Feb 11 2005
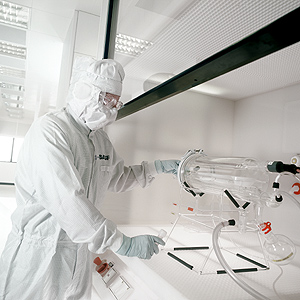
Modern computers have little room to spare, with as many as a billion transistors per square centimeter jostling for position on their processors and memory chips. Imagine the entire population of India holidaying in Washington DC and you’ll have some idea of the density. What makes it possible is that transistors are so small. And that, in fact, is the biggest problem in their production. Circuits this tiny can be paralyzed by a particle smaller than a flu virus. A single misplaced atom may render a chip useless.
Microchip production is complicated. More than 600 working steps are required to turn the raw material, quartz sand, into a modern processor. Most of these steps require the use of special chemicals, for example to clean and etch silicon chips. “BASF is a leading manufacturer of electronic chemicals,” says Claus Poppe, Director Global Business Management for Electronic Chemicals. “At least one BASF product was used in the production of any microchip manufactured today.”
The first step is to get silicon (the building material for most microchips) from simple quartz sand. To clean the “dirty” silicon produced, technicians convert it to trichlorosilane using hydrogen chloride. This clear liquid is easily purified by multiple distillations. The much cleaner silicon emerging from this process is ready for the next step, in which specialists use the Czochralski method (see info box) to grow impressive shiny silver crystals up to two meters tall with a perfect interior structure.
Special saws cut these crystals into paper-thin wafers that form the basis of microchip production, but they need to be smoothed down first and polished to a shine. Again, a number of high-purity BASF chemicals such as nitric acid, sulfuric acid and hydrochloric acid are used for the polishing and cleaning process. The finished wafers are round disks measuring up to 30 centimeters across. Their surface has to be absolutely perfect with no irregularities larger than a couple of nanometers – if they were the size of a football pitch, this would mean no bumps larger than one-tenth of a millimeter.
When computers were first produced, technicians were able to solder transistors by hand. Today’s tiny circuits call for a different technique. The modern technology for etching transistors onto wafers is called photo-lithography. In this process, specialists first apply a barrier layer to the silicon which they illuminate using a mask. The layer dissolves at the sites exposed to light and the underlying silicon layer is etched. Chip manufacturers treat the etched locations with chemicals and repeat the process a number of times, building up transistors layer by layer, like building houses from layers of blocks.
Finished transistors will not work if more than one atom out of a million is faulty. But dirt is everywhere. Metal devices invariably give off unwanted atoms. Humans transmit impurities by a mere touch or breath. That’s not counting the approximately half a billion particles of dust floating around a normal room. For this reason every step of chip manufacture takes place in pristine working areas where all the furnishings are plastic and filters are installed to remove the last particle of dust from the ambient air. Anyone entering these facilities must wear a full set of protective gear including gloves and a face mask.
“Finished microchips must be absolutely free of contaminants, so the chemicals that are used in their manufacture have to be extremely pure,” explains Dr. Karl-Rudolf Kurtz, head of BASF’s Electronic Materials business unit. “BASF currently supplies around 30 chemicals of electronic grade purity.” BASF is equipped with cleanroom labs to check the chemicals’ purity before they are delivered to chip manufacturers. “We have the technology to detect impurities in trace amounts of less than one microgram per tonne of product. That’s like a needle in 100,000 haystacks. Detecting tiny concentrations of these magnitudes is only possible with state of the art spectrometry.”
The Prospects
Gordon Moore, co-founder of Intel, worked out a hypothesis in 1965 based on his observations of the market. He predicted that the number of transistors per unit of surface area would double every year as microchip technology progressed. Moore’s law basically still applies to this day, with transistors getting smaller and smaller all the time. For as long as the trend still holds, the quality of electronic chemicals must continue to rise.
BASF is a leading supplier of chemicals to the semiconductor industry. The global electronic chemical business acquired from Merck KGaA at the start of 2005 will significantly strengthen BASF’s market position. Electronic chemicals distribution is organized in a global business management system for easier ordering and shorter delivery times. BASF was conferred the UK gas supplier BOC Edwards’ Supplier Quality Award for the reliability and quality of its electronic gases hydrogen chloride and ammonia. BASF is also the world’s only supplier of hydroxylamine free base, a highly active solvent for cleaning microchips.
The Info Box
From beach sand to computer chip
Silicon (from the Latin silex meaning ‘flint’) is the second most abundant element in the earth’s crust after oxygen and is contained in most minerals. Elemental silicon is a semiconductor. Its electronic properties can be modified in a targeted fashion by introducing foreign atoms, a process called doping. Silicon is widely used in microelectronics and solar cell technology.
The Czochralski method is the technology used to grow the large crystals required in the chip industry. A tiny but perfectly formed crystal is immersed in a melted purified silicon bath that is only slightly warmer than the melting point. If the crystal is removed from the molten silicon carefully enough, silicon atoms will remain attached. The attached atoms align themselves precisely to the structure of the little seed crystal. The process results in the growth of ideal monocrystals up to two meters tall. The method was named after the Polish scientist Jan Czochralski who discovered it by serendipity in 1916 after accidentally dipping his quill into a tub of molten metal instead of an inkpot.
Hydroxylamine is a colorless crystalline compound produced from nitrates and hydrogen. BASF is the world’s only supplier of pure hydroxylamine in the form of a 50 percent aqueous solution. The 7,000 tonne production capacity in Ludwigshafen is enough to supply the entire global microchip industry, where the compound is used to clean chips after etching.
Transistors switch an electric current on or off between two connectors, depending on the voltage applied to a third connector attached to the respective transistor. They can also increase the flow of current. Silicon-based microchip transistors are very fast switchers, economical and tiny. Modern computers could not have been developed without them.
For more infromation on transistors click here.