Major suppliers of advanced materials in the UK have identified that metal matrix composites (MMCs) would have an impact on all transport industries including aerospace. In response to this challenge, companies such as Alcan, BP,Cray, ICI and LSM invested heavily in new equipment to accommodate the exacting demands of the production of difficult materials to high standards of technical performance. For five years the UK could demonstrate competence in the production of metal composites by spray deposition, powder metallurgy, mechanical alloying, liquid metal pressure forming, stir casting, squeeze casting and reactive processing. It could claim also to be a major supplier of the constituent materials of the composites including continuous monofilaments of silicon carbide or of fine fibres in alumina and to be most advanced in the production of fine powders of aerospace alloys. The recent withdrawal of most of the major companies from the production of metal matrix composites has created a negative image despite the significant technical progress that has been achieved. That is, MMCs are being used today to achieve significant weight and performance benefits. A small but thriving MMC industry exists in Europe, with emphasis on real engineering applications and the industry has good prospects for growth. The Defence Research Agency (DRA) has played its part in enhancing the technology both for the production of particulate reinforced composites, now operated by Aerospace Metal Composites, and for the development and production of silicon carbide monofilament and titanium alloy composites. Advantages of MMC’s Metal matrix composites are used to competitive advantage to provide weight or performance benefits. Increased operating speeds of more than 50% have been achieved in high speed machinery. A unique combination of lightness, fatigue resistance, damage performance and stiffness is ideal for designing road and mountain bicycles. Increased stiffness of more than 50% for isotropic (particulate) composites and of more than 100% for fibre reinforced systems is readily achieved, figure 1. 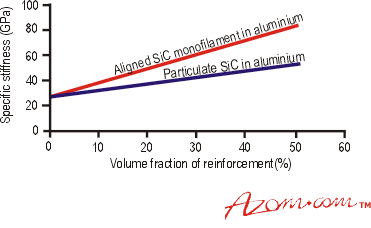 | Figure 1. Improvements in specific stiffness of MMC’s with increasing silicon carbide content. | MMC’s in Engines Diesel pistons employing metal matrix composites are used for locomotive engines to enhance performance and reduce life cycle costs. In addition, high performance automotive components are manufactured to achieve major performance advantages. These often rely on a combination of stiffness, elevated temperature fatigue and outstanding wear resistance. In these respects, the startling advantages of particulate reinforced aluminium alloys in maintaining strength and fatigue strength at elevated temperature are perhaps yet not fully exploited, figure 2. Both fine fibres in aluminium alloys and monofilaments in titanium alloys are used to maintain strength and stability in high temperature engine and aeroengines, figure 3. Selective circumferential fibre reinforcement of the aeroengine compressor allows radical new designs to become feasible. Weight savings of up to 80% have been predicted. The potential of such performance improvements cannot be ignored by materials engineers or aeroengine designers. 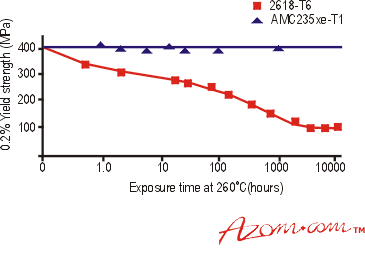 | Figure 2. Thermal stability of particulate reinforced MMC’s. 2618-T6 is an Al-Cu-Mg-Fe-Ni alloy used on the Concorde for high temperature applications. AMC 235 is Aluminium 2124 with 35 vol% SiC. | 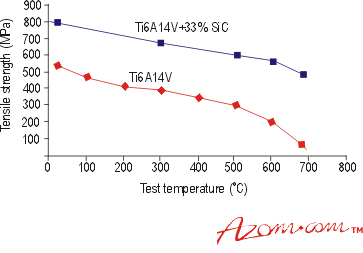 | Figure 3. Elevated temperature strength of a Ti6Al4V alloy unreinforced and reinforced with silicon carbide monofilament. | Despite recessionary pressures, metal matrix composites based primarily on aluminium alloys are available commercially from both UK and US sources, produced by several powder metallurgy routes, by stir casting, by reactive processing and by mechanical alloying. Fibre and monofilament variants, although perhaps less well advanced commercially, are also available and are produced by both liquid metal forming and diffusion bonding methods. It is clear that an embryonic MMC industry has survived the recession and that there is increasing interest in application of these materials, predominantly in the sports, motor sports and high speed machinery industries. However, military and commercial qualification programmes are under way, a sure indicator of a real interest in a market with exceptional levels of technical requirement and an associated long lead time to utilisation. Limitations to Wide MMC Acceptance It is worth considering the limitations that may hamper the full commercialisation of metal composites. Information The gap in understanding between the materials experts knowledge of the performance of new material and real engineering application must be bridged. This would involve helping the engineering community to design with MMCs by providing property data covering key aspects of performance and to apply appropriate processing techniques (eg forming, machining, joining etc). It is in this area that demonstrator programmes are of most value. Component Cost The disadvantage of MMCs is that they offer increased performance but at increased cost. The benefit must always be balanced by the related costs. However, there may be a misconception here; that is, if an aluminium based MMC is offered against a conventional aluminium component, then a major increase in performance is vital if the significant increase in costs is to be justified. However, it is often the case that an aluminium based MMC is offered in replacement of a titanium or polymeric composite part, competing on both performance and cost. Design Consideration The MMC component design must also take into account of cost effective processing techniques. MMCs commonly require net shape forming with minimal losses. Selective reinforcement techniques allow the high performance fibre and monofilament materials to be applied in critical areas. However, the major factor is the high price of the monofilament reinforcement per se and the costs of its incorporation into a reactive matrix. Moving from development to production scale of these advanced materials will bring big savings but will require a major commitment from end-users and producers alike. The Outlook Metal matrix composites have good prospects for the future, however exponential growth is not expected. Steady incremental growth in performance limited markets is likely with niche applications offering competitive advantage in engineering design. |