At JEC World 2023, AZoMaterials spoke with Thorsten Groene, CEO & Co-Founder of Cevotec, about their Fiber Patch Placement technology and how the company has continued to grow and evolve.
Please could you give me some background on Cevotec as a company?
We at Cevotec enable manufacturers to produce complex composites in high volume and quality. We do this by providing industrial composite lay-up automation based on Fiber Patch Placement (FPP) technology, along with engineering software for laminate design and automated robot programming. Our equipment addresses lay-up challenges in aerospace and in composite tanks.
As a company, we started out about nine years ago as a spin-off from the Technical University of Munich. Today we are the leading supplier of patch-based lay-up technologies and serve customers across Europe, the US, and in Asia with our Fiber Patch Placement solutions.
Can you tell me more about the start and early years of Cevotec?
We kicked off full-time in the spring of 2014 after successfully securing a federal grant to transfer a promising new composite technology from R&D to the industry: Fiber Patch Placement. The grant allowed us to start up Cevotec in a university office and use their labs to advance the technology. FPP was initially invented by Airbus and then developed to TRL 2-3 in partnership with the Technical University of Munich. At that stage, we took over the technology stack and started to develop commercially viable solutions.
In 2015 we founded the company and went fundraising. It was pretty clear that, if we wanted to bring this to industry, we couldn't do this bootstrapped. Our first investment round in 2016 enabled us to hire the first employees and move out of the university office. We were then located at the Airbus Defense & Space campus in Munich for the next four years, as they just started their local start-up support program around that time.
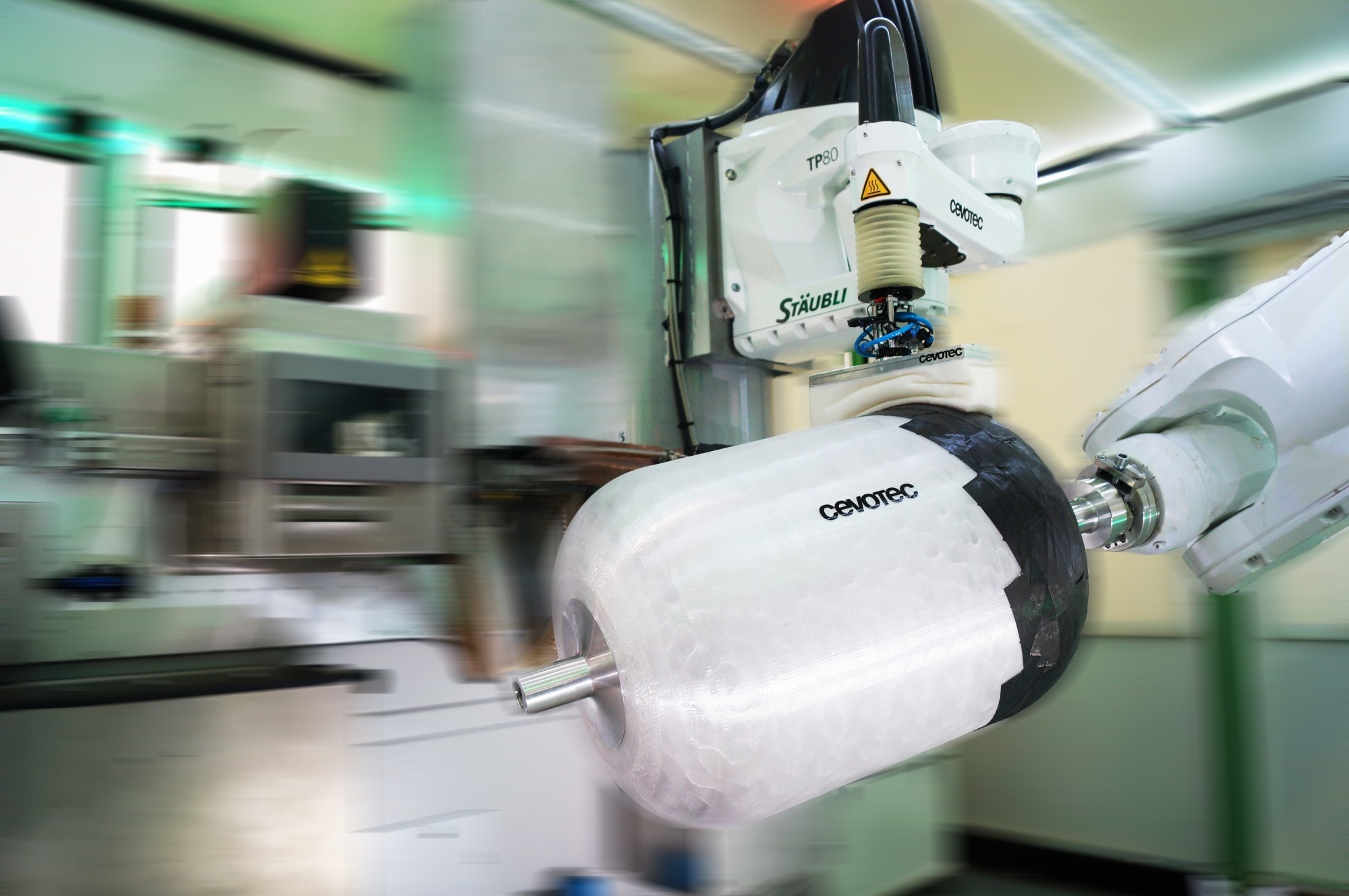
Image Credit: Cevotec
In 2021, we welcomed a new investor and entered a strategic partnership with GFM from Austria. They're a third-generation family business and have been successfully serving the aerospace industry for several decades. The partnership with GFM provides us with a stable basis for further growth and opportunities to collaborate and combine our technology solutions.
How did your relationship with Airbus strengthen your foundation as a business?
The FPP process was actually developed in a Ph.D. thesis of a student working with Airbus and the Technical University of Munich. Airbus holds some base patents that we license, and over the years, of course, we have developed our own IP around Fiber Patch Placement. The tech relationship with Airbus, therefore, can be seen as one of the foundations of our business.
The co-location on the Airbus Defense and Space campus was, in hindsight, a lucky coincidence. They are a relevant industry player in the Munich area, and they opened the campus to host innovative companies in the materials and processes business like us. From the beginning, we had several close connections to the most important aerospace player in Europe.
Cevotec uses fiber patch placement (FPP) technology to drive production in the composites field. What is FPP?
Fiber Patch Placement is a robotic-based pick-and-place composite lay-up technology. Defined fiber patches are cut from a tape and placed precisely onto complex 3D molds. The complexity of producible geometries is much larger than with any other automated lay-up technology. Our FPP systems achieve such complex lay-ups by using a dedicated, form-flexible patch gripper mounted on a 6-axis robot.
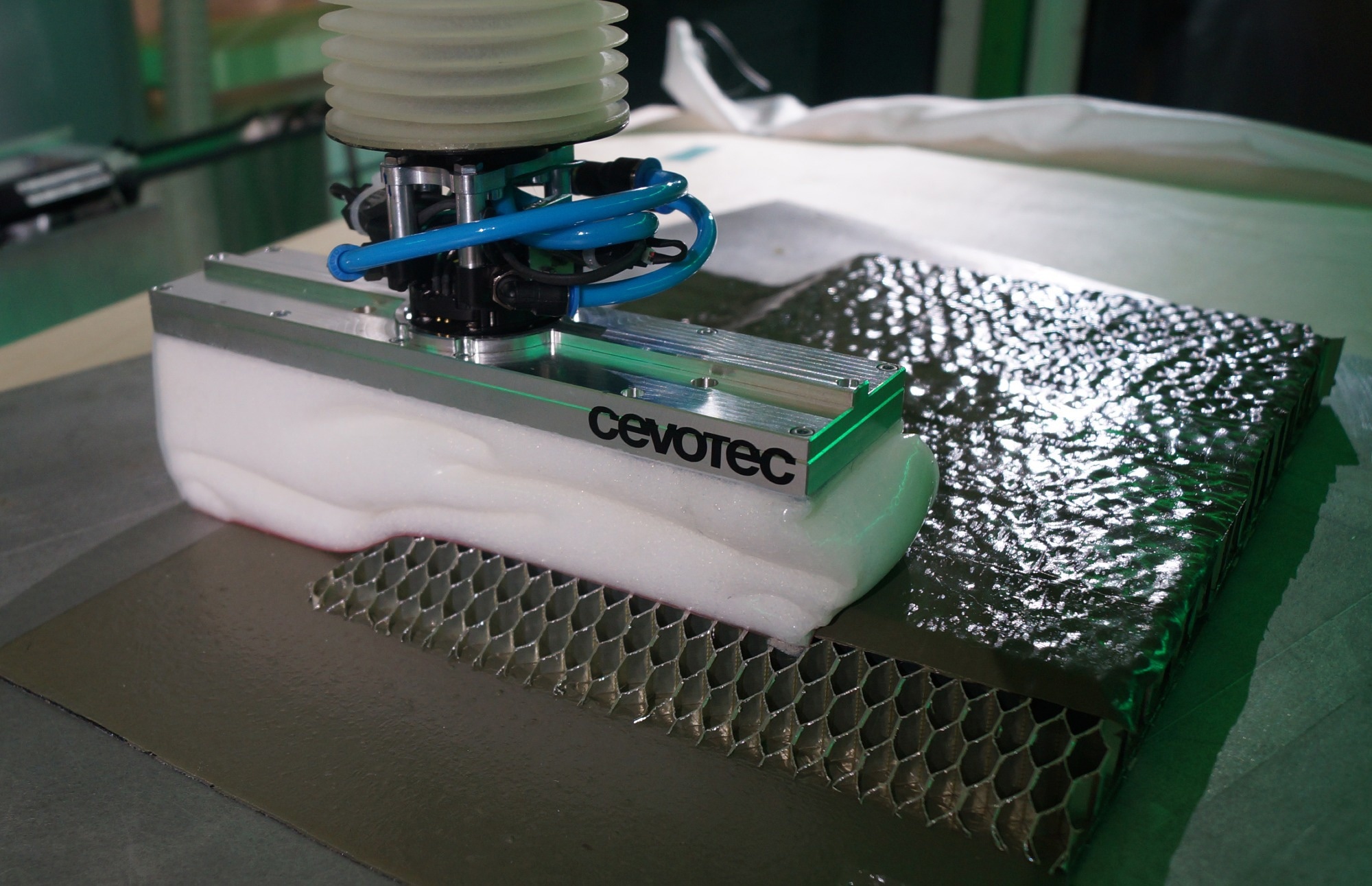
Image Credit: Cevotec
Over the past decades, aerospace has adopted and significantly advanced automated tape laying and automated fiber placement technologies (ATL / AFP). While these processes work well on flat or simple curved parts like wing or fuselage skins, they quickly reach their limits when the geometrical complexity is high, the parts are small, or the material differs from standard carbon fiber tape. We saw a big gap in the industry between the standard hand lay-up and those large AFP / ATL systems with continuous fiber tape.
We fill this gap with FPP technology. In order to handle the geometric complexity, we ask, "What’s the largest size that you can handle fully automated on that geometry with our grippers?" This is where the patch concept comes to life. We see it as additive manufacturing in “sensible increments”. What is sensible? Well, adjusted to the size and the geometry that we have at hand in order to enable automation. We want to go as large as possible for high productivity and as small as needed to achieve a great lay-up in high quality.
The patch concept also makes the process pretty material-agnostic, as our patch grippers easily handle a broad variety of materials. This significantly expands the automation envelope, e.g., for multi-material parts like sandwich structures.
You launched SAMBA and ARTIST STUDIO at JEC World in 2017. Could you tell me more about the equipment and the software system?
SAMBA is the trade name of our automated lay-up systems. In addition to featuring a very rhythmic sound by the pressured air it utilizes – which provided for the name in the first place – there are very versatile “tools” to automate complex fiber lay-up tasks. But before you can physically produce a lay-up, you need to “produce” it digitally: you need to design it.
One of the important early decisions that we took when starting Cevotec was to build our own software as a key enabler for FPP technology. Some of the first people we hired were software engineers, which, in hindsight, was absolutely the right decision.
You can only handle complexity if you have good software to deal with it. Of course, not every patch is created manually. There are algorithms for that. The designer determines the fiber direction and the lay-up area. The rest is done by the software. The software also has algorithms to optimize the position of patches in the different layers relative to each other. There is some secret sauce behind it that optimizes the strength and stiffness of the laminate.
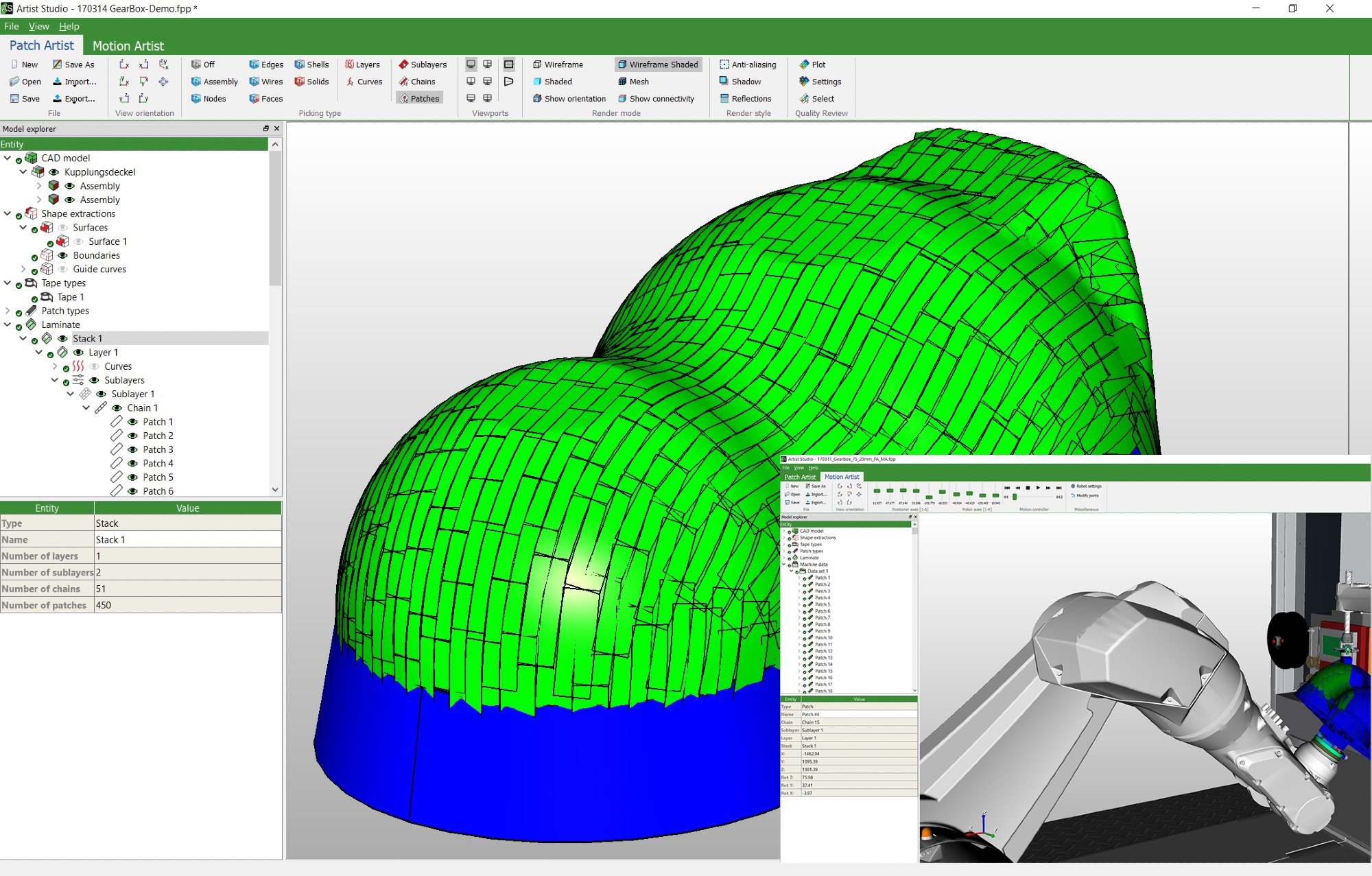
Image Credit: Cevotec
With our Finite Element Interface, designers can also export laminates to commercial FE software in order to run simulations on stiffness, strength, or whatever they want to calculate before moving to physical production. Once a laminate is defined, it is transferred to the second module, the CAD module of our software - Motion Artist. It works with the digital twin of the production system and the laminate that has just been created and programs the robots offline fully automated.
The software can simulate the entire production process. You can check for collisions and make adjustments as necessary. You end up with a production program that you upload to the system, and the production can start.
What are some of the ways that your technology is constantly evolving?
We at Cevotec are in a continuous FPP development process, especially as we learn about new applications that we can serve. For the pressure vessel application, our engineers have created special features that make it easier for designers of pressure vessels to reinforce the domes. Aerospace has its very own requirements that we take care of. In the scope of grant-supported development projects, we also team up with other value chain partners to develop new applications or process adaptations. In general, we follow a defined R&D roadmap that we constantly adapt to the needs of our customers.
Our SAMBA lay-up systems have probably seen the biggest evolution. We started with a flexible standard cell that we introduced in 2017. Since then, we’ve created an equipment “toolbox” with key modules in various sizes and for different applications.
The build envelope of the very first SAMBA system was approximately one cubic meter, dedicated to smaller parts. The system was very fast, but we soon learned that many customers require larger sizes. We then extended the capabilities of the system and also scaled the gripper technology. We started with a size of a business card, 60 x 40 millimeters. Now we have arrived at the equivalent of an A4 size of paper (300 x 200 millimeters), which is approximately 50 times that initial size.
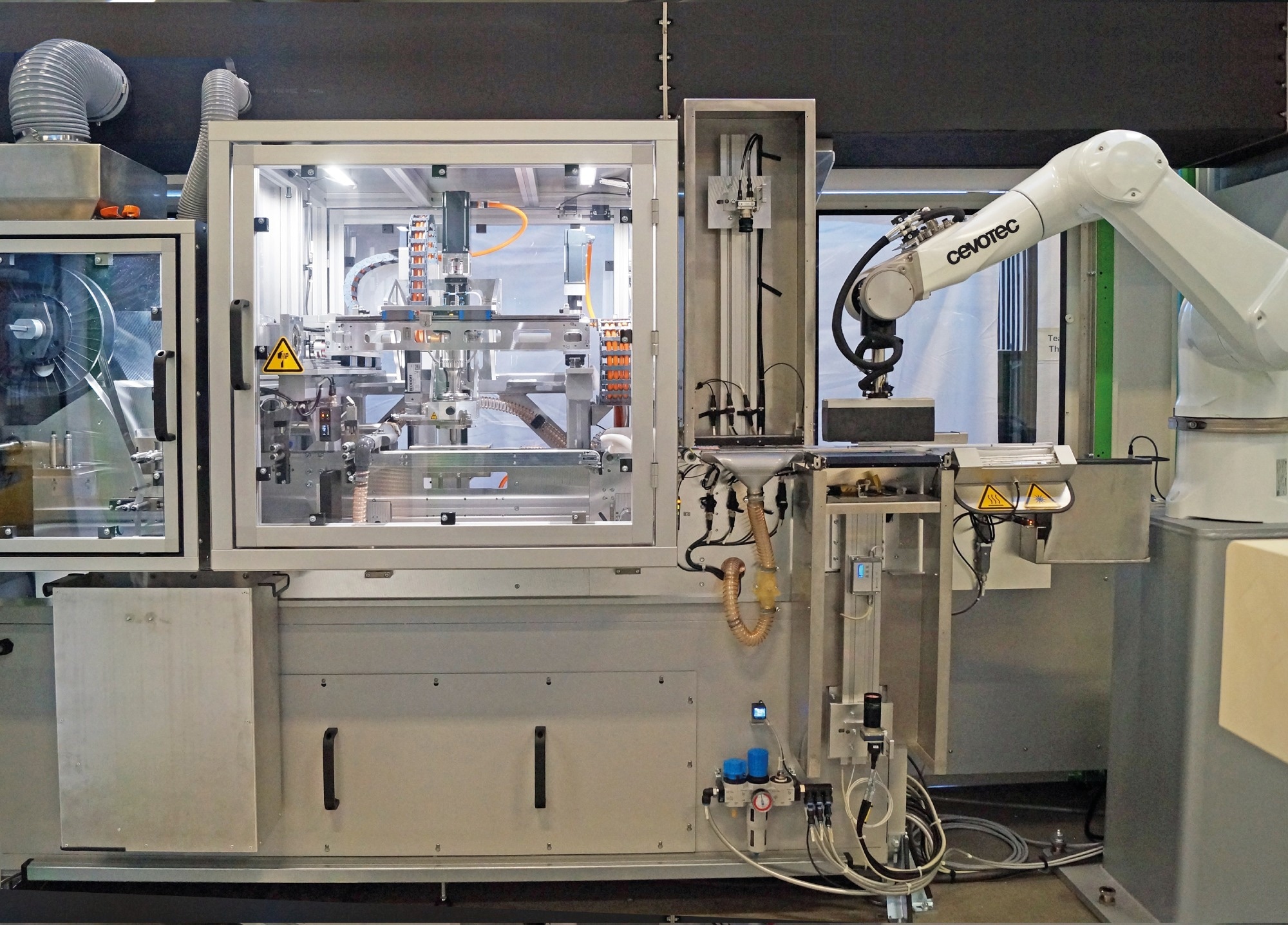
Image Credit: Cevotec
We also learned pretty soon that there is a need to process several materials in parallel or work with different tape widths, so we added a second material feeding line. Especially in aerospace, there's often more than carbon fiber to be placed. There's glass fiber, there are adhesive films, and there is special lightning strike protection material with copper mesh included. All of these difficult materials can be handled by our FPP lay-up system – we’ve tested and, where necessary, adapted our lay-up equipment for each material type. Broadening the range of processible materials over the last years was certainly also a key development of FPP technology.
Why is it important to be adaptable to the needs of industry?
As a supplier of high-tech equipment, we need to consider how our products are used by our customers. And how they would like to use them in the future. As technology experts, we can evaluate what’s possible with Fiber Patch Placement. From our customers, we learn how they think about composite lay-up of the next generation, and what’s important to them. It’s our job to match the possible with the desirable – and thereby create innovative solutions that exceed customer expectations.
Are there any new industries you are looking to break into in the future?
Due to its high-performance characteristics, FPP is focused on high-value applications for composites – typically in aerospace. We’ve trialed and tested applications in many different industries in the last years, and found the most attractive use cases for FPP in aerospace and composite tanks.
One additional industry we look at is the medical sector, in particular, prosthetics and orthotics, as well as exoskeletons. The composite parts are smaller but require high performance and high quality. Unfortunately, the volumes are not that high, which is why automation has not been yet so much in focus, but I can definitely see some applications for FPP there in the future.
What does research and development look like at Cevotec?
It pretty much looks like a joint effort of experts for composite applications, process automation, industrial equipment, and software technology. While our teams constantly work on improving our technology base, we also develop new applications for and together with our customers. And that’s a very important aspect of R&D at Cevotec – the focus on the customer application. We receive a lot of questions like: “Hey, that's interesting. Can it work for my part?”. We then take a look, and if positive, we propose a first small demo project.
Our Application Development team then takes over and develops applications for and with our customers on the basis of FPP technology, using our SAMBA lab systems and our ARTIST STUDIO software. Given the close collaboration of our technical teams, we can incorporate new features or adapt the process also on short notice as needed in project work.
When FPP operates in its sweet spot, manufacturers usually save between 20% and 60% of time and cost when switching to Fiber Patch Placement.
Why is it important for Cevotec to attend shows like JEC World?
It is an opportunity to speak with customers, suppliers, job candidates, industry media, and many more stakeholders. Trade shows offer opportunities for interested engineers to approach us very informally and educate themselves about Fiber Patch Placement, asking all kinds of questions. This informal exchange is easier in person than it is online.
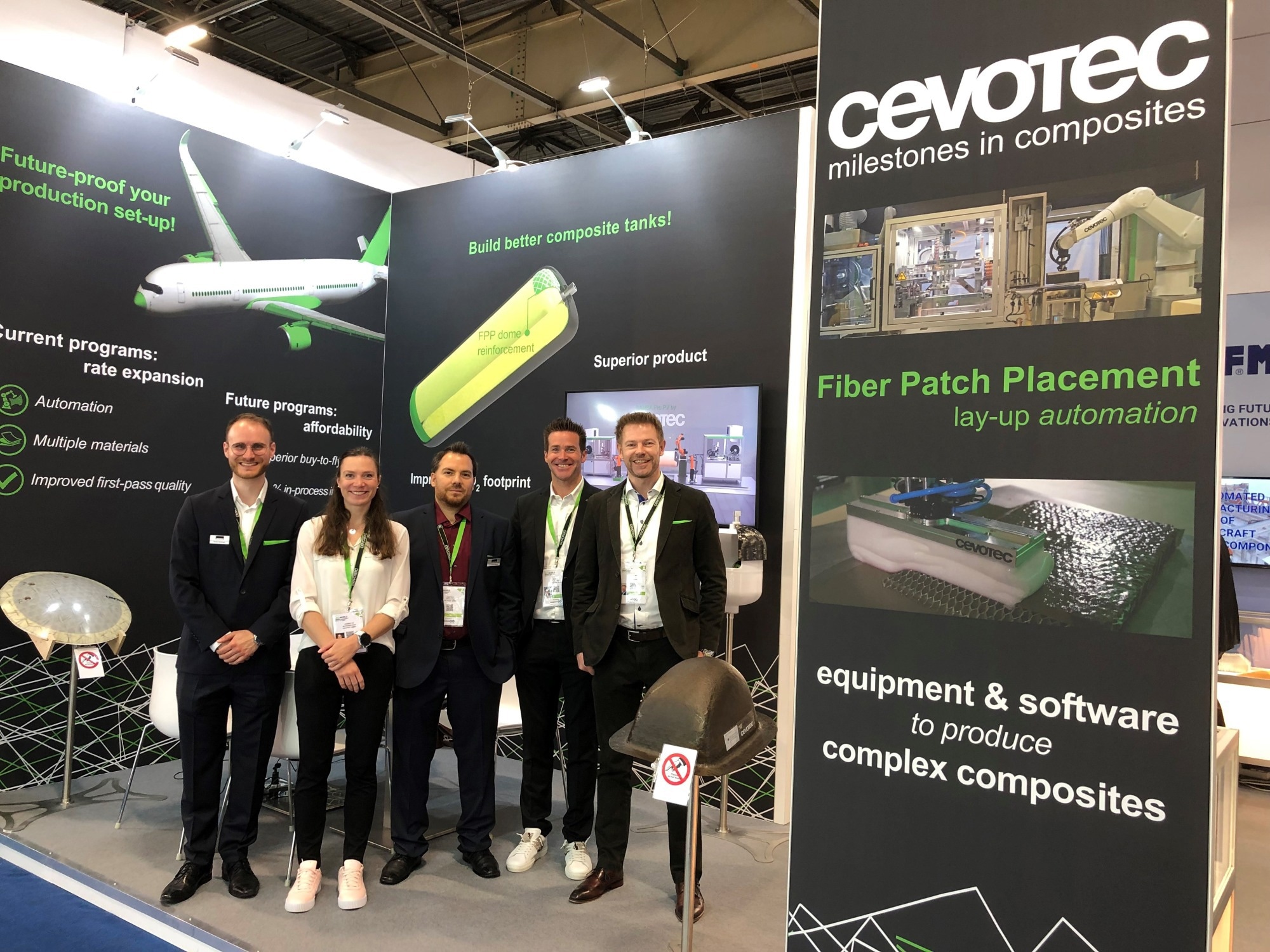
Image Credit: Cevotec
It's also great to meet up with customers and suppliers who you see only once or twice per year. Being able to schedule 5-10 meetings on one day is very efficient. We probably have had more face-to-face meetings over these three days at JEC than we had in the previous 12 months.
We always bring engineers to JEC World. In addition to being available for deeper technical conversations with visitors, they also take care of our suppliers and get updates on their latest developments that we can potentially use to improve our technological basis.
One feature of the composite industry is that nobody can do it alone. Everyone is required to collaborate along the value chain to bring composites to life. This also creates, in my opinion, a great atmosphere at these shows because it's really a global family of specialists.
How do you expect Cevotec will continue to grow?
The composite industry is well known for three-letter acronyms. JEC is one of them, and FPP (Fiber Patch Placement) is another. If you mention AFP or ATL in a composite context, almost everyone knows what you are talking about. They have become three-letter standards. Our big vision for 2030: add FPP to that list of three-letter standard technologies to process high-performance composites.
And on that route, we have certain strategies to grow, both technologically and geographically. For example, the US market is important to us, and we only just got started there. Last year we delivered the first FPP system on US soil to a very prestigious location, the National Institute for Aviation Research, NIAR, at Wichita State University. I couldn't imagine a better location for the first system over there because at NIAR, it can serve all interested US-based manufacturers with prototyping and demo projects.
We will see a growing number of Fiber Patch Placement deployments in the next years, both in aerospace and for composite tank reinforcements. This is what we are working hard for, but we’ve also promised our customers not to speak about ongoing projects, so I can’t reveal much more at this point yet. Stay tuned!
About Thorsten Groene
Thorsten Groene, CEO and Co-Founder of Cevotec GmbH, graduated as an MBA from IESE Business School with a strong technical mindset. Leading the company from its inception, Thorsten acquired a deep expertise in automated composite processes early on and assembled an exceptional team that developed Fiber Patch Placement from a scientific R&D project to an industrial automation solution for composite manufacturers in aerospace and renewable energy.
Disclaimer: The views expressed here are those of the interviewee and do not necessarily represent the views of AZoM.com Limited (T/A) AZoNetwork, the owner and operator of this website. This disclaimer forms part of the Terms and Conditions of use of this website.