Mar 31 2008
Engineers have known for years about the wonderful positives of different thermoplastics, including light weight, low friction, non-corrosion, dimensional stability, cleanliness and static dissipation.
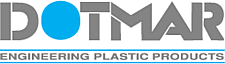
But while these brilliantly versatile materials have advantages that would make a designer’s mouth water, they are sometimes not considered for extreme applications because of perceived limitations such as temperature and tensile strength.
Sometimes these limitations are real (for “ordinary” thermoplastics); sometimes they are the result of an Australasian engineering ethos that is overwhelmingly metals-focussed and alternatives-blind.
However, there is a new generation of Advanced Engineering Plastic Products (AEPP) that is going to rattle a few preconceptions and give these thermoplastics the edge over metals and ordinary thermoplastics for more extreme applications.
Our AEPP aristocrats of thermoplastic engineering are now being introduced the world over for applications requiring continuously high temperature tolerances, sometimes exceeding 300 deg C in air (500 deg C for short times) and up to 140MPA tensile strength.
It is important to note that these extreme materials for extreme applications are already in use in applications where top performance and reliability are proven – ranging from the previously mentioned electrical connectors, rotary compressor vanes, can mandrels, breaker welding supports, computer chip nests, scraper blades in heat exchangers, pump wear rings, solvent extractor conveyor bushings, insulating printer bearings, and structural, friction and wear applications spanning industries from automotive, electronics, food and pharmaceuticals through to construction and cranage, materials handling, mineral processing, water treatment and aggressive chemical environments in primary processing. Applications are discussed on engineering websites, where you can familiarise yourself with the specific advantages of wonder materials with weird names such as Celazole, Torlon PAI, PPSU, PEI/Semitron, Ketron Peek, Flurosint, Techtron HPV, PVDF and others. These arcane titles cover some very down-to-earth advantages, including:
• retention of mechanical and fatigue properties at elevated temperatures
• resistance to high energy radiation
• maximum thermal operating temperatures surpassing those of PTFE plastics
• As well as improved chemical resistance and increased dielectric properties.
Peak of the Pyramid of Performance
On the pyramid of performance, AEPPs sit right at the peak, directly above the more common Engineering Plastics category, which in turn ranks above the common garden Commodity Plastics.
To give you an idea of the sort of performance we are talking about, let’s look at Celazole PBI (one of the highest performance engineering thermoplastics available today, with extremely high maximum allowable service temperature in air of 310 deg C continuously, going up to 500 deg C for short periods (3-4 hours)).
Celazole also offers improved wear performance and longer life in sensitive applications, such as light bulb contact parts and providing an extra margin of safety in electrical connectors used by aircraft engine manufacturers.
Also near the top of the performance pyramid are the different types of Torlon (including Torlon 4203, 4503, Torlon 4301 and 4501 bearing grade and Torlon glass fibre reinforced). These also offer very high temperature performance combined with excellent mechanical performance and dimensional stability.
Established applications include rotary compressor vanes, can mandrels, breaker welding supports and chip nests and sockets. A word of caution though: because of this material’s response to water and chemicals, it rewards handling and installation regimes detailed by its distributors, Dotmar EPP, to derive maximum benefits.
Immediately below the Celazole and Torlon families on the AEPP performance pyramid are plastics that fall into the amorphous and semi-crystalline categories.
The amorphous group includes the PSU 1000 Polysulphone and PPSU 1000 Polyphenylsulphone and PEI 1000 Polyetherimide.
These unreinforced materials offer a combination of excellent mechanical, thermal and electrical properties, as well as excellent hydrolysis resistance and physiological inertness. (properties making them suitable for repeated steam sterilisation and food contact respectively).
So good is their performance that they are used in medical equipment such as endoscopic probe positioning ferrules and sighting arms used to position screws to realign broken bones.
Broader established applications include cleaning equipment inserts. PEI 1000 is used to make clamps with high dielectric strength and inherent low flammability used to connect circuit boards to video display units.
The semi-crystalline group of AEPPs similarly offers plastics with unfamiliar names that deal with familiar problems in pumps, scrapers, bearings and bushes, for example.
The main groups here include Ketron PEEK polyetherehterketones (no, it’s not a spelling mistake), Techtron HPV PPS Polyphenylene Sulphide bearing grade and PVDF 1000 Polyvinylidenefluorides.
This complicated nomenclature again denotes some straightforward benefits, which in the case of Ketron PEEK semi-crystalline materials include a unique combination of high mechanical performance, temperature resistance and chemical resistance. It is probably the most popular AEPP. Established applications include gas analyser structural body parts, scraper blades in heat exchangers, sleeve bearings for steel wire guide rollers and pump wear rings
PVDF fluoropolymers exhibit excellent mechanical properties combined with superb chemical resistance. These qualities have seen the material used in applications varying as widely as pH-meter housings in harsh industrial applications; and dishwasher arm bearings with a 20-year service life.
Finally, Techtron HPV reinforced, internally lubricated semi-crystalline polymer is designed to close the gap both in performance and price between standard thermoplastic materials and AEPPs. Examples of applications include solvent extractor conveyor bearings and insulating printer bearings.
Continuous solvent extractors are used where aggressive chemicals extract oil or sugar from the meal. The Techtron HPV PPS bushings installed in the rollers of the screen transporting the meal are continuously submerged in the solvent. Under these “impossible to lubricate” conditions, the material provides a long-lasting maintenance solution.
Posted February 26th,2006