Semiconductor metrology, a pivotal aspect of the intricate semiconductor manufacturing process, navigates through the labyrinth of product quality, accuracy, and efficiency across numerous manufacturing steps. Encompassing the accurate measurement of multiple parameters in semiconductor wafers, such as line width, hole diameter, and thin film thickness, semiconductor metrology safeguards the semiconductor production pathway from potential pitfalls that come from imperfections and inconsistencies.
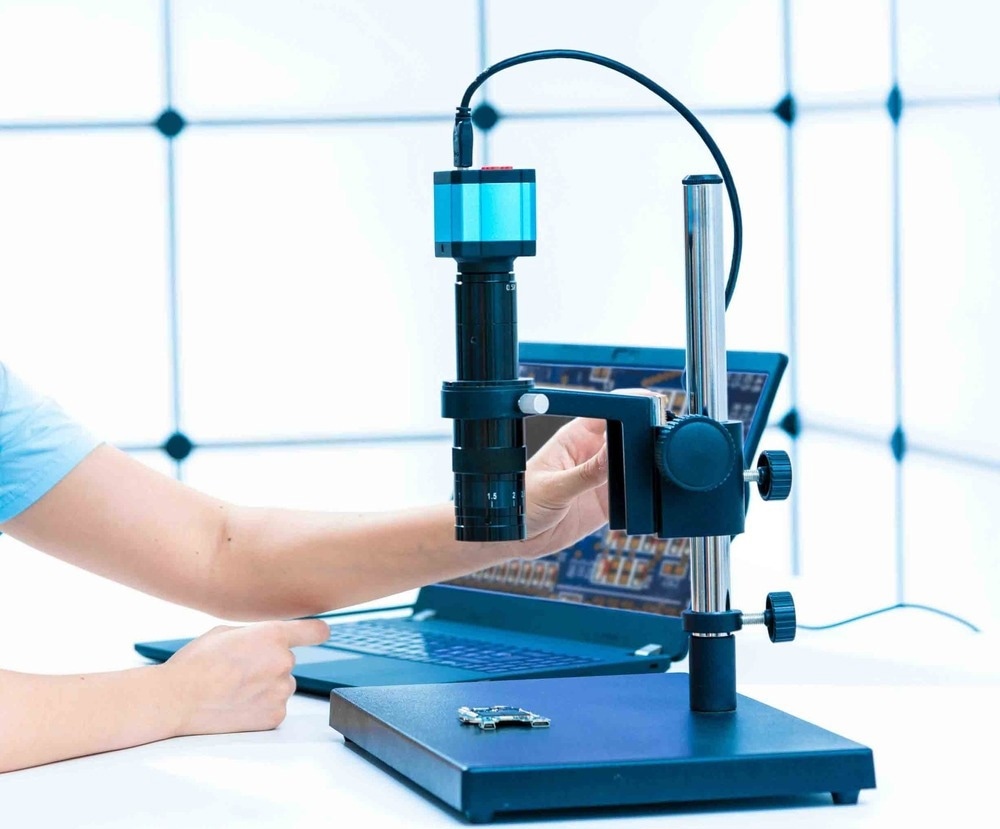
Image Credit: luchschenF/Shutterstock.com
Defining Semiconductor Metrology and Its Importance
Within the meticulous and layered journey of manufacturing semiconductor wafers, which could encapsulate anywhere from hundreds to thousands of steps over one to two months, even a minor defect or deviation in early stages could cascade into a domino effect, culminating in substantial resource wastage and reduced yield.
Semiconductor metrology has two major facets: providing the requisite detailed information about the physical properties of the wafer during the manufacturing process and enabling the optimal adjustment of the production process to adhere to specified parameters. In doing so, it not only ascertains the production of high-quality, reliable semiconductor devices but also significantly reduces wastage, ensuring that the manufacturing process remains economically viable and sustainable.
Key Measurements: Line Width, Hole Diameter, and Thin Film Thickness
Drilling down into the microcosm of semiconductor manufacturing, three critical measurements emerge as essential: line width, hole diameter, and thin film thickness. These measurements are crucial in ensuring the seamless transfer of circuit patterns and, thus, maintaining the desired functionality of the semiconductor devices.
- Line Width: This pertains to the width of the lines etched onto the semiconductor material, which are fundamental in ensuring that the electrical circuits are imprinted accurately. Ensuring that the line width adheres to the specified dimensions is pivotal for maintaining the integrity and performance of the semiconductor devices.
- Hole Diameter: Particularly relevant in the context of contact holes, which facilitate electrical connectivity across various layers of the semiconductor device, the hole diameter must be meticulously measured and controlled to assure optimal electrical performance and reliability of the final product.
- Thin Film Thickness: The thickness of the deposited films, integral for the electrical properties and structural integrity of the semiconductor devices, must be systematically measured to adhere to design specifications, ensuring that the semiconductor device performs reliably under varied conditions.
Metrology utilizes sophisticated equipment, such as CD-SEM (Critical Dimension Scanning Electron Microscopy) and ellipsometers, to navigate through the delicate intricacies of these measurements, ensuring accuracy and precision and thereby safeguarding the efficacy and reliability of the manufactured semiconductor devices. The tailored synergy between various metrology tools and strategic methodologies underscores a vital backbone, ensuring that semiconductor manufacturing processes not only achieve but consistently maintain a pinnacle of excellence and reliability throughout the production lifecycle.
The Critical Role of Metrology in Semiconductor Manufacturing
- Importance of Early Defect Identification
Early-stage defect identification is pivotal to preclude the percolation of errors or imperfections into subsequent manufacturing steps, thereby safeguarding against escalated resource consumption and potential wastage. Semiconductor metrology, through its vigilant screening, curtails the proliferation of such defects, ensuring that each subsequent step is built upon a foundation that is robust and error-free. This is imperative to guarantee that the final semiconductor products are not only of superior quality but also reliable in their functionality.
- Strategic Placement of Metrology and Inspection Processes
Strategically embedding metrology and inspection processes at pivotal junctures throughout the manufacturing pathway enables a continuous and dynamic quality check. This ensures that deviations from desired parameters are identified and rectified in real time, maintaining a consistently high yield and ensuring that the final product adheres to the requisite quality and performance benchmarks. In essence, strategic metrology acts as a series of checkpoints, safeguarding the integrity of the manufacturing process from start to finish.
Tackling Challenges in Semiconductor Metrology
Navigating through the layered complexity of semiconductor manufacturing, metrology confronts a myriad of challenges, demanding a meticulous balance between accuracy, efficiency, and resource optimization to ensure optimal output.
- Balancing Accuracy and Efficiency
Ensuring unparalleled precision in measurements while concurrently maintaining an optimal pace of production posits a complex challenge. Too much emphasis on one can inadvertently compromise the other, thereby impacting overall output and effectiveness. A delicate equilibrium must be established, where the exacting precision of measurements is upheld without stalling the manufacturing process. The advent of cutting-edge metrology technologies, such as the eBeam metrology systems by Applied Materials, signifies strides towards achieving this balance by facilitating precise imaging and measurements of nanoscale features without compromising on efficiency.
- Managing Hundreds of Steps in Wafer Production
Each wafer undergoes hundreds, sometimes thousands, of meticulously orchestrated steps in its manufacturing journey. Managing and ensuring quality and precision across these multifarious steps demands an intricate web of coordination, monitoring, and control. Metrology, in this context, is tasked with not only ensuring that each individual step adheres to specified parameters but also ensuring that they harmoniously converge to culminate in a product that meets the desired benchmarks in quality, reliability, and performance.
Tools and Equipment in Semiconductor Metrology
Metrology equipment is the linchpin around which the scrutiny and measurement of semiconductor wafers revolve.
Introduction to CD-SEM and Ellipsometers
Critical Dimension Scanning Electron Microscopes (CD-SEM) and ellipsometers are paramount in the realm of semiconductor metrology, each offering a unique set of capabilities in terms of measurement and analysis. The CD-SEM specializes in gauging the critical dimensions of semiconductor patterns, such as line width, while ellipsometers provide vital data about the thickness and refractive index of thin films. Together, they offer a comprehensive analysis of the semiconductor wafers, ensuring each layer and pattern adheres to the precise specifications required.
Navigating the Use and Functionality of eBeam Metrology Systems
eBeam metrology systems, such as those deployed by Applied Materials, are celebrated for their capacity to conduct precise imaging and measurement of nanoscale features on semiconductor wafers. The utility of eBeam metrology systems extends to applications like defect review, inline monitoring, and lithography, mapping the microcosm of the semiconductor wafer with exceptional accuracy and detail, thus facilitating the maintenance of product quality and manufacturing consistency across the semiconductor manufacturing spectrum.
Applied Materials: Enabling Cutting-Edge Semiconductor Technologies
Insights into VeritySEM® CD-SEM and Its Capabilities
VeritySEM® CD-SEM, a cornerstone in Applied Materials’ eBeam metrology offerings, represents the zenith in precision imaging and nanoscale feature measurement. It ensures semiconductor manufacturers can perpetually scrutinize and validate the minute details of their wafers, thereby guaranteeing that the end products not only adhere to but surpass the requisite quality and performance benchmarks. VeritySEM® CD-SEM is distinguished for its ability to deliver detailed and accurate measurements, thereby becoming an invaluable asset in the intricate processes of semiconductor manufacturing.
Enhancing Imaging and Nanoscale Feature Measurement
Imaging and measuring nanoscale features with utmost accuracy is imperative in semiconductor manufacturing to safeguard the reliability and performance of the final products. This is particularly pivotal as we tread further into the era of miniaturization and complex, multi-layered semiconductor designs. Enhanced imaging enables manufacturers to visualize and assess the intricate patterns and layers of the semiconductor wafer, while precise nanoscale feature measurement ensures that even the minutest deviations are identified and rectified, ensuring the integrity of the final product.
Applied Materials, through technologies like VeritySEM® CD-SEM, provide the industry with the tools it needs to navigate through this nanoscale world.
Case Study: Establishing a Robust Semiconductor Metrology Hub in Europe
Applied Materials and Fraunhofer IPMS: A Collaboration of Expertise
In a significant stride towards fortifying Europe's semiconductor industry, Applied Materials and the Fraunhofer Institute for Photonic Microsystems IPMS have come together to pave the way for an innovative era in semiconductor metrology through a pioneering collaboration.
The joint venture between Applied Materials and Fraunhofer IPMS has germinated into the largest technology hub for semiconductor metrology in Europe, nestled at the Center Nanoelectronic Technologies (CNT) of Fraunhofer IPMS in Dresden. This hub is not merely a physical entity but a symbolic epicenter of innovation, expertise, and future-driven research, projected to influence semiconductor R&D across Europe by providing access to state-of-the-art eBeam metrology equipment and shared knowledge from both powerhouse organizations.
Choosing Silicon Saxony in Dresden as the locale for this technology hub is a strategic decision, injecting vitality into Europe's largest semiconductor cluster. This geographical positioning not only signifies an infrastructure-laden, resource-rich environment but also ensures proximity to a vibrant network of researchers, manufacturers, and industry stakeholders, thereby establishing a fertile ground for symbiotic growth and innovation in semiconductor technologies.
The technology hub is poised to be a catalyst in the realm of semiconductor research by providing access to advanced eBeam metrology systems, thus propelling forward the cycles of learning and development in semiconductor manufacturing. These systems permit researchers to probe into the microcosmic world of semiconductor materials and structures with unparalleled precision, thereby aiding in the swift transformation of conceptual knowledge into applicable technologies.
By fostering an environment where knowledge and resources are shared, and industry challenges are tackled collaboratively, the hub aims to evolve into a pulsating nexus that nurtures innovation and seeds advancements in the semiconductor domain. Its embrace is expected to extend beyond mere technological innovation, providing a platform where new applications can be developed, processes can be validated, and industry challenges can be addressed through a synergized, collective effort.
Spotlight on Research in Semiconductor Metrology [1]
Studies and research reports often unveil new methodologies, highlight challenges, and propose solutions in the semiconductor manufacturing process, particularly focusing on aspects like defect detection, measurement precision, and process optimization. Summarizing these findings not only encompasses identifying key takeaways but also involves distilling complex data into information that seeds understanding and drives forward advancements in practical applications.
A study titled “Metrology for the Next Generation of Semiconductor Devices” uncovers a series of insights that are pivotal in semiconductor metrology. Detailing technical innovations and identifying potential bottlenecks, the study underscores the need for advanced metrological solutions. The findings spotlight technological requirements, anticipated challenges, and proposed methodologies that could pave the way for the seamless integration of next-gen technologies into semiconductor manufacturing, ensuring that metrological processes evolve in tandem with semiconductor devices.
Engaging with Technical Details and Insights
While the technical intricacies of semiconductor metrology are foundational to advancements in the field, rendering these insights accessible to non-experts is pivotal for fostering a comprehensive understanding and appreciation of the technology. This entails distilling complex technical data into comprehensible information. This accessibility not only democratizes information but also engenders an environment where expertise is shared, understood, and valued across various strata of the semiconductor industry and beyond.
Conclusion
Within the meticulous realms of semiconductor metrology, recent studies such as "Metrology for the Next Generation of Semiconductor Devices" underline a future sculpted by nuanced technological needs and evolving manufacturing processes. These insights do not merely herald advancements but also bring to light the need for tailored metrological solutions that align with the growing complexity of semiconductor devices.
The strategic alliance between Applied Materials and Fraunhofer IPMS, amidst the spirited Silicon Saxony cluster, heralds an era wherein collaborative innovations, accelerated learning cycles, and symbiotic relationships between research and application come to the forefront.
Europe's journey in maintaining its leadership in semiconductor innovation will undeniably be characterized by its commitment to nurturing a thriving R&D ecosystem capable of attracting global talent, securing investments, and forging partnerships that further bolster its position on the global stage. The semiconductor industry in Europe, underpinned by a spirit of unbridled innovation and a steadfast commitment to research and development, stands poised to navigate through the labyrinth of future challenges, ensuring its sustained leadership in global semiconductor innovation and continuing to illuminate pathways for technological advancements across myriad applications and industries.
More from AZoM: Sustainable Technology in Semiconductor R&D
References and Further Reading
- N. G. Orji, M. Badaroglu, B. M. Barnes, C. Beitia, B. D. Bunday, U. Celano, R. J. Kline, M. Neisser, Y. Obeng, A. E. Vladar (2018). Metrology for the next generation of semiconductor devices. Nat Electron, 1, doi: 10.1038/s41928-018-0150-9. [Online] Available at: https://www.ncbi.nlm.nih.gov/pmc/articles/PMC6605074/
- Taha Khan (2023, August 23). A New Home for Europe's Semiconductor Metrology. AZoNano. [Online] Available at: https://www.azonano.com/article.aspx?ArticleID=6530
Kuhn, M., Cea, S., Zhang, J., Wormington, M., et al. (2017). Transistor Strain Measurement Techniques and Their Applications. In Metrology and Diagnostic Techniques for Nanoelectronics, Eds. Z. Ma and D.G. Seiler [Online] Available at: https://books.google.com.sa/books?hl=ar&lr=&id=auneDwAAQBAJ&oi=fnd&pg=PP18&ots=Qz9DpAuUoz&sig=pMq8GozTeZ-AwcMbj3ItITW6n_A&redir_esc=y#v=onepage&q&f=false
Disclaimer: The views expressed here are those of the author expressed in their private capacity and do not necessarily represent the views of AZoM.com Limited T/A AZoNetwork the owner and operator of this website. This disclaimer forms part of the Terms and conditions of use of this website.