PEEK is an organic thermoplastic material that has excellent chemical resistance and superior mechanical and physical robustness. As a result, this well-characterized material is often used in engineering applications.
It is generally used on the optical fiber to improve the strength of the fiber in adverse environments in the energy, civil engineering, aerospace, and medical industries. However, certain difficulties have been faced when using PEEK coating on optical fibers, for example, the physical stresses the fiber experiences as the coating cools down to below its glass transition temperature.
These distortions such as bends, compression, and other similar deformations negatively impact the transmission of fibers and lead to signal attenuation.
Zeus carried out initial testing to compare PEEK coated fibers against uncoated fiber to assess the performance and utility of PEEK coated optical fibers. Initial testing made using Zeus’ optical time-domain reflectometer (OTDR), suggested that attenuation characteristics were retained by PEEK coated fiber as opposed to the uncoated fiber.
In order to validate these findings, Zeus teamed up with Luna, an industry expert with specialized capabilities in fiber optic testing and technology. Luna’s optical backscatter reflectometer model 4600 (OBR 4600) was used to assess the Zeus PEEK coated fiber. Based on optical frequency domain reflectometry (OFDR), the device establishes the fiber’s optical properties.
OBR 4600’s sharp capabilities make it possible to identify defects that cannot be viewed clearly with a standard OTDR. When Luna’s OBR 4600 was used to test the PEEK coated fibers, deficiencies were observed in the fiber, which were otherwise not seen during the earlier testing process, especially for sections comprising of fiber Bragg gratings.
The PEEK’s compressive effects caused the arrays to display a deformed grating peak that could not be seen clearly with the previous Zeus OTDR. In order to deal with these issues, Zeus devised a uniquely optimized PEEK coating process to accomplish thermal stability with coated optical fiber.
Test Configuration
Testing was designed to assess whether decibel (dB) attenuation or loss was brought to a normal single-mode Nufern 155 µm polyimide R1550B-P fiber suitable for Brillouin based strain sensing and distributed temperature after applying the PEEK coating. The optical fiber was applied with the PEEK coating to create a last outside diameter (OD) of 400 µm. Engineers at Zeus and Luna carried out three testing modes comparing Zeus PEEK coated fiber and uncoated fiber:
- Elevated temperature testing when inducing small bend radii inside a test area of the optical fiber
- High temperature thermal cycling from ambient temperature to 240°C
- Sub-zero (low temperature) thermal cycling from ambient temperature to -10°C
For individual test modes, Luna's OBR 4600 was used to establish the dB loss over the fiber’s 250 m test area. To serve as a jumper between the test location and the instrument, the Luna OBR 4600 was fixed to a 150 m delay line.
A 455 m length of PEEK coated fiber and a 410 m length of the reference fiber were twisted together in about 0.4 m diameter loops, and they were placed initially in a freezer and then in a furnace for sub-zero testing and high temperature testing, respectively.
Two K-type thermocouples are located in each fiber to record the furnace’s internal temperature and the fiber’s temperature. Removal of the fibers was done by crushing the end and twisting the fiber into loops of 5 to 6mm diameter. Kapton® tape was used to hold these loops and to also lower back-reflection from the fiber end to levels that enabled the best Rayleigh backscatter signal-to-noise ratio and lowest noise floor.
Each fiber was scanned at each temperature interval and the data documented. With the help of the OBR software, the resulting data was assessed to determine the dB loss inside the fiber along the 250 m section, starting 50 m from the delay line end. After setting the insertion loss (IL) integration width at 20 m, the PEEK coated fiber and the reference fiber were tested individually. Prior to testing each fiber, reference data was collected (Figure 1).
.jpg)
Figure 1. Reference data for the PEEK coated (blue) and reference fiber (red) prior to temperature and bend radii testing.
At 150 m, a loss event was seen for the PEEK coated sample due to connector loss between the PEEK fiber sample and the 150 m jumper. However, this loss does not contribute to subsequent fiber testing (Figures 1 and 2).
.jpg)
Figure 2. Luna OBR 4600 screen capture depicting the loss measurement at 150 m for the PEEK coated fiber before temperature and bend radii testing.
Luna’s OBR 4600 was used to measure the polarization states for both fibers. It seemed that the development of the polarization states as a function of fiber length was from the fiber’s coiled section as identified with the OBR receiver (Figure 3 and 4).
.jpg)
Figure 3. Polarization states for the first 50 m of the measurement region of the PEEK coated fiber prior to the start of temperature and bend radii.
.jpg)
Figure 4. Polarization states for the first 50 m of the measurement region of the uncoated reference fiber prior to the start of temperature and bend radii testing.
Polarization states, S and P from the outer edges displayed a period of about few meters. This period was found to match with the birefringence beat length promoted by fiber coiling. There were no apparent inconsistencies with respect to the differences between the PEEK coated fibers and the reference fiber. This lack of difference seen between the reference and PEEK fibers indicates that the Zeus PEEK coating process has caused minimal, if any, residual strain.
Test Results
This section outlines the data acquired for the elevated thermal cycle, sub-zero testing, and bend radius testing.
Sub-Zero Test Results
In the initial sequence of tests, the optical fiber coils were placed within a sub-zero freezer and the temperature between -10°C and ambient temperature (~24°C) was cycled. Present in the freezer testing compartment, the K-type thermocouples were employed to find out the point at which temperatures stabilize before testing.
The average of the two thermocouple measurements was considered as the final temperatures. Subsequently, the Luna OBR 4600 was used to test each fiber optic cable for any dB loss along the length of the cable during the temperature cycling (Table 1).
.jpg)
Figure 5. Testing scheme for sub-zero temperature measurements showing placement of fiber optic coils in the sub-zero freezer.
Table 1. Loss results obtained during low temperature testing using Luna OBR 4600
Set point (Temp.) |
Reference Fiber |
PEEK Coated Fiber |
Measurement
(Temp.) |
Scan 1
(dB loss) |
Scan 2
(dB loss) |
Measurement
(Temp.) |
Scan 1
(dB loss) |
Scan 2
(dB loss) |
ºC |
ºC |
dB/km |
dB/km |
ºC |
dB/km |
dB/km |
Ambient |
24.1 |
1.20 |
1.17 |
24.1 |
1.23 |
1.24 |
-10 |
-10.6 |
1.11 |
1.08 |
-9.7 |
1.19 |
1.23 |
Ambient |
24.1 |
1.21 |
1.20 |
24.1 |
1.27 |
1.25 |
-10 |
-11.1 |
1.25 |
1.24 |
-10.1 |
1.13 |
1.11 |
Ambient |
22.9 |
1.04 |
1.02 |
22.9 |
1.51 |
1.53 |
23.7°C was the average ambient temperature for the low or sub-zero temperature cycling, and -10.4°C was the average low temperature (Table 2). At ambient temperature, 1.34 dB/km was the average loss of the PEEK coated fiber, but this loss was only slightly higher than that of the 1.14 dB/km average reference fiber loss.
Both the reference and PEEK coated fibers showed equal loss of 1.17 dB/km at -10°C. These results indicate that the PEEK coating used on the optical fiber does not change the fiber’s attenuation properties.
Table 2. Summary of sub-zero / low temperature cycling test results from Table 1
Average Temperature (Ref and PEEK ambient temps. were identical) |
Average loss |
Difference (PEEK – Ref) |
Reference Fiber |
PEEK Coated Fiber |
ºC |
dB/km |
dB/km |
dB/km |
23.7 |
1.14 |
1.34 |
0.20 |
-10.4 |
1.17 |
1.17 |
0.00 |
Elevated Temperature Testing
In order to determine the dB loss over an extended temperature range of ~217°C, elevated temperature analysis was carried out on the reference and the PEEK coated optical fibers. This was done by placing the test fibers in a furnace with the two K-type thermocouples as illustrated for the sub-zero fiber testing.
.jpg)
Figure 6. Testing scheme for elevated temperature cycling measurements showing placement of fiber optic coils in the furnace.
A temperature gradient inside the furnace compartment was detected by the temperature gradient. This temperature gradient was less than 10°C. After cloying test temperatures between 240°C and ambient temperature (~27°C), the fiber’s transmission loss was determined at ambient temperature - 100°C, 150°C, 200°C, and 250°C. Using the Luna OBR 4600, loss measurements were carried out on the increasing as well as decreasing temperature slopes of each cycle and examined similarly to the sub-zero testing (Tables 3 and 4).
Table 3. Loss results obtained during elevated temperature cycling using Luna OBR 4600
Set point (Temp.) |
Reference Fiber |
PEEK Coated Fiber |
Measurement
(Temp.) |
Scan 1
(dB loss) |
Scan 2
(dB loss) |
Measurement
(Temp.) |
Scan 1
(dB loss) |
Scan 2
(dB loss) |
ºC |
ºC |
dB/km |
dB/km |
ºC |
dB/km |
dB/km |
Ambient |
22.9 |
1.04 |
1.02 |
22.9 |
1.51 |
1.53 |
100 |
100.5 |
1.02 |
0.98 |
101.2 |
1.43 |
1.43 |
150 |
153.5 |
1.30 |
1.33 |
152.8 |
1.72 |
1.68 |
200 |
204.3 |
1.02 |
0.78 |
204.8 |
0.79 |
0.82 |
240 |
244.9 |
1.51 |
1.53 |
244.2 |
0.91 |
0.89 |
Ambient |
31.5 |
1.19 |
1.18 |
32.1 |
1.23 |
1.23 |
100 |
100.9 |
1.06 |
1.04 |
101 |
1.20 |
1.15 |
150 |
148.4 |
1.30 |
1.30 |
146.8 |
1.27 |
1.25 |
200 |
204.1 |
1.40 |
1.43 |
207.8 |
1.20 |
1.19 |
240 |
246.1 |
1.25 |
1.24 |
245.8 |
1.12 |
1.12 |
150 |
154.5 |
1.38 |
1.32 |
154.2 |
1.20 |
1.18 |
Ambient |
28.5 |
1.00 |
1.01 |
27.2 |
1.34 |
1.29 |
Table 4. Summary of elevated temperature testing results. (Ambient temperature: 27.4 - 6°C)
Average Temperature |
Average Loss |
Difference (PEEK – Ref) |
Reference |
PEEK |
Ref and PEEK combined |
Reference Fiber |
PEEK Fiber |
°C |
°C |
°C |
dB/km |
dB/km |
dB/km |
27.6 |
27.4 |
27.5 |
1.07 |
1.36 |
0.28 |
100.7 |
101.1 |
100.9 |
1.02 |
1.30 |
0.28 |
152.1 |
151.3 |
151.7 |
1.32 |
1.38 |
0.06 |
204.2 |
206.3 |
205.3 |
1.16 |
1.00 |
-0.16 |
245.5 |
245.0 |
245.3 |
1.38 |
1.01 |
-0.37 |
After the elevated temperature cycling and testing, the PEEK coated fiber and the reference fiber exhibited an average loss of less than 1.5 dB/km for each temperature tested (Tables 3 and 4; Figure 7).
.jpg)
Figure 7. Graphical representation of the attenuation data from Table 4 for the reference and PEEK coated fiber optics during elevated temperature cycling. Temperatures are the average of the PEEK and reference fiber temperature measurements combined.
At closer to ambient temperatures, the reference fiber showed less than 0.3dB/km loss as opposed to the PEEK coated fiber. However, in spite of this temperature being close to the PEEK material’s glass transition temperature, both fibers showed identical increased loss properties of about 1.35dB/km at 150°C.
At 150°C, the increased attenuation seen in the reference fiber was unexpected and remains unexplained at this point. However, at over 150°C, attenuation in the PEEK coated fiber seemed to reduce from 1.38 dB/km to 1.01 dB/km as and when the fiber was heated as opposed to the reference fiber.
While it is possible to measure to these attenuation variations between the two fibers, they are still considered to be extremely low. Therefore, the overall data indicates that Zeus PEEK coating does not have a major impact on dB attenuation for the coated optical fiber.
Bend Radius Testing
The last test was performed to measure the dB loss owing to the introduction of a bend of a known radius within the fiber. In this analysis, a fixture was constructed to hold the fiber at three varied radii by covering it around a cylinder.
On the test fixture, the reference R1550B-P fiber or the PEEK coated fiber was mounted and held on one side with a spring loaded clamp equipped with a silicone pad. This clamp pad ensured that the fiber does not get broken or strained by the clamping pressure. Subsequently, the fiber was wrapped 1.5 times around one of three radii of the fixture cylinder and again back to the clamp where it was securely fastened.
.jpg)
Figure 8. Test fixture used for bend radii testing. The Multiple radii test cylinder is in the middle of the fixture, and the silicone padded spring-loaded clamps are on the ends.
The radii of the cylinder measured 10, 30, and 50 mm. For these measurements, attenuation was performed over a 10 m fiber section. Selection of the exact position of the spring clamp on the fixture was done by introducing attenuation to the fiber. This was done by bending the fiber and at the same time measuring the attenuation seen in the fiber with the Luna OBR 4600 (Figure 9). The site at which the attenuation took place was plainly viewed and recorded.
.jpg)
Figure 9. Representative image showing the determination of the positioning of the spring clamp on the fiber by artificially inducing attenuation by bending (PEEK coated fiber shown).
The fiber was placed in the test fixture, and attenuation was determined at 150°C and near ambient conditions after placing the fixture in the furnace. Once the heated steady state temperature was reached, attenuation measurements were taken, and this was followed by removing the test fixture from the furnace and unwrapping the fiber from the cylinder.
Soon after, the fiber returned to ambient temperature. Once again, attenuation was measured when the unwrapped fiber reached ambient temperature. This process was again performed for each of the three bend radii as well as on the R1550B-P control fiber and the PEEK coated fiber.
At ambient conditions, the reference fiber did not exhibit any attenuation after thermal cycling to 150°C at 10 mm and 50 mm bend radii (Table 5).
Table 5. Attenuation during elevated temperature cycling at multiple fiber bend radii. Measurements were for a 10 m fiber test length containing the bend. (*Unwrapped fiber; ND = not determined.)
Radius |
Temperature |
Reference Fiber |
Temperature |
PEEK Coated Fiber |
Difference |
Scan 1 |
Scan 2 |
Scan 1 |
Scan 2 |
mm |
ºC |
dB |
dB |
ºC |
dB |
dB |
dB |
50 |
24.1 |
0.01 |
ND |
22.4 |
0.04 |
0.04 |
0.03 |
50 |
143.9 |
0.02 |
0.03 |
154.2 |
0.04 |
0.04 |
0.01 |
30 |
ambient |
ND |
ND |
33.6 |
0.03 |
0.04 |
ND |
30 |
136.0 |
0.03 |
0.00 |
149.2 |
0.04 |
0.03 |
0.02 |
10 |
146.8 |
1.60 |
1.59 |
150.5 |
1.23 |
1.22 |
-0.37 |
*0 |
24.1 |
0.01 |
ND |
22.4 |
0.02 |
0.02 |
0.01 |
As these were predicted results, no recording was taken for attenuation for the 30 mm radius for the reference fiber at ambient temperature. Similarly, the PEEK coated fiber and the reference fiber did not display attenuation at an elevated temperature when promoting a 30 or 50 mm radii bend in them.
An interesting fact was that for the 10 mm radius bend at 150°C, the PEEK coated fiber displayed 1.2 dB loss, and the reference fiber exhibited an attenuation of 1.6 dB, indicating 25% less attenuation as opposed to the reference fiber. This enhanced attenuation properties of the Zeus PEEK coated fiber can well be explained by the increased thickness of the fiber after applying the PEEK coating.
The thickness obtained would locate the fiber’s light guiding core inside a larger radius when compared to the uncoated fiber, alleviating attenuation.
Conclusion
Zeus Industrial Products partnered with Luna to evaluate the effects of a new optimized PEEK coating process designed by Zeus for use in fiber optic applications. The area of focus of Zeus’ primary project is developing a PEEK coating process that is thermally stable towards the optical fiber and allowing the coated fiber to maintain its desirable attributes like efficiency in signal transmission.
In this regard, Zeus and Luna designed a series of test procedures to assess Zeus’ PEEK coated fiber comparing attenuation in coated and uncoated fibers. The evaluation involved a battery of thermal cycling methods studying both low and high temperatures and their effects upon the fibers as well as upon Zeus’ PEEK coating process.
From the test results, Zeus’ PEEK coated optical fiber and the reference fiber showed identical attenuation across their 250 m test lengths at sub-freezing temperatures (~ -10°C). Compared to the reference fiber, the PEEK coated fiber showed only slightly increased attenuation (~0.2 dB/km) at ambient temperatures.
However, this deviation in attenuation between the reference and PEEK coated fibers decreased with increasing temperature to 150°C. At this point, their attenuation difference was equal. It is to be noted that the reference fiber exhibited increased attenuation at temperatures beyond 150°C when compared to the Zeus PEEK coated fiber.
After the temperature cycling tests, Luna and Zeus studied the effects of inducing small bend radii to the PEEK coated fibers and then compared attenuation in the uncoated reference and PEEK coated fibers. They also conducted these tests at higher temperatures. In this analysis, identical attenuation was observed in the uncoated reference and Zeus’ PEEK coated fibers across the 10 m fiber test lengths, at 50 mm and 30 mm bend radii, at ambient and at 150°C.
Notably, the uncoated reference fiber, however, exhibited greater attenuation compared to the PEEK coated fiber for the smallest bend radii tested, 10 mm, at 150°C
These findings reveal that no physical stresses or deformations like microbends were introduced into the fiber by Zeus’ PEEK coating process. Moreover, the data suggests that the coating shows thermal stability after its application and is not prone to shrinkage, especially where large temperature swings may take place.
The performance of the Zeus PEEK coated fiber was at least as well as the uncoated similar fiber, but with improved resistance to radiation, heat, and chemicals for which PEEK is known. However, under other conditions, the performance of Zeus PEEK coated fibers may be better than uncoated fibers.
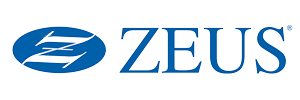
This information has been sourced, reviewed and adapted from materials provided by Zeus Industrial Products, Inc.
For more information on this source, please visit Zeus Industrial Products, Inc.