Feb 22 2009
BASF’s special product line for composites will be shown at the JEC Composites Show in Paris, March 24 to 26, 2009. Around the globe the fair is considered as one of the most important for the named specialty materials. To provide greater efficiencies in manufacturing high-performance wind turbine rotors the company is offering new systems based on epoxy resins and curing agents sold under the Baxxodur® brand. BASF’s RELIUS Coatings, designed especially for rotor blades, will represent another highlight.
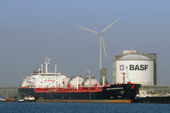
Also featured at BASF’s booth will be a special Ultrason®, a high-temperature resistant polyethersulfone now being made available as a powder. Its use improves not only the production process but also the toughness of heat-resistant epoxy resins which are applied, for instance, in the production of automotive racing and aircraft components.
Innovative epoxy resin systems for high-performance rotor blades
Larger rotor blades have increased the output of modern wind turbines. Composites based on epoxy resins have become the material of choice in fabricating such rotor blades. Most recently BASF has been supplying Baxxodur two-component systems based on epoxy resins and curing agents.
With these systems production of large rotor blades can be significantly accelerated thanks to a new curing agent. To assure that the forms for blades are filled completely and rapidly, the BASF systems react slowly initially. Subsequent heat application speeds the curing action and releases the form for production of the next blade more quickly. Consequently cycle times for the manufacture of rotor blades can be reduced by up to 30 percent, raising productivity accordingly. Because the new systems are processed additionally in a broader temperature range than conventional products, the production process becomes more flexible. The BASF systems have been approved by Germanischer Lloyd AG (GL) for use in wind turbines. GL is one of the world’s leading certification agencies for those turbines. Recently GL has been accepting performance tests conducted by BASF’s own laboratories on epoxy systems and composites made with these systems.
New: RELIUS coating systems for reconditioning wind turbines
As one of the world’s leading suppliers of rotor blade coatings for wind turbines BASF is marketing high-quality solutions under the RELIUS brand. The coatings benefit from economies, high weather resistance and excellent elongation at break properties. Now the company is introducing an innovative, highly elastic repair system that in many cases will avoid a costly exchange of blades. New, too, are the WindCoat Finish and WindCoat Protector SA coatings. Both products represent further developments of the established RELIUS line. WindCoat Finish is a matt final coat which can be applied manually or automatically without problems even if thicker coats are specified. Based on polyurethane, the WindCoat Protector spray coating adheres excellently without the use of solvents. It provides excellent adhesion to epoxy laminates and PUR Gelcoats. For years the RELIUS Rotor Blade System has served as a coating delivering durable protection for wind turbines. RELIUS products, especially suited for processing on glass fiber surfaces of rotor blades, include Gelcoat protective coatings, fillers, edge protection and top coats. The two-component coatings based on polyurethane are supplied low in solvents or solvent-free and conform to current VOC guidelines. Whether applied by roller, spray gun, manual or automatic methods, RELIUS coatings can be used in all manufacturing processes, including wet lamination, on prepreg laminates and in the infusion process. BASF’s strengths, ranging from solution-oriented consultations and individualized technical service to training attendant personnel, augment the advantages available from RELIUS brand products. RELIUS coatings for wind turbines have proven their worth for more than 15 years. As the world turns so do 25,000 RELIUS-coated rotor blades around the globe.
High-performance plastic for epoxy resin composites now also available as micro-powder
Recently the plastics divisions of BASF launched a high-temperature resistant Ultrason® thermoplastic E 2020 P SR, not only in the form of flakes but also micronized – thus as a powder. It is designated Ultrason E 2020 P SR micro.
Due to its higher share of hydroxyl end groups the special version of the polyethersulfone (PESU) is highly compatible with high-performance epoxy resins and has long proven itself in applications as an impact modifier. Sophisticated composites based on high-temperature resistant epoxy resins are used in airplanes and racing cars but stay very brittle unless modified with heat-resistant impact modifiers such as Ultrason E 2020 P SR. In its new powder form it is more simply incorporated in the resin system. No longer does it have to be solubilized in a solvent which subsequently has to be removed. This saves customers time and money. The new micro-powder is immediately available in commercial quantities.