Introduction Numerous studies have been devoted recently to porous Si3N4 as well as SiAlON ceramics and their composites [1-8]. These materials offer exciting opportunities for applications, in hot gas filtration, high temperature separation membranes, and catalyst supports, due to their excellent mechanical properties, thermal resistance, thermochemical corrosion resistance and thermal shock resistance. For filtration applications, the pore size is critically important, as small particle size will lead to a decreased permeability, and as large pore size will result in escape of the particles. It can be concluded that the desired pore size of these ceramics depend on an application, so that the pore size should correspond to the mean size of particles that will be filtered. As an example of application of these non-oxide porous ceramics, ceramic candle filtration is an attractive technology for the removal of particulate at high temperature in Pressurized Fluidized Bed Combustion (PFBC), Integrated Gasification Combined Cycle (IGCC) and other coal utilization processes. This is due to their simple, cost effective design, excellent high-temperature/chemical stability, and effectiveness in particulate removal [9]. In these systems, the size of coal ashes was as fine as below 50 μm, so that porous ceramics with a mean pore size of 20-50 μm are strongly indicated. In our previous work, we fabricated several Si3N4- based porous ceramics, through various processes such as partial hot-pressing [4, 5], partial sintering [10, 11] and reaction sintering [12, 13]. The porous Si3N4 ceramics fabricated by these processes have pore sizes as small as around 1 μm. Although their mechanical strength is high, the permeability is not high enough. One method commonly employed to fabricate porous ceramics is to add fugitive particles to an initial ceramic mixture to produce large regularly-spaced pores. Various different fugitive particles were investigated: (i) equiaxial organic particles, such as starch powder [14], plastic particles (carbohydrate powders) [15], (ii) long fibers, such as cotton threads [16] and metal wires [17]. Uni-directional pore morphology is preferred for high permeability, but the fabrication process is too complicated and difficult for components of large size. To overcome the shortcomings of using long fibers to fabricate porous ceramics with uni-directional pores, it is considered that short fibers can be used as a pore- forming agent. The resultant pores are random, but the pore morphology is a long, rod-shaped tunnel, which contributes to high permeability. This kind of porous ceramic will therefore combine the advantages of partially sintered porous ceramic and ceramics with uni-directional pores. It is reported in this paper an attempt to fabricate porous Si3N4 ceramics from a water-based ceramic slurry containing various volume content of organic fiber, using slip casting. As a comparison, porous Si3N4 ceramics are also fabricated using die-pressing and CIPing of ceramic powder mixtures containing various volume content of starch. After sintering, porous Si3N4 ceramics with different pore morphology, such as rod-shaped and equiaxial pores, have been obtained from these two kinds of the pore forming agents. The effects of pore forming agent content on the porosity, microstructure and flexural strength have been investigated. The effects of pore morphology on gas permeability have also been investigated. Experimental Starting Powders In this study, a typical ceramic powder was obtained from a mixture of α-Si3N4 (SN-E10, UBE Industries, Ltd., Tokyo, Japan; α ratio: >95%, mean particle size: 0.5 μm, main impurities by weight: O = 1.6%; C < 0.2%; Cl, Fe, Ca, and Al2O3 < 50 ppm), 5 wt% Y2O3 (99.9% purity, Shin-etsu Chemical Co., Ltd., Tokyo, Japan), and 2 wt% Al2O3 (TMD, Taimei Chemicals Co., Ltd., Nagano, Japan). An organic whisker with a diameter of 33 μm and a length of 300 μm (KF-10BT, Nippon Kynol Inc., Osaka, Japan) was used as the fugitive particle. The whiskers were composed of phenol-formaldehyde resin, which has the desirable characteristics for a pore-forming agent of non-combustibility, heat resistance, and minor deformation during heating. A kind of potato starch with a mean diameter of 50 μm was used as the pore forming agent for the equiaxial pores. Fabrication Process The density of the whisker was measured by Archimedes’ displacement method, as 1.2185 g/cm3. The whiskers were added in varying volumes: 0, 10, 20, 30, 40, 50, and 60 vol%. The ceramic powders and whiskers were weighed according to these compositions, and aqueous slurries were prepared at a solid content of 60 wt% (32 vol% for 0% whisker and 42 vol% for 60 vol% whisker) [18]. Dispersion was promoted by adding 2 wt% cationic dispersant (7347-C, San Nopco Limited, Kyoto, Japan) and 0.5 wt% surface active agent (RA-20A, Matsumoto Yushi-Seiyaku Co., Ltd., Osaka, Japan) to the milling container, to minimize agglomeration and bubbles in the slurries. These slurries were ball milled for 4 h, followed by degassing under vacuum for 30 min before casting. Square samples of 55 mm in length and 12.5 mm in thickness were obtained by pouring the above slurries into Plaster of Paris moulds. After removal from the mould, the samples were subjected to further heating at 70°C for 48 h. With starch as the pore forming agent, the starch particles were mixed with the Si3N4-Y2O3-Al2O3 powder directly. After drying, the powder mixtures were die-pressed and subsequently CIPed under a pressure of 150 MPa, resulting in samples of 65 mm in length and 12 mm in thickness. These two kinds of dried samples were fired at a constant heating rate of 5°C/min to 800°C for 4 h, to burn off the whiskers and starch. The resultant samples were placed in a BN crucible, and subsequently sintered in a graphite resistance furnace (Model No. FVPHP-R-10, Fujidempa Kogyo Co., Ltd., Osaka, Japan). The heating rate was 5°C/min to 1850ºC followed by 4 h soaking at this temperature in flowing nitrogen-gas of a pressure of 0.63 MPa. The samples were covered with a powder mixture of 50:50 vol% Si3N4:BN to protect them from decomposition and deformation due to densification shrinkage during sintering. Characterization Densities and porosities of as-sintered bodies were determined by Archimedes’ displacement method using distilled water and are given as relative densities based on the theoretical density of silicon nitride, 3.19 g/cm3. All datum points represent the average of five density measurements. The microstructural development of sintered parts was observed on fractured surfaces of samples using scanning electron microscopy (SEM; Model JSM-6330, JEOL, Tokyo, Japan). The pore-size distributions of the sintered body were measured by mercury porosimetry (Model PoreMaster-60-GT, Yuasa Ionics Inc., Osaka, Japan). Strength was measured by three-point bending. Gas permeability was measured by pressure drop between the two sides of the specimens. Results and Discussion The powder mixture containing a high volume fraction of organic whisker was difficult to press, and the density increases very little after CIPing. After burning out the whiskers, the green body is too weak and easily destroyed. The reason is that the whiskers form cross-links which limit densification during die-pressing. Therefore, we utilized the slip casting technique for the preparation of porous Si3N4 ceramics with rod-shaped pores. Due to the fixed solids content in the slurry, the viscosity changed with the whisker content. It slightly increased with 10 vol% whiskers, but a further increase in the content led to decreased viscosity. The viscosity reached minimum at a whisker content of 30-40 vol%, and increased again when the whisker content was >40 vol%. The Si3N4 particles have a very small particle size of 0.5 μm, with a large surface area. On the other hand, the size of the organic whisker is much larger than that of the Si3N4, VIZ. 33 μm in diameter and 300 μm in length. Higher whisker content corresponds to less surface area in the mixtures and, thus leads to lower viscosity. The further increase in the viscosity of the slurries with > 40% whiskers can be explained as follows: the high whisker content leads to bridging of the whiskers, leading to large shear stress during rotation in the viscometer. The viscosities ranged between 20 and 40 mPa.s, which is suitable for a slip casting process [18, 19]. The relative densities, porosities and open porosities of samples after pressureless sintering are shown in Tables 1 and 2 for the porous ceramics fabricated from organic whisker and starch, respectively. It can be seen that the final densities of the samples with the same volume fraction of the pore forming agent were not exactly the same, maybe due to the difference of porosity in the green body and shrinkage in sintering. The porosities increased linearly with whisker and starch contents. With 60 vol% of the pore forming agent, 45% porosity can be obtained. Table 1. Densities and porosities of samples with varying whisker content. | 0 | 100 | 0 | 0.1 | 2 | 95 | 5 | 0.2 | 5 | 94 | 6 | 0.5 | 8 | 93 | 7 | 0.8 | 10 | 89 | 11 | 0.8 | 20 | 85 | 15 | 4.0 | 30 | 79 | 21 | 10.0 | 40 | 71 | 29 | 23.7 | 50 | 65 | 35 | 30.1 | 60 | 56 | 44 | 44.0 | Table 2. Densities and porosities of samples with varying starch content. | 40 | 69 | 31 | 28.9 | 60 | 52 | 48 | 45.3 | The SEM microstructure of samples containing 60 vol% pore-forming agent are shown in Figure 1. It was shown that large rod-shaped and equiaxial pores can be formed by the burnout of organic whiskers and starch, respectively. Formation of rod-like grains in the matrix was also confirmed in the SEM observation. The pores were inter-connected in both samples. 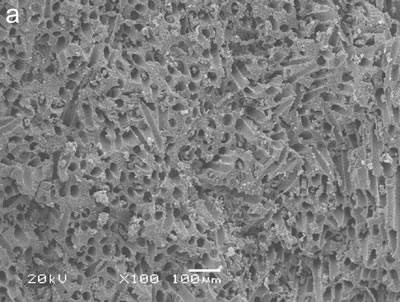 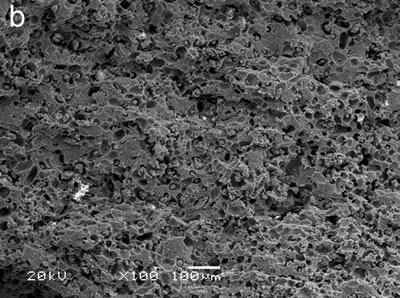 | Figure 1. SEM micrograph of porous Si3N4 ceramics in which the pores were formed by (a) Organic whisker; (b) Starch. The content of the pore-forming agent was 60 vol%. | Figure 2 shows flexural strength as a function of porosity for porous Si3N4 samples containing rod-shaped and equiaxial pores. There is almost no difference in the strength of these two types of samples. The strength decreased with a small amount of pore-forming agent, however, further addition of the pore-forming agent resulted in only a moderate decrease of strength. This can be explained as follows. The pore-forming agent has a large size of 30-50 μm, and the resultant pores can act as fracture origins; but as pore size is the key factor affecting the flexural strength, increasing the porosity by increasing the whisker content results in only a moderate strength decrease. 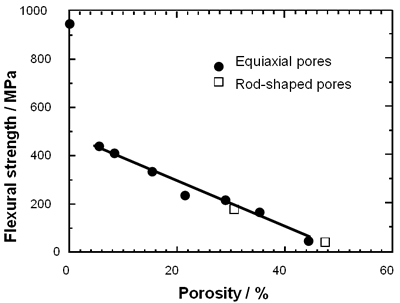 | Figure 2. Flexural strength as a function of porosity for porous Si3N4 samples containing rod-shaped and equiaxial pores. | The permeability of the two sample types is shown in Figure 3. The rod-shaped pores resulted in considerable permeability. The permeability was primarily determined by the pore size [20], but it was also related to the pore morphology. The level of pore size for these two types of porous ceramics was almost the same. This outstanding permeability can be attributed to the rod-shaped pore structure enhancing the gas flow locally due to a relatively long tunnel-like pore. The rod-shaped pores provide a direct tunnel at short range and facilitate gas flow during the filtering process. 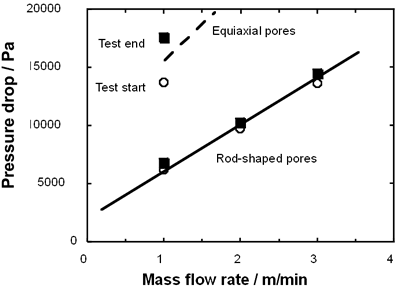 | Figure 3. Pressure drop as a function of mass flow rate for porous Si3N4 samples containing rod-shaped and equiaxial pores. The porous ceramics with rod-shaped pores exhibited outstanding permeability in comparison with these containing equiaxial pores. | Conclusions The formation of rod-shaped pores in Si3N4 ceramics was demonstrated using slip-casting of aqueous slurries of Si3N4 + 5 wt% Y2O3 + 2 wt% Al2O3 with 0-60 vol% fugitive organic whiskers; loading of 60 wt%, and the formations of equiaxial pores was demonstrated using starch as the pore- forming agent using die-pressing. The porosity of the porous Si3N4 ceramics was closely related to the whisker content, with a high content leading to high porosity. 60 vol% of the fugitive particle resulted in a porosity of about 45%. The whiskers and starch were uniformly distributed in the samples. Flexural strength decreased with increasing porosities, but no difference in flexural strength was exhibited by these two kinds of samples. Outstanding permeability was demonstrated for the porous Si3N4 ceramics with rod-shaped pores. Acknowledgements This work has been supported by AIST, METI, Japan, as part of the Synergy Ceramics Project. The authors are members of the Joint Research Consortium of Synergy Ceramics. References 1. Y. Shigegaki, M. E. Brito, K. Hirao, M. Toriyama and S. Kanzaki, “Strain Tolerant Porous Silicon Nitride”, J. Am. Ceram. Soc., 80 (1997) 495-98. 2. Inagaki, N. Kondo and T. Ohji, “High Performance Porous Silicon Nitrides”, J. Eur. Ceram. Soc., 22 (2002) 2489-94. 3. Y. Shigegaki, M. E. Brito, K. Hirao, M. Toriyama and S. Kanzaki, “Processing of a Novel Multilayered Silicon Nitride”, J. Am. Ceram. Soc., 79 (1996) 2197-200. 4. Y. Shigegaki, M. E. Brito, K. Hirao, M. Toriyama and S. Kanzaki, “Processing of a Novel Multilayered Silicon Nitride”, J. Am. Ceram. Soc., 79 (1996) 2197-200. 5. J.-F. Yang, G.J. Zhang and T. Ohji, “Porosity and Microstructure Control of Porous Ceramics by Partial Hot-Pressing”, J. Mater. Res., 16 (2001) 1916-18. 6. J.-F. Yang, T. Ohji, S. Kanzaki, A. Díaz and S. Hampshire, “Microstructure and Mechanical Properties of Silicon Nitride Ceramics with Controlled Porosity”, J. Am. Ceram. Soc., 85 (2002) 1512-16. 7. N. Kondo, Y. Suzuki and T. Ohji, “High-Strength Porous Silicon Nitride Fabricated by the Sinter-Forging Technique”, J. Mater. Res., 16 (2001) 32-34. 8. C. Kawai and A. Yamakawa, “Effect of Porosity and Microstructure on the Strength of Si3N4: Designed Microstructure for High Strength, High Thermal Shock Resistance, and Facile Machining”, J. Am. Ceram. Soc., 80 (1997) 2705-708. 9. A. Díaz, S. Hampshire, J.-F. Yang, T. Ohji and S. Kanzaki, “Comparison of Mechanical Properties for Different Porous Silicon Nitride Materials Fabricated by Partial Sintering, Addition of Fugitive Inclusions and Partial Hot-Pressing”, J. Am. Ceram. Soc., (In press) 10. K. Schulzk and M. Durst, “Advanced and an Integrated System for Hot Gas Filtration using Rigid Ceramic Elements”, Filtration & Separation, 31 (1994) 25-28. 11. J.-F. Yang, G.J. Zhang and T. Ohji, “Fabrication of Low-Shrinkage, Porous Silicon Nitride Ceramics by Addition of a Small Amount of Carbon”, J. Am. Ceram. Soc., 84 (2001) 1639–41. 12. J.-F. Yang, Z.Y. Deng and T. Ohji, “Fabrication and Characterisation of Porous Silicon Nitride Ceramics using Yb2O3 as Sintering Additive”, J. Eur. Ceram. Soc., 23 (2003) 371-378. 13. J.-F. Yang, G. J. Zhang, N. Kondo and T. Ohji, “Synthesis and Properties of Porous Si3N4/SiC Nanocomposites by Carbothermal Reaction between Si3N4 and Carbon”, Acta Mater., 50 (2002) 4831-4840. 14. J.-F. Yang, Y. Beppu, G.J. Zhang and T. Ohji, “Synthesis and Properties of Porous Single-Phase β’-SiAlON Ceramics”, J. Am. Ceram. Soc., 85 (2002) 1879–81. 15. O. Lyckfeldt and J. M. F. Ferreira, “Processing of Porous Ceramics by Starch Consolidation'”, J. Eu. Ceram. Soc., 18 (1998) 131-140. 16. D.M. Liu, “Fabrication of Hydroxyapatite Ceramic with Controlled Porosity”, J. Mater. Sci. – Mater. M., 8 (1997) 227-232. 17. G.J. Zhang, J.F. Yang, Z.Y. Deng and T. Ohji, “Fabrication of Porous Ceramics with Unidirectionally Aligned Continuous Pores” J. Am. Ceram. Soc., 84 (2001) 1395–97. 18. N. Miyagawa and N. Shinohara, “Fabrication of Porous Alumina Ceramics with Uni-Directionally-Arranged Continuous Pores using a Magnetic Field” J. Ceram. Soc. Jpn., 107 (1999) 673-677. 19. R. Moreno, A. Salomoni and S. M. Castanho, “Colloidal Filtration of Silicon Nitride Aqueous Slips. Part I: Optimization of the Slip Parameters”, J. Eu. Ceram. Soc., 18 (1998) 405-416. 20. C. Olagnon, D. McGarry and E. Nagy, “The Effects of Slip Casting Parameters on the Sintering and Final Properties of Si3N4”, Br. Ceram. Trans. J., 88 (1989) 75-78. 21. A. P. Phillipse and H. L. Schram, “Non-Darcian Air-Flow through Ceramic Foams”, J. Am. Ceram. Soc., 74 (1991) 728-732. Contact Details |