of the component considerably.
We are one of the very few manufacturers who actually produce all of our materials on site. We not only manufacture the components in composites, but we also manufacture the materials that go into the components - full inline composite production.
What is TRB doing to stay at the forefront of material science?
TRB already has many resin recipes, and we are always looking at new additions to these, including biocomposites and recipes utilizing more natural fibers and fabrics.
We work in collaboration with partners and our supply chain, and this helps us keep abreast of new developments in the industry, particularly in terms of materials for high-temperature and high-impact applications.
We also allow multiple materials to be impregnated at the same time because we manufacture our own materials.
By manufacturing materials onsite, we can develop new resin systems and impregnate these with new fabrics a lot quicker than many of our competitors, bringing these new components to market rapidly because there are no supplier minimum order quantities.
How do the design of components and the materials utilized to create these components impact energy consumption?
We work with both suppliers and customers to reduce the number of parts that are required. We also use thermally insulating materials within our enclosures, where required. This helps keep the requirements for cooling and heating of battery packs to a minimum.
All our components are designed to use space efficiently and to be lightweight, the lighter the component, the lighter the vehicle. This means ultimately the vehicle uses less energy and can extend its range.
What are some of the biggest challenges facing the composites and materials industries currently?
The biggest challenge for the composites industry at the moment is getting the materials and the components onto mid-to high-volume programs, particularly when it comes to composite materials. This has always been a challenge because composite materials are known for being an expensive and very labor-intensive market.
Thanks to our FPC process, the use of an automated production line and our ability to manufacture materials in-house, composite materials are now comparable to metallic structures in terms of both cost and capacity.
What do you see in the future of the composites and the material industry, and how does TRB fit into this?
In the future, we’ll see a big move towards automation of the component manufacturing process. We’ll see the speed of curing increasing, which is very important in meeting the takt time requirements for automotive applications.
We will also see the use of more industrial fibers in order to reduce material costs. Also a move towards sustainable materials and new processes which will enable carbon fiber to become fully recyclable. This is something TRB are working on at the moment.
Finally, I think we’ll see a lot more vertical integration required from OEMs and tier one suppliers in order to help bring the price point down for high-volume applications.
About the interviewee
Andrew Dugmore has been working in the composite engineering industry since 1991. He has been on the board of Composites UK and enjoyed the role of Chairman for Composites UK. Andrew has excellent knowledge of Polymers, Thermoset and Thermoplastics and has been instrumental in utilising his knowledge in the development of TRB's new vertically integrated composite manufacturing process.
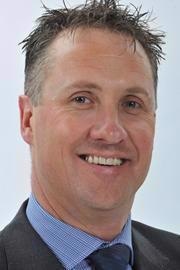
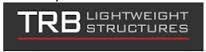
This information has been sourced, reviewed and adapted from materials provided by TRB Lightweight Structures Ltd.
For more information on this source, please visit TRB Lightweight Structures Ltd.
Disclaimer: The views expressed here are those of the interviewee and do not necessarily represent the views of AZoM.com Limited (T/A) AZoNetwork, the owner and operator of this website. This disclaimer forms part of the Terms and Conditions of use of this website.