Mar 31 2008
One of the foremost of the light, clean and tough engineering thermoplastics making inroads into the traditional domains of metal machinery components is that wonderfully versatile material acetal.
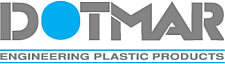
A highly crystalline stable form of polymerised formaldehyde, acetal (supplied by Australasian plastics engineering specialist Dotmar under the name Ertacetal C ®) is undoubtedly one of the most pervasive and important engineering plastics sold by the plastics stock shapes industry.
This strong, stiff plastic is increasingly prized by engineers for its physiological inertness, strength and rigidity, excellent dimensional stability, resilience and toughness and electrical properties. It is an excellent bearing material, with a low co-efficient of friction and good tribological (wear) properties in both wet and dry environments. Natural acetal is FDA compliant for direct food contact.
Acetal/Ertacetal C is used in a wide variety of applications, ranging from heavy industrial and processing, through to consumer items. Applications include:
• bearings, bushes, cams and gears, including small moduli cams, heavily loaded bearings and rollers,
• assembly fixtures and wear pads
• valves, vale stems, pumps (inc milk pumps), filter housings, impellers and tapware
• conveyor links, including food conveyors
• handles and brackets, snapfit assemblies
• food machinery components
• packaging machinery precision parts
• electrical insulators, semiconductors and analytical equipment
• water and chemical processing equipment (including components that which operate continuously in water of 60°C-80°C) because it has better chemical and corrosion resistance than many metals parts
Engineering machine shops like to work with acetyl/Ertacetal C because it machines easily and because of its excellent dimensional stability, which is primarily a result of the material’s low thermal expansion and low moisture absorption.
But to fully appreciate the benefits that can be derived when this material is correctly specified, it is useful to examine acetal in its various forms and discuss the features, benefits and limitations of each variety.
Acetal compared with other mechanical plastics
Many thermoplastic materials are known for a single special property, such as the optical clarity of acrylic, or the lubricity of Teflon®. The appeal of acetyl, however, is that it offers a wonderful balance of properties now found in other materials. The table on the next page compares acetal with some other common mechanical plastics in order to illustrate this point.
Copolymer vs Homopolymer
While both types of acetal material have similar properties, there are some notable differences, which allow Dotmar to go to market with Copolymer material as a better all-round choice.
Copolymer is a better choice for the food processing industry – and
copolymer acetal also has superior resistance to hot water, steam and heat aging, when compared with homopolymer material. Because of this, copolymer acetal is often specified for hot food processing applications or other applications where the material will be exposed to elevated temperatures, hot water or steam. Copolymer acetal has better resistance to some chemicals, including alkali.
Speciality grades
Acetal/Ertacetal stock shapes are available in a wide variety of specialty grades with additional additives and fillers that modify the mechanical, electrical and wear properties of the material.
Bearing and wear grades of acetal may include combinations of PTFE, silicone, and carbon fibres. These additives are used to enhance the tribological properties of the material. Bearing-grade acetals are engineered for longer wear, higher limiting PV (pressure velocity) ratings, and lower co-efficients of friction for smoother operation of moving parts. Unlike metal bearing materials, bearing grades of acetal do not usually require oil or grease for smooth operation. Acetal bearings tend to run quieter and are lighter than their metal counterparts.
Static-control acetals are seeing wide use by the semiconductor, electronics, printing and explosives manufacturing industries where static electricity discharge can have costly or even catastrophic results. Carbon fibres, stainless steel fibres and proprietary alloys are all used to modify the electrical resistivity of acetal resin to that static charge can dissipate safety through the material.
Processing (Extrusion V Compression Moulding)
Acetal stock shapes are produced by two methods: extrusion and compression moulding. Rod, tube and film are typically extruded, while sheet may be produced using either manufacturing process. Each process had advantages and disadvantages.
Extruded acetal sheet may be product to any length, which allows end-users to select the appropriate length to maximize part yields. Extruded sheet can also be manufacturing to tighter thickness tolerances compared with the tolerances that can be achieved with compression moulding.
Compression moulded acetal tends to have lower residual stress levels than extruded sheet, which allows it to be machined to complex shapes with minimal warping. Compression moulded acetal sheet also tends to have smoother surface finishes that extruded material.